Injection Mold Tooling Quotes: Key Factors to Consider
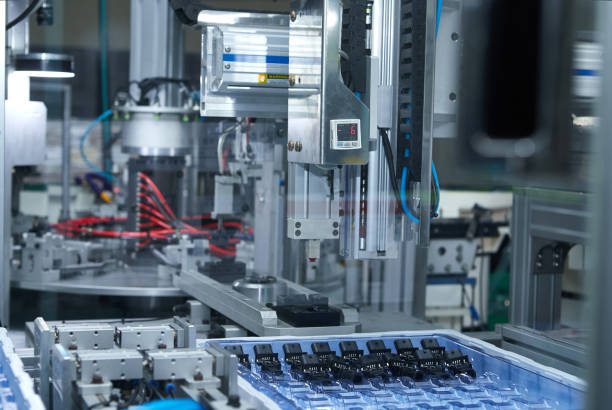
Injection mold tooling is a critical component of the manufacturing process, enabling the mass production of custom plastic parts with high precision and consistency. Obtaining accurate quotes for injection mold tooling is essential for manufacturers, engineers, and product designers to effectively plan and budget for their projects.
The quoting process for injection mold tooling involves several key factors that can significantly impact the overall cost and lead time of a project. Understanding these factors and how they influence the quoting process is crucial for making informed decisions and optimizing the manufacturing process.
In this article, we'll explore the various aspects of injection mold tooling quotes, including the factors that influence costs, design and engineering considerations, and strategies for optimizing the quoting process. By gaining a deeper understanding of these elements, manufacturers can make more informed decisions and streamline their injection molding projects.
Understanding Injection Mold Tooling Quotes
Injection mold tooling quotes provide a detailed breakdown of the costs associated with designing, engineering, and manufacturing the molds required for producing custom plastic parts. These quotes take into account various factors such as part complexity, material selection, production volume, and expected mold lifespan.
The quoting process typically begins with the manufacturer or designer providing detailed part specifications, including 3D CAD models, 2D drawings, and any additional requirements. The injection molding supplier then analyzes these specifications to determine the feasibility of the project and identify any potential design or manufacturing challenges.
Based on this analysis, the supplier generates a comprehensive quote that outlines the costs for each stage of the tooling process, including:
- Mold design and engineering: This involves creating the detailed design of the mold, taking into account factors such as part geometry, material properties, and injection molding machine specifications. Advanced techniques like mold flow analysis and simulation may be used to optimize the design and ensure efficient production.
- Mold manufacturing: Once the design is finalized, the mold is manufactured using high-precision CNC machining, EDM (electrical discharge machining), or other specialized techniques. The choice of mold material, such as aluminum, steel, or pre-hardened steel, depends on the production volume, part complexity, and expected mold lifespan.
- Sampling and testing: After the mold is manufactured, a series of test runs are conducted to validate the mold's performance and ensure that the produced parts meet the required specifications. Any necessary adjustments or modifications are made during this stage to optimize the mold's functionality.
- Production: The final stage of the process involves using the mold to mass-produce the custom plastic parts. The quote will include the cost per part based on the production volume, material costs, and any additional post-processing or assembly requirements.
Accurate injection mold tooling quotes are essential for manufacturers to effectively budget for their projects and make informed decisions about their production processes. By understanding the various components of a quote and the factors that influence costs, manufacturers can better navigate the quoting process and establish strong partnerships with reliable injection molding suppliers—like we offer at Phasio.
Factors Influencing Injection Mold Tooling Costs
Injection mold tooling costs hinge on several critical factors, each contributing to the overall expense and complexity of the project. A primary consideration is the part complexity and design features. The intricacies of the part—such as its dimensional specifications and structural elements—affect the complexity of the mold. Features like intricate geometries and detailed surface finishes necessitate advanced engineering and tooling efforts. Moreover, the number of cavities within a mold determines the production efficiency; multi-cavity molds enhance output but demand more sophisticated design and manufacturing processes.
Material selection plays a pivotal role in determining tooling costs. Selecting the appropriate thermoplastic resins, such as polycarbonate or thermoplastic elastomers, directly influences the mold's design and capability requirements. Each material has specific characteristics that impact the tooling process. Additionally, the choice of mold materials—options like hardened tool steel or specialty alloys—affects both the cost and the durability of the mold. For instance, hardened steel molds are ideal for extended production runs, while aluminum molds offer cost advantages for short runs.
