Injection Molding Basics: What You Need to Know
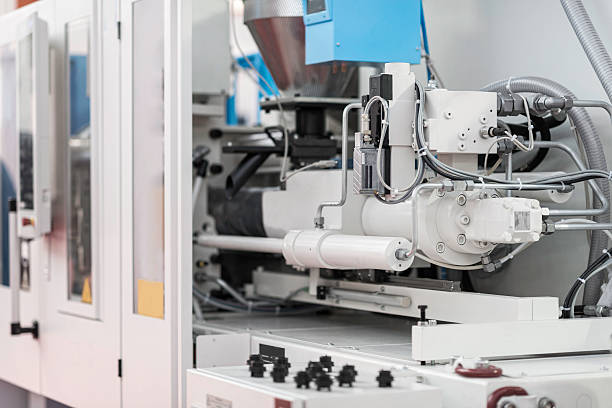
Injection molding is a versatile and widely used manufacturing process that has revolutionized the production of plastic parts. From everyday consumer goods to complex industrial components, injection molding has become an indispensable technology in the modern world.
The process involves injecting molten plastic material into a mold cavity, where it cools and solidifies to form the desired shape. This enables the mass production of identical parts with high precision and consistency.
In this article, we will explore the fundamentals of injection molding, its applications, and the advantages it offers to manufacturers and product designers alike. We will also delve into the key considerations for designing parts for injection molding and optimizing the process for maximum efficiency.
What is Injection Molding?
Injection molding is a manufacturing process that involves injecting molten plastic material into a mold cavity under high pressure. The molten plastic takes the shape of the cavity and solidifies upon cooling, resulting in a finished part that is ejected from the mold. This process is suitable for mass production of identical parts with complex geometries and tight tolerances.
One of the key advantages of injection molding is its design flexibility. The process allows for the creation of parts with intricate details, varying wall thicknesses, and complex shapes that would be difficult or impossible to achieve with other manufacturing methods. Additionally, injection molding offers high repeatability, ensuring that each part produced is virtually identical to the next.
Another significant benefit of injection molding is its cost-effectiveness for high-volume production. While the initial investment in tooling can be substantial, the cost per unit decreases dramatically as the production volume increases. This makes injection molding an ideal choice for manufacturers looking to produce large quantities of parts at a low cost per unit. However, it is important to note that injection molding does have relatively long lead times compared to other processes, as the design and fabrication of the mold can take several weeks or even months.
How Does the Injection Molding Process Work?
The injection molding process is an intricate sequence of operations, where the injection unit plays a foundational role in transforming raw plastic into a malleable form. Initially, plastic in pellet or granular form is fed into the unit, which employs heat to melt the material. The reciprocating screw within the unit not only mixes but also injects the plastic into the mold cavity. By precisely managing speed, pressure, and temperature, the unit ensures optimal filling and packing, crucial for consistent part quality.
The Mold
Central to the entire process is the mold, consisting of two halves—core and cavity—which determine the shape of the final part. As the molten plastic enters, the mold defines its configuration. Integrated cooling channels expedite the solidification of the plastic, allowing it to maintain its intended dimensions. Ejector pins facilitate the removal of the solidified part. Mold materials, such as steel or aluminum, are chosen based on the required durability and production demands, providing flexibility in both design and cost considerations.
The Clamping and Ejection Unit
The clamping and ejection phases are vital for the seamless function of injection molding. The clamping unit ensures the mold halves remain securely closed during injection, preventing leakage and ensuring part integrity. Post-cooling, the ejection unit efficiently removes the finished product from the mold, utilizing a hydraulic or electric mechanism. This precise control over clamping and ejection actions not only enhances production efficiency but also contributes to the durability and reliability of the molding equipment.
Common Injection Molding Applications
Injection molding finds extensive use across diverse industries, each leveraging its efficiency to create precise and intricate components. In consumer goods, the process is indispensable for manufacturing items such as toys, household products, electronics casings, and packaging solutions. Its ability to produce high volumes with consistent quality makes it an ideal choice for products that demand both functionality and aesthetic appeal.
In the automotive sector, injection molding is vital for producing components that meet stringent safety and performance standards. The process is employed to manufacture interior trims, which require a blend of durability and design flexibility, as well as critical functional parts used under the hood. The ability to produce lightweight yet robust components is essential, contributing to vehicle efficiency and enhanced performance.
The medical industry benefits significantly from injection molding, particularly in the production of disposable syringes, implants, and diagnostic equipment parts. These medical products require the highest levels of precision and hygiene, which injection molding consistently delivers. The process accommodates medical-grade materials, ensuring the safe production of components essential for patient care.
