How to Enhance Your MJF Production Workflows for Efficiency
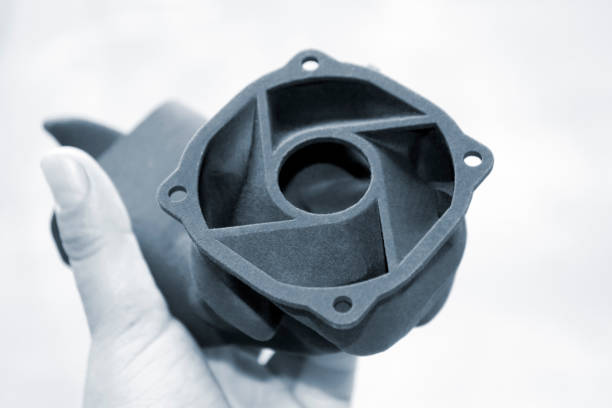
Multi Jet Fusion (MJF) has revolutionized the additive manufacturing landscape, offering unprecedented speed, precision, and cost-effectiveness for producing high-quality parts. As more manufacturers adopt this technology, optimizing MJF production workflows becomes crucial to maximizing its benefits.
Enhancing your MJF production workflows involves a systematic approach that encompasses careful planning, material selection, process automation, and post-processing techniques. By focusing on these key areas, you can significantly improve efficiency, reduce waste, and deliver superior parts to your customers.
In this article, we'll delve into the intricacies of MJF production workflows and explore practical strategies to optimize each phase of the process. Whether you're a seasoned MJF user or considering integrating this technology into your manufacturing operations, these insights will help you unlock the full potential of MJF and stay ahead of the competition.
What is MJF Production Workflow?
MJF Production Workflow refers to the end-to-end process of creating parts using HP's Multi Jet Fusion technology. It encompasses all the steps involved, from design and material selection to printing, post-processing, and quality control. The goal of an MJF Production Workflow is to streamline the entire process, minimizing lead times and maximizing efficiency without compromising on part quality.
A well-optimized MJF Production Workflow takes into account the unique characteristics of the technology, such as the ability to nest multiple parts in a single build, the use of fusing and detailing agents, and the need for efficient cooling and powder recovery. By carefully planning and executing each phase of the workflow, manufacturers can take full advantage of MJF's speed, precision, and versatility.
Key components of an MJF Production Workflow include:
- Design Optimization: Ensuring that part designs are optimized for MJF printing, considering factors such as wall thickness, feature size, and orientation to minimize warping and maximize build efficiency.
- Material Selection: Choosing the most suitable MJF material, such as HP's PA12 or PA11, based on the part's intended application, required mechanical properties, and cost considerations.
- Build Planning: Strategically arranging parts within the build chamber to maximize packing density, minimize material waste, and ensure consistent part quality across the build.
- Post-Processing: Efficiently removing excess powder, applying surface treatments, and conducting quality control measures to achieve the desired final part properties and appearance.
By optimizing each of these components and leveraging automation tools like those offered at Phasio, manufacturers can create a seamless and efficient MJF Production Workflow that delivers high-quality parts faster and more cost-effectively than ever before.
How to Enhance Your MJF Production Workflows
Enhancing your MJF production workflows requires a deep dive into the process dynamics. A key starting point involves refining build execution strategies to enhance material efficiency and output quality. By tailoring your design specifications to align with the machine's operational strengths, you can maximize efficiency. Employing advanced nesting algorithms can facilitate the simultaneous production of diverse components, optimizing the use of available space and resources.
Choose Optimal Material Solutions
Identifying the right materials is crucial for achieving excellence in MJF production. Materials like Nylon PA12 and PA11 are known for their robust mechanical attributes and adaptability. When selecting, consider factors like durability, flexibility, and thermal resistance specific to your application needs. This strategic selection can reduce the need for modifications during post-processing, allowing for seamless integration into the production line.
Leverage Advanced Automation
Integrating advanced automation solutions into your MJF workflows can dramatically reduce manual tasks and error rates. By implementing intelligent software for order and inventory management, you can ensure precise and swift operations. These systems can handle intricate data sets and calculations, freeing personnel to concentrate on strategic improvements. Automation not only complements MJF's rapid capabilities but also ensures consistent workflow efficiency.
