Key Considerations for Effective Additive Production Planning
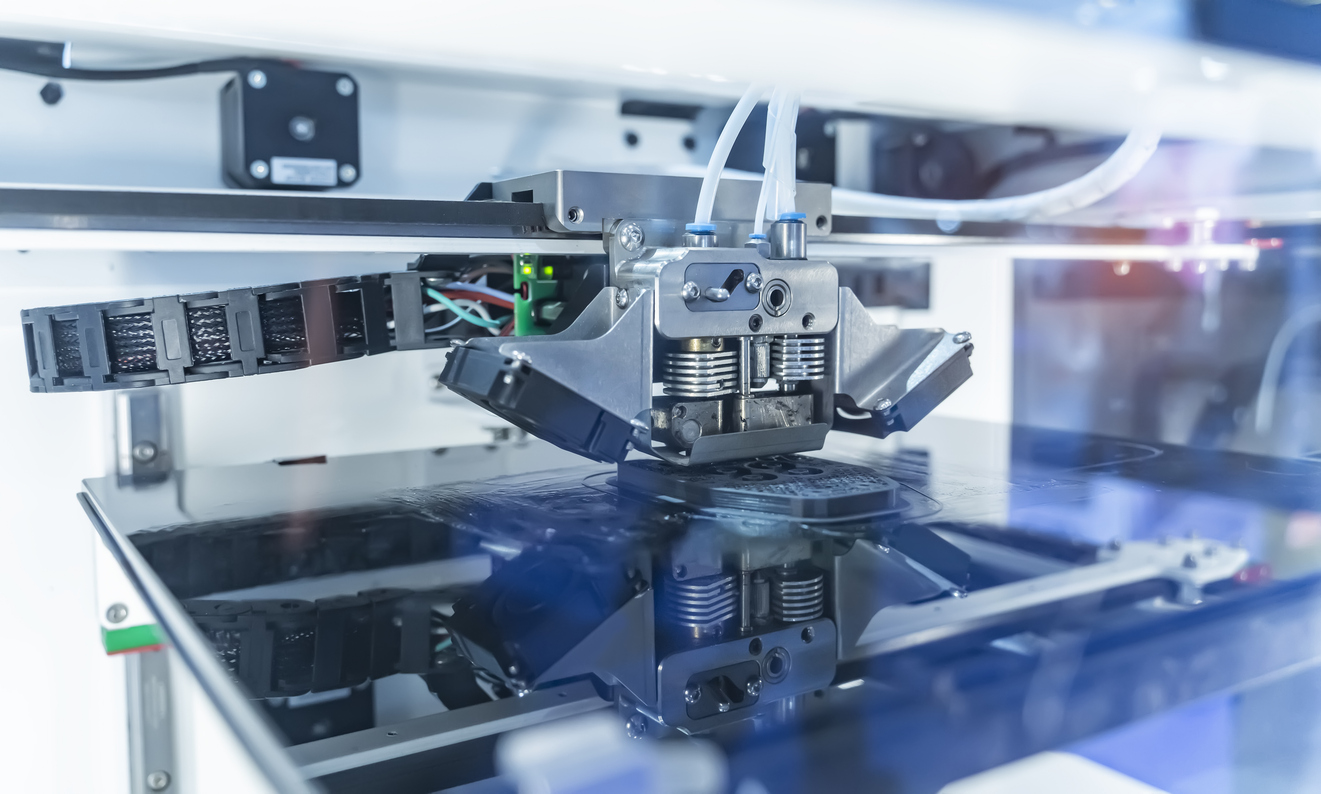
Additive manufacturing, also known as 3D printing, has revolutionized the way products are designed and produced. As this technology continues to evolve and mature, manufacturers are increasingly looking to adopt additive manufacturing processes for large-scale production.
However, integrating additive manufacturing into existing production lines and scaling up operations presents unique challenges. Effective production planning becomes crucial to ensure efficiency, quality, and cost-effectiveness.
In this article, we will explore the key considerations and best practices for additive production planning. We will delve into the strategies and techniques that can help manufacturers optimize their additive manufacturing processes and achieve their production goals.
Defining Additive Production Planning
Additive production planning is the process of coordinating all the required actions once a print run is completed. This encompasses a wide range of activities, including planning post-processing tasks, conducting quality assurance checks, and managing logistics.