Industrial and commercial sectors also capitalize on injection molding for crafting gears, handles, knobs, and machine housings. The process facilitates the creation of parts essential for machinery and equipment, offering the strength and precision necessary for these applications. Injection molding's capacity to produce complex geometries efficiently allows for the seamless integration of intricate designs into functional components, catering to a wide range of industrial needs.
Advantages of Injection Molding
Injection molding stands out for its remarkable capability to produce large quantities of parts swiftly and economically. As production volumes grow, the process becomes increasingly cost-effective, making it a preferred choice for manufacturers focused on high-output operations. This efficiency is largely due to the automated nature of injection molding—a system that streamlines production by minimizing manual intervention and optimizing cycle times. This allows businesses to keep pace with market demands while maintaining high standards of quality.
Consistency and precision are hallmarks of injection molding, driven by its automated processes that ensure each part adheres to exact specifications. This capability is critical for industries like automotive and medical devices, where uniformity and precision are non-negotiable. The process supports the creation of intricate designs with detailed features, allowing manufacturers to explore innovative solutions without compromising the structural integrity of the parts.
The adaptability of injection molding materials further enhances its appeal. The process supports a diverse range of materials, including thermoplastics, thermosets, and elastomers, each selected for their specific properties such as durability, flexibility, or resistance to environmental factors. This flexibility in material choice allows for customization according to the application's needs. Additionally, the integration of features like in-mold labeling or decoration reduces the need for additional processing, streamlining production and adding value to the final product.
Designing for Injection Molding
When it comes to designing parts for injection molding, understanding the thermal and mechanical behavior of materials is essential. Wall thickness plays a pivotal role in determining how a part cools and solidifies. Consistent wall thickness throughout the part is crucial for achieving uniform cooling, which, in turn, helps maintain the structural integrity and aesthetic quality of the final product. Variations in thickness can introduce internal stresses, leading to defects such as sink marks or voids. To mitigate these issues, designers often incorporate features like ribs and gussets. These elements strengthen thicker sections without adding excessive material, thereby optimizing the balance between strength and efficiency.
Draft Angles
Incorporating draft angles into the design of injection-molded parts is vital for facilitating their removal from the mold. Draft angles—typically ranging from 1° to 3°—are crucial for reducing friction and ensuring smooth ejection. The specific angle required depends on factors such as the depth of the feature and the material's properties. Applying draft to both sides of the mold enhances the efficiency of the ejection process, minimizing the risk of part damage and extending the mold's lifespan. By carefully considering draft angles, manufacturers can improve both the quality of the parts produced and the overall efficiency of the injection molding process.
Undercuts and Side-Actions
While undercuts can enhance a part's functionality, they often introduce additional complexity to the mold design. Avoiding undercuts can streamline the process, but when they are necessary, designing them perpendicular to the mold's parting line can simplify ejection. Exploring alternative design solutions, such as incorporating snap-fits or living hinges, can eliminate the need for complex mold components. These approaches not only reduce tooling costs but also enhance the overall efficiency of the injection molding process, offering a cost-effective way to produce high-quality, functional parts.
Optimizing Your Injection Molding Process
Enhancing the injection molding process starts with engaging knowledgeable professionals who can provide strategic guidance in design optimization for efficient manufacturing. Their expertise is crucial in fine-tuning aspects such as mold design and material compatibility, ensuring that the production aligns with both technical specifications and market expectations. This collaborative approach significantly aids in navigating the complexities of injection molding, facilitating the seamless transition from design to full-scale production.
Undertaking a detailed mold flow analysis is essential for preemptively resolving potential challenges within the molding process. This involves using simulation tools to assess the flow of material through the mold, allowing for the identification of areas where issues like improper filling or air entrapment may occur. By strategically adjusting gate placements, runner configurations, and venting systems, manufacturers can optimize flow dynamics and mitigate defect risks, resulting in higher-quality outputs and reduced material waste.
Implementing a comprehensive quality assurance framework is vital for upholding the standards of the injection molding process. This involves systematic inspections and monitoring at different production stages to ensure that dimensions, surface finishes, and material characteristics consistently meet predefined standards. By integrating rigorous quality checks, manufacturers ensure the delivery of products that not only meet customer expectations but also comply with industry standards, thus enhancing their reputation for reliability and quality.
Fostering a culture of continuous process enhancement is crucial for sustaining improvements in injection molding. Through systematic data analysis and identification of defect causes, manufacturers can implement targeted corrective measures that enhance overall process efficiency. This proactive approach not only addresses immediate production challenges but also encourages ongoing innovation and operational excellence, ensuring competitiveness in the ever-evolving manufacturing landscape.
As you embark on your injection molding journey, remember that partnering with experts who understand the intricacies of the process is key to success. We are here to support you every step of the way, from design optimization to production efficiency. Schedule a demo or try the platform to experience its capabilities and discover how we can help you unlock the full potential of injection molding.