The Future of Production: Understanding Digital Manufacturing Platforms
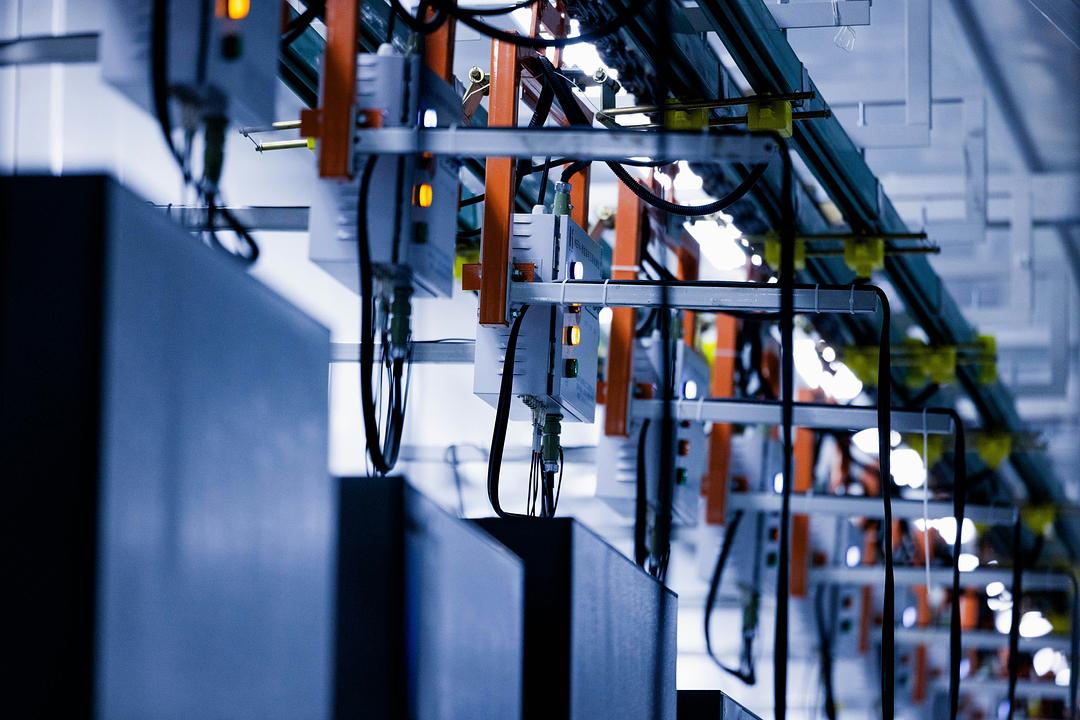
In today's rapidly evolving manufacturing landscape, companies are increasingly turning to digital solutions to stay competitive. The Fourth Industrial Revolution, also known as Industry 4.0, has ushered in a new era of smart manufacturing, where advanced technologies seamlessly integrate with traditional production processes.
At the forefront of this transformation are digital manufacturing platforms—powerful software solutions designed to optimize and streamline manufacturing operations. These platforms harness the power of data, automation, and connectivity to drive efficiency, improve quality, and accelerate innovation.
By leveraging cutting-edge technologies such as the Industrial Internet of Things (IIoT), artificial intelligence (AI), and cloud computing, digital manufacturing platforms are revolutionizing the way products are designed, produced, and delivered. They enable manufacturers to make data-driven decisions, respond quickly to changing market demands, and unlock new levels of productivity and profitability.
What are Digital Manufacturing Platforms?
Digital manufacturing platforms are integrated software solutions that bring together various digital technologies to optimize and automate manufacturing processes. These platforms serve as a centralized hub for collecting, analyzing, and leveraging data from across the manufacturing value chain—from product design and simulation to production planning and execution.
One of the key features of digital manufacturing platforms is their ability to enable real-time data exchange between physical assets and digital systems. By connecting machines, sensors, and devices on the factory floor, these platforms can capture valuable data about production performance, equipment health, and process efficiency. This data can then be analyzed using advanced analytics tools to identify bottlenecks, predict maintenance needs, and optimize resource allocation.
Digital manufacturing platforms also provide a collaborative environment for product design, simulation, and production planning. They allow engineers, designers, and production teams to work together seamlessly, sharing data and insights in real-time. This collaborative approach helps to streamline product development cycles, reduce errors, and improve overall product quality.
Some of the core capabilities of digital manufacturing platforms include:
- Digital Twin Technology: Creating virtual replicas of physical assets and processes to simulate and optimize manufacturing operations
- Production Planning and Scheduling: Automating production scheduling and resource allocation based on real-time data and demand forecasts
- Quality Management: Monitoring production processes in real-time to identify and address quality issues before they impact the final product
- Supply Chain Integration: Connecting suppliers, manufacturers, and customers to enable end-to-end visibility and collaboration across the value chain
By leveraging these capabilities, digital manufacturing platforms help manufacturers to achieve greater agility, responsiveness, and efficiency in their operations. They enable companies to adapt quickly to changing market conditions, optimize resource utilization, and deliver high-quality products to customers faster than ever before.
