How to Streamline Your MJF Build Planning Process
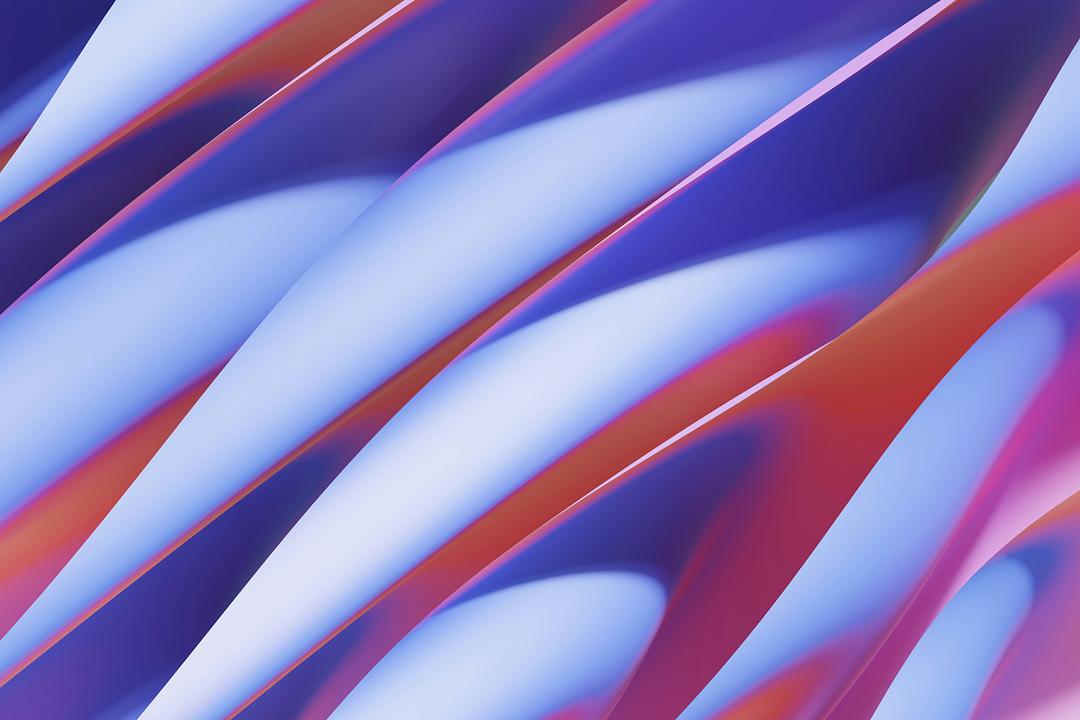
Multi Jet Fusion (MJF) technology has revolutionized the additive manufacturing landscape, enabling the production of highly complex, precise, and durable parts. To fully harness the potential of MJF and achieve optimal results, a well-executed build planning process is crucial.
Effective MJF build planning involves a comprehensive understanding of the technology's capabilities, limitations, and best practices. By carefully considering factors such as material selection, part orientation, and design optimization, manufacturers can streamline their MJF workflows and produce high-quality parts consistently.
In this article, we will delve into the essential elements of MJF build planning, providing insights and strategies to help you optimize your MJF processes. From material compatibility to design considerations and process guidelines, we will cover the key aspects that contribute to successful MJF builds.
What is MJF Build Planning?
MJF build planning is the strategic approach to organizing and preparing parts for production using HP's Multi Jet Fusion technology. It encompasses a range of considerations and decisions that aim to optimize the efficiency, quality, and cost-effectiveness of the 3D printing process.
Effective MJF build planning involves carefully evaluating part geometries, material properties, and application requirements to determine the most suitable orientation, support structures, and process parameters. By taking a holistic view of the entire build process—from design to post-processing—manufacturers can minimize potential issues, reduce waste, and achieve consistent results.
The importance of thorough MJF build planning cannot be overstated. Poorly planned builds can lead to part failures, increased material consumption, and longer production times, ultimately impacting the bottom line. On the other hand, a well-planned MJF build can yield significant benefits, such as:
- Improved part quality and dimensional accuracy
- Reduced post-processing requirements
- Optimized material usage and cost savings
- Faster turnaround times and increased productivity
To streamline your MJF build planning process, it is essential to follow a systematic approach that addresses the key aspects of the technology. This includes:
- Material selection: Choose materials that are compatible with MJF and align with the desired properties and performance of the final part.