The production volume and anticipated mold lifespan significantly influence tooling expenses. High-volume production typically warrants the investment in robust and costly molds, as the expense is spread across numerous parts. In contrast, for smaller quantities, economical materials and simplified mold configurations may be preferable. Additional tooling components, such as hydraulic slides or mechanical inserts, can add to both complexity and cost. These elements are crucial for achieving specific part functionalities, necessitating careful planning during the design and quoting stages to ensure an efficient and cost-effective molding process.
Mold Design and Engineering Considerations
Effective mold design and engineering are critical to ensuring the success of injection molding projects. The design phase sets the foundation for efficient manufacturing processes and ultimately influences the quality and performance of the final product. A comprehensive approach to mold design and engineering encompasses several key elements that enhance the manufacturability and functionality of the mold.
Design for Manufacturability (DFM) analysis is a vital step in the mold design process. This analysis involves assessing the part design to identify potential manufacturing challenges and optimize the design for efficient production. By considering factors such as draft angles, wall thickness, and undercuts, DFM analysis ensures that the mold can be manufactured with minimal complications and that the resulting parts meet the desired quality standards. This proactive approach not only reduces production costs but also minimizes the risk of defects and rework during the manufacturing process.
To anticipate and mitigate potential molding challenges, engineers often employ computer-aided simulations. These simulations analyze the mold's design to forecast the behavior of polymers during the injection phase, allowing for precise adjustments to gate designs and cooling systems. By understanding the material flow dynamics, engineers can enhance the distribution of polymers, reducing the likelihood of common molding defects such as voids and surface blemishes. This technology-driven insight enables the fine-tuning of the mold before it enters production, ensuring high-quality outcomes.
Prototyping through rapid tooling techniques allows for the creation of short-run molds that facilitate design validation. These initial molds serve as a testing ground for refining the design, providing a tangible means to evaluate the mold's performance under real conditions. By closely examining the prototype outputs, manufacturers can identify areas requiring adjustments—ensuring the final mold is optimized for full-scale production. This iterative approach, supported by rapid tooling, provides a cost-effective method to address potential design flaws early on.
Tooling modifications and revisions are sometimes necessary to address unforeseen challenges or changes in project requirements. These adjustments ensure that the mold continues to meet production demands and delivers high-quality parts. Whether it's refining the mold's features or incorporating additional functionalities, proactive engineering solutions contribute to the mold's longevity and adaptability. By maintaining flexibility in design and engineering, manufacturers can respond effectively to evolving market needs and technological advancements.
Evaluating Injection Mold Tooling Quotes
The process of evaluating injection mold tooling quotes involves a strategic analysis to ensure that the chosen supplier aligns with both technical requirements and financial constraints. A foundational approach begins with soliciting quotes from a diverse range of suppliers. This strategy provides a broad perspective on market offerings, revealing differences in pricing structures and service capabilities. When comparing these quotes, ensure that each supplier has based their estimates on uniform specifications and requirements to maintain consistency and accuracy in the evaluation process.
A thorough investigation into supplier capabilities and past performance is crucial. Examine the supplier's proficiency in delivering molds for projects with comparable technical demands. This evaluation should encompass not only technical competencies but also the supplier's familiarity with industry-specific standards and expectations. Reviewing portfolios and client feedback, as well as examining documented case studies, can provide valuable insights into the supplier’s operational strengths and innovative problem-solving abilities. A supplier with a proven track record can offer not only technical expertise but also strategic guidance, enhancing project outcomes.
Dissecting the cost breakdowns in each quote offers a transparent view of financial allocations, uncovering opportunities for cost efficiencies. These breakdowns typically detail expenses related to design, raw materials, machining, and post-production processes. Analyzing these components can highlight areas where cost optimization is possible, potentially lowering overall expenses without sacrificing quality. For example, while an initial investment in robust tooling may seem high, it could be offset by efficiencies in production cycles or material savings, especially in large-scale operations. Reviewing cost distributions can also reveal any ancillary charges or potential additional expenses not immediately visible.
