Calculating Injection Molding Costs: Tips and Tools
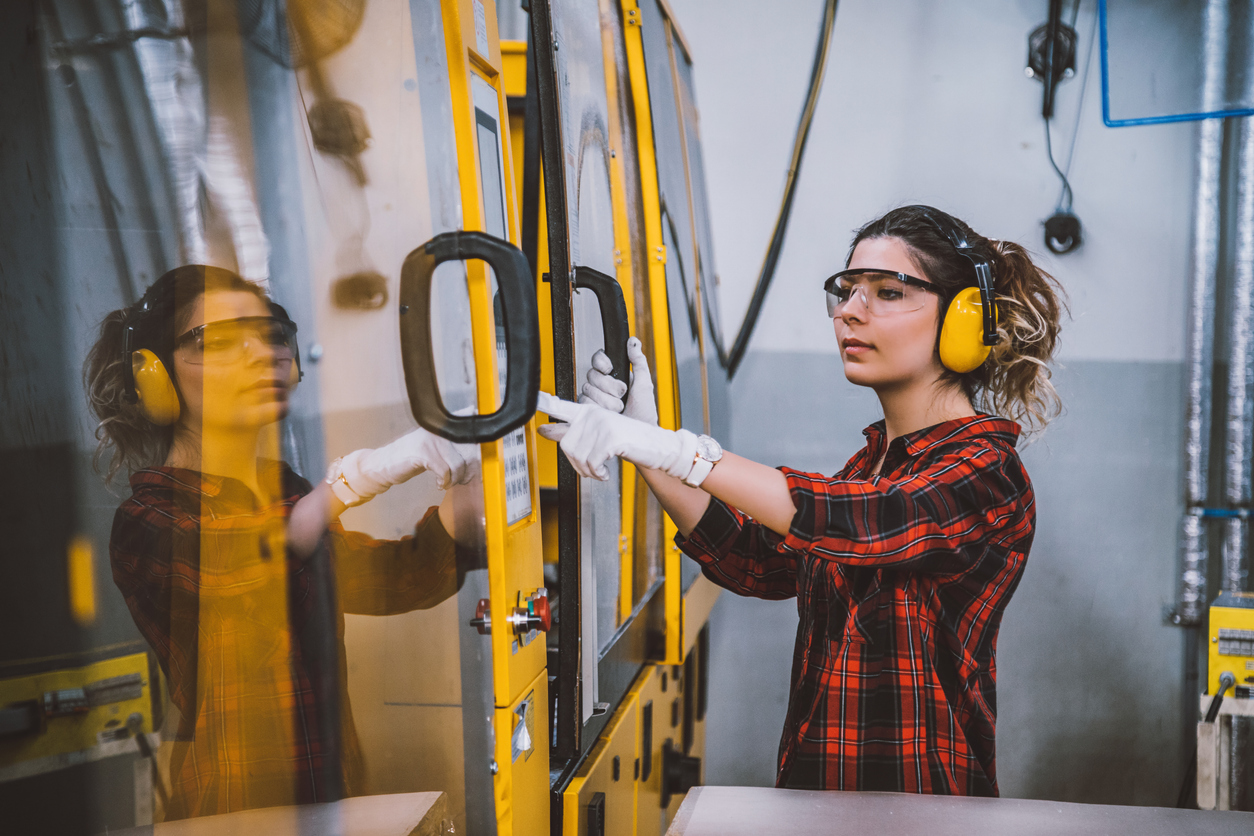
Injection molding is a popular manufacturing process that enables the mass production of plastic parts with consistent quality and precision. However, determining the cost of injection molding can be a complex task, as it involves various factors such as material selection, mold design, and production volume.
Accurate cost estimation is crucial for manufacturers to make informed decisions and optimize their resources. By understanding the key components that contribute to injection molding costs, businesses can effectively plan their budgets and ensure the profitability of their projects.
In this article, we will explore the concept of injection molding cost calculation and provide insights into the factors that influence the overall expenses. We will also discuss strategies for optimizing costs and leveraging tools to streamline the estimation process.