- Part orientation: Analyze part geometry to determine the optimal orientation that minimizes support structures, enhances surface quality, and ensures consistent mechanical properties.
- Design optimization: Implement design strategies that leverage the capabilities of MJF, such as lattice structures, topology optimization, and wall thickness considerations.
- Process guidelines: Adhere to best practices for layer thickness, support structure generation, and post-processing techniques to achieve the desired results.
By focusing on these critical elements and continually refining your MJF build planning strategies, you can unlock the full potential of this advanced 3D printing technology. Whether you are producing functional prototypes, end-use parts, or custom tooling, effective build planning is the foundation for success in MJF manufacturing.
Step 1: Material Selection for MJF
Selecting the right material is a crucial step in MJF build planning. HP's MJF technology is compatible with a range of thermoplastic materials, each with unique properties and characteristics. The most commonly used materials in MJF include:
- PA11: Known for its excellent chemical resistance and ductility, PA11 is ideal for applications requiring flexibility and durability.
- PA12: This versatile material offers a balance of strength, stiffness, and thermal stability, making it suitable for a wide range of functional parts.
- PP: Polypropylene (PP) is lightweight, resistant to fatigue, and offers good chemical resistance, making it an excellent choice for automotive and industrial applications.
- TPU: Thermoplastic polyurethane (TPU) is a flexible and elastic material that can withstand repeated stress and strain, making it suitable for applications requiring high impact resistance.
When selecting a material for your MJF build, consider the specific requirements of your application:
- Mechanical properties: Evaluate the strength, stiffness, and toughness needed for your part to perform its intended function.
- Chemical resistance: Assess the part's exposure to chemicals, oils, or other substances that may degrade the material over time.
- Thermal stability: Consider the temperature range in which the part will operate and choose a material that can withstand those conditions.
- Flexibility and elasticity: Determine if your application requires a material that can flex or stretch without breaking.
In addition to these properties, it is essential to consider the impact of material choice on the MJF printing process itself. Different materials may require adjustments to process parameters, such as layer thickness, printing temperature, and cooling time, to achieve optimal results.
By carefully evaluating your application requirements and understanding the capabilities of each material, you can make an informed decision that balances performance, cost, and manufacturability. Collaborating with material suppliers and staying updated with the latest developments in MJF-compatible materials can further expand your options and enable you to push the boundaries of what is possible with this technology.
Step 2: Optimize Part Orientation
Optimizing part orientation is a critical aspect of MJF build planning that can significantly impact the quality, efficiency, and cost of your 3D printed parts. The orientation of a part within the build chamber determines how it will be sliced into layers and affects various factors such as support structure requirements, surface finish, and mechanical properties.
To optimize part orientation for MJF, consider the following strategies:
1. Minimize support structures
- Analyze part geometry: Identify overhanging features, bridges, and other areas that may require support structures.
- Orient for self-supporting: Position the part in a way that minimizes the need for supports, leveraging the inherent strength of the material and the capabilities of MJF technology.
- Reduce support volume: If supports are unavoidable, orient the part to minimize the volume of support material required, reducing material consumption and post-processing time.
2. Improve surface finish
- Align critical surfaces: Orient the part so that critical surfaces, such as those requiring a smooth finish or precise dimensions, are positioned parallel to the XY plane of the build chamber.
- Minimize visible layer lines: Consider the visibility of layer lines on the final part and orient it to minimize their appearance on important surfaces.
- Leverage MJF's capabilities: Take advantage of MJF's ability to produce high-quality surfaces without the need for extensive post-processing, such as chemical smoothing or sanding.
3. Ensure consistent mechanical properties
- Consider load distribution: Analyze the expected load and stress distribution on the part and orient it to maximize its strength and durability.
- Align with print direction: Orient the part so that its critical load-bearing features are aligned with the print direction, as MJF parts typically exhibit higher strength in the XY plane compared to the Z direction.
- Optimize for isotropy: When possible, orient the part to promote isotropic mechanical properties, ensuring consistent performance regardless of the direction of applied forces.
By carefully considering these factors and experimenting with different orientations, you can find the optimal balance between part quality, efficiency, and cost. Specialized software tools and simulation capabilities can further assist in this process, allowing you to visualize and analyze the impact of different orientations before committing to a final build setup.
Remember, the ideal part orientation may vary depending on the specific geometry, material, and application requirements of your project. Continuously refining your orientation strategies and learning from previous builds will help you develop a keen eye for optimizing MJF parts and achieving the best possible results.
