3-Axis CNC Machining: How to Get Accurate Quotes
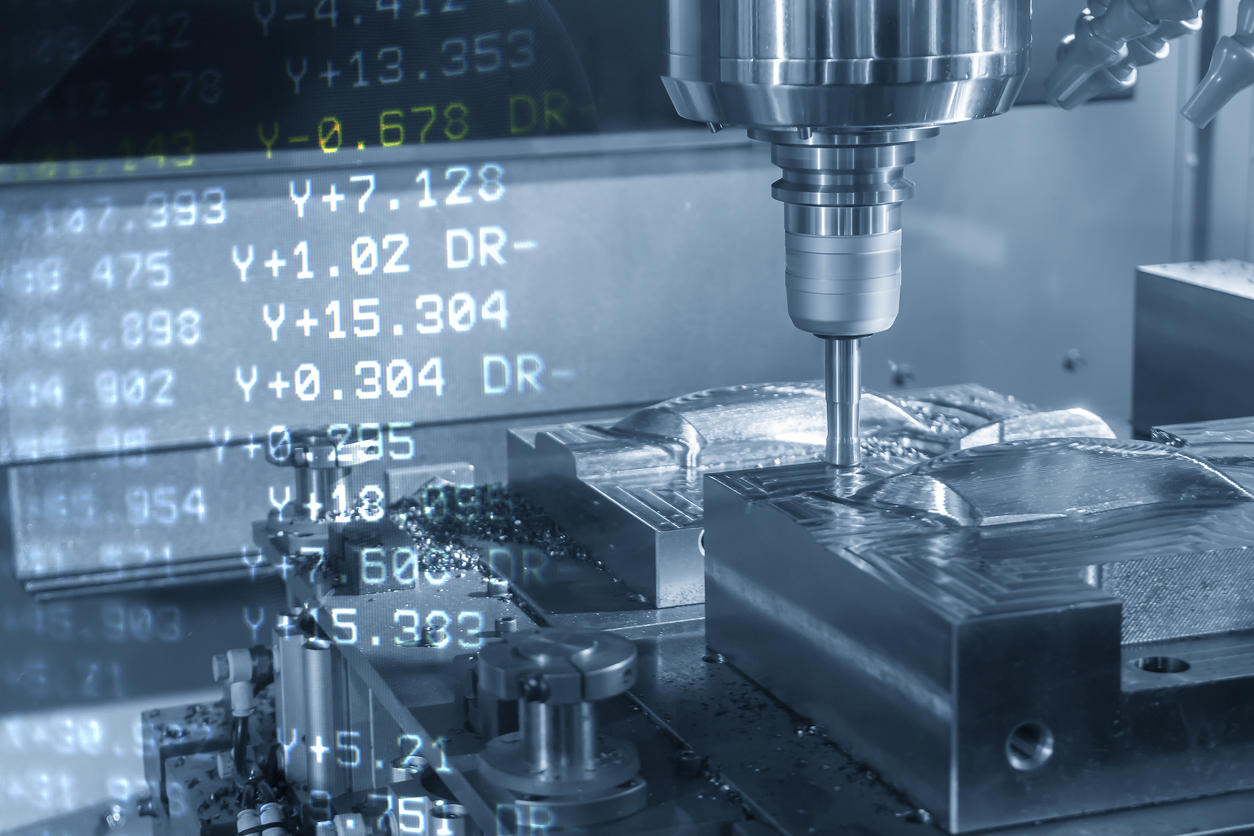
3-axis CNC machining is a widely used manufacturing process that offers precision and versatility in creating custom parts and prototypes. It has become an essential technology for industries ranging from aerospace to consumer goods. Understanding the capabilities and quoting process for 3-axis CNC machining is crucial for businesses looking to optimize their manufacturing operations.
Obtaining accurate quotes for 3-axis CNC machining projects is a key step in ensuring cost-effectiveness and project feasibility. By familiarizing yourself with the factors that influence pricing, you can make informed decisions and secure competitive quotes from service providers.
In this article, we will explore the intricacies of 3-axis CNC machining and provide a comprehensive guide on how to obtain accurate quotes for your projects. We will delve into the essential steps and considerations that can help you streamline the quoting process and achieve optimal results.
What is 3 Axis CNC Machining?
