Key Strategies for Effective Injection Molding Cycle Planning
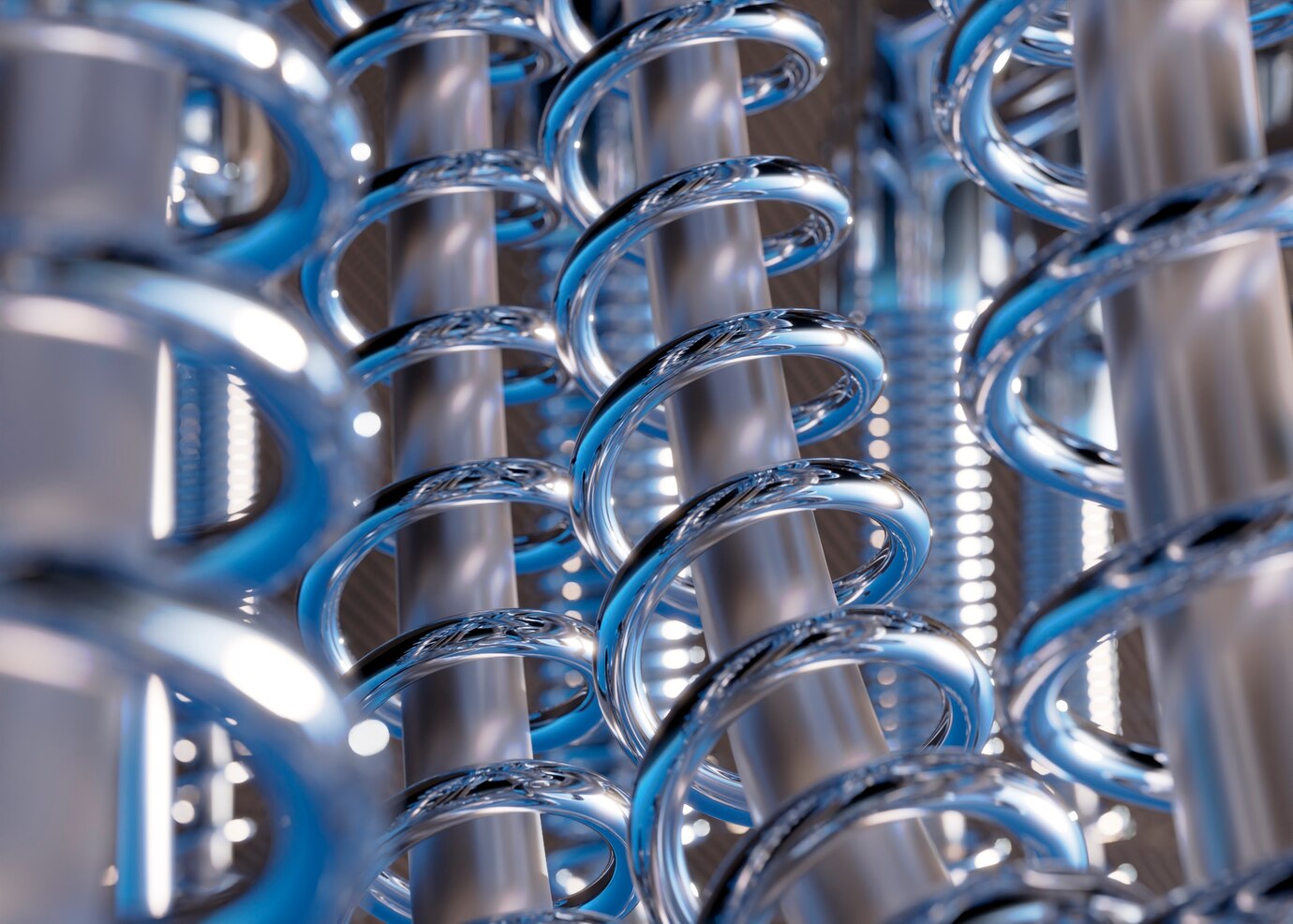
In the fast-paced world of injection molding, efficiency is paramount. Manufacturers are constantly seeking ways to streamline their processes, reduce cycle times, and maintain the highest standards of quality.