Step 3: Design Considerations for MJF
To fully leverage the capabilities of MJF technology and ensure successful builds, it is essential to incorporate specific design considerations into your part development process. By optimizing your designs for MJF, you can improve part performance, reduce manufacturing costs, and streamline the overall production workflow.
1. Wall thickness and feature size
- Maintain minimum wall thickness: Ensure that your part designs adhere to the recommended minimum wall thickness for MJF, typically around 0.8-1.0 mm, to prevent warping, distortion, or breakage during printing.
- Avoid overly thick walls: Excessively thick walls can lead to longer cooling times, increased material consumption, and potential issues with dimensional accuracy. Aim for a balanced wall thickness throughout your design.
- Consider feature size limitations: Be aware of the minimum feature size that MJF can accurately reproduce, usually around 0.5 mm, and design your parts accordingly to avoid print failures or loss of detail.
2. Clearances and tolerances
- Allow for adequate clearances: When designing parts with moving components or assemblies, provide sufficient clearance between mating surfaces to account for the inherent tolerances of the MJF process and ensure smooth operation.
- Consider post-processing effects: If your parts require post-processing steps, such as sanding or painting, factor in the additional material removal or added thickness when specifying clearances and tolerances.
- Leverage MJF's accuracy: Take advantage of MJF's high dimensional accuracy, typically within ±0.2 mm, to create precise and well-fitting parts that require minimal post-processing.
3. Design for nesting and build efficiency
- Optimize part nesting: Carefully arrange your parts within the build chamber to maximize space utilization and minimize the number of builds required, reducing overall production time and cost.
- Consider part orientation: As discussed in the previous section, part orientation plays a crucial role in build efficiency. Design your parts with optimal orientation in mind, minimizing support structures and maximizing packing density.
- Consolidate multiple parts: Where possible, consolidate multiple components into a single, more complex part to reduce assembly time and simplify the overall manufacturing process, taking advantage of MJF's ability to produce intricate geometries.
4. Strength and aesthetics
- Incorporate lattice structures: Utilize lattice structures to reduce part weight, improve strength-to-weight ratios, and enhance the overall performance of your designs. MJF's high resolution enables the creation of intricate lattice patterns.
- Optimize for load distribution: Analyze the expected loads and stresses on your part and design features that distribute these forces evenly, such as ribs, fillets, or internal structures.
- Consider surface textures: Take advantage of MJF's ability to produce textured surfaces, such as knurling or patterning, to improve grip, aesthetics, or functionality without the need for additional post-processing.
By incorporating these design considerations into your MJF parts, you can create high-quality, efficient, and visually appealing products that meet the demands of your specific application. Continuously refining your design strategies and staying updated with the latest advancements in MJF technology will help you push the boundaries of what is possible and unlock new opportunities for innovation.
Step 4: Process Guidelines for MJF
To achieve consistent, high-quality results with MJF technology, it is crucial to adhere to best practices and process guidelines throughout the build planning and execution stages. By following these guidelines, you can optimize your MJF workflow, reduce the risk of print failures, and ensure that your parts meet the desired specifications.
1. Layer thickness and resolution
- Select appropriate layer thickness: Choose a layer thickness that balances resolution, surface quality, and build time. Thinner layers produce smoother surfaces and finer details but increase the overall print duration.
- Consider the trade-offs: Evaluate the specific requirements of your application and select a layer thickness that delivers the necessary level of detail and surface finish while maintaining acceptable build times and costs.
- Leverage MJF's high resolution: Take advantage of MJF's ability to produce layers as thin as 80 microns (0.08 mm) to create parts with intricate features and smooth surfaces.
2. Support structure generation
- Minimize support structures: As discussed in the part orientation section, design your parts and orient them in a way that minimizes the need for support structures, reducing material consumption and post-processing time.
- Use automated support generation: Utilize software tools that automatically generate optimized support structures based on your part geometry and orientation, ensuring adequate support while minimizing material usage.
- Consider support removal: When designing support structures, consider the ease of removal during post-processing. Use breakaway supports or design supports with accessible connection points for easier cleaning.
3. Post-processing techniques
- Remove excess powder: After printing, remove any excess powder from the part using compressed air, brushes, or other suitable methods to ensure a clean surface and prevent contamination.
- Perform necessary cleaning: Depending on the material and application, parts may require additional cleaning steps, such as washing with water or solvent, to remove any residual agents or debris.
- Consider surface treatments: If your application requires a specific surface finish or appearance, explore post-processing techniques such as sanding, polishing, dyeing, or painting to achieve the desired result.