Refine Post-Processing Methods
To achieve exceptional finishes on MJF parts, refining post-processing methods is essential. Techniques such as media blasting and the efficient reuse of leftover materials enhance surface aesthetics and minimize waste. By continuously optimizing these processes, manufacturers can deliver parts that meet high standards while controlling costs. Regular assessments of these methods ensure the outputs align with MJF's potential for quality and innovation.
By focusing on strategic enhancements in these areas, manufacturers can fully harness the capabilities of MJF technology, driving improvements in both efficiency and product quality.
Step 1: Optimize MJF Build Planning
Crafting an efficient MJF build plan involves harmonizing the intricate details of part design with the capabilities of the MJF printer, aiming to minimize both production time and material waste. This process commences with a thorough evaluation of part geometry, focusing on how these elements can be best utilized within the printer's operational framework. By aligning design specifications with machine strengths, production can proceed with greater predictability and control.
Precision in Design Integration
Integrating design elements with the printer's strengths is essential for maximizing efficiency. This includes:
- Optimized Layer Management: Adjusting layer thickness to balance detail with build speed, ensuring that critical features receive the necessary resolution without sacrificing time efficiency.
- Critical Dimension Emphasis: Focusing on dimensions that are vital for functionality, ensuring precise reproduction and reducing the need for extensive post-processing.
- Reduced Complexity: Streamlining complex features where possible to facilitate smoother fabrication and decrease the potential for errors.
These adjustments not only refine material use but also contribute to a smoother production timeline, enhancing the overall reliability of the manufacturing process.
Maximizing Build Volume Efficiency
A pivotal aspect of MJF build planning is the strategic use of available build space. Through sophisticated arrangement techniques, manufacturers can enhance part output per build cycle:
- Spatial Arrangement: Allocating parts within the build area to optimize space usage and reduce voids, enhancing throughput and material efficiency.
- Homogeneous Batch Processing: Organizing parts with similar characteristics to streamline post-processing and minimize handling times.
- Thermal Distribution Balance: Ensuring an even distribution across the build platform to maintain thermal equilibrium and reduce the risk of deformations.
These techniques enable a robust control of the production environment, enhancing the consistency and dependability of the MJF process. By employing these strategies, manufacturers can strike a balance between rapid production and high quality, fully leveraging MJF technology's capabilities.
Step 2: Select Appropriate Materials
Selecting materials for MJF production demands a strategic approach, as the chosen material significantly shapes the performance, durability, and cost-effectiveness of the manufactured parts. Each material's unique attributes must align with the intended application, ensuring the final product meets exacting standards. This alignment enhances both the functional integrity and aesthetic quality of the components.
Evaluating Material Properties for Application
A thorough understanding of material properties is crucial to making informed selections. For example, Nylon PA12’s robustness and fine feature capability make it ideal for applications requiring precision and fine detail. It excels in environments where chemical resistance and surface finish quality are paramount. Conversely, Nylon PA11 offers superior flexibility and resilience, catering to sectors needing materials that can absorb impact without compromising structural integrity, such as in dynamic or high-load scenarios.
- Nylon PA12: Offers excellent surface finish and dimensional stability, suitable for detailed and precise applications.
- Nylon PA11: Provides enhanced elasticity and impact resistance, ideal for applications demanding durability under stress.
These characteristics guide manufacturers in tailoring material choices to specific operational needs, ensuring optimal performance and reliability.
Balancing Economic and Environmental Factors
The economic and environmental implications of material choice extend beyond immediate production needs. While initial costs may vary, leveraging MJF's efficient use of materials can mitigate longer-term expenses. The technology's capability to reuse unfused powder not only reduces waste but also aligns with sustainable manufacturing initiatives. This approach not only supports cost management but also enhances the company's commitment to eco-friendly practices, resonating well with sustainability-conscious stakeholders.
- Economic Viability: Utilizing MJF's material reuse capabilities helps manage costs effectively while ensuring high-quality outcomes.
- Environmental Stewardship: Selecting materials that support recycling and sustainability initiatives contributes to responsible manufacturing.
By integrating these considerations into the material selection process, manufacturers can align their production practices with both fiscal prudence and environmental responsibility, reinforcing MJF technology’s role in modern manufacturing.