3-axis CNC machining is a subtractive manufacturing process that involves the use of computer-controlled cutting tools to remove material from a solid block, creating precise and complex geometries. The term "3-axis" refers to the three linear axes—X, Y, and Z—along which the cutting tool can move.
In a 3-axis CNC machine, the workpiece remains stationary while the cutting tool moves along the three axes, following a pre-programmed toolpath. This toolpath is generated based on a 3D CAD model of the desired part, which is then translated into machine-readable code, such as G-code.
The cutting tool, typically a rotating spindle with interchangeable cutting bits, removes material through various operations such as milling, drilling, and boring. The machine can work with a wide range of materials, including metals like aluminum, brass, and stainless steel, as well as plastics like ABS, nylon, and polycarbonate.
Benefits of 3-Axis CNC Machining
- Precision: 3-axis CNC machines offer high precision and repeatability, ensuring consistent quality across multiple parts.
- Versatility: With the ability to handle a variety of materials and perform different cutting operations, 3-axis CNC machining is suitable for a wide range of applications.
- Efficiency: Automated toolpaths and quick tool changes enable faster production times compared to manual machining methods.
- Cost-effectiveness: 3-axis CNC machining is often more cost-effective than other manufacturing processes, especially for low to medium production volumes.
Applications of 3-Axis CNC Machining
3-axis CNC machining finds applications across various industries, such as:
- Aerospace: Machining of aircraft components, engine parts, and structural elements.
- Automotive: Production of engine components, suspension parts, and interior trim pieces.
- Medical: Fabrication of surgical instruments, implants, and medical device components.
- Electronics: Machining of enclosures, heat sinks, and custom electronic housings.
- Consumer Goods: Creation of prototypes and end-use parts for consumer products.
With its versatility, precision, and cost-effectiveness, 3-axis CNC machining has become an indispensable tool for manufacturers seeking to produce high-quality parts efficiently. By understanding the capabilities and limitations of this technology, businesses can leverage its potential to optimize their manufacturing processes and stay competitive in their respective industries.
How to Get Accurate Quotes for 3 Axis CNC Machining
Securing accurate quotes for 3-axis CNC machining involves a comprehensive approach to identifying key cost factors and navigating the quoting process efficiently. This approach not only supports effective budgeting but also ensures your projects remain viable and competitive.
Step 1: Prepare Detailed CAD Models
Initiating the quoting process with precise CAD models is essential. These models form the foundational template for production, so precision remains critical. Any discrepancies or unclear specifications can lead to increased costs and processing times. Comprehensive CAD designs minimize potential alterations, facilitating a seamless transition from design to manufacturing.
Step 2: Specify Material Requirements
Material choice significantly impacts CNC machining costs. Each option—be it aluminum, stainless steel, or a polymer like ABS—presents unique machining challenges and costs. Specifying your exact material requirements upfront allows providers to generate more precise quotes. Evaluate factors such as machinability, availability, and suitability to ensure alignment with your project goals.
Step 3: Consider Surface Finishes
Surface treatments can add complexity and cost to a machining project. Whether your parts need anodizing, bead blasting, or other finishes, these details must be considered in the initial quote. Specifying these requirements early helps avoid unforeseen expenses and ensures the final product meets both functional and aesthetic standards.
Step 4: Provide Production Volume
Production volume directly influences pricing strategy. Larger orders often benefit from reduced per-unit costs due to economies of scale. Clearly indicating your required quantity allows providers to adjust their quotes appropriately. This transparency is vital for negotiating favorable terms and securing the most cost-effective solution.
Step 5: Utilize Online Quoting Platforms
Employ online platforms that offer immediate CNC quotes to simplify the quoting process. These tools provide rapid feedback on design specifications and costs, enabling quick comparisons across service providers. Online quoting systems enhance efficiency by integrating various factors like material choice, part complexity, and order size, offering a detailed cost breakdown instantly.
Step 6: Engage in Exceptional Communication
Effective dialogue with your CNC service provider is key to obtaining precise quotes. Discuss project details, clarify specifications, and address any potential issues early on. Clear communication aligns expectations between parties, minimizing the risk of misunderstandings or costly changes. This collaborative approach fosters a more streamlined and productive engagement, leading to successful project outcomes.
Step 1: Prepare Detailed CAD Models
Crafting comprehensive CAD models is pivotal to the success of any 3-axis CNC machining endeavor. These models are more than mere blueprints; they are intricate guides that define every aspect of the machining process. The level of detail in your CAD designs has a significant impact on the production quality, cost efficiency, and overall success of your project.