Key Technologies Driving Digital Manufacturing
Industrial Internet of Things (IIoT)
The Industrial Internet of Things (IIoT) redefines the connectivity of manufacturing environments by establishing a network of interconnected devices. This system enables the seamless flow of data from sensors and machinery across the production landscape. IIoT enhances operational transparency by providing continuous insights into equipment performance, production rates, and resource utilization. By implementing IIoT, manufacturers gain the advantage of remote access to machine health data, allowing them to anticipate issues and maintain optimal performance levels.
The capability of real-time data acquisition opens pathways for advanced maintenance strategies. Manufacturers can implement condition-based maintenance regimes, intervening precisely when necessary to prevent unexpected failures. This strategic alignment of maintenance activities minimizes disruptions and extends the operational life of assets. Furthermore, IIoT data supports the optimization of production workflows, enhancing adaptability to production demands and improving overall process efficiency.
Cloud Computing and Big Data Analytics
Cloud computing, paired with big data analytics, provides the infrastructure to manage and analyze the vast datasets generated by modern manufacturing operations. This combination allows manufacturers to efficiently store and process information, scaling resources according to demand. The cloud's flexibility ensures data accessibility and computational power without the overhead of traditional IT infrastructure.
Big data analytics transforms this wealth of information into strategic insights. By employing sophisticated algorithms, manufacturers can uncover patterns and correlations within their data, leading to enhanced decision-making capabilities. These insights drive improvements in production planning, enable precise demand forecasting, and facilitate resource optimization. Advanced analytics empower manufacturers to fine-tune their operations, reducing waste and maximizing productivity.
Artificial Intelligence and Machine Learning
Artificial intelligence (AI) and machine learning (ML) are pivotal in revolutionizing manufacturing processes by introducing adaptive improvements. AI systems analyze comprehensive datasets to identify inefficiencies and propose optimization strategies autonomously. This automation fosters consistent production quality and enhances throughput by reducing the dependency on manual oversight.
Machine learning continuously refines manufacturing processes by learning from operational data and adjusting parameters to enhance efficiency. This iterative improvement cycle ensures that production systems remain responsive to new challenges, maintaining high standards of quality and reliability. AI and ML integration enables manufacturers to harness precision and adaptability, essential for navigating the complexities of contemporary manufacturing landscapes.
Benefits of Implementing Digital Manufacturing Platforms
Digital manufacturing platforms redefine operational workflows, allowing manufacturers to achieve unparalleled efficiency by integrating cutting-edge technologies. These platforms enhance process automation, effectively reducing bottlenecks and optimizing resource allocation. By leveraging advanced analytics and real-time data, manufacturers can strategically manage production schedules and dynamically adjust operations to meet fluctuating demands—maximizing throughput and minimizing waste.
A standout advantage of implementing these platforms is the elevated precision and consistency in production outputs. By utilizing predictive analytics and sophisticated quality control mechanisms, manufacturers can preemptively address potential issues, ensuring that each product meets exacting standards. This proactive approach not only enhances product quality but also fosters a culture of continuous improvement, positioning manufacturers as industry leaders in innovation and reliability.
Furthermore, the adoption of digital manufacturing platforms fosters a holistic approach to product lifecycle management, bridging the gap between development and production. By facilitating seamless communication and collaboration among cross-functional teams, these platforms enable rapid prototyping and iteration. This synergy accelerates innovation cycles, empowering manufacturers to bring new products to market with unprecedented speed and agility, thereby staying ahead in competitive landscapes.
Challenges and Considerations for Adopting Digital Manufacturing Platforms
Introducing digital manufacturing platforms into existing operations involves navigating several complex challenges that manufacturers must strategically address. A primary concern is the integration of these platforms with existing infrastructure. Many factories operate with a mix of older systems that often lack the capability for seamless integration with modern digital solutions. This situation necessitates a careful approach to harmonize new platforms with legacy technologies, potentially involving the development of bespoke interfaces or leveraging advanced middleware solutions.
Cybersecurity and data privacy stand out as pivotal concerns when connecting factory systems to digital platforms. With increased connectivity comes the heightened risk of cyber threats, emphasizing the need for stringent security measures. Manufacturers must deploy cutting-edge encryption technologies, conduct regular vulnerability assessments, and enforce strict access protocols to protect sensitive operational data. This vigilant approach is crucial for maintaining the integrity of manufacturing data and safeguarding against potential breaches.
