Key Steps to Enhance Your FDM Workflow Efficiency
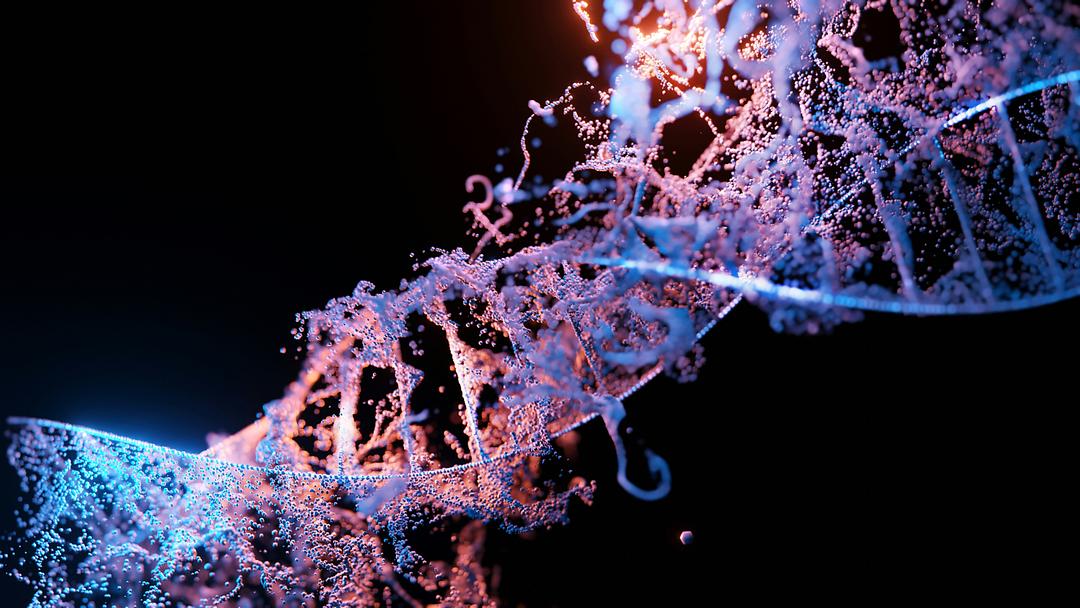
Fused Deposition Modeling (FDM) has revolutionized the manufacturing landscape, offering a cost-effective and efficient solution for producing high-quality parts and prototypes. As the demand for additive manufacturing grows, optimizing the FDM production workflow becomes crucial for businesses looking to stay competitive.
Implementing a streamlined FDM workflow can significantly enhance productivity, reduce lead times, and improve overall part quality. By understanding the key principles and best practices involved in each stage of the process, manufacturers can unlock the full potential of FDM technology.
In this article, we will explore the essential steps to enhance your FDM workflow efficiency, from design optimization to post-processing techniques. We will also discuss common challenges and provide tips for maintaining a consistent and reliable production process.
What is FDM Production Workflow?
FDM production workflow is a systematic approach to utilizing Fused Deposition Modeling technology for manufacturing processes. It involves a series of steps that optimize the printing process, from initial design to final product, ensuring efficiency and quality in production.
The FDM workflow encompasses several critical stages: design optimization, material selection and preparation, printer calibration and setup, slicing and printing parameters, post-processing, and troubleshooting. Each stage plays a vital role in achieving the desired results and maintaining a streamlined production process.
By adopting a comprehensive additive manufacturing workflow, manufacturers can streamline their operations, reduce waste, and improve overall productivity. This approach allows for greater flexibility in design, faster iteration cycles, and the ability to produce complex geometries that would be challenging or impossible with traditional manufacturing methods.
How to Enhance Your FDM Workflow Efficiency
Improving the efficiency of FDM processes calls for a methodical approach that leverages the capabilities of additive manufacturing. A well-structured system not only enhances operational flow but also capitalizes on the strengths of FDM technology. Key to this is an understanding of design adaptations specific to FDM, strategic material choices, precise equipment tuning, and fine-tuned slicing parameters.