What is Injection Molding Cost Calculation?
Injection molding cost calculation is the process of estimating the total expenses associated with producing parts using the injection molding technique. It involves a comprehensive analysis of all the cost drivers, including material costs, tooling expenses, production time, and overhead costs.
The primary goal of injection molding cost calculation is to provide manufacturers with a clear understanding of the financial implications of their projects. By accurately estimating the costs upfront, businesses can make informed decisions regarding material selection, mold design, and production volume.
Injection molding cost calculation is not a one-time process; rather, it requires continuous monitoring and adjustment throughout the project lifecycle. Factors such as design changes, material price fluctuations, and production efficiency can impact the overall costs, making it essential to regularly update and refine the cost estimates.
Key Components of Injection Molding Cost Calculation
To effectively calculate injection molding costs, it is crucial to consider the following key components:
- Material Costs: The cost of the plastic resin used in the injection molding process is a significant factor. Different materials have varying prices, and the choice of material directly impacts the overall cost. It is essential to consider the material properties required for the specific application and select a cost-effective option that meets the desired performance criteria.
- Tooling Costs: Injection molding requires the creation of a mold, which is a significant upfront investment. The cost of tooling depends on factors such as mold complexity, material choice, and the number of cavities. Optimizing mold design and selecting appropriate materials can help reduce tooling costs without compromising part quality.
- Production Time: The time required to produce each part, known as the cycle time, directly affects the production cost. Longer cycle times result in higher labor and machine utilization costs. Optimizing the injection molding process to reduce cycle time can lead to significant cost savings, especially for high-volume production runs.
- Overhead Costs: Overhead costs include expenses such as facility rent, utilities, and equipment maintenance. These costs are typically allocated to each project based on the production volume and duration. Accurately accounting for overhead costs ensures a comprehensive understanding of the total project expenses.
Tools for Injection Molding Cost Calculation
To streamline the injection molding cost calculation process, manufacturers can leverage various tools and resources. These tools help in estimating costs accurately and exploring cost-saving opportunities.
- Injection Molding Cost Calculators: Online cost calculators, such as the one offered by Phasio, provide a user-friendly interface to input project parameters and obtain cost estimates. These calculators consider factors such as part geometry, material choice, and production volume to generate accurate cost projections.
- Material Databases: Comprehensive material databases provide information on the properties, pricing, and availability of different plastic resins. These databases assist in selecting the most suitable and cost-effective material for the specific application.
- Design for Manufacturing (DFM) Tools: DFM tools analyze part designs and provide recommendations for optimizing manufacturability and reducing costs. These tools help identify design features that may increase production complexity or require additional tooling, allowing manufacturers to make informed design decisions.
Strategies for Optimizing Injection Molding Costs
In addition to utilizing cost calculation tools, manufacturers can employ several strategies to optimize injection molding costs:
- Design Optimization: Collaborating with experienced design engineers to optimize part geometry, wall thicknesses, and other design features can significantly reduce material usage and simplify the molding process. Simplified designs often result in shorter cycle times and lower tooling costs.
- Material Selection: Choosing the right material is crucial for balancing performance requirements and cost-effectiveness. Manufacturers should consider factors such as material properties, price, and availability when making material selections. In some cases, using alternative materials or recycled resins can provide cost savings without compromising part quality.
- Mold Optimization: Investing in high-quality, well-designed molds can lead to long-term cost savings. Molds with optimized cooling channels, proper venting, and efficient ejection systems can reduce cycle times and minimize production defects. Additionally, exploring multi-cavity molds or family molds can increase production efficiency and reduce per-part costs.
- Process Optimization: Continuously monitoring and optimizing the injection molding process can yield significant cost savings. This includes fine-tuning machine parameters, minimizing scrap and waste, and implementing lean manufacturing principles. Regular maintenance and calibration of injection molding machines also contribute to improved efficiency and reduced downtime.
