Best Practices for Ensuring FDM Print Quality
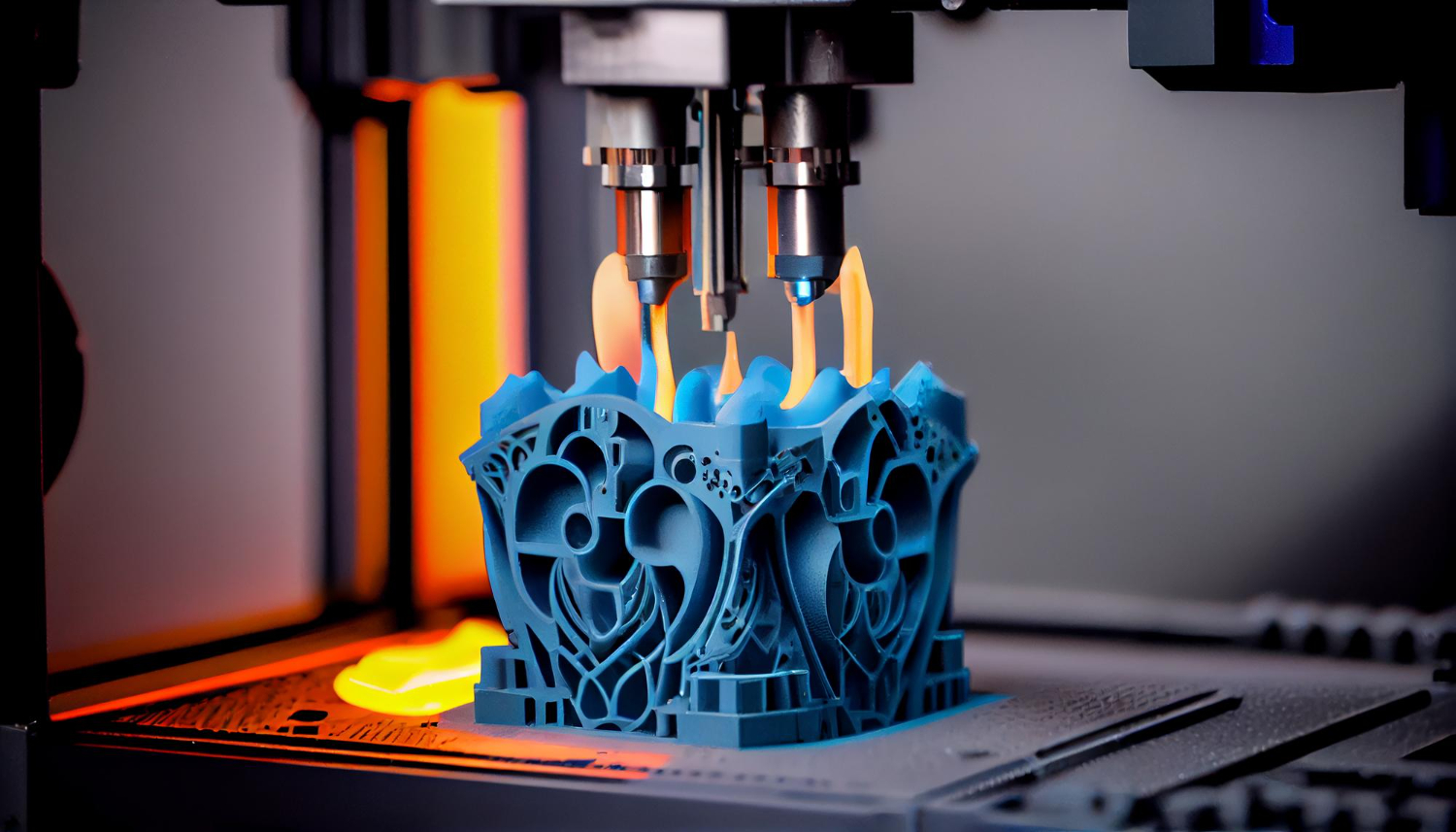
Fused Deposition Modeling (FDM) has revolutionized the manufacturing industry by enabling the rapid production of complex parts and prototypes. However, ensuring the quality and accuracy of FDM-printed components remains a critical challenge for manufacturers.
To unlock the full potential of FDM technology, it is essential to understand the factors that influence print quality and implement effective verification methods. By adopting best practices and utilizing advanced tools, manufacturers can significantly enhance the reliability and precision of their FDM-printed parts.
In this comprehensive guide, we will explore the key aspects of FDM quality verification, providing insights into optimizing printer settings, selecting high-quality materials, and implementing robust quality control measures. Whether you are a seasoned professional or new to FDM printing, this article will equip you with the knowledge and strategies to achieve exceptional results consistently.