Establishing an Integrated Additive Manufacturing System
Creating a cohesive system is essential for effective FDM operations. Begin by aligning all stages of production—from initial design through to post-processing—into a unified process. This approach ensures smooth transitions between phases and minimizes potential delays. Utilizing management tools can assist in monitoring progress, pinpointing inefficiencies, and enhancing team collaboration.
Essential Elements for FDM Workflow Enhancement
- Tailor Designs for FDM: Adapt designs to reduce the need for excessive support structures, which conserves material and shortens print duration. Use CAD solutions to refine models, ensuring they suit the specific properties of selected materials.
- Strategic Material Selection: Select materials that align with both the design and the intended function, taking into account attributes such as durability, elasticity, and heat tolerance. Proper material handling and storage are crucial to maintaining quality.
- Precise Equipment Adjustment: Regularly adjust and calibrate equipment to maintain consistent performance and quality. This includes tasks like leveling the print bed and aligning the nozzle to avoid common issues like misalignment or warping.
Implementing these strategies empowers manufacturers to significantly enhance FDM production, resulting in quicker project turnarounds and superior product quality. This method not only harnesses the benefits of FDM technology but also enables businesses to swiftly meet market demands and foster ongoing innovation.
Step 1: Optimize Design for FDM
Crafting designs that align with FDM’s unique capabilities is essential for maximizing production efficiency. The design process must account for FDM’s layer-by-layer approach, ensuring that each component is both functional and conducive to a smooth printing process. This requires a keen understanding of how FDM's additive nature impacts the final product's geometry and integrity.
Implement FDM-Specific Design Adjustments
Designs should incorporate strategies that leverage FDM's strengths while addressing its constraints. This involves:
- Minimizing Support Requirements: Evaluate part orientation and incorporate design elements that naturally support themselves. This reduces the need for additional structures, conserving material and decreasing print time.
- Optimizing Structural Features: Use advanced CAD tools to refine structural elements of the design, focusing on essential features that enhance part functionality without adding unnecessary complexity.
Integrate Material Characteristics into Design
Choosing the appropriate material is integral to design success. Each filament used in FDM presents unique properties that influence the printing process and final part quality:
- Design-Material Synergy: Ensure that the design takes full advantage of the material's properties. For instance, some materials may offer superior strength but require specific design modifications to mitigate issues like warping or shrinkage.
- Layer Bonding: Tailor the design to enhance inter-layer adhesion by adjusting parameters such as wall thickness and infill geometry, ensuring that the part maintains its structural integrity throughout its lifecycle.
By embedding these considerations into the design phase, manufacturers can produce FDM parts with enhanced performance and efficiency, facilitating a more seamless and productive workflow. This approach leads to faster iterations and superior quality outputs, fully harnessing the potential of FDM technology.
Step 2: Material Selection and Preparation
Choosing the most suitable materials is a crucial step in advancing FDM workflow efficiency. This choice impacts the part's performance and appearance, necessitating a careful evaluation of available thermoplastics. Each material comes with distinct properties that must match the specific demands of the project, ensuring the finished product is both functional and reliable.
Key Considerations for Material Selection
Evaluating filament options involves a detailed assessment of their intrinsic qualities to ensure alignment with project goals. Important aspects include:
- Application-Specific Requirements: Identify materials based on the intended use—such as choosing Nylon for parts requiring high impact resistance or ASA for outdoor applications due to its UV stability.
- Processing Ease: Consider the ease of printing with specific materials. PLA is favored for its user-friendly nature, making it ideal for quick prototypes with less focus on mechanical properties.
Maintaining Material Quality
Ensuring the quality of materials throughout the FDM process is essential for consistent results. Poor storage or handling can lead to compromised prints, so adhere to these practices:
- Optimal Storage Practices: Keep filaments in airtight containers with desiccants to prevent moisture uptake, which can cause defects like stringing or weak adhesion.
- Consistent Quality Checks: Regularly test and verify filament quality before printing to ensure optimal performance and avoid unexpected print failures.
Implementing these strategies in material selection and preparation enhances the reliability and quality of FDM-produced parts, fostering a more efficient and effective workflow.
