How to Implement a Mold Validation System for Quality Assurance
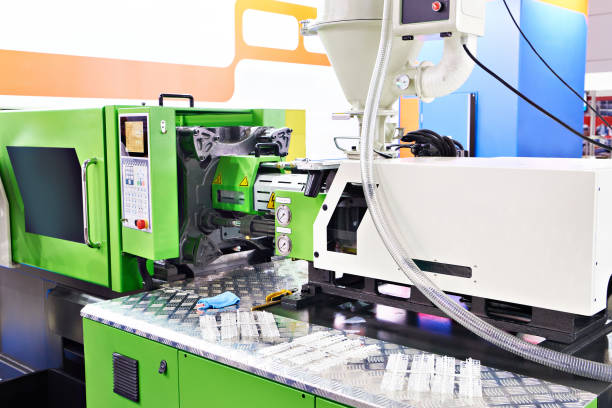
Ensuring consistent quality and reliability in injection molded parts is crucial for manufacturers. Implementing a robust mold validation system is key to achieving this goal.
A well-designed mold validation process helps identify potential issues early, reducing costly defects and waste. It also enables compliance with stringent regulatory requirements, particularly in industries like medical devices and automotive.
By thoroughly validating molds, manufacturers can enhance efficiency, minimize production setbacks, and ultimately deliver products that consistently meet or exceed customer expectations. Let's explore the essential components of an effective mold validation system and how to implement it for optimal results.
What is a Mold Validation System?
A mold validation system is a comprehensive set of procedures and protocols designed to confirm that an injection mold consistently produces parts meeting predefined quality criteria. It involves a series of tests, inspections, and evaluations aimed at verifying the mold's performance and the resulting parts' conformance to specifications.
The primary objectives of a mold validation system are:
- Consistency: Ensuring the injection molding process consistently delivers parts with the same quality attributes, which is crucial in industries like automotive, aerospace, and medical devices, where precision and uniformity are paramount.
- Cost reduction: Identifying and rectifying potential issues before full-scale production, thus reducing costly defects and waste. It is a preemptive measure to prevent production setbacks.
- Regulatory compliance: Meeting legal requirements in industries like medical devices and pharmaceuticals, where process validation is often mandatory to avoid severe consequences.
Mold validation typically involves several stages, including installation qualification (IQ), operational qualification (OQ), and performance qualification (PQ). Each stage has specific objectives and criteria that must be met before proceeding to the next phase.
During the IQ stage, the mold is inspected to ensure it is installed correctly and functions as intended. This includes using scientific injection molding (SIM) tools to generate a cosmetic process window and conducting initial dimensional evaluations through first article inspection reports (FAIR).
The OQ stage focuses on verifying the process's capability to produce parts meeting customer requirements, even at the edge of the process window. This involves conducting design of experiments (DOE) to understand the relationship between process factors and outputs, creating response surfaces to model process behavior, and validating worst-case scenarios.
Finally, the PQ stage confirms the process's ability to consistently produce conforming parts under normal production conditions, considering multiple setups, shifts, personnel, and material lots. Successful completion of the PQ stage indicates the mold and process are ready for full-scale production.
Implementing a mold validation system requires close collaboration between the manufacturer and the customer to develop a comprehensive validation plan tailored to the specific product and its associated risks. This plan should include detailed protocols, acceptance criteria, and documentation requirements to ensure a thorough and traceable validation process.
By investing in a robust mold validation system, manufacturers can gain a competitive edge through improved quality, reduced costs, and enhanced customer satisfaction. As technology advances, automation and data-driven approaches are increasingly being leveraged to streamline the validation process and enable continuous improvement.
How to Implement a Mold Validation System for Quality Assurance
Setting up a mold validation system ensures that production consistently achieves high standards. A well-organized methodology aids in pinpointing improvement opportunities and upholds compliance with industry benchmarks.