By understanding the key components of injection molding cost calculation and leveraging available tools and strategies, manufacturers can make informed decisions and optimize their injection molding projects for cost-effectiveness. Accurate cost estimation, coupled with proactive cost optimization efforts, enables businesses to remain competitive in the market and deliver high-quality parts at competitive prices.
How to Calculate Injection Molding Costs
Calculating injection molding costs involves a nuanced approach that takes into account several critical factors. Manufacturers need to prioritize balancing quality requirements with budget constraints, ensuring that every decision made during the design and production phases aligns with both performance and cost objectives. A structured methodology to cost estimation enables businesses to identify savings opportunities while maintaining product integrity.
Material Selection and Costing
The type of resin selected dictates a significant portion of the injection molding expenses. Each resin provides unique characteristics affecting not just the material cost but also the overall molding efficiency. Manufacturers should evaluate these resins considering physical properties such as tensile strength and thermal resistance, ensuring they align with the product's end-use requirements. Utilizing material guides and comparison tools facilitates an informed selection process, enabling the identification of resins that deliver value in terms of both cost and performance. Considerations like using regrind material or innovative resin blends can offer additional cost reductions without compromising quality.
Tooling and Mold Design
The initial expenditure on tooling is a pivotal factor in injection molding. The intricacies and precision of mold design influence both the upfront investment and the lifecycle cost. To control these expenses, manufacturers should aim to streamline mold designs, focusing on simplicity and durability. This includes selecting robust materials for the mold to withstand high usage and employing advanced design techniques to minimize cycle times. Collaborating with skilled mold engineers can lead to creative design solutions that optimize production efficiency, thereby reducing per-unit costs significantly.
Production Volume and Efficiency
The scale of production directly impacts the cost efficiency of injection molding. Larger production runs allow the distribution of fixed costs like tooling over a greater number of units, lowering the cost per part. Accurate forecasting and aligning production scale with anticipated demand are critical to achieving cost-efficiency. Additionally, enhancing production workflows through process optimization and leveraging cutting-edge technologies can improve throughput, thereby reducing operational costs. Implementing systems for real-time process analytics allows manufacturers to swiftly identify and address production inefficiencies, ensuring a seamless operation.
Understanding the complexities involved in calculating injection molding costs is vital for manufacturers aiming to streamline their operations. By concentrating efforts on strategic material selection, efficient tooling, and production scalability, businesses can craft cost-effective manufacturing strategies that support both fiscal and performance objectives, ensuring a robust competitive position in the market.
1. Material Costs
Material expenses are a cornerstone in the financial planning of injection molding projects, influenced heavily by the specific types and quantities of polymers utilized. Each resin brings distinct pricing, influenced by its inherent qualities and market dynamics. For example, high-performance thermoplastics like PEEK or Ultem generally incur higher costs due to their exceptional properties compared to more commonly used resins such as ABS or polypropylene.
When assessing material expenses, it is essential to weigh the balance between cost and the resin's functional attributes. The chosen material's traits—such as tensile strength, thermal stability, and resistance to chemicals—should align with the intended application. Leveraging sophisticated tools, such as price estimation software, enables a detailed exploration of how varying material choices affect the overall budget. These tools facilitate scenario planning, accounting for factors like material efficiency and reuse potential, providing a holistic view of financial impacts.
In addition, strategic sourcing strategies can lead to substantial cost savings. Forming long-term partnerships with suppliers or negotiating bulk purchase agreements can result in competitive pricing and secure supply continuity. Additionally, incorporating recycled materials where feasible offers a cost-effective and environmentally conscious approach to material sourcing. When recycled content is integrated carefully, it can reduce expenses while maintaining the desired quality and structural integrity of the final product.
2. Tooling Costs
Tooling expenses are a critical component of the injection molding process, encompassing the intricate design and precise manufacturing of molds necessary for producing high-quality parts. These costs are influenced by the detailed engineering required to create molds that meet specific design specifications and production needs. Attention to detail in the initial design phase can significantly impact overall tooling expenses.