Step 3: Printer Calibration and Setup
Achieving optimal results in FDM production hinges on meticulous printer calibration and setup. These foundational steps ensure that the printer's performance aligns with the desired quality and precision, reducing the likelihood of errors during the printing process.
Critical Calibration Procedures
Ensuring the printer is finely tuned involves several essential procedures:
- Platform Leveling: This step is crucial to ensure that the initial layer adheres uniformly, preventing defects such as warping or layer shifting. A level platform supports even material distribution and enhances layer cohesion.
- Extruder Calibration: Aligning the extruder accurately is vital for consistent filament flow. Proper calibration avoids issues like under-extrusion or over-extrusion, which can compromise the part's dimensional accuracy and surface finish.
Maintaining Optimal Printing Conditions
Beyond calibration, maintaining the right environmental conditions is essential for reliable output. Considerations include:
- Stable Temperature Environment: Controlling the ambient temperature around the printer helps maintain consistent material properties. This stability reduces thermal fluctuations that can lead to print defects.
- Routine Equipment Checks: Regular inspection and cleaning of key printer components, such as the build surface and extruder, are necessary to prevent build-up and ensure smooth operation. Scheduled maintenance helps sustain the printer's efficiency and extends its operational lifespan.
By implementing these detailed calibration and setup strategies, manufacturers can achieve consistent, high-quality FDM prints, supporting an efficient and reliable production workflow.
Step 4: Slicing and Printing Parameters
The slicing phase translates a digital design into precise instructions for the FDM printer, determining both the efficiency and quality of the final print. This stage requires careful calibration of settings to align with production objectives, ensuring that both speed and detail are optimized.
Key Slicing Adjustments
Several parameters must be carefully selected to tailor the printing process:
- Layer Thickness: This defines the vertical resolution of the print. Thinner layers yield finer detail and smoother surfaces, ideal for intricate designs. In contrast, thicker layers expedite the printing process, making them suitable for less detailed models.
- Print Velocity: Finding the right balance between speed and quality is crucial. Higher velocities reduce print times but may affect detail and finish. Slower velocities enhance precision and strength, requiring a strategic approach based on project needs.
- Thermal Settings: Proper temperature control for both the nozzle and build surface is essential to prevent defects such as warping or material breakdown, ensuring part stability and aesthetic appeal.
Streamlining Workflow through Efficient Slicing
Enhancing workflow efficiency involves strategic slicing adjustments:
- Dynamic Layering: By implementing variable layer heights based on model complexity, one can optimize for time and detail, applying finer layers to complex features while using thicker layers for simpler sections.
- Infill Optimization: Adjusting infill patterns and densities allows for a balance between mechanical strength and material economy. Denser infills enhance structural integrity, while lighter patterns conserve material and increase speed.
By refining these slicing and printing parameters, manufacturers can significantly enhance the output quality and overall efficiency of the FDM process, aligning production capabilities with market demands while maintaining high standards of quality.
Step 5: Post-Processing for Quality Enhancement
In the realm of FDM production, post-processing serves as a crucial step to elevate the final quality of printed parts. This phase aims to refine the surface and enhance the structural integrity of components, ensuring they meet the desired standards of performance and aesthetics. By employing targeted techniques, manufacturers can significantly improve the functionality and appearance of their parts.
Techniques for Surface and Strength Enhancement
Several post-processing methods can be employed to achieve smooth surfaces and reinforce part strength:
- Mechanical Finishing: Utilizing tools like sanders or rotary buffers helps in smoothing out visible layer lines and minor defects. Starting with lower grit levels for initial smoothing, and transitioning to higher grits for a refined finish, ensures a uniform appearance.
- Chemical Smoothing: For materials such as ABS, applying controlled solvent exposure can yield sleek, polished surfaces. This method effectively removes surface roughness, resulting in a visually appealing finish without compromising dimensional accuracy.
- Coating Applications: Applying protective coatings or paints enhances the visual appeal and durability of the part. Using primers ensures proper adhesion, while successive layers of paint or sealant provide additional customization and protection against environmental factors.
Implementing a Quality Control Checklist
To ensure each part meets stringent quality standards, a structured checklist is vital:
- Comprehensive Evaluation: Conduct thorough inspections focusing on both visual aspects and dimensional accuracy. Ensure critical features align with design specifications for consistency across production runs.