Step 3: Implement Automation in Workflow
Incorporating automation into MJF workflows revolutionizes the manufacturing landscape by significantly reducing manual interventions. This shift not only enhances precision but also accelerates production timelines, facilitating more effective resource management. By deploying cutting-edge software solutions, organizations can streamline various workflow components—extending from initial customer engagement to production execution—thereby ensuring seamless operations and robust outcomes.
Streamlining Administrative Processes
A key advantage of automating MJF workflows lies in refining administrative tasks such as quoting and order processing. Automated systems can efficiently generate detailed cost projections, thereby minimizing the manual efforts traditionally involved in these processes. By embedding these systems into the workflow, manufacturers can swiftly address customer needs, enhancing overall service delivery and fostering stronger client relationships.
- Efficient Cost Projections: Implement software that delivers precise cost evaluations swiftly, reducing delays in customer interactions.
- Streamlined Order Handling: Use automated systems to manage order details accurately, ensuring timely and error-free fulfillment.
These improvements refine the entire customer interaction process, transforming inquiries into completed orders with greater speed and reliability, allowing teams to concentrate on strategic initiatives rather than routine tasks.
Enhancing Operational Oversight
Automation also plays a pivotal role in optimizing production oversight and control. Advanced systems can deliver real-time insights, equipping manufacturers with the data needed to manage production cycles proactively. This capability ensures that any discrepancies in the process are quickly identified and corrected, maintaining the high standards synonymous with MJF production.
- Live Data Insights: Utilize systems that provide continuous updates on production metrics, enabling prompt detection and correction of issues.
- Analytics-Driven Strategy: Leverage data analytics to refine workflow patterns, enhancing production strategies through informed insights.
By integrating these strategies, businesses can improve transparency and maintain a firm grip on production processes, ensuring each stage is executed with precision and efficiency. This approach not only enhances product quality but also identifies further areas for optimization, promoting a culture of ongoing enhancement within the organization.
Step 4: Optimize MJF Quoting Process
Refining the quoting process for MJF production demands a blend of precision and expediency in pricing methodologies. This ensures that cost assessments are not only accurate but also enhance the business's ability to quickly respond to customer requests. By implementing sophisticated digital tools, manufacturers can automate cost estimations, factoring in critical elements such as material consumption, part complexity, and production timelines to deliver swift and dependable quotes.
Enhance Pricing Precision
To optimize the quoting process, focus on precision, taking into account every aspect of production meticulously. Consider implementing:
- Comprehensive Cost Analysis: Utilize systems that categorize expenses into detailed sections like raw materials, workforce, and equipment utilization, offering clients a clear and thorough cost overview.
- Flexible Pricing Algorithms: Adopt pricing models that adjust to variations in material costs and manufacturing capabilities, ensuring quotes stay competitive and aligned with market trends.
These strategies not only foster client trust through transparency but also position the business to adjust rapidly to changing operational factors, maintaining a competitive edge in pricing.
Reduce Response Times
A streamlined quoting process significantly reduces response times, enabling manufacturers to address customer inquiries more efficiently. This involves:
- Automated Estimation Tools: Implement technologies that handle standard computations and data management, cutting down on manual input and facilitating quicker quote generation.
- Connected CRM Integration: Link quoting systems with customer relationship management platforms to streamline interactions and ensure seamless communication and follow-up processes.
By prioritizing these elements, manufacturers can ensure that their quoting processes not only meet client expectations for speed but also enhance internal workflow efficiencies, paving the way for improved operational effectiveness across the board. Through these optimizations, the quoting process becomes a pivotal component of the MJF production workflow, driving both customer satisfaction and business growth.
Step 5: Enhance Post-Processing Techniques
Enhancing post-processing techniques in MJF workflows is critical for achieving superior parts that meet rigorous quality standards. This phase involves refining surface finishes and reclaiming materials to maintain an efficient and sustainable production cycle. By focusing on advanced post-processing strategies, manufacturers can elevate both the aesthetic and functional properties of their products, ensuring they meet the diverse needs of various applications.
Surface Finish Optimization
Refining surface finishes requires a combination of precision and the use of advanced techniques. Utilizing methods such as vapor smoothing can significantly enhance the surface quality of MJF parts, providing a polished finish that meets aesthetic and functional requirements.
- Vapor Smoothing: Apply this technique to achieve a high-gloss finish and reduce surface roughness. This method is particularly effective for parts with intricate geometries, improving both appearance and performance.
