A checklist to help you run an Additive Manufacturing Service Bureau
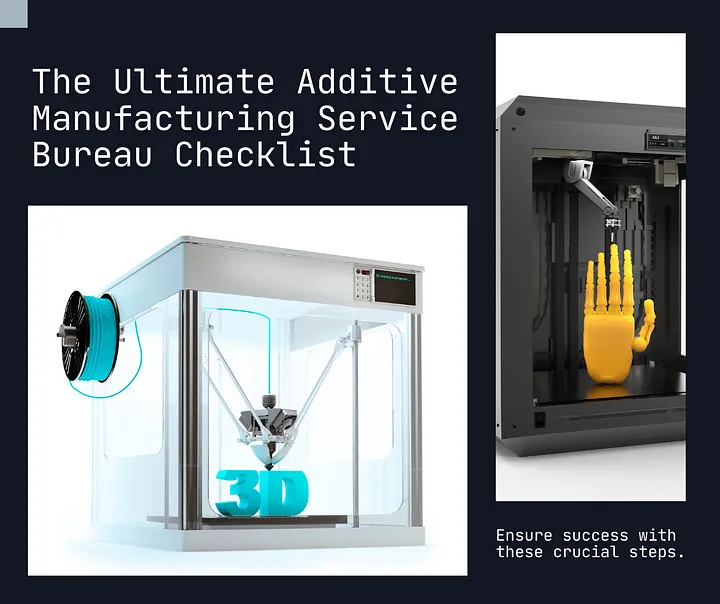
To run an Additive Manufacturing Service Bureau, you must ensure you have the resources and infrastructure to efficiently provide high-quality part production services. This checklist will serve as a guide to get you started on scaling your AM facility to the next level. Here are the necessities:
1. 3D Printers and Equipment: The heart of your operation will be the 3D printers. There are many types of 3D printers, including FDM (Fused Deposition Modeling), SLA (Stereolithography), SLS (Selective Laser Sintering), DMLS (Direct Metal Laser Sintering), and others.
Each has its strengths, weaknesses, and costs. The choice will depend on the products you're planning to produce. Industrial-grade 3D printers will be required for a company due to their speed, reliability, and build quality.
You might invest in a fleet of Stratasys Fortus 450mc printers for FDM printing of durable prototypes or end-use parts and a few Formlabs Form 3 printers for highly detailed resin prototypes.
2. Skilled Workforce: A team of experienced professionals, including 3D printing experts, CAD designers, and customer service representatives. A knowledgeable and talented workforce is essential to deliver quality services and effectively handle customer inquiries.
3. 3D Printing Materials: Stock a variety of 3D printing materials, such as filaments, resins, and powders, to cater to different applications and customer demands. Ensure you have a reliable supply chain for these materials.
Depending on the printers and products, you might need PLA, ABS, or Nylon filaments; Standard, Tough, or Flexible resins; or even specialized materials like metal powders for a printer like the EOS M 290.
4. Computer-Aided Design (CAD) Software: Invest in CAD software licenses to create, modify, and optimize 3D models for printing. Make sure your design team is proficient in using these tools. A designer might use Blender or SketchUp for initial concept designs, then move to SolidWorks CAD or AutoCAD Fusion 360 to finalize the design.
5. Slicing Software: Use slicing software to convert 3D models into printable instructions for your 3D printers. Choose software compatible with your printers and offers the settings for optimal print quality. It can be software like Ultimaker Cura or PrusaSlicer to prepare the design for printing for FDM machines and Materialise Magics or Netfabb for more industrial machines.
6. Post-Processing Equipment: Have the appropriate post-processing equipment, such as tools for removing support structures, sanding, and finishing, to prepare printed objects for delivery.
It could be as simple as a workshop with a sandblaster, drill press, and hand tools or as complex as a dedicated post-processing line with an automatic polishing machine, a paint booth, and a UV curing chamber.
7. Quality Control Tools: Depending on your industry and clients, you may need equipment and personnel to conduct quality control checks, from simple visual inspections to more complex dimensional accuracy checks with tools such as calipers, micrometers, or even more advanced coordinate measuring machines (CMMs) or 3D scanning systems.
For dimensional checks, a quality technician might use Mitutoyo digital calipers and micrometers, a Creaform 3D scanner for more complex geometries, or a Zeiss CONTURA CMM for precise measurements.
8. Safety Equipment: Provide safety equipment, such as gloves, safety glasses, and ventilation systems, to protect your staff from potential hazards associated with 3D printing materials and processes.
9. Storage and Packaging: Set up a proper storage system to organize manufactured parts. Use appropriate packaging materials to protect finished parts during transportation.
10. Online Presence: Create a professional website to showcase your services, share portfolio examples, and provide information about your company. An online presence is essential for marketing and attracting potential customers. One could create a professional website using a platform like WordPress or Shopify.
11. Order Management System: Implement an efficient order management system to track and manage customer orders from inquiry to delivery. Tools like 3YourMind, AMFG, and Phasio can assist with efficient order management of your facility.
12. Business Infrastructure: Have essential office equipment, such as computers, printers, scanners, and administrative tools, to manage day-to-day operations, accounting, and customer communications. For order and inventory tracking, a small business might use QuickBooks or Zoho, while a larger company might implement a full SAP or Oracle ERP system
13. Legal and Regulatory Compliance: Ensure you comply with all relevant local regulations and standards for AM services, product safety, and business operations. If the company prints custom surgical implants, it must adhere to the US FDA’s regulations for additive manufacturing of medical devices or similarly rigorous standards in other countries.
14. Customer Service: Establish a customer service process to handle inquiries, provide quotes, and support clients throughout their engagement with your company. CRM systems like Salesforce or Zendesk to manage customer relationships and support requests.
15. Market Research and Marketing: Conduct market research to identify your target audience and competition. Develop a marketing strategy to promote your services and attract potential customers. You can attend trade shows like the Additive Manufacturing Users Group (AMUG) conference or Formnext to promote its services.
Remember that the specific necessities may vary depending on the scale and scope of your Additive Manufacturing Services. Proper planning and investment in the right resources will set the foundation for a successful and sustainable Service Bureau.