- Rigorous Testing: Engage in mechanical testing to confirm the structural capabilities of the part. This step is essential for parts expected to endure significant stress or load during use.
- Detailed Process Documentation: Maintain accurate records of post-processing activities and outcomes. Documentation supports traceability and continuous improvement efforts, allowing for process optimization based on historical data.
By systematically applying these post-processing techniques and adhering to a meticulous quality control framework, manufacturers can ensure their FDM-produced parts are ready for a variety of demanding applications, meeting both functional and aesthetic requirements.
Step 6: Troubleshooting Common FDM Challenges
Effectively navigating the challenges in FDM production requires precise identification and targeted problem-solving strategies. Issues such as warping, layer separation, and extrusion inconsistencies present distinct challenges that need careful attention to maintain production quality. Each of these problems has specific indicators and underlying causes that can be addressed with tailored solutions to ensure smooth operations.
Diagnosing and Addressing Typical FDM Issues
A systematic approach to diagnosing issues is essential. Warping, often caused by uneven cooling or suboptimal bed adhesion, and layer separation, potentially due to incorrect temperature settings or filament quality, demand specific interventions:
- Improve Bed Adhesion: Use adhesives or specialized build surfaces to enhance initial layer contact, reducing the likelihood of warping.
- Adjust Temperature Settings: Align nozzle and build plate temperatures with filament specifications to prevent layer separation, ensuring better interlayer bonding.
Strategies for Sustaining Workflow Efficiency
To maintain an efficient workflow, it is vital to anticipate challenges and implement preventive measures. Regularly scheduled maintenance and keeping a stock of critical components can prevent minor issues from escalating. Detailed records of print parameters and outcomes also facilitate the identification of recurring issues, enabling process improvements.
Assuring Quality and Consistency
Consistency in FDM production is achieved through proactive quality assurance practices and adherence to standardized procedures. Establishing a routine for calibrations and inspections helps ensure that each print adheres to strict quality benchmarks. By systematically addressing common challenges, manufacturers can maintain the reliability and quality of their FDM operations, driving continuous improvement.
Tips on Maintaining an Efficient FDM Workflow
Regularly Update Software and Firmware
For optimal performance in FDM workflows, it's vital to keep your equipment's software and firmware up to date. Updates often bring enhancements that bolster system performance, improve user interfaces, and integrate new capabilities that streamline the printing process. Staying current with these updates helps ensure reliable operations and maximizes the potential of your FDM equipment.
- Leverage Cutting-edge Features: Regular updates introduce features that enhance print quality and production speed, reflecting the latest advancements in FDM technology. This continual enhancement can lead to more precise control over printing parameters and improved overall efficiency.
- Ensure Operational Resilience: Proactive updating mitigates the risk of unexpected issues that can impede workflow. Consistent performance and reduced downtime are critical for meeting production goals and maintaining high standards of output quality.
Continuous Learning and Adaptation
The field of FDM is ever-evolving, with continuous innovations that can significantly impact production methods. Keeping abreast of these developments is essential for maintaining a competitive edge. Engaging in educational opportunities, such as webinars and industry conferences, offers insights into cutting-edge practices and emerging technologies.
- Integrate New Methodologies: By incorporating the latest methodologies, manufacturers can enhance both the efficiency and effectiveness of their workflows. This might involve adopting new printing strategies or exploring advanced material options that offer unique benefits.
- Cultivate Expertise and Agility: Promote a culture where ongoing learning is prioritized, and team members are encouraged to expand their skillsets. This approach not only boosts individual capabilities but also drives innovation, enabling the organization to swiftly adapt to changes in FDM manufacturing techniques.
Enhancing your FDM workflow efficiency is an ongoing process that requires continuous learning, adaptation, and a commitment to implementing best practices. By optimizing each stage of the production process, from design to post-processing, you can unlock the full potential of FDM technology and drive your manufacturing operations to new heights. If you're ready to take your FDM workflow to the next level, schedule a demo or try the platform to experience how we can help you streamline your processes and boost your productivity.