To stay at the forefront of MJF technology and continuously improve your build planning processes, it is essential to stay informed about the latest developments and best practices in the field. Regularly review industry publications, attend webinars and conferences, and engage with the MJF community to gain insights and learn from the experiences of others.
Software tools and digital manufacturing platforms, like those offered at Phasio, can further streamline your MJF workflow by providing features such as:
- Build simulation: Simulate the MJF build process to identify potential issues, optimize part placement, and minimize the risk of print failures.
- Error prediction: Analyze part geometries and identify areas that may be prone to distortion, warping, or other defects, allowing you to make necessary design adjustments before printing.
- Process parameter optimization: Automatically determine the optimal process parameters, such as layer thickness, printing temperature, and cooling time, based on your specific material and application requirements.
By leveraging these tools and staying updated with the latest MJF process guidelines, you can streamline your build planning, reduce lead times, and consistently produce high-quality parts that meet the demands of your customers and end-users.
Tips on Enhancing MJF Build Quality
- Regularly update design software: Stay current with the latest versions of your CAD and 3D printing software to ensure compatibility with MJF advancements and access new features that can improve your build planning processes.
- Collaborate with material suppliers: Engage with material suppliers to stay informed about new MJF-compatible materials, their properties, and best practices for processing. This collaboration can help you identify opportunities for innovation and optimize your material selection strategies.
- Conduct post-build analysis: Regularly analyze completed MJF builds to identify areas for improvement, such as part placement, support structure design, or process parameter settings. Use this data to refine your build planning strategies and continuously enhance the quality and efficiency of your MJF parts.
By implementing these tips and continually refining your MJF build planning processes, you can unlock the full potential of this advanced 3D printing technology and stay ahead of the competition. As MJF continues to evolve and new materials, software tools, and best practices emerge, maintaining a proactive approach to build planning will be essential for success in the rapidly advancing world of additive manufacturing.
Streamlining your Multi Jet Fusion (MJF) build planning process is essential for achieving efficient production and optimal resource utilization. A structured approach not only enhances product quality but also leverages the full potential of MJF technology. This involves integrating precise material selection, optimal orientation, and strategic design considerations, all supported by robust process guidelines.
Importance of Planning for Efficient MJF Processes
Successful MJF 3D printing relies on detailed strategic planning. This means understanding the machine's operational parameters and the specific characteristics of the materials employed. It's crucial to assess each component of the build to ensure the printer functions at its peak, minimizing errors and enhancing throughput. A methodical approach to planning reduces both waste and operational costs, optimizing the build volume utilization and resulting in quicker production cycles.
Leveraging digital tools enhances planning by allowing for simulations that preemptively identify potential issues. This foresight enables necessary adjustments, conserving both time and materials. By adopting these strategic practices, manufacturers can transition smoothly from design to production, maximizing process efficiency.
Benefits of Optimizing MJF Build Planning
Optimizing the MJF build planning process provides significant advantages, such as enhanced precision and repeatability in part production. By focusing on critical areas like material selection and part alignment, manufacturers can strengthen mechanical properties and ensure uniformity across batches. This uniformity is vital for fields requiring high accuracy and reliability.
Moreover, an optimized planning process drives cost-effectiveness by reducing the reliance on support structures, trimming material expenditure while upholding quality. This efficiency extends to post-processing, where less waste and greater precision result in reduced finishing time and effort.
Advanced design approaches, such as implementing lattice structures and leveraging generative design, further augment the benefits of streamlined planning. These strategies not only minimize material usage but also boost the performance and strength of parts. By continuously refining build strategies, manufacturers can maintain a competitive advantage in the dynamic field of additive manufacturing.
Step 1: Material Selection for MJF
Choosing the right material is pivotal to the success of any MJF endeavor, as it dictates the final part's performance and resilience. The MJF process offers a diverse array of materials, each tailored to meet specific application requirements. For instance, PA11, PA12, PP, and TPU offer distinctive attributes that cater to various industrial needs, from flexibility to impact resistance.
In evaluating materials for MJF, one must consider how well the material integrates with the technology's unique processes. PA11 is celebrated for its superior resistance to chemicals and its ability to withstand repeated stress, making it suitable for dynamic applications. Conversely, PA12 is valued for its robust thermal properties and dimensional stability, making it ideal for precision parts. Polypropylene (PP) is lightweight and offers excellent fatigue resistance, making it a preferred choice for components where weight reduction is crucial. TPU's strength lies in its elasticity and durability, perfect for applications that demand flexibility and resilience.
