Exploring SLA 3D Printing: Applications and Innovations
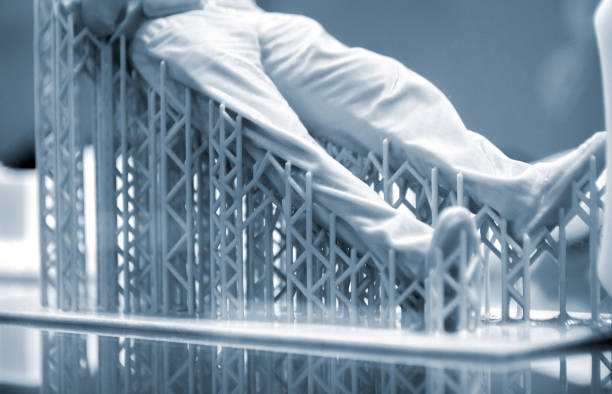
Stereolithography, or SLA, has been a trailblazer in the world of 3D printing since its inception in the 1980s. This technology has revolutionized the way we create prototypes, end-use parts, and intricate designs across various industries.
SLA 3D printing is a highly precise and versatile process that has stood the test of time. It has become a go-to choice for professionals seeking high-quality, smooth-surfaced parts with exceptional accuracy and fine details.
In this article, we will delve into the intricacies of SLA 3D printing, exploring its working principles, materials, applications, and post-processing techniques. We will also discuss the advancements in SLA technology and provide insights on designing parts specifically for this process.
What is SLA 3D Printing?
SLA, short for stereolithography, is a form of vat photopolymerization that utilizes ultraviolet (UV) lasers to cure liquid photopolymer resin into solid plastic parts. The process selectively solidifies the resin layer by layer, creating highly accurate and isotropic parts with smooth surface finishes.
Invented in the 1980s by Charles "Chuck" Hull, SLA is one of the oldest and most established 3D printing technologies. It laid the foundation for the additive manufacturing industry and has since been widely adopted across various sectors.
The SLA 3D printing process offers several advantages over other 3D printing methods:
- High accuracy: SLA can produce parts with very fine features and details, making it suitable for applications that require high precision, such as dental and medical devices.
- Smooth surface finish: The layer-by-layer curing process results in parts with exceptionally smooth surfaces, often eliminating the need for extensive post-processing.
- Isotropic properties: SLA-printed parts exhibit consistent mechanical properties in all directions, unlike some other 3D printing technologies that may have weaker properties along the Z-axis.
SLA 3D printers, like those offered by Phasio, come in various sizes and configurations to suit different application needs. Some printers use a top-down approach, where the laser source is positioned above the resin tank, while others employ a bottom-up orientation, with the light source placed beneath the tank.
SLA 3D Printing Materials
Stereolithography technology utilizes photopolymer resins, which are solidified through light exposure. These resins come in a variety of formulations, each designed to fulfill distinct mechanical, thermal, and optical criteria. This customization capability makes SLA a flexible option for diverse industrial applications, enabling the creation of parts with specialized attributes.
Types of SLA Resins
- Standard Resins: Primarily used for creating prototypes and models, these resins offer excellent detail and finish but lack the specialized properties needed for more robust applications.
- Engineering Resins: Tailored for functional prototypes, these resins deliver improved mechanical characteristics, such as enhanced durability and resistance to heat. They are ideal for simulating the properties of engineering-grade plastics in prototypes.
- Dental/Medical Resins: These materials comply with stringent medical standards, making them suitable for producing precise surgical guides, dental molds, and medical apparatus that demand biocompatibility and accuracy.
- Castable Resins: Designed for use in investment casting, these resins ensure a residue-free burnout, crucial for the creation of detailed jewelry designs and other intricate casting patterns.
- Biomaterial Resins: Intended for applications needing specific biological interactions, these resins are pivotal in research areas like tissue engineering, offering unique material properties tailored for biological applications.
Tailoring Resin Properties
The formulation of SLA resins can be adjusted to exhibit particular traits by modifying their chemical structure. For example, resins designed for high-temperature environments are developed for superior thermal resistance, while those intended for optical applications are optimized for clarity. This adaptability allows manufacturers to choose materials that precisely match their project specifications, ensuring that the final products meet desired performance standards.
SLA 3D Printing Applications
SLA 3D printing is a cornerstone for numerous industries, offering an unmatched ability to produce precise and detailed parts. Its applications span a wide range, from initial concept models to complex functional components. By leveraging SLA technology, businesses can enhance their production capabilities and innovate in ways previously unimaginable.
Prototyping and Product Development
When it comes to developing new products, SLA excels at creating detailed and functional prototypes that facilitate comprehensive testing and evaluation. Designers and engineers can explore complex geometries and fine-tune design elements, ensuring that the final product meets all necessary specifications before moving to large-scale production. This process reduces iteration times and helps avoid costly design flaws.
Dental and Medical Devices
The healthcare sector benefits significantly from SLA 3D printing due to its precision and adaptability. Dental labs utilize SLA to produce accurate dental aligners and prosthetics, which require stringent adherence to patient-specific measurements. Additionally, medical professionals use SLA to fabricate anatomical models, which serve as valuable tools for surgical planning and educational purposes.
Jewelry Casting Patterns
In the jewelry industry, SLA technology allows for the creation of intricate designs with high fidelity. It supports the production of detailed wax patterns used in investment casting, enabling jewelers to achieve designs that are difficult to craft using traditional methods. This capability opens up new creative possibilities for custom and complex pieces.