What is FDM Quality Verification?
FDM quality verification is a critical process that involves assessing and ensuring that 3D printed parts meet specific quality standards. It encompasses a range of techniques and methods designed to evaluate the dimensional accuracy, surface finish, layer adhesion, and overall integrity of FDM-printed components.
The primary goal of FDM quality verification is to identify and address any defects or inconsistencies that may impact the functionality, durability, or aesthetic appeal of the printed parts. By implementing rigorous quality control measures, manufacturers can minimize the risk of producing subpar components, reduce waste, and improve customer satisfaction.
FDM quality verification typically involves a combination of visual inspections, dimensional measurements, and functional testing. Visual inspections allow operators to identify surface imperfections, layer separation, or other visible defects. Dimensional measurements, using tools such as calipers or micrometers, help ensure that the printed parts meet the specified tolerances and geometrical requirements. Functional testing, on the other hand, assesses the performance of the printed components under real-world conditions, verifying their strength, durability, and intended functionality.
To facilitate effective FDM quality verification, manufacturers often rely on specialized software tools and automated inspection systems. These solutions streamline the verification process, providing detailed analysis and reporting capabilities. For instance, Phasio offers a comprehensive platform that integrates quality verification features, enabling manufacturers to optimize their FDM printing workflow and ensure consistent, high-quality results.
Implementing a robust FDM quality verification process is crucial for manufacturers seeking to leverage the benefits of additive manufacturing. By detecting and addressing quality issues early in the production cycle, manufacturers can reduce costs, minimize rework, and accelerate time-to-market. Moreover, by delivering reliable and precise FDM-printed parts, manufacturers can enhance their reputation, gain a competitive edge, and meet the evolving demands of their customers.
How to Ensure FDM Print Quality
Achieving optimal FDM print quality requires a thorough understanding of the technology's nuances and a commitment to precision. One crucial aspect is the meticulous calibration of the 3D printer. Adjusting the extruder's flow rate and ensuring the build platform's levelness can significantly impact the print's final appearance and accuracy. Additionally, using the correct infill patterns and densities can enhance both the structural integrity and aesthetic quality of the prints.
Material selection plays a pivotal role in the printing process. Opting for filaments with stable thermal properties and consistent mechanical characteristics can prevent common issues like warping or uneven extrusion. Proper storage conditions—such as maintaining low humidity environments—are essential in preserving the filament's quality. Techniques like pre-drying filaments can further improve their performance during printing by reducing moisture-related defects.
Incorporating advanced inspection techniques is vital for maintaining high standards in FDM printing. Non-destructive testing methods, like ultrasonic or X-ray analysis, can reveal internal inconsistencies or defects without damaging the part. Automated vision systems can also streamline the inspection process, providing precise feedback on dimensional conformity and surface quality. By integrating these advanced practices, manufacturers can ensure that every print meets the stringent demands of modern manufacturing.
Step 1: Optimize Printer Settings
To enhance the quality of FDM prints, refining printer settings is crucial. Begin by tailoring the layer height to achieve the desired balance between resolution and efficiency: a smaller layer height delivers finer detail and smoother finishes, while a larger height can expedite the process. It's essential to manage print speed with precision; a reduced speed often results in higher detail accuracy and improved layer bonding, whereas an increased speed may lead to potential inconsistencies or defects like skipped layers or incomplete sections.
Adjusting the nozzle temperature is another critical factor. Each filament exhibits a specific temperature range that optimizes its flow and bonding characteristics. Insufficient heat can compromise interlayer adhesion, resulting in structural weaknesses or separation. Excessive heat, on the other hand, might lead to issues such as stringing or over-extrusion, impacting the precision of the print. Reviewing material specifications and conducting test prints helps in pinpointing the ideal temperature setting.
Calibration forms the backbone of effective and consistent FDM printing. Regularly fine-tuning the printer ensures alignment and stability, preventing common issues like shifts or layer misalignments. Strategies such as regularly checking the tension of belts and confirming the accuracy of the Z-axis offset contribute to maintaining dimensional precision. Furthermore, ensuring the extruder delivers consistent flow by adjusting feed rates and verifying nozzle cleanliness can significantly enhance print outcomes.
Step 2: Use High-Quality Materials
Investing in high-quality materials is crucial for enhancing the performance and reliability of FDM prints. Opt for filaments that offer uniform thermal properties and mechanical consistency, which contribute to achieving precise and repeatable results. Look for materials that are specifically engineered for FDM processes, providing enhanced bonding and reduced shrinkage. This focus on quality minimizes the risk of defects and ensures that each print meets the desired specifications.