To ensure optimal material selection, focus on these critical aspects:
- Load Bearing Capabilities: Determine the mechanical forces your component will face and select a material that can endure these conditions without compromising structural integrity.
- Elasticity Requirements: For parts needing frequent bending or stretching, prioritize materials with high resilience to maintain performance over time.
- Environmental Compatibility: Consider the operational environment, including exposure to chemicals and temperature extremes, to ensure the material remains stable and effective.
Selecting an appropriate material impacts not only the functionality of the part but also the efficiency of the MJF process, affecting factors like energy consumption and cycle time. By aligning material properties with specific application needs and technological capabilities, manufacturers can achieve superior quality and process efficiency. Keeping abreast of emerging materials and advancements will further enhance material selection strategies, fostering innovation and competitive advantage.
Step 2: Optimize Part Orientation
Part orientation in MJF printing is pivotal for achieving desired outcomes in terms of quality, strength, and aesthetics. By evaluating the geometry of each component, manufacturers can strategically position parts to minimize reliance on additional support structures. This strategic positioning not only conserves material but also streamlines post-processing activities, enhancing overall efficiency. Effective orientation leverages the natural properties of the material and the capabilities of the MJF process, ensuring robust structural outcomes.
Positioning components to minimize the appearance of layer lines directly influences surface quality. By aligning parts such that critical surfaces lie parallel to the primary build plane, the visual and tactile quality of the finished product is significantly enhanced. This approach is crucial for applications demanding high aesthetic standards or precision fitment. Furthermore, reducing visible layer lines cuts down the need for extensive post-processing, such as surface smoothing, thereby preserving the dimensional fidelity of the parts.
To maintain consistent mechanical performance across the part, orientation should be informed by an understanding of stress pathways and load distribution. Aligning features such as reinforcements with anticipated force vectors enhances the component's ability to withstand operational stresses. This strategic alignment ensures the part performs reliably in its intended application. Additionally, efforts to achieve isotropic strength properties are beneficial, promoting uniformity in performance irrespective of the direction of applied forces. This requires a nuanced approach, balancing design constraints with functional imperatives, often necessitating iterative refinement to achieve optimal results.
Step 3: Design Considerations for MJF
In the realm of Multi Jet Fusion, design intricacies play a pivotal role in determining the success of a build. Attention to detail in the design phase ensures that parts not only meet functional requirements but also capitalize on the unique advantages of MJF technology. Key design considerations encompass wall thickness, clearances, and nesting strategies, each contributing to optimal build performance and structural integrity.
Wall Thickness and Clearances
Achieving the right balance in wall thickness is essential for both efficiency and reliability. Thin walls, while beneficial for reducing weight, can compromise the strength of a part if not carefully calculated. A thickness of at least 1 mm in critical areas ensures robustness without excessive material use. This approach helps maintain the dimensional accuracy needed for high-performance applications.
Clearances must be thoughtfully incorporated into designs, especially when dealing with components that require movement or assembly. Providing sufficient space between parts prevents them from adhering during the printing process and ensures that each component functions as intended. This precision in design offsets potential variances in the MJF production process.
Nesting Strategies for Efficiency
Effective nesting is a cornerstone of maximizing the potential of MJF. By arranging parts strategically within the build chamber, manufacturers can enhance space utilization and streamline production workflows. This approach reduces the number of builds required, ultimately lowering costs and increasing throughput.
To optimize nesting, consider the geometric compatibility and orientation of parts within the build volume. Tools that simulate nesting configurations can prove invaluable, helping to identify the most advantageous layouts. Such strategic planning ensures that every build maximizes both material efficiency and production speed.
Enhancing Strength and Aesthetics
Incorporating advanced design features can significantly bolster both the structural integrity and visual appeal of parts. For example, employing cantilevered support structures can enhance load distribution, providing additional strength without unnecessary weight. This technique leverages MJF's ability to create complex geometries that contribute to overall part performance.
Aesthetic enhancements, such as incorporating fine embossed details or unique surface textures, can be achieved directly through the MJF process. By designing these features into the model, manufacturers can produce parts that are not only functional but also visually striking, meeting the specific aesthetic requirements of their applications.
Step 4: Process Guidelines for MJF
To achieve efficient and successful MJF processes, implementing comprehensive guidelines tailored to MJF's specific capabilities is vital. These guidelines focus on the strategic optimization of layer thickness, the intelligent reduction of support structures, and the integration of cutting-edge software tools for enhanced build accuracy and problem-solving.