Emphasizing Detail
Ensuring that CAD models are meticulously detailed is essential to avoid errors during machining. Precision in design translates to fewer adjustments and smoother operations. A thorough model aids in the generation of efficient toolpaths, reducing manual interventions.
- Exact Measurements: Providing precise measurements ensures parts fit and function as intended, minimizing costly rework.
- Tolerance Precision: Specifying tolerances accurately helps communicate the acceptable range of variations, aligning with the machine's capabilities.
Optimizing CAD Design
Adhering to optimal design practices when creating CAD models enhances the ease of manufacturability and streamlines production.
- Manufacturability Considerations: Integrate features that facilitate machining, such as consistent wall thickness and avoidance of complex undercuts.
- Clear Feature Definition: Articulate features distinctly to eliminate ambiguity, ensuring complex details are accurately machined.
- Pre-Production Analysis: Leverage software tools to conduct pre-production tests, identifying potential issues before they arise in actual production.
Advanced CAD Tools
Selecting the right CAD software enhances design precision and flexibility. Modern tools offer advanced functionalities that improve design efficiency.
- Dynamic Modeling: Utilize dynamic modeling features for quick updates and modifications, allowing rapid adaptation to design changes.
- Built-in Testing Features: Use software with built-in testing capabilities to visualize machining operations and address potential problems before they occur.
By dedicating attention to the preparation of detailed CAD models, manufacturers can significantly mitigate the risk of errors and streamline subsequent processes. This foundational step sets the stage for a successful and efficient 3-axis CNC machining operation.
Step 2: Specify Material Requirements
Choosing the right material is fundamental to achieving the desired outcome in a 3-axis CNC machining project. Materials must align with the part's functional demands and the machining process itself, which requires a thorough understanding of their distinct properties and characteristics.
Evaluating Material Characteristics
Materials such as metals and plastics each offer unique properties that influence machining behavior and application suitability. Metals like aluminum provide excellent machinability and are ideal for applications requiring lightweight strength. Plastics, such as ABS, offer versatility and ease of shaping, making them suitable for a broad range of industries including consumer electronics and automotive components.
- Metals: Known for their robustness and resilience; commonly include aluminum and stainless steel.
- Plastics: Valued for their adaptability and thermal stability; options like ABS and nylon are prevalent.
Economic Impact of Material Selection
Material choice directly affects both the cost of machining and the overall budget. While metals often incur higher initial costs due to their density and durability, plastics may require additional considerations in terms of finish and strength. An informed selection can lead to cost savings by optimizing machining efficiency and reducing tool wear.
- Ease of Machining: Materials that facilitate smoother machining processes can lower operational costs by reducing tool degradation and production time.
- Supply Chain Factors: The availability and sourcing of materials can impact cost, with widely used materials typically offering more competitive pricing and availability.
Precision in Material Specifications
Providing explicit material details when requesting a quote ensures precision in the manufacturing process and cost estimation. Clear specifications help align the capabilities of the machining service with your project's needs, resulting in more accurate quotes.
- Specific Grades and Alloys: Define not only the type of material but also its specific grade or alloy to ensure the correct mechanical properties.
- Dimensional Accuracy: Specify exact dimensions and tolerances to demonstrate the material's appropriateness for your design.
- Finish Requirements: Indicate any surface treatments or finishes required post-machining, which can affect both material selection and cost.
By meticulously specifying material requirements, manufacturers can better optimize production processes, ensuring alignment with design goals and enhancing overall project success.
Step 3: Consider Surface Finishes
Surface treatments are pivotal in defining both the visual appeal and functional integrity of CNC machined components. Selecting the right finish not only enhances appearance but also bolsters the part's resilience against environmental factors. This choice directly affects the component's longevity, making it a vital consideration during the planning phase.
Understanding Surface Finish Options
Various finishing techniques are available, each offering distinct attributes that cater to different application needs. These processes can significantly alter a part’s appearance and durability.
- Hard Coating: Ideal for parts requiring increased hardness and abrasion resistance, hard coating provides a robust layer that enhances durability in demanding environments.
- Electropolishing: This process smoothens and brightens metal surfaces, improving cleanliness and corrosion resistance. It is particularly beneficial for components used in medical and food processing industries.