- Thermal Treatments: Use controlled thermal exposure to enhance surface integrity and eliminate minor imperfections. This step helps in achieving a consistent finish across the entire part, suitable for applications demanding high visual standards.
These techniques ensure that parts not only meet industry standards but also exceed customer expectations in terms of quality and appearance.
Material Reclamation and Cost Efficiency
Implementing effective material reclamation strategies is essential for optimizing cost-efficiency and reducing environmental impact. By adopting comprehensive recycling protocols, manufacturers can maximize resource utilization and support sustainability goals.
- Automated Material Recovery: Develop systems that efficiently segregate reusable material from waste, ensuring consistent quality in recycled powder. This approach minimizes costs and enhances the sustainability of the production process.
- Advanced Recycling Systems: Invest in state-of-the-art recycling technology to refine powder recovery processes, reducing dependency on new material and supporting eco-friendly initiatives.
Focusing on these strategies allows manufacturers to maintain a balance between efficiency, cost management, and environmental responsibility, positioning MJF workflows as a sustainable and competitive choice in modern manufacturing.
Step 6: Monitor and Analyze Workflow Efficiency
Continuous monitoring and analysis of MJF production workflows are pivotal for identifying improvement opportunities and optimizing operational efficiency. This requires a strategic approach to assess current processes, allowing manufacturers to adapt swiftly to market demands and technological advancements. By utilizing comprehensive data insights, businesses can refine their workflows to enhance both productivity and quality.
Establishing Key Performance Metrics
Defining and employing key performance metrics offer a structured method to evaluate workflow efficiency. These metrics should align with production goals, providing clarity on areas needing attention and facilitating informed decision-making for process enhancement.
- Throughput Efficiency: Evaluate the number of parts produced within a given time frame, identifying any discrepancies that may indicate underlying process inefficiencies. This metric helps highlight areas where production speed can be improved.
- Defect Rate Monitoring: Track the frequency and types of defects occurring during production to ensure consistent quality standards. This data aids in implementing targeted quality control measures and reducing waste.
These metrics serve as a benchmark for ongoing process evaluation, ensuring that production remains aligned with business objectives.
Leveraging Feedback Mechanisms for Improvement
Incorporating robust feedback mechanisms is essential for fostering a culture of continuous improvement in MJF workflows. Gathering insights from various stakeholders enables a comprehensive evaluation of the production process, driving enhancements that improve efficiency and outcomes.
- Operator Insight Programs: Develop channels for operators to provide feedback on workflow challenges and potential improvements. Their firsthand experience offers valuable perspectives that can lead to effective, practical solutions.
- Interdepartmental Collaboration: Facilitate regular meetings between departments to discuss workflow efficiencies, leveraging diverse expertise to tackle complex issues. This collaborative approach ensures that improvements are holistic and well-integrated.
By embracing feedback and fostering collaboration, manufacturers can maintain a dynamic workflow that evolves with industry trends and technological innovations, ensuring sustained operational excellence.
Final Thoughts
In the dynamic field of additive manufacturing, Multi Jet Fusion offers novel opportunities for optimizing production workflows. As manufacturers aim to refine their processes, a comprehensive approach that includes leveraging innovative technologies and revisiting traditional methods is essential. By incorporating new techniques and strategies, businesses can enhance the quality and efficiency of their operations, setting new benchmarks for industry standards.
Strategic decisions regarding the use of cutting-edge technologies can significantly influence the success of MJF processes. Integrating digital solutions and exploring advanced methodologies can lead to more efficient resource management and improved workflow synchronization. This alignment not only supports streamlined operations but also fosters an environment conducive to innovative problem-solving.
Moreover, the pursuit of continuous improvement positions manufacturers to adapt to the evolving demands of the market with robustness and flexibility. By adopting a forward-thinking mindset and remaining open to emerging trends, businesses can maintain competitive advantages. This adaptability not only enhances resilience but also ensures that MJF remains a pivotal tool in pushing the boundaries of what's achievable in additive manufacturing.
As you embark on optimizing your MJF production workflows, remember that the journey towards efficiency is an ongoing process that requires dedication and adaptability. We at Phasio are committed to supporting you in this endeavor, providing cutting-edge solutions and expert guidance to help you unlock the full potential of MJF technology. If you're ready to take your MJF production to the next level, schedule a demo or try the platform to experience its capabilities and let us help you revolutionize your manufacturing processes.