The primary objective of additive production planning is to optimize production processes, address challenges, and implement effective strategies to ensure smooth and efficient operations. It involves careful consideration of various factors such as machine utilization, material management, and resource allocation.
Effective additive production planning requires a holistic approach that takes into account the unique characteristics of additive manufacturing technology. Unlike traditional manufacturing methods, additive manufacturing allows for greater design freedom, customization, and complex geometries. However, it also introduces new variables and constraints that need to be considered during the planning phase.
Key Components of Additive Production Planning
To develop a comprehensive additive production plan, manufacturers need to consider the following key components:
- Post-Processing Planning: Additive manufacturing often requires post-processing steps to achieve the desired part quality and functionality. This may include support removal, surface finishing, heat treatment, or assembly. Planning these post-processing tasks efficiently is crucial to minimize lead times and ensure timely delivery.
- Quality Assurance: Maintaining consistent part quality is essential in additive manufacturing. Quality assurance checks need to be integrated into the production planning process to identify and address any issues early on. This may involve implementing in-process monitoring, conducting dimensional inspections, or performing material testing.
- Logistics Management: Additive production planning also involves managing the flow of materials, parts, and information throughout the manufacturing process. This includes inventory management, scheduling, and coordination with other departments or suppliers. Efficient logistics management helps to minimize delays, reduce waste, and ensure smooth operations.
Benefits of Effective Additive Production Planning
By implementing effective additive production planning, manufacturers can reap several benefits:
- Increased Efficiency: Proper planning allows for optimized machine utilization, reduced downtime, and streamlined workflows. This leads to higher productivity and faster turnaround times.
- Cost Reduction: Efficient production planning helps to minimize waste, reduce inventory costs, and optimize resource allocation. This results in lower overall production costs and improved profitability.
- Enhanced Quality: By integrating quality assurance checks into the planning process, manufacturers can ensure consistent part quality and reduce the risk of defects or rework.
- Improved Customer Satisfaction: Effective production planning enables manufacturers to meet customer demands, deliver products on time, and provide a seamless experience, as we strive for at Phasio.
To achieve these benefits, manufacturers need to adopt a systematic approach to additive production planning. This involves leveraging advanced planning tools, data analytics, and automation technologies to streamline processes and make informed decisions.
Integrating Additive Manufacturing with Traditional Processes
Bringing additive manufacturing into harmony with conventional production methods requires a strategic overhaul of workflow management. Traditional manufacturing typically follows a linear progression, where each stage relies on the previous step’s completion. Additive manufacturing diverges from this sequence by enabling concurrent actions and offering flexibility in design and execution. This shift demands a rethink of how production tasks are scheduled and synchronized across the manufacturing landscape.
Innovations in Production Scheduling
To integrate additive manufacturing effectively, it's vital to develop strategies that enable parallel processing of tasks. Additive manufacturing allows for the simultaneous creation of multiple components, which can drastically reduce lead times and increase output. However, it necessitates meticulous coordination to ensure that resources are utilized optimally, avoiding congestion in the production line.
Manufacturers should explore these strategies:
- Simultaneous Production: Utilizing additive manufacturing, various parts of a product can be fabricated at the same time, rather than sequentially. This not only expedites the production process but also facilitates a higher degree of product customization.
- Adaptive Scheduling: Traditional manufacturing often adheres to a rigid timeline with limited flexibility. In a hybrid setting, adaptive scheduling systems can be implemented to respond to shifts in demand, resource availability, or production priorities, requiring real-time analytics for efficient decision-making.
Transitioning Between Manufacturing Methods
A key aspect of marrying additive and traditional manufacturing involves the seamless transition of parts between different process steps. This not only includes the physical handover of components but also the fluid exchange of information and data. By aligning both processes, manufacturers can fully exploit the strengths of each technology.
- System Compatibility: The software and systems used in additive processes should integrate smoothly with existing traditional manufacturing setups, ensuring effective data flow and coordination, thereby minimizing errors.
- Material Compatibility: Manufacturers must evaluate the compatibility of materials used across different manufacturing methods. Understanding their interactions and ensuring they meet quality and performance standards is critical for successful integration.
Weighing Production Time Against Costs
Balancing the advantages of additive manufacturing with traditional methods requires a keen understanding of the tradeoffs between production speed and expenses. While additive manufacturing offers rapid prototyping and flexibility, it may incur higher initial investments. Manufacturers need to assess these tradeoffs to determine the most cost-effective approach for their production goals.