Effective cycle planning lies at the heart of this pursuit. By optimizing each stage of the injection molding cycle — from clamping and injection to cooling and ejection — manufacturers can unlock significant improvements in productivity and profitability.
This article delves into the intricacies of injection molding cycle planning, exploring the key strategies and best practices that can help you take your operations to the next level. We'll examine the critical stages of the process, discuss tools and techniques for optimization, and provide actionable insights to help you achieve your production goals.
What is Injection Molding Cycle Planning?
Injection molding cycle planning is the strategic process of organizing and optimizing each stage of the injection molding cycle to maximize efficiency, minimize cycle times, and ensure consistent product quality. It involves a meticulous analysis of the entire production workflow, from the moment the mold closes to the instant the finished part is ejected.
The primary goal of cycle planning is to create a seamless and synchronized flow of operations, eliminating bottlenecks, reducing waste, and optimizing resource utilization. By carefully planning and coordinating each stage of the cycle, manufacturers can achieve:
- Reduced cycle times: Efficient cycle planning helps identify and eliminate unnecessary delays, allowing for faster production rates and increased throughput.
- Improved product quality: By ensuring precise timing and control over each stage, cycle planning helps maintain consistent product quality, minimizing defects and variations.
- Cost savings: Optimized cycle times lead to reduced energy consumption, lower material waste, and more efficient use of labor and equipment, ultimately translating into cost savings for the manufacturer.
Effective cycle planning requires a deep understanding of the injection molding process, as well as the ability to analyze data, identify improvement opportunities, and implement targeted optimizations. It involves a collaborative effort among various teams — from product design and mold engineering to production and quality control — to ensure a holistic approach to cycle time reduction.
Within the realm of injection molding, cycle planning functions as a strategic framework that ensures precision and effectiveness throughout the production process. By carefully aligning resources and operations, manufacturers can enhance their production capabilities and maintain a competitive edge. This strategic alignment is crucial for meeting industry demands and ensuring that manufacturing processes are both agile and robust.
Beyond the basics of managing workflow, cycle planning embodies a comprehensive approach to synchronizing all facets of production — from equipment to materials — to execute a seamless cycle. This synchronization is vital for achieving swift production rates, which supports high-volume manufacturing while maintaining stringent quality standards. Rapid cycle times facilitate timely delivery, an essential factor in building trust and reliability with clients, thereby fostering long-term business relationships.
Additionally, cycle planning is instrumental in advancing sustainability initiatives by optimizing resource utilization. By refining each stage of the injection process, manufacturers can significantly cut down on excess material usage, thereby promoting both cost efficiency and environmental stewardship. This focus on sustainability not only bolsters profitability but also aligns with the industry's growing emphasis on eco-conscious manufacturing practices. Successfully balancing quality, efficiency, and sustainability reflects the strategic importance of effective cycle planning within injection molding operations.
How to Optimize Injection Molding Cycle Planning
Optimizing injection molding cycle planning necessitates an in-depth grasp of the entire process, which encompasses the crucial stages of clamping, injection, cooling, and ejection. Each stage presents unique challenges and opportunities for efficiency improvements. By focusing on precision in timing and coordination, manufacturers can enhance the seamless flow of operations, resulting in minimized delays and maximized production output.
Mastering Key Stages
The clamping phase acts as the cornerstone of the injection molding cycle. This stage involves the secure closure of the mold halves with adequate force to endure the pressures during material injection. Effective clamping ensures the integrity and consistency of the final product. During the subsequent injection phase, material is introduced into the mold cavity, requiring meticulous control of variables such as pressure and temperature to achieve thorough mold filling and prevent defects.
Efficient cooling of the part within the mold is paramount for maintaining dimensional accuracy and reducing cycle time. Advanced cooling technologies and precise thermal management strategies can significantly enhance this stage. The ejection phase follows, where the part is removed from the mold. Innovative ejection techniques reduce the risk of deformation and streamline the transition to subsequent cycles.