Attention to lead times and delivery schedules is paramount, as these factors directly impact production planning and market entry strategies. Suppliers should offer clear timelines for each phase of the tooling and production process, from initial design through to final part delivery. Delays at any stage can disrupt the entire production timeline, affecting time-to-market and competitiveness. It is essential that the supplier's proposed timelines are realistic and account for current operational capacity and workload. Aligning these schedules with your production needs ensures that the project progresses smoothly without unforeseen interruptions.
Strategies for Optimizing Injection Mold Tooling Costs
To manage injection mold tooling expenses efficiently, manufacturers can adopt targeted strategies focused on design and process enhancements. One effective method involves re-evaluating part designs to maximize efficiency and minimize unnecessary intricacies. This approach involves refining the part's geometry to facilitate easier manufacturing processes, which can reduce machining efforts and material usage. By focusing on simplicity that retains essential functionality, manufacturers can achieve cost reductions without compromising the quality or performance of the final product.
Incorporating innovative mold configurations such as tandem and stack molds can significantly enhance production output. Tandem molds allow for alternate layer production within the same cycle, optimizing machine usage and reducing time between cycles. Stack molds, on the other hand, consist of multiple levels of molds that can produce separate components simultaneously, making them ideal for complex assemblies with interconnected parts. These configurations enhance the capacity and efficiency of production runs, distributing tooling costs over a broader range of parts and reducing the overall cost per unit.
Leveraging dynamic pricing and quoting technologies introduces precision into financial planning. These systems use real-time data and advanced algorithms to generate accurate quotes quickly, allowing manufacturers to assess project feasibility and allocate resources more effectively. By integrating these automated solutions, manufacturers can enhance response times to customer inquiries and streamline decision-making processes, ensuring that pricing reflects current market conditions and operational capabilities.
Building strategic alliances with experienced supply chain partners is essential for sustained cost management in injection mold tooling. Collaborating with trusted suppliers provides access to specialized knowledge and resources that can drive innovation and efficiency. These partnerships can lead to preferential pricing arrangements, expedited services, and collaborative development initiatives that foster continuous improvement. By investing in long-term relationships, manufacturers can benefit from enhanced support and expertise, contributing to more resilient and cost-effective production strategies.
Navigating the Injection Mold Tooling Quoting Process
The journey through the injection mold tooling quoting process starts with the meticulous gathering of part specifications and requirements. Manufacturers need to submit well-documented technical drawings and detailed material requirements, alongside a comprehensive overview of the part's purpose and functional demands. This groundwork ensures that suppliers have an accurate picture of the project, enabling them to create precise and customized quotes. By delivering clear and organized information, manufacturers can minimize misunderstandings and prevent potential delays in the quoting phase.
Establishing clear communication channels with suppliers is essential for a streamlined quoting process. Engaging in open discussions about project timelines, potential obstacles, and specific needs can help bridge any gaps in understanding. This proactive communication fosters a collaborative environment where expectations align closely, promoting a more efficient and productive quoting process. Keeping communication ongoing throughout the project allows for quick adjustments and resolutions to any emerging issues, ensuring a seamless transition from concept to completion.
Upon receiving quotes, careful analysis and evaluation are key to making well-informed decisions. Manufacturers should scrutinize each quote, taking into account not just the financial aspects but also the supplier's expertise, track record, and commitment to quality. By delving into the cost structures outlined in the quotes, manufacturers can identify opportunities for cost-saving measures. Comparing the quotes against the project's criteria helps in selecting the most appropriate supplier that meets both technical requirements and budgetary limits. This thorough evaluation ensures that the selected supplier can effectively deliver the desired results.
Overseeing tooling projects from start to finish requires detailed coordination and execution. Manufacturers should implement a structured project management approach, defining clear targets, responsibilities, and a timeline for progress tracking. Regular updates and discussions with suppliers can help identify any issues or deviations from the plan early on. By maintaining a proactive and systematic approach to project management, manufacturers can adeptly handle the intricacies of the injection mold tooling process, ensuring confidence and efficiency throughout.
Navigating the complexities of injection mold tooling quotes requires a strategic approach that balances technical requirements, cost considerations, and supplier capabilities. By understanding the key factors influencing tooling costs and adopting strategies to optimize the quoting process, manufacturers can make informed decisions that drive efficiency and profitability. If you're looking to streamline your injection molding projects and enhance your quoting process, schedule a demo or try the platform to experience how we can help you achieve your goals.