- Passivation: By removing surface contaminants, passivation enhances the corrosion resistance of stainless steel parts. This treatment is crucial for maintaining the integrity of components exposed to harsh conditions.
- Painting and Plating: These finishes offer aesthetic customization while adding a protective layer against corrosion and wear. They are often used in consumer products to achieve specific visual effects.
Economic Considerations of Surface Finishes
Choosing a surface finish requires balancing cost implications with the benefits each finish provides. Some treatments, like hard coating, may involve higher initial costs due to the processes involved, but can offer long-term savings by extending a part’s service life.
- Process Complexity: The complexity of applying certain finishes can increase costs, but may be justified by the enhanced performance they provide.
- Long-term Savings: Consider the potential for reduced maintenance and replacement costs when evaluating the upfront investment in advanced finishes.
Specifying Surface Finishes in Quotes
When requesting quotes, detailing your surface finish requirements helps ensure accurate pricing and adequate preparation by the machining service provider. This clarity facilitates a more efficient production process.
- Detailing Desired Outcomes: Clearly specify the desired characteristics of the finish, such as smoothness or reflectivity, to guide the provider in achieving your objectives.
- Application Techniques: Describe any preferred methods for applying the finish to ensure consistency with your project’s quality standards.
- Compliance and Standards: Indicate any industry standards or compliance requirements the finish must meet, ensuring compatibility with regulatory guidelines.
By thoroughly considering and specifying surface finishes, you ensure that your components not only meet aesthetic and functional expectations but also align with budgetary and operational goals.
Step 4: Provide Production Volume
Stating your intended production volume clearly is essential for securing precise quotes in 3-axis CNC machining. It not only affects pricing structures but also guides the manufacturing approach and potential cost benefits. By communicating your production requirements, you allow service providers to optimize their processes, enhancing both cost efficiency and production effectiveness.
Influence of Quantity on Pricing
The number of units ordered plays a pivotal role in determining the cost structure of CNC machining projects. Larger orders can lead to reduced costs per unit due to the distribution of fixed expenses over a greater quantity of parts. This efficiency arises from enhanced material management and streamlined production techniques.
- Initial Setup Allocation: The allocation of setup resources across many units helps minimize the cost per part, as these expenses are proportionately lowered with increased production.
- Resource Optimization: By capitalizing on bulk material procurement and improved resource planning, providers can offer more competitive pricing for larger volumes.
- Enhanced Throughput: High-volume orders enable more consistent machine utilization and workflow efficiency, leading to reduced time and labor expenses.
Strategic Volume Planning
Thoughtful planning of production volume can provide significant advantages, particularly when negotiating costs and terms with service providers. Understanding how your volume needs interact with cost dynamics allows for more informed decision-making and effective budget management.
- Negotiation Potential: Larger orders often provide greater leverage in price negotiations, yielding more advantageous terms and conditions.
- Supplier Collaboration: Maintaining open dialogue about volume expectations enhances relationships with providers, ensuring better service and support.
- Market Alignment: Anticipating volume needs in line with market demand helps avoid overproduction, aligning supply with customer requirements.
Conveying Volume Specifications
Accurate communication of your production volume to CNC service providers is crucial for precise quoting and efficient execution. Ensuring clarity in your requirements minimizes misunderstandings and facilitates a smoother production process.
- Detailed Quantity Breakdown: Clearly outline the total units needed, including any variations or batch-specific details.
- Schedule Coordination: Provide an anticipated timeline for production and delivery to synchronize efforts and expectations.
- Adaptability and Growth: Discuss the potential for scaling production to adapt to fluctuating demand without compromising efficiency.
Step 5: Utilize Online Quoting Platforms
In the competitive landscape of CNC machining, online quoting platforms have emerged as game-changers, offering an expedited process for obtaining precise quotes. These digital tools allow manufacturers to swiftly evaluate cost implications and streamline the decision-making process by showcasing a range of competitive options in real-time. This shift to online solutions marks a significant departure from traditional methods that often proved time-consuming and cumbersome.
Unique Benefits of Digital Quoting Tools
By leveraging the capabilities of online quoting platforms, manufacturers can experience unparalleled efficiency in obtaining project estimates. These systems not only reduce lead times but also enhance the precision of quotes through advanced technological features.
- Instantaneous Feedback: Online platforms deliver near-instant feedback on cost estimates, empowering users to make informed decisions swiftly without awaiting lengthy manual assessments.