- Financial Analysis: A comprehensive financial analysis helps manufacturers understand the impact of incorporating additive manufacturing. This includes evaluating potential savings from decreased waste, improved efficiency, and accelerated market entry.
- Scalability and Adaptability: With changing production demands, manufacturers must ensure their processes are scalable. Additive manufacturing offers the adaptability to quickly adjust production volumes and accommodate design changes, leading to long-term savings and enhanced market competitiveness.
Integrating additive manufacturing with traditional processes allows manufacturers to leverage the benefits of both technologies. By innovating scheduling strategies, ensuring seamless transitions, and balancing time and cost considerations, manufacturers can create a dynamic and efficient production environment.
Automating Post-Production Management
In the evolving landscape of additive manufacturing, the shift from optimizing production to enhancing post-production processes has become pivotal. This phase encompasses essential activities that ensure products meet quality benchmarks and are market-ready. By automating post-production management, manufacturers can significantly boost efficiency, minimize errors, and improve traceability—creating a seamless and adaptive manufacturing system.
Digitizing Post-Production Processes
The journey toward automation begins with digitizing processes such as tracking parts, ensuring quality, and fostering interdepartmental communication. Transitioning from manual, paper-based procedures to digital platforms enhances data flow and enables real-time updates, resulting in superior accuracy and faster turnaround times.
- Part Tracking: Digital systems employ unique identifiers, like QR codes or NFC tags, to monitor parts throughout production. This reduces manual mistakes and provides instant access to specifications and status, ensuring components are correctly positioned and handled.
- Quality Control: Integrated software solutions enable ongoing monitoring and documentation of quality parameters, offering a comprehensive view of product integrity. Automated checks swiftly identify deviations, allowing for immediate corrective measures to prevent defects from reaching customers.
- Streamlined Communication: Automation enhances communication by centralizing information-sharing platforms. This integration ensures all production stakeholders have access to up-to-date data, promoting collaborative problem-solving and decision-making.
Utilizing Additive Production Software
Implementing software specifically designed for additive manufacturing can streamline workflows and improve overall efficiency. These tools provide features tailored to the unique needs of additive processes, from managing build parameters to optimizing materials and scheduling.
- Task Automation: Cutting-edge software solutions automate post-production task scheduling, aligning with production timelines to minimize bottlenecks and optimize resource allocation, resulting in more streamlined operations.
- Insightful Data: By gathering and analyzing production data, these systems offer invaluable insights for informed decision-making and continuous improvement. Manufacturers can track performance metrics, recognize trends, and implement enhancements that boost productivity and quality.
Leveraging Data Analytics for Continuous Optimization
Data analytics is essential for automating post-production management, offering tools to monitor and continually optimize processes. This involves collecting and analyzing data from various production stages to identify improvement opportunities and implement data-driven strategies.
- Continuous Monitoring: Analytics platforms provide real-time visibility into production activities, enabling proactive tracking and resolution of potential issues, enhancing operational resilience and adaptability.
- Anticipatory Maintenance: Historical data analysis allows manufacturers to predict equipment failures and schedule maintenance activities in advance, minimizing downtime and prolonging the lifespan of essential machinery.
- Efficiency Enhancement: Data analytics enables manufacturers to assess post-production process efficiency and implement targeted improvements, achieving higher productivity and quality levels.
The integration of automation and data analytics in post-production management leads to a more cohesive and efficient manufacturing process. By digitizing workflows, utilizing specialized software, and leveraging data-driven insights, manufacturers can enhance their operations and deliver superior products.
Optimizing Build Orientation and Nesting
Optimizing build orientation and nesting in additive manufacturing is crucial for achieving high-quality results with minimal material waste and reduced production costs. The orientation of parts during the build process can significantly influence mechanical properties and surface finish, impacting both quality and efficiency.
Strategies for Optimal Part Orientation
The orientation of a part on the build platform affects several production parameters. To determine the best orientation, manufacturers must consider:
- Support Material Reduction: Position parts to minimize areas requiring support structures, reducing material usage and post-processing efforts.
- Mechanical Integrity: Align parts to ensure critical features are oriented to enhance strength and stability.
- Thermal Management: Consider heat distribution to prevent issues such as warping or distortion, which can affect part integrity.
Maximizing Machine Utilization through Nesting
Nesting involves strategically arranging parts within the build volume to optimize space utilization and minimize production cycles. Effective nesting strategies can significantly enhance machine productivity:
- Consistent Layer Heights: Ensure uniformity in layer heights across nested parts to streamline the build process and reduce error potential.