Leveraging Advanced Tools and Techniques
To refine cycle planning, manufacturers can employ cutting-edge tools and methodologies. Simulation software provides a robust platform to explore various production scenarios, allowing for the identification and rectification of potential process inefficiencies before full-scale production. These tools also enable precise cycle time analysis, facilitating comparisons with industry benchmarks to establish actionable improvement targets.
In addition to simulation, integrating real-time data acquisition systems—such as those available through specialized manufacturing platforms—can offer invaluable insights into process performance. These systems enable immediate adjustments, fostering a proactive approach to process management. By incorporating these advanced technologies, manufacturers can shift from traditional reactive measures to a more dynamic, anticipatory model of process optimization.
Strategic Enhancements for Ongoing Improvement
Continuous improvement in cycle planning involves strategic enhancements to both processes and equipment. Fine-tuning machine settings—such as adjusting injection speeds and optimizing temperature profiles—can dramatically reduce cycle times while maintaining adherence to quality standards. Enhancements in cooling strategies, including the adoption of conformal cooling techniques, can further expedite the cooling phase and improve thermal efficiency.
Innovative mold designs also play a vital role in process optimization. By facilitating improved material flow and heat dissipation, these designs contribute to shorter cycle times and consistent product quality. Regular equipment maintenance and strategic upgrades ensure machinery operates at peak efficiency, further reducing the likelihood of unplanned downtime.
The pursuit of optimized cycle planning is an ongoing endeavor that requires a commitment to innovation and adaptability. By embracing technological advancements and refining operational strategies, manufacturers can achieve superior efficiency in their injection molding processes, ensuring they remain at the forefront of the industry.
Step 1: Analyze Current Cycle Times
Initiating an in-depth review of cycle times is crucial for enhancing injection molding operations. This requires a meticulous assessment of each phase in the production cycle to uncover inefficiencies and delays. By harnessing precise production metrics, manufacturers can obtain a clear understanding of the workflow, identifying critical areas for optimization.
Discovering Process Constraints
Start by collecting accurate data for each segment of the injection molding cycle. This entails recording specific durations for clamping, injection, cooling, and ejection processes. The aim is to identify stages where time is disproportionately extended or where disruptions frequently occur. Understanding these constraints allows for the development of strategies tailored to streamline operations.
- Process Mapping: Examine the flow of operations to identify stages with prolonged cycle times or performance variations. Evaluate factors such as equipment efficiency, material handling, and operational conditions that could impact the process.
- Causal Analysis: Conduct detailed investigations into each constraint to uncover root causes. These may include equipment wear, improper settings, or procedural inconsistencies.
Establishing Industry Benchmarks
Positioning current cycle times against industry benchmarks provides valuable context for performance evaluation. This involves gathering data from comparable operations to set performance baselines. Understanding how your cycle times measure up to industry norms enables the establishment of practical improvement targets.
- Performance Metrics: Gather and analyze KPIs from industry leaders to serve as benchmarks for cycle time assessment.
- Objective Setting: Create specific, attainable targets for cycle time reduction informed by benchmarking insights. Align these targets with broader operational goals, such as throughput enhancement or quality improvements.
Driving Improvements Through Data Insights
With a comprehensive analysis and benchmarking framework in place, manufacturers can implement targeted improvements. This includes adjustments in equipment, refining processes, or enhancing workforce training to address inefficiencies and meet improvement objectives.
By sustaining a focus on data-driven evaluation and ongoing refinement, manufacturers can ensure their injection molding processes achieve peak efficiency and competitiveness.
Step 2: Implement Optimization Strategies
Enhancing injection molding efficiency requires a strategic blend of innovative techniques and precise process adjustments. By adopting diverse optimization strategies, manufacturers can significantly improve cycle times and elevate production quality.
