How MJF Stacks Up: A Comparison of Dimensional Accuracy in 3D Printing
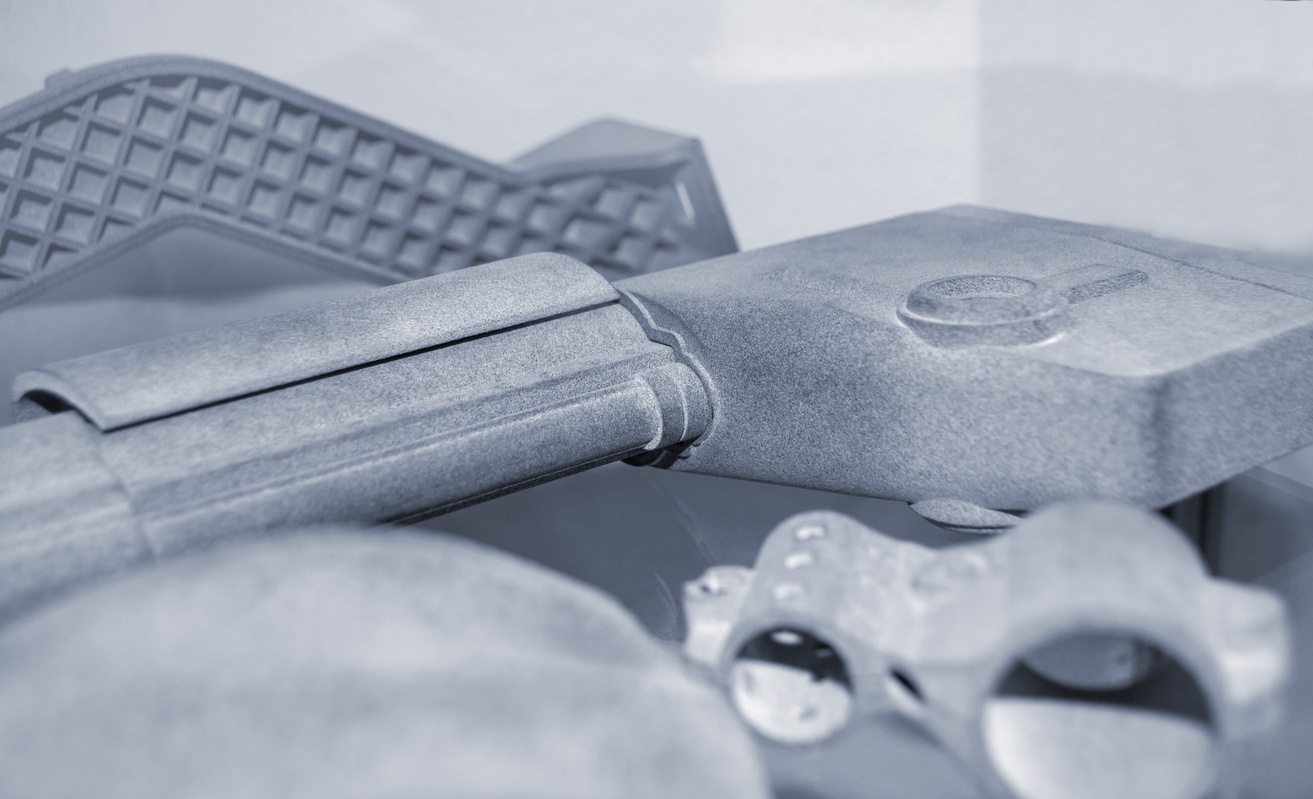
In the world of additive manufacturing, dimensional accuracy is a critical factor that determines the success of a 3D printed part. Multi Jet Fusion (MJF), a cutting-edge 3D printing technology, has garnered attention for its ability to produce parts with exceptional dimensional accuracy and precision.
As manufacturers and engineers seek to optimize their production processes, understanding the intricacies of dimensional accuracy in MJF becomes paramount. By delving into the factors that influence accuracy and exploring best practices for design, businesses can unlock the full potential of this advanced technology.
This article aims to provide a comprehensive overview of dimensional accuracy in MJF 3D printing, equipping readers with the knowledge necessary to make informed decisions and achieve superior results in their manufacturing endeavors. Let's embark on this journey to unravel the secrets behind MJF's remarkable accuracy and precision.
What is Dimensional Accuracy in 3D Printing?
Dimensional accuracy in 3D printing refers to how closely a printed part matches the original CAD design dimensions. It is a crucial metric that determines the functional performance and quality of the final product. Accuracy measures the deviation between the intended and actual dimensions, while precision refers to the consistency and repeatability of the 3D printing process in producing parts with the same dimensions.
To ensure that a 3D printed part meets the required specifications, manufacturers must consider the acceptable range of deviation from the specified dimensions, known as tolerance. Tolerance is determined by the specific application requirements and can vary depending on the industry and intended use of the part.
Several factors can influence the dimensional accuracy of 3D printed parts:
- Material properties: Characteristics such as shrinkage, warping, and layer adhesion can impact the final dimensions of the printed part. Different materials exhibit varying levels of dimensional stability, and understanding these properties is essential for achieving accurate results.
- 3D printer hardware: The resolution, calibration, and build volume of the 3D printer play a significant role in determining dimensional accuracy. Higher resolution printers can produce finer details and more precise dimensions, while proper calibration ensures consistent performance across multiple prints.
- Post-processing techniques: Support removal and surface finishing processes can affect the final dimensions of the printed part. Careful consideration must be given to the methods used to remove support structures and smooth surfaces to maintain dimensional accuracy.