The workforce's readiness to embrace digital transformation presents another significant challenge. As digital platforms become central to manufacturing processes, there is an urgent need for employees to develop new competencies in digital tools and data analytics. This shift necessitates comprehensive training programs to upskill the workforce, enabling them to proficiently manage and utilize digital technologies. Manufacturers must foster an environment of continuous learning to equip their teams with the necessary skills for driving innovation.
Investing in digital transformation requires careful financial planning, as significant upfront costs are involved in implementing digital platforms. These costs encompass not only the acquisition of new technologies but also the potential downtime and adjustments necessary during the transition phase. Companies must weigh these initial expenditures against the long-term gains of increased efficiency and competitiveness. This strategic investment underscores a broader commitment to innovation, necessitating both financial resources and a cultural shift towards embracing digital change within the organization.
Industry Applications and Use Cases
Automotive and Aerospace Manufacturing
In the automotive and aerospace sectors, digital manufacturing platforms are pivotal in refining design and production methodologies. These industries employ advanced simulation technologies to conduct exhaustive virtual tests on vehicle and aircraft components, verifying performance metrics before physical manufacturing. This approach allows engineers to address potential design issues early, reducing the need for costly physical prototypes and accelerating development timelines.
Furthermore, these platforms harness real-time information from production environments, enhancing the precision of planning and scheduling activities. By doing so, manufacturers can effectively allocate resources, minimize production disruptions, and adapt swiftly to demand fluctuations, ensuring a seamless flow within the supply chain.
Consumer Goods and Electronics
Digital manufacturing platforms are transforming how consumer goods and electronics are produced by facilitating customization and on-demand production. These platforms enable manufacturers to offer tailored products, catering to individual consumer preferences with unparalleled flexibility. This capability not only elevates customer satisfaction but also opens new avenues for niche market penetration.
Enhanced supply chain transparency is another significant benefit for these industries. Through integrated data sharing across the value chain, manufacturers achieve better synchronization with suppliers and retailers, optimizing inventory levels and reducing lead times. This interconnected approach allows companies to respond adeptly to market trends and consumer demands.
Industrial Equipment and Machinery
In the realm of industrial equipment and machinery, digital manufacturing platforms offer substantial advantages through predictive maintenance and remote asset management. By continuously analyzing equipment performance data, these platforms can forecast maintenance needs, thus avoiding unexpected breakdowns and enhancing operational efficiency.
Moreover, these platforms streamline order processing and quotation workflows by integrating sophisticated manufacturing software. Automated systems provide precise cost estimates quickly, improving customer interaction and boosting sales success rates. This integration enhances the overall efficiency of order fulfillment, ensuring manufacturers can meet market demands with agility and precision.
The Future Outlook for Digital Manufacturing Platforms
Digital manufacturing platforms are set to undergo significant transformations, driven by rapid advancements in AI, IoT, and cloud computing. Emerging AI technologies will offer enhanced capabilities for process automation, enabling platforms to seamlessly adjust to dynamic manufacturing environments. IoT will continue to evolve, creating a more interconnected landscape where devices provide detailed operational data. This comprehensive connectivity will allow for intricate monitoring and fine-tuning of manufacturing processes, ensuring optimal performance and resource management.
The evolution of cloud computing will further bolster the scalability and accessibility of digital manufacturing platforms. Enhanced cloud infrastructure will provide the necessary backbone for handling extensive data volumes and complex computational tasks. This development will support the deployment of advanced applications such as digital twins and real-time simulations, fostering a cohesive approach to production management across multiple locations.
As industries increasingly acknowledge the strategic benefits of these platforms, adoption is expected to rise. Businesses will capitalize on the platforms' abilities to refine workflows, cut costs, and elevate product standards. The seamless integration of real-time collaboration and agile development will lead to innovative business models and service offerings. Insights derived from platform ecosystems will empower manufacturers to customize their outputs, aligning with market shifts and consumer preferences.
Simultaneously, digital manufacturing will drive a shift towards sustainable and circular economy practices. Platforms will empower manufacturers to enhance efficiency, reduce waste, and implement eco-conscious strategies throughout their operations. By incorporating sustainability metrics into their frameworks, manufacturers can achieve reduced environmental impact and foster green innovations. This emphasis on sustainability will not only meet regulatory and consumer demands but also position companies at the forefront of environmentally responsible manufacturing, supported by the evolving capabilities of digital manufacturing platforms.
As the manufacturing industry continues to evolve, digital manufacturing platforms will play an increasingly crucial role in driving efficiency, innovation, and competitiveness. By harnessing the power of advanced technologies and data-driven insights, these platforms are transforming the way products are designed, produced, and delivered. If you're ready to embark on your digital manufacturing journey, schedule a demo or try the platform to experience its capabilities firsthand and see how we can help you unlock new levels of productivity and profitability.