How a Lack of Automation Is Hurting Additive Manufacturing
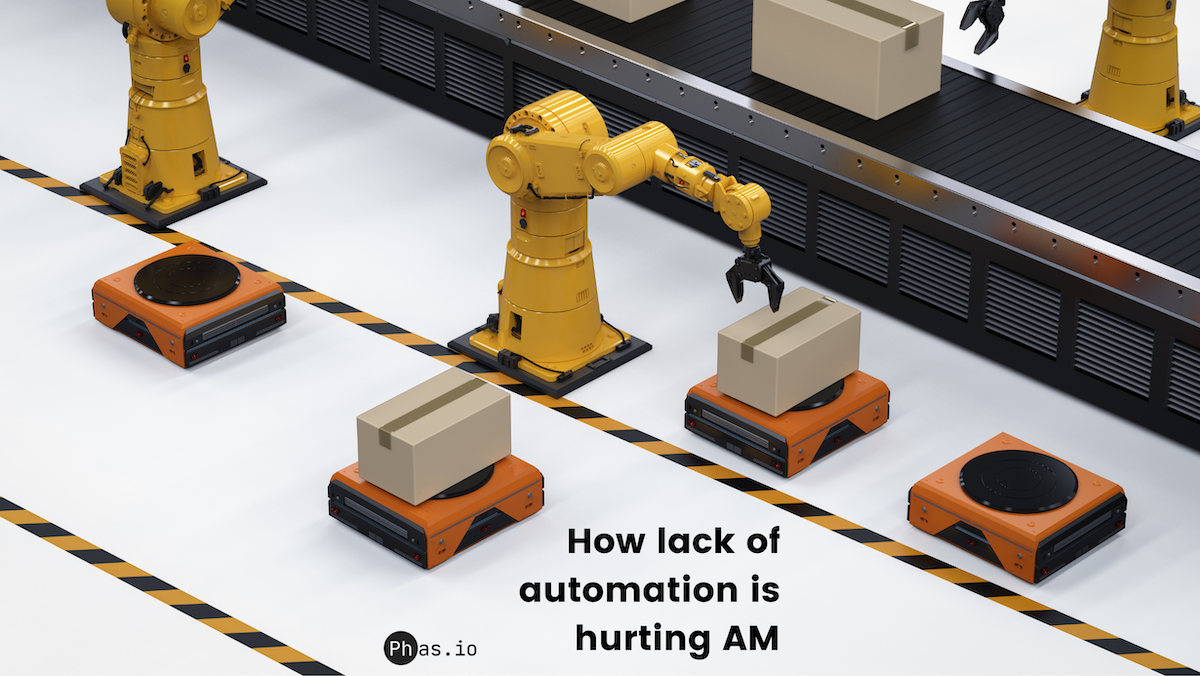
What Does Automation Really Mean?
Just to make sure everyone is on the same page, let’s define automation. It’s simply when you let software, computers, something mechanical, or algorithms do the work for you without human interaction.
In our example of Ford’s semi-autonomy, an assembly line would mechanically move the vehicle through the building process. People were still involved, but the process was sped up dramatically.
In today’s age, automation is a lot more hands-off. Self-driving cars, robots that perform everyday tasks, even robotic dog sitters. Still, the additive manufacturing industry is largely unchanged.
That is, until Phasio started automating 3D printing.
Looking at Additive Manufacturing Facilities
Take a look around your additive manufacturing facility. For a standard metal printing shop, you probably have one operator taking care of two or three machines. The operator has to set up the print, watch it run, and troubleshoot any issues.
For a majority of plants that we work with, these operators are typically college-educated engineers — many of whom have a PhD. The big price tag tacked onto their qualification makes it a waste that they’re often just sitting, monitoring machines.
Meanwhile, your 3D printer is doing all the work. The need for a hands-on operator at all times around the clock is old news. You just need a little automation to help.
How Can Automation Improve Additive Manufacturing Operations?
Right off the bat, we should mention that automation can help specific plants in unique ways when it comes to additive manufacturing. The following points are some of the general improvements that we’ve seen in additive manufacturing operations that started implementing Phasio.
Free Your Engineers’ Time
At a typical additive manufacturing site, an engineer can wear multiple hats. They can be the designer, overseer, and maintainer of 3D printers and prints.
