AI will change Machine Shops forever
.png)
CRM, ERP, PLM, ISA95, MES, MRP, what do all of these have in common?
They’re all part of the world of Manufacturing Software and they all play an important role in how manufacturers function. Without software packages such as these, many manufacturers would be unable to provide coordination, traceability and compliance on a production floor which could be staffed by hundreds, or even thousands, of manufacturing experts.
But these software solutions have a serious problem; they’re usually a burden on the people doing the work.
If you’re doing quality control of parts coming off a production line, it’s necessary but also time-consuming to fill out a QMS form for each part. From a software standpoint you can think of this as a User Experience problem — solving the problem is very different to making it a pleasant or even efficient experience.
Furthermore, this is just at the production floor level. Machine shops need a sales team which might be better described as an “education team”.
Manufacturing processes are quite complex and opaque to the general population. We’re often not aware of just how much ingenuity is involved in fabricating the products we use. This poses a serious problem for the sales team of the machine shop, who are basically expected to tell the customer what they need, educate them on why they need it and then get the deal closed.
Truth be told, we shouldn’t blame the world of software either. We’re used to a world of User Experience Design which is “pull-based”, meaning we design on the assumption that the user wants to interact with our software! This is not always the case, especially in manufacturing.
The Burden of Traditional Manufacturing Software
Let’s dive deeper into why these software solutions often become a burden.
Take MES (Manufacturing Execution Systems) for example. While it’s crucial for tracking production processes, it often requires operators to input data manually at various stages of production. This not only slows down the actual manufacturing process but also introduces the possibility of human error in data entry.
Similarly, ERP (Enterprise Resource Planning) systems, while excellent for managing resources across an organization, can be cumbersome when it comes to real-time production floor updates. The disconnect between what’s happening on the shop floor and what’s recorded in the system can lead to inefficiencies and miscommunications.
PLM (Product Lifecycle Management) software, essential for managing a product from inception through engineering design and manufacture, to service and disposal, often suffers from similar issues. The software might be comprehensive, but it’s not always intuitive or easy to use for all stakeholders involved in the product lifecycle.
The result? Employees often view these software solutions as necessary evils rather than helpful tools. They spend significant time inputting data, navigating complex interfaces, and trying to reconcile real-world events with digital records. This time could be better spent on value-adding activities that require human expertise and creativity.
The Sales Challenge in Manufacturing
The complexity of the sales process in manufacturing also presents issues today. Unlike selling consumer goods where the customer often knows what they want, manufacturing sales require a deep understanding of the customer’s needs — needs that the customer themselves might not fully grasp.
Imagine selling custom automotive parts. Your sales team needs to understand:
- The specific requirements of automotive manufacturing
- The customer’s current manufacturing capabilities and limitations
- How their solution fits into the customer’s existing processes
- Regulatory compliance issues in the automotive industry
- The long-term implications of implementing their solution
This level of complexity means that sales cycles in manufacturing can be incredibly long, often spanning months or even years. It’s not uncommon for the sales process to involve multiple stakeholders, from engineers and production managers to C-suite executives.
The sales team often needs to work closely with the engineering team to develop custom solutions. This requires a level of technical knowledge that goes far beyond traditional sales skills. In essence, the sales teams in machine shops often acts as consultants, helping customers solve complex problems rather than simply selling a product.
AI for Machine Shops
The key problem with the software we have seen thus far in manufacturing is that, to be crude about it, it doesn’t really do anything. The software is often working as a kind of “ledger” for recording what happened, but the work itself is done by a person. This leaves the person in a position where they have to do the work and then also tell the machine that they did the work.
AI is pivotal for machine shops because it flips this around. The scope of activities which can be done by the computer is significantly expanded. The computer is able to support us with:
- Educating the customer
- Sending the quote
- Booking the PO
- Scheduling the part into production
- Automated quality control and QMS compliance
This is only now becoming possible due to the multi-modal nature of AI, which enables the computer to talk to the customer, look at a picture of the part, and understand part requirements.