- Complex Geometries: Employ advanced software to manage complex geometries efficiently, maximizing build space without compromising quality.
Automating Orientation and Nesting Decisions
Advanced additive manufacturing workflow tools can automate orientation and nesting decisions, using algorithms to assess multiple configurations and identify optimal setups based on specific criteria like material efficiency and production speed.
- Algorithmic Solutions: Implement algorithms that consider production constraints, enabling quick identification of efficient build orientations and nesting arrangements.
- Simulation and Testing: Conduct simulations to validate orientation and nesting plans, ensuring theoretical gains translate into real-world performance.
By focusing on optimizing build orientation and nesting, manufacturers can maximize efficiency and product quality, fully leveraging the benefits of additive manufacturing.
Implementing an Additive Manufacturing Execution System
Deploying an Additive Manufacturing Execution System (AMES) signifies a transformative step toward optimizing production management within additive manufacturing settings. This system acts as a central hub, consolidating essential operations such as data oversight, production scheduling, and equipment regulation, thereby enabling manufacturers to refine workflows and minimize inefficiencies.
Unified Oversight for Improved Coordination
An advanced AMES offers a consolidated view of production data, enabling precise scheduling and control across manufacturing processes. This centralization facilitates cohesive coordination, aligning resources and tasks with overarching production objectives.
- Data Integration: By harmonizing all production data within a singular system, manufacturers gain streamlined access to critical insights, supporting strategic decision-making and resource deployment.
- Dynamic Scheduling: AMES solutions provide adaptive scheduling tools that respond to fluctuating production demands, ensuring resource allocation aligns with operational priorities.
- Equipment Optimization: Centralized machine management enhances performance, minimizes idle time, and ensures output consistency.
Instantaneous Insight for Informed Adjustments
The ability to receive real-time updates characterizes a sophisticated AMES, empowering manufacturers with the agility to detect and address issues promptly. This capability is vital for sustaining operational fluidity and ensuring production activities meet strategic targets.
- Continuous Monitoring: Real-time tracking of production metrics allows for the swift identification and resolution of potential disruptions, maintaining the momentum of production schedules.
- Responsive Adaptation: Utilizing real-time feedback, manufacturers can adjust plans dynamically to accommodate shifts in production needs or unforeseen challenges, preserving efficiency.
Seamless Connectivity for Holistic Tracking
Integrating an AMES with enterprise-wide systems offers a comprehensive view of production, ensuring connectivity and coherence across the manufacturing landscape. This integration fosters a complete traceability framework, linking each stage of the manufacturing process.
- System Cohesion: By interfacing with broader enterprise systems, AMES facilitates a unified operational perspective, encompassing supply chain logistics and customer delivery.
- Complete Traceability: Holistic tracking capabilities ensure manufacturers can monitor every phase of production, from initial material acquisition to final product deployment, guaranteeing quality and compliance.
Implementing an AMES not only streamlines operational processes but also cultivates an environment conducive to continual enhancement and innovation. Through centralized coordination, real-time insights, and comprehensive integration, manufacturers can harness the full potential of additive manufacturing, positioning themselves competitively in the industry.
Addressing Unique Additive Manufacturing Constraints
Navigating the complexities of additive manufacturing requires a deep understanding of the unique constraints associated with this technology. Unlike traditional manufacturing methods, additive manufacturing introduces specific challenges that must be addressed to optimize production efficiency and output quality. These constraints are often tied to the technology's distinct characteristics, demanding a tailored approach to production planning.
Evaluating Technology-Specific Factors
The constraints in additive manufacturing stem largely from the inherent characteristics of the technology, necessitating careful consideration of several critical factors:
- Production Volume Limitations: Each machine's capacity to handle specific part sizes and quantities affects how production is organized. Manufacturers must strategically plan production runs to optimize the use of available space, possibly utilizing modular design approaches to accommodate larger assemblies in phases.
- Material Behavior: The selection of appropriate materials is crucial for ensuring both functional performance and process compatibility. Different materials exhibit unique thermal and mechanical properties, which influence printability and final part characteristics. Manufacturers must account for these variations when selecting materials to achieve optimal results.
- Surface Finishing and Precision: Achieving desired surface finishes and dimensional accuracy often requires additional processing steps. By understanding the specific finishing processes required for different materials and designs, manufacturers can better predict and plan for the necessary time and resources, thereby optimizing workflow efficiency.