Automotive and Aerospace Components
SLA plays a crucial role in the automotive and aerospace fields by enabling the fabrication of components that require precision and lightweight properties. The technology supports the development of parts used in aerodynamic testing and fitting trials, as well as certain end-use components where efficiency and weight reduction are key. This allows for the exploration of innovative design solutions and materials.
Consumer Goods and Electronics
For consumer products and electronics, SLA provides an advantageous method for producing prototypes that closely mimic the appearance and function of final products. This is particularly useful for design validation and market testing, allowing companies to gather feedback and make necessary adjustments before entering mass production. The rapid iteration facilitated by SLA ensures that products align with consumer expectations effectively.
Post-Processing SLA 3D Printed Parts
In SLA 3D printing, post-processing is a critical phase that transforms raw prints into high-quality final products. This stage involves a series of precise steps designed to enhance both the appearance and functionality of parts, ensuring they meet industry standards and application requirements.
Cleaning and Curing
The initial step involves removing any residual resin from the printed parts. This typically involves immersing the parts in a solvent bath, such as isopropyl alcohol, which efficiently cleanses the surface and prevents any leftover resin from affecting the final outcome. This cleaning step is crucial for preparing the parts for subsequent processes.
Following cleaning, parts undergo UV curing to complete the polymerization process. This step solidifies the material, enhancing its structural integrity and resistance to environmental factors. The curing process varies depending on resin type and part complexity, ensuring that each part achieves its intended mechanical properties and stability.
Surface Finishing Techniques
Further finishing processes may be applied to meet specific functional or aesthetic criteria. Sanding is often used to refine the surface texture, eliminating any minor imperfections for a smoother finish. For enhanced visual appeal, painting or additional coatings can be applied, offering not only an improved look but also added protection against external elements.
Advanced techniques, such as electroplating or vapor smoothing, may also be employed for specialized applications. These processes can add unique characteristics to the parts, expanding the application possibilities of SLA 3D printing. By thoughtfully selecting and executing these post-processing techniques, manufacturers can ensure their parts are both visually appealing and functionally robust.
Advancements in SLA 3D Printing Technology
Recent advancements in SLA 3D printing technology have significantly broadened its scope and efficiency, enhancing its appeal for various industrial applications. A key development is the ability to print larger components, which allows for the production of substantial parts and assemblies in a single build. This capability not only reduces the need for post-production assembly but also streamlines workflow, making SLA an attractive option for industries requiring large-scale production capabilities.
Innovative Speed and Detail
The evolution in laser systems has led to remarkable improvements in speed and detail capture. Modern SLA printers incorporate dynamic laser scanning methods that optimize the curing process, allowing intricate details to be captured more swiftly and accurately. This technological leap enhances the efficiency of creating complex geometries, making it especially beneficial for applications that demand rapid prototyping and iterative design processes.
Expanded Material Horizons
The development of new resin formulations has opened up a wider spectrum of material possibilities, catering to a diverse range of industrial needs. These include specialized resins that offer unique properties such as enhanced durability, high-temperature resistance, and specific optical characteristics. This expansion allows manufacturers to innovate in their material choices, aligning with the specific performance requirements of advanced applications in fields like electronics and consumer goods.
Designing for SLA 3D Printing
Creating designs optimized for SLA 3D printing involves a strategic approach to maximize the quality and efficiency of the final product. A critical component is determining the optimal orientation of parts during the printing process. This consideration profoundly influences the surface quality, ease of support removal, and efficiency of the build process. Proper orientation minimizes both the use of support materials and post-processing efforts, thereby enhancing the overall finish and reducing production time.
Optimizing Part Orientation and Support Structures
Strategic part positioning within the build volume is essential for achieving superior results in SLA printing. By carefully aligning parts to minimize support requirements, you can significantly reduce surface blemishes and streamline post-processing. This approach also ensures consistent exposure to the curing laser, enhancing layer adhesion and part durability.
When supports are unavoidable, their placement should be carefully planned to ensure straightforward removal. Ideally, supports should be positioned on less critical areas or surfaces that will undergo further finishing, such as sanding or coating. This strategy preserves the integrity of the design and minimizes the risk of damage during support detachment.
Addressing Overhangs, Bridges, and Drainage
Effective SLA design minimizes unsupported overhangs and bridges, which can lead to sagging or incomplete curing. Incorporating gradual angles and transitions helps support these features naturally, while strategic support placement maintains their structural integrity throughout the printing process.
Incorporating drainage holes is another crucial design element. These holes facilitate the removal of uncured resin from internal cavities, ensuring complete curing and preventing material waste. Proper drainage design also contributes to reduced print time and material usage, enhancing overall production efficiency.
Leveraging Isotropy for Complex Designs
SLA technology's capability to produce isotropic parts with uniform properties throughout enables designers to create complex geometries and consolidated assemblies that traditional manufacturing methods cannot achieve. By integrating multiple components into a single print, designers can reduce assembly complexity and enhance part performance through improved structural integrity.
Utilizing isotropy in design considerations allows exploration of innovative solutions that capitalize on SLA's precision and material properties. This strategy not only broadens the applications of SLA technology but also fosters advancements in product development and manufacturing processes, leading to more refined and efficient designs.
As we continue to push the boundaries of SLA 3D printing, its applications and innovations will undoubtedly expand, revolutionizing the way we approach manufacturing and product development. By leveraging the advancements in materials, speed, and design optimization, you can unlock new possibilities and stay at the forefront of this transformative technology. If you're ready to explore how SLA 3D printing can elevate your manufacturing processes, schedule a demo or try the platform to experience its capabilities firsthand – we're here to help you every step of the way.