Fine-Tuning Process Parameters
Optimizing process parameters starts with a detailed examination of the entire molding operation. This involves configuring machine settings, such as injection pressures and material feed rates, to match the specific requirements of each project. Precision in these settings enhances material flow and reduces cycle variability.
- Machine Synchronization: Align machine operations to the unique demands of each molding cycle. By coordinating speed and pressure with mold specifications, manufacturers can achieve consistent and reliable part production.
- Adaptive Process Controls: Implement controls that automatically adjust parameters in real-time to respond to material behavior, ensuring optimal performance under varying conditions.
Innovative Thermal Management Solutions
Effective thermal management is crucial for reducing cycle times and maintaining product quality. Employing advanced techniques, such as integrated heating and cooling systems, can significantly enhance the efficiency of the cooling phase.
- Integrated Cooling Systems: Use systems that combine heating and cooling elements within the mold design, allowing for precise temperature regulation across the entire mold surface.
- Heat Transfer Optimization: Focus on improving the efficiency of heat exchange within the mold, employing materials and designs that facilitate rapid thermal conductivity and uniform temperature distribution.
Strategic Mold Design and Upkeep
Mold design plays a critical role in the optimization process. By incorporating features that enhance material distribution and minimize cycle delays, manufacturers can achieve a more efficient production cycle. Regular mold maintenance ensures these designs perform at peak capacity.
- Optimized Flow Channels: Design molds with channels that allow for smooth material flow, reducing resistance and mitigating fill-time inconsistencies.
- Preventive Maintenance Programs: Establish proactive maintenance routines that include regular inspections, cleaning, and timely repairs to maintain mold precision and performance.
By integrating these advanced strategies into the injection molding process, manufacturers can achieve substantial gains in cycle efficiency and product quality, positioning themselves for sustained operational success.
Step 3: Leverage Technology for Cycle Time Reduction
Integrating state-of-the-art technology is vital for advancing cycle time reduction in injection molding. Cutting-edge systems and digital monitoring tools offer unprecedented opportunities to enhance process precision and efficiency. By automating critical stages, these technologies free up skilled operators to focus on complex tasks, thereby improving overall productivity and operational agility.
Automation and Real-Time Monitoring
Incorporating advanced automation within injection molding setups can revolutionize process management. These systems not only carry out repetitive tasks with high precision but also ensure that production stages are seamlessly coordinated. This integration results in:
- Uniform Quality: Automation ensures that each production run maintains the same high standards, significantly reducing variability.
- Reduced Human Oversight: Automated systems decrease the need for constant human intervention, reducing the potential for manual errors and increasing the reliability of outputs.
Real-time monitoring acts as a complementary technology, providing continuous oversight over the molding process. By employing sophisticated sensors and digital analytics, these systems can detect and address deviations promptly, ensuring that operations remain within optimal parameters:
- Proactive Process Control: Real-time data enables immediate adjustments, keeping the production process aligned with desired outcomes.
- Enhanced Decision-Making: Access to real-time insights allows operators to make informed decisions, optimizing the overall production workflow.
Advanced Molding Cycle Analysis
Utilizing comprehensive molding cycle analysis tools provides a granular view of each cycle's performance. By capturing detailed data on machine operations and environmental factors, manufacturers can pinpoint inefficiencies and implement precise enhancements. This analytical approach offers:
- Adaptive Production Techniques: Insights from analysis tools support adjustments that fine-tune operations to meet evolving production demands.
- Strategic Maintenance Scheduling: Data-driven predictions help schedule maintenance proactively, minimizing unexpected disruptions and maintaining continuous operation.
Molding cycle analysis supports strategic long-term improvements by identifying trends and patterns over time. By leveraging historical data, manufacturers can refine processes continuously, ensuring that efficiency gains are sustained and evolve with technological advancements. Integrating these advanced technologies into the injection molding process not only accelerates cycle time reduction but also elevates the entire manufacturing operation to new levels of excellence.
Step 4: Train and Engage Your Team
Elevating the capabilities of your workforce is integral to optimizing injection molding operations. By equipping team members with the necessary skills and knowledge, you not only enhance process efficiency but also empower them to make informed contributions to operational improvements. This holistic approach ensures that technological advancements are supported by a proficient workforce ready to capitalize on these innovations.