Optimizing Production Plans
An effective production plan in additive manufacturing hinges on optimizing processes based on the capabilities of machines and materials. Manufacturers must leverage technological insights to enhance production strategies, ensuring that each element of the manufacturing process is aligned with the technology's strengths.
- Equipment Utilization: A comprehensive understanding of machine capabilities enables manufacturers to maximize throughput and minimize downtime. Implementing predictive maintenance strategies can help maintain optimal machine performance and prevent unexpected disruptions.
- Resource Efficiency: Efficient deployment of materials and energy resources is critical to reducing costs and environmental impact. Advanced software solutions can aid in calculating precise resource needs and minimizing waste, thus contributing to a more sustainable production model.
Balancing Part Quality, Lead Time, and Cost Objectives
Achieving a balance between quality, lead time, and cost is essential to the success of any manufacturing process. In additive manufacturing, this balance requires careful planning and prioritization of production objectives:
- Ensuring Consistency: Implementing stringent quality control measures throughout the production process is vital for maintaining high standards. This includes employing in-line monitoring technologies to detect and correct deviations in real-time.
- Time Optimization: Streamlining production schedules to reduce lead times without sacrificing quality is a key goal. By utilizing advanced planning tools, manufacturers can synchronize production activities and enhance overall efficiency.
- Cost Management: Strategic decision-making in materials, processes, and technologies is required to maintain cost efficiency. Analyzing cost structures and identifying opportunities for savings enable manufacturers to optimize operations while delivering high-value products.
Addressing the unique constraints of additive manufacturing requires a comprehensive approach that considers the interplay of various factors. By focusing on technology-specific challenges, optimizing production plans, and balancing key objectives, manufacturers can unlock the full potential of additive manufacturing and drive innovation across industries.
Leveraging Simulation and Optimization Techniques
Incorporating advanced simulation and optimization strategies into additive manufacturing allows for precise calibration of production processes. By employing state-of-the-art mathematical models and algorithms, manufacturers can craft production plans that are both effective and resource-efficient. These techniques facilitate strategic foresight, enabling businesses to preemptively address potential challenges and streamline operations.
Harnessing Mathematical Models and Algorithms
Mathematical models serve as foundational tools for forecasting and refining production strategies. They provide a structured approach to evaluating outcomes and refining methodologies, ensuring that every aspect of production is optimized for peak efficiency.
- Data-Driven Algorithms: Cutting-edge algorithms synthesize complex datasets to discern the most efficient production routes. This data-centric approach helps balance operational goals with resource limitations to drive productivity.
- Prognostic Evaluation: Utilizing historical and real-time data, predictive models offer insights into future production dynamics, allowing manufacturers to tweak plans in anticipation of market and operational shifts.
Simulating Scenarios for Strategic Insights
Simulation technologies offer a sandbox for testing production strategies under varied conditions. This capability allows manufacturers to analyze the effects of different variables on production outcomes, providing a comprehensive understanding of how to enhance performance metrics.
- Dynamic Scenario Testing: By simulating a range of operational scenarios, manufacturers can pinpoint potential inefficiencies and optimize production schedules. This proactive analysis ensures that operations remain agile and responsive.
- Contingency Development: Simulation tools help identify vulnerabilities and develop robust contingency plans, safeguarding against potential disruptions and maintaining steady production flows.
Continual Plan Optimization
In the rapidly evolving landscape of additive manufacturing, maintaining agility is crucial. Through continuous refinement based on empirical data and operational insights, manufacturers can remain nimble, adapting swiftly to changes in the production environment and consumer demand.
- Responsive Strategy Adjustment: By integrating feedback loops from ongoing operations, manufacturers can fine-tune their strategies to accommodate shifts in production demands, ensuring that processes remain aligned with business objectives.
- Ongoing Iterative Enhancement: Through a process of regular assessment and recalibration, manufacturers foster a culture of innovation and operational excellence, ensuring that they remain competitive and forward-thinking in the dynamic field of additive manufacturing.
By embracing these key considerations and best practices, you can unlock the full potential of additive manufacturing and transform your production processes. As you navigate the complexities of additive production planning, remember that innovation and adaptability are essential for staying ahead in this rapidly evolving industry. If you're ready to take your additive manufacturing operations to the next level, schedule a demo or try the platform to experience how we can help you streamline your workflows and achieve your production goals.