Essential Features of Additive Manufacturing Workflow Software
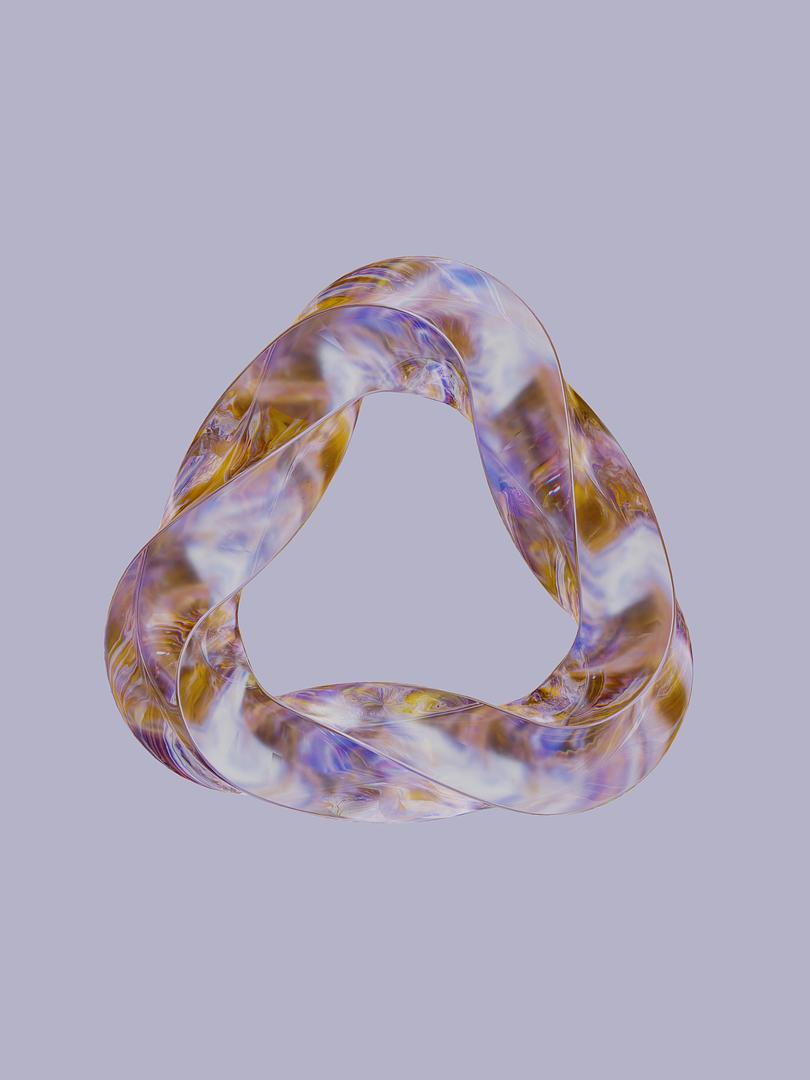
Additive manufacturing, also known as 3D printing, has revolutionized the way products are designed and produced. As the technology continues to advance, manufacturers are seeking solutions to optimize their workflows and streamline the entire process from design to finished part.
Additive manufacturing workflow software has emerged as a critical tool for managing the complexities of 3D printing. These powerful platforms provide a centralized system for overseeing every aspect of the additive manufacturing process, enabling manufacturers to improve efficiency, reduce costs, and deliver high-quality parts faster than ever before.
In this article, we'll dive into the world of additive manufacturing workflow software, exploring its key features, benefits, and how it's transforming the industry. We'll also highlight some of the top solutions on the market and provide guidance on selecting the right software for your organization's needs.
What is Additive Manufacturing Workflow Software?
Additive manufacturing workflow software is designed to support and optimize the entire additive manufacturing process from design to finished part. It plays a critical role in 3D printing workflows, encompassing everything from modeling and simulation to machine control and post-processing.
One of the primary functions of additive manufacturing workflow software is to enable creators to produce fully prepped design files that are ready for printing. This includes tools for optimizing part geometry, generating support structures, and slicing models into printable layers.
In addition to design preparation, additive manufacturing workflow software provides a direct connection to 3D printers. This allows users to seamlessly transfer files, monitor print progress, and control machine settings from a single interface — streamlining the production process and reducing the risk of errors.