- Integrated Design Checks: Many tools offer integrated checks for design compatibility, allowing users to preemptively address potential production issues, thereby reducing the likelihood of costly post-quote adjustments.
- Flexible Comparison Metrics: The ability to juxtapose multiple quotes based on customizable metrics ensures that manufacturers select options that best align with their operational and financial objectives.
Essential Features for Optimal Use
Selecting the right online quoting platform involves considering several key features that contribute to a seamless and effective quoting experience. These features not only enhance usability but also ensure that quotes are tailored to specific project needs.
- Intuitive Navigation: A user-friendly interface is crucial, enabling users to effortlessly navigate the quoting process and input necessary data with minimal hassle.
- Advanced Customization: The ability to specify detailed project parameters, such as material preferences and surface finish requirements, ensures quotes are accurately tailored to project specifications.
- Seamless Software Integration: Platforms that integrate smoothly with existing design and management software facilitate a cohesive transition from design to production, enhancing overall efficiency.
Streamlining Processes with Digital Solutions
Incorporating online quoting platforms into your CNC machining workflow can lead to significant operational enhancements. These digital solutions not only improve the speed and accuracy of quoting but also contribute to a more strategic approach to project management.
- Efficiency Through Automation: Automation of the quoting process significantly reduces manual labor, allowing resources to be redirected toward more value-added activities such as design optimization and stakeholder engagement.
- Comprehensive Data Utilization: Access to rich datasets and analytics from previous projects provides valuable insights for refining cost estimates and improving future project planning.
- Global Accessibility and Collaboration: Cloud-based platforms enable access and management of quotes from any location, fostering collaboration among team members and stakeholders across various geographies.
By integrating these advanced online quoting platforms, manufacturers can greatly enhance their operational efficiency, ensuring they receive precise and competitive quotes that align with their strategic goals.
Step 6: Engage in Exceptional Communication
Effective communication with your CNC machining service provider is essential for project success. It involves more than just exchanging information—it's about fostering a collaborative partnership that ensures both parties have a clear understanding of the project requirements. This mutual understanding helps to streamline the manufacturing process and reduce complications.
Building Effective Communication Channels
Creating robust communication pathways is crucial for maintaining a smooth flow of information. This involves choosing appropriate methods and tools to facilitate timely and efficient interaction.
- Consistent Updates: Implement regular progress meetings to discuss project status, tackle any issues promptly, and keep all stakeholders aligned.
- Unified Communication Tools: Use integrated platforms that enable easy access to shared project details, promoting transparency and minimizing errors.
- Clear Contact Points: Designate specific team members to act as communication liaisons, ensuring consistent and responsible exchanges.
Defining Specifications and Expectations
It is vital to communicate all project specifications and expectations clearly from the start to prevent misunderstandings. Detailing every requirement helps set the foundation for successful execution.
- Comprehensive Project Outlines: Develop detailed outlines that cover all project aspects, ensuring the provider comprehensively understands your objectives.
- Expectation Alignment: Discuss and record all expectations, including quality requirements and delivery schedules, to ensure alignment and prevent surprises.
- Feedback Mechanisms: Set up systems for regular feedback, allowing for ongoing assessment and adjustment throughout the project.
Encouraging a Cooperative Environment
Promoting a cooperative approach to communication strengthens the relationship between you and the service provider and enhances project outcomes. This involves cultivating a culture of open dialogue.
- Inviting Expertise: Encourage input and suggestions from the service provider, leveraging their knowledge to refine the project and explore improvements.
- Collaborative Problem Solving: Address challenges collectively, working together to devise solutions that benefit both parties.
- Acknowledging Achievements: Recognize and celebrate key milestones, reinforcing positive collaboration and laying the groundwork for future endeavors.
By prioritizing effective communication, you establish a solid foundation for a successful partnership with your CNC machining provider, ensuring that the final product aligns with your expectations and project goals.
Obtaining accurate quotes for your 3-axis CNC machining projects is a critical step in ensuring the success and cost-effectiveness of your manufacturing endeavors. By following these essential steps and leveraging the right tools and communication strategies, you can streamline the quoting process and secure competitive prices that align with your project goals. If you're ready to take your CNC machining projects to the next level, schedule a demo or try the platform to experience how we can help you optimize your manufacturing processes and achieve exceptional results.