Layer Thickness and Support Structure Optimization
Choosing the right layer thickness is crucial for balancing detail fidelity and production speed. With MJF, adjusting layer height can significantly influence surface finish and feature definition. For intricate parts demanding high precision, finer layers—around 80 microns—are recommended, as they capture detailed geometries effectively. Conversely, thicker layers can expedite builds when detail is less critical, optimizing throughput without compromising essential part attributes.
Reducing reliance on support structures can conserve resources and streamline post-production. By strategically positioning parts and utilizing MJF's inherent ability to support complex geometries, manufacturers can decrease the need for additional supports. This strategy not only saves material but also enhances the final surface quality of parts. Advanced software tools can aid this process by evaluating part geometries and suggesting optimal support placements or even eliminating unnecessary supports altogether.
Harnessing Digital Manufacturing Trends
Keeping current with the latest MJF technological advancements provides a competitive advantage. Engaging with digital platforms offers insights into cutting-edge techniques and material developments, allowing manufacturers to refine their processes in real-time. This proactive approach ensures process parameters are continuously optimized, adapting to variables like material flow and environmental conditions, ultimately leading to more consistent quality and efficiency.
Predictive modeling and simulation tools have revolutionized error mitigation in MJF. By replicating the build process virtually, these tools allow manufacturers to anticipate and address potential issues, such as thermal distortions, before they occur. This foresight is invaluable, enabling adjustments that prevent defects and ensure smooth production runs. By incorporating these predictive capabilities, manufacturers can maintain high standards of quality while reducing downtime and material waste.
Software Tools for Enhanced Production
The role of sophisticated software tools in MJF cannot be overstated. These tools offer detailed simulations of the entire production cycle, from initial setup to final post-processing, providing critical insights into potential inefficiencies. By exploring various configurations virtually, manufacturers can optimize builds without the risk of costly errors or delays.
Error prediction technologies further enhance production reliability by identifying weak points in the design or process that could lead to failures. With these insights, manufacturers can implement robust corrective measures, ensuring that each build proceeds as planned. The integration of these advanced tools into the MJF workflow not only elevates the quality and uniformity of outputs but also yields valuable data for future projects, fostering a culture of continuous improvement and excellence in additive manufacturing.
Tips on Enhancing MJF Build Quality
In the pursuit of superior MJF build quality, the integration of cutting-edge techniques and continuous refinement of strategies is essential. This approach not only involves leveraging advancements in technology and materials but also requires a commitment to ongoing process evaluation and improvement.
Regular Software Enhancements
Keeping design software aligned with the latest MJF innovations is crucial for maintaining high-quality builds. This involves not just routine updates but a proactive approach to integrating advanced features and functionalities. Enhanced simulation tools, for instance, can predict potential issues before they arise, allowing for preemptive adjustments. By optimizing how design tools interact with updated hardware and novel materials, manufacturers can significantly improve precision and efficiency across the production cycle.
Engaging with Material Innovators
Developing a strong rapport with material innovators can open doors to groundbreaking advancements in MJF applications. These collaborations offer access to pioneering material solutions that drive performance improvements across various parameters, such as tensile strength and thermal stability. Engaging with these innovators provides a comprehensive understanding of how new materials behave under different conditions, enabling you to tailor applications that meet specific industry demands. This strategic partnership not only enhances your material selection process but also offers valuable insights into material processing and optimization.
Systematic Post-Production Evaluation
Implementing a rigorous post-production evaluation framework is vital for identifying and addressing inconsistencies in the build process. This involves a meticulous analysis of completed parts, focusing on key metrics such as mechanical integrity and surface smoothness. By capturing and analyzing data on production outcomes, manufacturers can pinpoint areas for refinement and adjust future build parameters accordingly. This iterative process fosters a culture of continuous enhancement, where insights gained from each analysis inform subsequent builds, ultimately leading to improved reliability and efficiency in MJF production.
Streamlining your MJF build planning process is an ongoing journey that requires a commitment to continuous improvement and innovation. By leveraging cutting-edge tools, collaborating with material experts, and systematically analyzing production outcomes, you can unlock the full potential of this transformative technology and stay ahead in the rapidly evolving landscape of additive manufacturing. If you're ready to take your MJF build planning to the next level, schedule a demo or try the platform to experience how we can help you optimize your processes and achieve unparalleled results.