Advanced workflow software, like the platform offered at Phasio, takes things a step further by incorporating intelligent automation and data analytics. By leveraging machine learning algorithms, these systems can continuously optimize print parameters, predict maintenance needs, and provide valuable insights into production performance.
Key Benefits of Additive Manufacturing Workflow Software
Additive manufacturing workflow software optimizes production by reducing inefficiencies and enhancing speed. This optimization stems from the software's capability to handle complex tasks with precision, allowing teams to allocate resources more effectively. By minimizing manual input, manufacturers can streamline operations, translating into cost reductions and expedited product delivery.
A unified management system is essential for comprehensive workflow oversight in additive manufacturing. These systems integrate various stages of the manufacturing process into one cohesive framework. This integration facilitates seamless data flow and coordination across teams, reducing errors and improving adaptability to production demands. The outcome is a more synchronized operation that can swiftly adjust to market shifts or production needs.
Enhanced connectivity and cooperation among teams are further supported by workflow software. Utilizing advanced solutions, stakeholders can access and manage information efficiently, irrespective of their location. This capability promotes a dynamic environment where teams collaborate effectively, make data-driven decisions promptly, and address challenges with agility. Improved cooperation not only enhances the manufacturing process's efficiency but also drives product quality and innovation.
Design Optimization Tools
Integrating design optimization tools into the additive manufacturing workflow transforms the production of complex parts. These tools use sophisticated algorithms to enhance structural efficiency and functionality. One key method, topology optimization, refines a part's layout to eliminate excessive material while preserving essential strength and performance characteristics. This approach creates lightweight structures that are both cost-efficient and offer improved mechanical properties.
Generative design expands the horizon of possibilities by automatically generating numerous design alternatives based on defined parameters. Unlike traditional design workflows, this method employs algorithmic power to explore and propose optimal solutions that align with specific performance goals. By utilizing generative design, manufacturers can harness innovative geometric configurations that enhance material efficiency and functionality, resulting in components that excel in both form and function.
Simulation features play a pivotal role by allowing virtual testing of designs under realistic conditions before printing. These tools identify potential challenges like stress points and thermal variances, ensuring that the final product adheres to quality standards. Furthermore, automatic generation of support structures and optimization of part orientation are crucial for efficient printing. These features suggest ideal support placements and orientations, reducing material usage and print time while maintaining part integrity, thus enhancing the overall manufacturing process.
Machine Connectivity and Control
The seamless integration of additive manufacturing workflow software with a broad spectrum of 3D printers ensures efficient file management and enhances remote operation capabilities. This integration allows operators to manage production workflows without being tethered to a single location, thereby improving flexibility and response time to production changes. Supporting various printer models and technologies, these systems enable manufacturers to swiftly adapt to shifting production requirements, ensuring continuity and efficiency in operations.
Advanced monitoring systems provide comprehensive oversight of printing processes, enabling operators to intervene with precision. With capabilities to pause, stop, or modify print settings in real time, these systems minimize material waste and enhance the quality of the output. Access to live data facilitates proactive decision-making, allowing manufacturers to optimize print conditions dynamically and maintain high standards of quality and consistency.
Automation in slicing and G-code generation streamlines the preparation phase, tailoring instructions to the specific printer and material characteristics. By automating these tasks, the software reduces manual input errors and enhances print accuracy. This level of automation enables operators to focus on strategic tasks, ensuring that the manufacturing process is both efficient and capable of producing high-quality results consistently.
Material and Inventory Management
Material and inventory management is crucial for ensuring smooth additive manufacturing operations. A robust material database provides insights into material characteristics, compatible printing technologies, and the best settings for each job. This resource enables manufacturers to choose the right materials and adjust process parameters effectively, promoting both quality and efficiency. By leveraging such a database, operations become more streamlined, reducing waste and enhancing the consistency of production outcomes.
Advanced inventory tracking and management systems are essential to maintain a steady supply of materials and prevent disruptions. These systems keep a close watch on material consumption, automating the reordering process to align with production needs. By utilizing predictive analytics, manufacturers can accurately foresee material requirements, avoiding shortages or excess stock. This proactive approach not only cuts costs but also boosts production efficiency, enabling swift adaptation to market demands or changes in production plans.