By understanding these factors and implementing appropriate design and processing strategies, manufacturers can optimize the dimensional accuracy of their 3D printed parts using technologies like Multi Jet Fusion offered by companies such as Phasio. In the following sections, we will explore how MJF compares to other 3D printing technologies in terms of dimensional accuracy and discuss best practices for achieving precise and consistent results.
Comparing the Dimensional Accuracy of MJF and SLS
Overview of Multi Jet Fusion (MJF) Technology
Multi Jet Fusion (MJF) represents a significant advancement in additive manufacturing, offering a precise method for crafting intricate geometries. This technology utilizes an inkjet array to meticulously apply fusing and detailing agents onto a polymer powder bed, activating thermal fusion. This approach negates the need for additional support structures, enabling the creation of complex designs with exceptional precision. MJF consistently achieves tolerances around ± 0.2% and maintains a minimum threshold of ± 0.2 mm. Such accuracy positions MJF as a preferred choice for sectors demanding high-precision components, marking it as a leader in delivering detailed and reliable 3D printed parts.
Selective Laser Sintering (SLS) Process and Accuracy
Selective Laser Sintering (SLS) offers a robust alternative, employing targeted laser beams to sinter polymer powder particles incrementally. This layer-by-layer process also eliminates the requirement for support structures, facilitating the production of complex forms. SLS achieves dimensional tolerances of ± 0.3% with a lower boundary of ± 0.3 mm, providing solid reliability though slightly less precision compared to MJF. Despite this, SLS remains highly valued for its versatility in material selection and ability to handle intricate designs, making it a staple in industries where precision is important but not the sole priority.
Head-to-Head Comparison Studies
Comparative analyses between MJF and SLS illuminate their distinct strengths. Research indicates that MJF outshines SLS in terms of dimensional accuracy, with observed deviations between 2.1-5.2%, while SLS exhibits a range of 5-7%. This difference manifests significantly in applications requiring superior surface finish and detail clarity. MJF's capability to render finer details and smoother surfaces underscores its suitability for projects where aesthetic quality and precision are essential. These insights guide manufacturers in selecting the appropriate technology based on their specific design and functional requirements, leveraging MJF's strengths for high-precision tasks.
Design Considerations for Optimizing MJF Part Accuracy
Minimum Feature Sizes and Wall Thicknesses
Multi Jet Fusion (MJF) technology offers the flexibility to create features with impressive detail, making it essential to carefully consider feature sizes and wall thicknesses in your designs. MJF can achieve wall thicknesses as thin as 0.3 mm and produce features as small as 0.1 mm. While it can handle these fine details, opting for slightly larger features and thicker walls can improve the stability and accuracy of the printed parts. This approach helps to ensure that the parts are robust and less susceptible to potential deformations during the printing and post-processing stages.
Orientation and Geometry Best Practices
Effective part orientation within the MJF build environment can greatly enhance the dimensional accuracy and quality of the final product. By minimizing the cross-sectional area of each layer, the risk of warping is reduced. Large, flat surfaces are particularly prone to curling, so incorporating design elements such as ribs or lattices can provide additional support and stabilization. Additionally, ensuring uniform wall thicknesses and gradual transitions between different sections helps to manage internal stresses, thereby maintaining the integrity of the part's dimensions.
Leveraging the Capabilities of MJF
The capabilities of MJF are particularly suited for creating parts with fine details and complex geometries. This technology allows for the integration of multiple components into a single print, which can enhance the precision of assembly fits and minimize issues related to tolerance accumulation. By taking advantage of these capabilities, manufacturers can streamline production processes and achieve designs that are difficult to realize with conventional methods. This not only facilitates innovation but also improves efficiency and performance in the final product.
The Bottom Line on MJF Dimensional Accuracy
Multi Jet Fusion (MJF) stands out for its remarkable ability to produce parts with high dimensional fidelity, establishing a benchmark in the 3D printing industry. This technology's strengths lie in its capacity to handle intricate designs with ease, ensuring precision that meets the rigorous demands of modern manufacturing. Through thoughtful design optimization and strategic orientation, manufacturers can achieve exceptional outcomes that align with tight dimensional requirements. This capability makes MJF particularly effective for crafting both detailed prototypes and robust end-use parts.
The adaptability of MJF extends its applicability across diverse sectors, supporting projects that require intricate detailing and structural robustness simultaneously. MJF excels in producing components where geometric intricacy is paramount, maintaining dimensional integrity without compromising on structural soundness. This technology integrates seamlessly into various production processes, providing consistency and reliability. As a result, MJF becomes a vital asset in creating parts that demand meticulous adherence to specifications, regardless of whether they are in the prototyping phase or destined for final production.
In essence, MJF empowers engineers and designers to explore the full potential of additive manufacturing, enabling innovations that translate seamlessly into high-quality, precisely crafted components. With its unparalleled accuracy, MJF supports forward-thinking businesses in pushing the boundaries of design and functionality, ensuring that their creations meet both aesthetic and practical standards. As industries evolve, the role of MJF in delivering dimensionally precise and reliable parts will be increasingly significant, reinforcing its position as a cornerstone of cutting-edge manufacturing.
As you explore the possibilities of additive manufacturing and strive for dimensional accuracy in your 3D printed parts, Multi Jet Fusion emerges as a technology that can elevate your designs to new heights. We invite you to schedule a demo or try the platform to experience its capabilities firsthand. Let us help you unlock the full potential of MJF and revolutionize your manufacturing processes.