Selecting the appropriate materials for mold construction is essential for balancing cost and durability. While high-grade steel offers longevity and is ideal for high-volume production, aluminum can be advantageous for shorter runs due to its cost-effectiveness and ease of machining. Employing innovative design strategies, such as using inserts or modular components, can further reduce material usage and extend mold life, providing an economical advantage.
To enhance cost estimation accuracy, manufacturers can leverage sophisticated tooling estimation tools. These platforms offer simulations that project various design and material scenarios, providing valuable insights into potential cost-saving opportunities. By integrating these tools into the planning process, manufacturers can make strategic decisions that align with both budgetary goals and production efficiency targets, ensuring that tooling investments are optimized for both performance and cost-effectiveness.
3. Production Time
Efficient management of production time is crucial for optimizing the cost-effectiveness of injection molding projects. The time taken to complete each cycle influences not only the direct labor costs but also the overall machine efficiency. By understanding the factors that affect cycle duration, such as mold cooling and material flow, businesses can enhance their operational strategies to increase productivity.
Leveraging advanced tools for cycle time estimation provides manufacturers with valuable insights into the precise timing of production phases. These tools, which analyze mold configurations and material behavior, enable more accurate scheduling and resource management. With precise cycle time forecasts, manufacturers can align their production timelines with demand forecasts, ensuring that operations are both cost-efficient and responsive to market needs.
Streamlining cycle time requires a comprehensive approach that addresses various aspects of the injection molding process. Improvements such as optimizing mold venting, refining material selection, and adjusting machine settings can all contribute to quicker cycle times. By implementing continuous monitoring systems, manufacturers can rapidly identify and rectify inefficiencies, leading to enhanced process control and reduced costs. These refinements not only boost the speed of production but also enhance the overall quality and reliability of the manufactured parts.
4. Additional Cost Factors
Beyond the primary components of material, tooling, and production time, several additional factors contribute significantly to the overall cost of injection molding projects. These ancillary expenses, often overlooked, can influence the financial outcome and efficiency of the manufacturing process. By identifying and managing these elements, manufacturers can achieve a comprehensive understanding of total project costs and implement strategies to mitigate them.
Hidden Costs in Injection Molding
- Equipment Longevity: Ensuring the durability of injection molding machinery extends beyond routine maintenance. Investing in high-quality components and implementing an effective replacement strategy for worn-out parts can prevent operational disruptions. This approach not only prolongs equipment life but also stabilizes long-term cost management.
- Precision Assurance: Achieving consistent accuracy in part production necessitates advanced monitoring systems. These systems can detect deviations early, reducing the need for manual inspections and rework. Incorporating real-time data analytics enhances the precision of manufacturing processes, thereby optimizing resource allocation.
- Distribution and Handling: Efficient distribution involves more than just transportation logistics. It includes optimizing inventory management and utilizing automated handling systems to streamline operations. By embracing digital tracking solutions, manufacturers can improve supply chain transparency, reduce lead times, and lower overall distribution costs.
Utilizing Advanced Cost Estimation Tools
Advanced cost estimation tools provide manufacturers with the capability to analyze all potential cost variables comprehensively. These tools enable dynamic cost modeling, which accounts for fluctuations in material prices, labor rates, and other market conditions. By integrating these tools into their planning processes, manufacturers can gain a clearer view of potential cost drivers and explore scenarios to minimize expenses.
Adopting these comprehensive tools also facilitates regular updates to cost estimates, ensuring that budgets reflect the current realities of production. This proactive approach allows for agile responses to changes in market conditions or production requirements, maintaining alignment with financial objectives. Accurate, up-to-date cost estimates support informed decision-making, helping manufacturers to optimize their operations and sustain competitive advantage.
In conclusion, calculating injection molding costs requires a comprehensive understanding of the various factors that contribute to the overall expenses. By leveraging advanced tools and strategies, manufacturers can optimize their processes, reduce costs, and maintain a competitive edge in the market. If you're looking to streamline your injection molding operations and gain deeper insights into cost estimation, schedule a demo or try the platform to experience how we can help you achieve your manufacturing goals.