Material traceability and genealogy are pivotal for quality assurance and compliance with industry regulations. Maintaining detailed records of material batches, including their source and usage history, ensures transparency throughout the production cycle. This level of traceability allows manufacturers to quickly identify and rectify any quality issues, ensuring that all parts meet stringent specifications. Furthermore, comprehensive genealogy records simplify regulatory audits, demonstrating adherence to industry standards and fostering trust in the manufacturer's commitment to excellence.
Production Planning and Scheduling
Strategic production planning and scheduling are essential for enhancing the operational efficiency and productivity of additive manufacturing systems. Advanced job scheduling solutions leverage real-time data—taking into account factors like machine availability, material constraints, and delivery timelines—to optimize manufacturing workflows. By intelligently distributing tasks across available resources, these systems minimize delays and maximize output, ensuring that production processes remain agile and responsive to market demands.
Emphasizing build volume efficiency, nesting and batching techniques are crucial for optimizing part placements within the build chamber. These methods use intricate algorithms to organize multiple components optimally, reducing material usage and minimizing print times. This granular level of planning enhances the economic viability of high-volume production runs, contributing to faster turnaround times and reduced operational costs, which is particularly advantageous for scaling up manufacturing operations.
Integration with ERP and MES platforms offers a holistic view of the production landscape, facilitating seamless coordination across various stages of manufacturing. This connectivity ensures that all processes—from order initiation to product delivery—are synchronized and efficiently managed. Real-time data sharing between these systems provides manufacturers with comprehensive insights, empowering them to make data-driven decisions that align production schedules with broader business strategies. This integration not only enhances operational agility but also supports continuous improvement initiatives, driving overall productivity gains.
Quality Control and Inspection
Ensuring precision in additive manufacturing involves implementing robust systems that oversee the entire production lifecycle. Advanced in-process monitoring tools provide manufacturers with real-time insights into the manufacturing environment, facilitating immediate adjustments to maintain high quality standards. This proactive strategy not only identifies potential deviations but also mitigates the risk of rework, ensuring each layer of the build adheres to the prescribed specifications.
Utilizing sophisticated dimensional inspection tools automates the verification process, ensuring the final product accurately reflects the original design intent. By employing precise comparison methods with the CAD model, these systems detect even minor discrepancies, ensuring consistency and reliability. This level of automation reduces reliance on manual inspections and accelerates the validation process, enabling manufacturers to adhere to stringent timelines without sacrificing quality.
Integrating quality control processes with comprehensive metrology solutions further enhances inspection workflows. This integration creates a cohesive quality assurance framework, where data from multiple sources coalesces to offer a holistic view of the production process. By leveraging state-of-the-art metrology equipment, manufacturers can conduct detailed analyses efficiently, ensuring each component surpasses industry benchmarks.
Scalability and Customization
In the dynamic landscape of additive manufacturing, systems must be equipped to handle increased production demands and technological advancements. A modular framework is essential in achieving this adaptability, allowing manufacturers to enhance their systems with new functionalities as needed. By incorporating interchangeable components that address specific process requirements, businesses can not only meet current production challenges but also remain agile for future innovations. This flexible approach ensures that technological investments continue to support operational growth and efficiency.
Customization within workflow software extends its value by enabling businesses to configure processes and interfaces that align with their unique operational strategies. Customizable workflows provide the ability to optimize each phase of production, ensuring alignment with business objectives and maximizing efficiency. Tailored user interfaces further enhance usability, offering intuitive navigation and controls that empower teams to leverage the full potential of the software. This personalization fosters a streamlined environment, reducing complexity and promoting productivity.
The integration capabilities of open APIs and SDKs are crucial for creating a cohesive technological ecosystem in additive manufacturing. These tools facilitate seamless connectivity with existing systems, allowing manufacturers to integrate new solutions without disrupting established processes. By enabling communication between diverse software platforms, businesses can create a unified digital workflow that supports informed decision-making. This interoperability extends to third-party applications, expanding the software's utility and versatility, ensuring it remains a pivotal asset as the industry evolves and technology advances.
As the additive manufacturing industry continues to evolve, investing in a comprehensive workflow software solution is essential for staying competitive and maximizing efficiency. By leveraging the power of advanced features like design optimization, machine connectivity, and quality control, manufacturers can streamline their processes and deliver high-quality parts faster than ever before. If you're ready to take your additive manufacturing operations to the next level, schedule a demo or try the platform to experience its capabilities – we're here to help you unlock the full potential of 3D printing and drive your business forward.