Proper management of materials can significantly influence the final print quality. Store filaments in controlled environments to protect them from external factors that might affect their properties. Utilize specialized storage solutions that include temperature regulation to maintain the material's integrity over time. Implement practices such as using vacuum-sealed bags with desiccants to prolong the life of your filaments and reduce the likelihood of print failures due to environmental exposure.
Maintaining the cleanliness of materials is essential for consistent results. Implementing advanced filtration techniques, such as inline filament filters, can effectively remove dust and particulates before they reach the extruder. By ensuring only clean material enters the printer, these methods help maintain nozzle efficiency and reduce wear. This approach to material management plays a vital role in achieving high-quality prints, supporting the overall reliability and efficiency of the FDM process.
Step 3: Implement Effective Quality Control Measures
For consistent FDM print quality, integrating thorough inspection protocols is essential. Utilizing three-dimensional scanning technologies can provide a comprehensive view of the printed part, capturing intricate details that traditional measuring tools might miss. These systems allow for an in-depth comparison between the digital model and the physical print, ensuring that every dimension aligns with the intended design without manual intervention.
Surface evaluation is crucial for identifying flaws that may not be immediately apparent. Employing techniques such as dye penetrant testing can reveal micro-cracks or surface irregularities that compromise the print's integrity. This method highlights defects by applying a contrasting dye, making it easier to pinpoint and address issues before the part enters further stages of production or application.
Advanced analytical software can streamline quality control by offering predictive insights and automated reporting. These platforms utilize algorithms to assess the consistency of print parameters, offering alerts for any deviations that might affect quality. By integrating these systems into the workflow, manufacturers can enhance their ability to preemptively address potential issues, thereby optimizing the FDM process for reliability and efficiency.
Step 4: Post-Processing and Finishing
In FDM printing, post-processing refines raw prints into polished, ready-to-use components. Techniques such as precision sanding and buffing are essential for enhancing surface aesthetics by removing visible layer lines and minor defects. Employing varying grit sequences—starting with medium grit for initial smoothing and progressing to fine grit for a polished finish—ensures that each part achieves the desired visual and functional criteria without compromising its structural integrity.
Advanced chemical techniques provide an efficient alternative for materials like ABS, offering a smoother finish by employing methods such as vapor polishing. This technique uses controlled vapor exposure to gently melt the surface of the print, achieving a seamless finish that not only improves visual appeal but also reinforces the part against wear. Conducting this process in a carefully monitored environment is crucial to ensure both safety and consistency in results.
Coatings and paints open up further opportunities for customization, allowing parts to meet specific aesthetic and functional needs. Applying specialized coatings can enhance properties like abrasion resistance, thermal stability, or even electrical conductivity, depending on the end use. Selecting the appropriate finish and applying it correctly can elevate a standard print to meet specialized application demands, ensuring it performs optimally in its intended environment.
Step 5: Continuous Monitoring and Improvement
Sustaining high standards in FDM printing necessitates an ongoing commitment to evaluation and refinement. By diligently tracking print data, manufacturers can gain a comprehensive understanding of their systems' performance. This involves documenting variables such as layer adhesion, environmental conditions, and material flow rates, which can reveal trends impacting the print process. Leveraging this information allows for strategic modifications that enhance productivity and consistency across production runs.
Remaining at the forefront of FDM innovations requires proactive engagement with the latest technological and material advances. The field of additive manufacturing is dynamic, with frequent introductions of enhanced materials and techniques that promise superior results. Engaging in continuous learning through industry seminars, technical forums, and peer collaborations ensures that teams are equipped with the latest insights. This proactive approach facilitates the adoption of innovative methods that align with cutting-edge industry standards.
Cultivating a feedback-driven environment empowers teams to collectively drive improvements. Regular discussions and brainstorming sessions provide avenues for team members to share observations and propose solutions for ongoing challenges. Establishing a formalized feedback process ensures that all contributions are acknowledged and considered, promoting a culture of shared responsibility and innovation. This collaborative ethos not only refines the printing process but also strengthens team cohesion and expertise.
By adopting these best practices and embracing a commitment to continuous improvement, you can unlock the full potential of FDM printing and achieve consistent, high-quality results. As you navigate the evolving landscape of additive manufacturing, remember that the key to success lies in a combination of technical expertise, attention to detail, and a willingness to adapt. If you're ready to take your FDM printing to the next level, schedule a demo or try the platform to experience how we can help you streamline your processes and deliver exceptional quality.