At the same time, they could be asked to improve the plant’s production and tackle a number of different projects. In many cases, watching a 3D printer run is on the bottom of the list for an engineer. There is always something bigger and more important they can be working on, but they’re stuck staring at a printer.
Automation will remove this constraint. It will free up your engineers’ time so they can work on projects that add value to your company.
Make it Easier to Hire Operators
Finding a highly qualified engineer who is willing to work with 3D printers all day can be tough. They have a degree that comes with a higher pay scale. A lot of operations can’t (or shouldn’t) pay that much for a 3D printing operator.
By adding automation, the criterion for operators becomes much more manageable. It’s easier to find a candidate when they don’t have to have extensive college learning and hands-on experience with this specialized technology.
Stop Watching Over Printers Constantly
Watching grass grow and 3D printers run are the same in our book. We hate that there’s a need to watch over printers to make sure everything is going okay. Until now, it was the only way to minimize the impact of a failed print.
Once our software is running in your facility, you won’t have to do this anymore. Since the software monitors the print, the printer doesn’t have to be babysat. Phasio will do the hard work. Instead, operators can set up prints elsewhere or do other tasks.
Cut Your Labor Costs
Since printers don’t have to be physically monitored and the operators don’t have to be tenured engineers, your labor costs can drop dramatically.
Either your need for engineers will dramatically reduce or be removed altogether. The result? A much lower labor cost. The savings all has to do with how much you’re spending today for your workforce.
In larger companies, this could translate to hundreds of thousands or millions of dollars a year in savings.
Reduce the Impact of Failures
A failed print is sometimes unavoidable. The sites we surveyed average anywhere from a 5% to a 50% failure rate throughout the year.
If you don’t catch these failures, that’s wasted time and material costs. In this industry, time is money.
Our software will automatically track some key metrics when it comes to your printers. We’re looking for red flags that a print is about to fail or has just failed. Once noticed, we will stop the print and send a notification to the operator.
By catching these failures early, you’re wasting less time, material, and money. We predict that metal printing companies can save up to $10,000 every day by reducing the impact of failures.
Promote Around-the-Clock Printing
One of our goals is to eliminate the need for “hours of operation” when it comes to additive manufacturing companies.
3D printers don’t care what time of day it is — they’ll print at 3am without issue. The problem arises when you have to staff these machines. Engineers are a little less eager to set their alarms for 2am to head into work.
Software that checks on statuses of prints can run around the clock. The right software will automatically stop a print if a failure is detected. This means that the operation can continue while the engineers catch up on their sleep overnight.
What does this mean for your business? Your annual throughput can increase dramatically (depending on how many shifts you currently run). As the number of prints you make increases, so does the money in your pocket.
Ensure the Specs are Met
Simply examining a part after it’s printed doesn’t tell you much. It’s nearly impossible to know if the internal specs were met unless you subject the print to destructive testing.
This is pretty counterintuitive. In order to know if the part was printed correctly, you have to break the part and render it useless. This just wastes your time and money.
Instead, you can track the data while the print is being made. By looking at chamber pressures, temperatures, and laser power, you’ll get a good idea of what’s going on inside the print.
You can deliver parts with more confidence since you have data backing you up.
Automate Scheduling
Scheduling printers is often a full-time job for printing facilities of various sizes. The more printers and projects you have, the longer this takes.
Many companies opt to hire multiple people on a full-time basis just to juggle the schedule. Even then, mistakes happen. A little human error can ruin relationships with your clients, waste money, destroy your overall timeline, and hurt your reputation.
Instead, you should opt for software. Phasio automatically shuffles around the projects and assigns them to printers. By automating the process, you’re cutting back your expenses and removing the opportunity for human error. It allows you to optimize your schedule.
Faster delivery times, less money spent upfront, and little to no error. These are the results of using automation in additive manufacturing.
Add Automation to Your Additive Manufacturing Facility
There are a ton of benefits that come with implementing automation. Additive manufacturing is such a promising industry, yet a lot of sites are resorting to old-school methods of manually running these machines. If you want to jump into the modern era and beat your competitors, you need Phasio.
For questions about adding automation to your additive manufacturing facility, reach out to our team today. We will tell you the specific ways that your operation can see a huge improvement thanks to our software.