Comprehensive Training Programs
Crafting a detailed training regimen tailored to the specific demands of your molding processes is essential. This should encompass:
- Core Concepts: Deliver introductory sessions that cover fundamental aspects of injection molding, such as machine setup, material properties, and cycle phases. Ensuring a unified baseline of understanding across the team promotes consistent quality in operations.
- Specialized Skill Development: Offer targeted learning modules that delve into process refinement, diagnostic skills, and emerging industry trends. These educational experiences should encourage analytical thinking and equip the team to tackle sophisticated challenges effectively.
- Practical Application: Facilitate immersive training opportunities that allow employees to translate theoretical knowledge into practice. This hands-on approach deepens their understanding of complex molding processes, enhancing their ability to optimize production.
Fostering a Culture of Continuous Improvement
Creating an environment that emphasizes perpetual enhancement is critical for thriving in the competitive landscape of injection molding. This culture inspires team members to actively pursue improvements in production planning and efficiency, nurturing an innovative spirit.
- Active Feedback Systems: Establish regular feedback sessions and collaborative platforms where team members can exchange ideas and propose enhancements. This openness fosters a sense of belonging and benefits from a diversity of insights.
- Acknowledgment and Rewards: Develop incentive programs that recognize and reward process improvements and efficiency achievements. Celebrating successes motivates employees to remain engaged and pursue further advancements.
- Interdepartmental Collaboration: Encourage teamwork across different units by organizing collaborative initiatives and shared projects. This synergy harnesses the collective knowledge of the organization, leading to more comprehensive optimization strategies.
By investing in training and nurturing a culture of continuous improvement, manufacturers prepare their teams to excel in the evolving field of injection molding. This strategic emphasis on human resources complements technological progress, ensuring that process advancements are both sustainable and impactful.
Step 5: Review and Refine Regularly
To remain competitive, manufacturers must engage in ongoing assessments of their injection molding processes. By systematically examining production workflows and outcomes, they can uncover new areas for improvement. This approach allows for adaptation to changes in technology and market demands while ensuring that processes align with strategic objectives.
Strategic Use of Data Analytics
Leveraging data analytics supports precise refinement of the molding cycle. Detailed examination of production metrics enables manufacturers to detect patterns and inefficiencies. This information provides a basis for informed adjustments that optimize cycle times and enhance operational performance.
- Comprehensive Metrics Analysis: Regularly analyze the full spectrum of production metrics to gauge process effectiveness. This analysis reveals insights into operational strengths and areas needing enhancement.
- Forecasting Tools: Implement forecasting models to predict future trends and challenges. These tools allow for preemptive strategy adjustments, ensuring readiness for potential shifts in the production environment.
Collaborative Refinement Initiatives
Incorporating insights from a broad range of stakeholders enriches the refinement process. By fostering a culture of collaboration, manufacturers can ensure that diverse expertise contributes to process optimization.
- Interdisciplinary Team Meetings: Conduct meetings with team members from different departments to share insights and discuss process improvements. These interactions promote innovative solutions and comprehensive cycle management strategies.
- Real-Time Feedback Integration: Establish mechanisms for continuous feedback from production staff to identify and resolve inefficiencies swiftly. This feedback loop supports a dynamic approach to process refinement.
By embedding a continuous review and refinement ethos, manufacturers can ensure their injection molding processes evolve with industry advancements. This ongoing cycle of improvement not only addresses immediate operational needs but also positions the organization for sustained success in a competitive landscape.
Optimizing your injection molding cycle planning is an ongoing journey that requires dedication, innovation, and a willingness to adapt. By embracing the strategies outlined in this article, you can unlock new levels of efficiency and competitiveness in your manufacturing operations. If you're ready to take your injection molding processes to the next level, we invite you to schedule a demo or try the platform to experience its capabilities firsthand and see how we can support your success.