With this additional context, the machine is finally able to bridge the gap between the physical and the digital world and the scope for automation simply explodes. I’ve had some big ideas such as:
- Educating customers through Manufacturing AI: Imagine a chatbot powered by a large language model specifically trained on manufacturing data. This AI could engage with potential customers, answering their questions about manufacturing processes, materials, and capabilities. It could explain complex concepts in simple terms, provide instant quotes based on specifications, and even suggest design modifications to improve manufacturability. This would not only streamline the sales process but also empower customers with knowledge, leading to more informed decisions and potentially shorter sales cycles.
- Computer vision for quality control: AI-powered computer vision systems could revolutionize quality control in manufacturing. These systems could analyze parts coming off the production line in real-time, detecting defects that might be invisible to the human eye. They could learn from historical data to predict potential quality issues before they occur, allowing for preemptive maintenance or process adjustments. This would not only improve product quality but also reduce waste and increase efficiency.
- Predictive maintenance: By analyzing data from sensors on manufacturing equipment, AI could predict when a machine is likely to fail and schedule maintenance before a breakdown occurs. This could dramatically reduce downtime and extend the lifespan of expensive manufacturing equipment.
- Supply chain optimization: AI could analyze global supply chain data to predict potential disruptions and suggest alternative suppliers or routes. This could help manufacturers maintain production even in the face of unexpected events, from natural disasters to geopolitical upheavals.
- Design optimization: AI could analyze countless design iterations, considering factors like manufacturability, cost, and performance, to suggest optimal designs. This could lead to products that are not only better performing but also easier and cheaper to manufacture.
I think there’s going to be a lot developing in this space over the coming years, because manufacturing is full of interesting algorithmic problems too. It could be as simple as efficient scheduling of a sequence of jobs on a machine, but trying to account for things like probability of requirements changing, chance of part failure, etc.
The Future of Manufacturing
As AI technology continues to advance, we can expect to see a gradual transformation of the entire manufacturing landscape.
At Phasio, we have already begun experimenting with AI with our manufacturers. We’ve released Manufacturing AI which is an AI agent for helping manufacturers educate their customers.
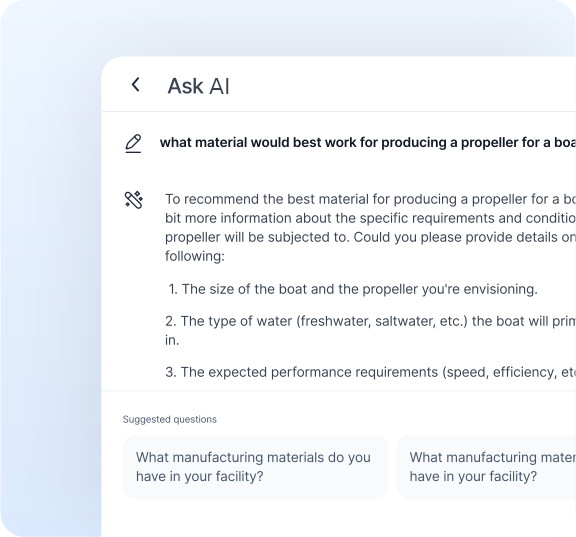
Manufacturing AI is trained using the processes of each manufacturer and can answer questions about their offerings. It’s able to provide support throughout the ordering and requirements gathering process to aid the customer in making their decision.
There are so many interesting questions you can ask to the AI:
- What’s the best material for a boat propeller?
“For a boat propeller, you would ideally want a material that is strong, corrosion-resistant, and able to withstand the mechanical stresses and saltwater environment. Based on the materials we offer, Stainless Steel 316 would be an excellent choice. It is known for its superior corrosion resistance, especially against chlorides like salt, making it ideal for marine applications.“ - Is PLA a suitable material choice for a part to be stored in a hot car?
PLA (Polylactic Acid) might not be the best choice for parts intended to be stored in a hot car. PLA has a relatively low heat deflection temperature (HDT) of around 55°C to 65°C, which means it can start to deform at temperatures commonly reached inside a car on a sunny day. For applications involving high temperatures, materials like ASA might be more suitable due to their higher heat resistance.
Phasio has a live demo of Manufacturing AI on the website now, so you can try it out for yourself. If you’d like to use Manufacturing AI in your machine shop, book a meeting with us to get started!