Step 1: Understand the Mold Validation Process
Begin by gaining a comprehensive understanding of the crucial phases involved in mold validation. Each phase plays a vital role in confirming that molds produce parts meeting stringent quality requirements. Initial checks involve thorough examinations to ensure alignment with design expectations. This foundational step guarantees that the mold operates effectively before advancing into the more intricate phases of process validation. Recognizing the significance of each phase within the broader scope of injection molding processes is fundamental for successful execution.
Step 2: Develop a Mold Validation Checklist
Creating an exhaustive checklist is pivotal for maintaining thoroughness and consistency in the validation process. The checklist should encompass all elements of mold testing procedures, including the evaluation criteria for qualification techniques and quality assurance standards. By having such a comprehensive list, manufacturers can systematically ensure that every component of the mold and the process is assessed, leaving no stone unturned. Utilize this checklist as a structured guide to uncover any potential issues right from the start.
Step 3: Conduct Initial Mold Qualification
Conducting the initial qualification involves detailed assessments to verify that the mold satisfies essential operational standards. This phase includes evaluating part dimensions to ensure they meet specified tolerances and checking the visual quality of the parts produced. Any necessary modifications should be documented before moving forward to more extensive process validations. This documentation is vital for maintaining a transparent history of the mold's development and any adjustments made during qualification.
Step 4: Establish Optimal Process Parameters
Following initial qualification, determining and setting optimal process parameters is crucial. Utilize data from preliminary tests to refine factors such as cycle time, pressure, and temperature. These parameters are critical in ensuring that production remains within quality specifications. Ensure that these settings are clearly documented and applied consistently to sustain quality and minimize variability.
Step 5: Execute Process Validation
Process validation entails running trials to confirm that the established process reliably produces parts that meet the required specifications. Implement cutting-edge validation systems to monitor and adjust the process in real-time, addressing any deviations promptly. Compile comprehensive documentation, such as a mold validation report, to substantiate findings and provide an accurate record of the validation process.
Step 6: Address Common Validation Challenges
Anticipate and manage challenges such as shifts in material properties or unexpected production hurdles. Employ stringent quality control measures in mold manufacturing to tackle these issues proactively. Maintain clear communication channels with team members to swiftly address any obstacles encountered during validation, ensuring a seamless transition from validation to full-scale production.
Step 1: Understand the Mold Validation Process
Delving into the mold validation process requires a comprehensive understanding of its distinct phases. This methodology is more than a simple checklist; it's a detailed strategy to ensure the mold's dependability and effectiveness. Each phase is integral and contributes significantly to overall quality assurance in injection molding. The process includes distinct stages that focus on evaluating different aspects of mold performance.
Initially, the focus lies on ensuring the mold meets all installation criteria through preliminary assessments. This phase involves detailed checks to confirm alignment with design expectations, ensuring full operational readiness. By prioritizing these foundational evaluations, potential issues can be identified early, preventing costly errors later. Subsequently, the operational evaluation phase examines how the mold performs under various production conditions, using a systematic approach to analyze process factors. This evaluation helps in pinpointing key areas for process refinement and adjustment.
The final stage emphasizes long-term process efficacy, ensuring the ability to consistently produce parts that meet stringent quality standards. This phase involves rigorous testing under simulated production scenarios to validate the mold's performance over time. Successfully navigating this stage demonstrates that both the mold and its processes can reliably meet regulatory and customer expectations. Mastering each phase ensures that the mold validation system effectively supports high-quality production outcomes.
Step 2: Develop a Mold Validation Checklist
Crafting a meticulous checklist is vital for executing a comprehensive mold validation process. This checklist acts as a cornerstone, steering manufacturers through each pivotal aspect of mold assessment. By thoroughly addressing every component of the validation process, it ensures no detail is overlooked, thereby bolstering the reliability of results.
Initiate the checklist by detailing specific benchmarks for mold evaluation and quality assurance. This should include parameters such as tolerance levels, surface integrity, and compatibility with intended materials. Clearly defining these benchmarks ensures that the mold is evaluated against rigorous industry criteria, facilitating a thorough analysis of its capabilities.
Further, the checklist should outline systematic procedures for recording observations and outcomes during the validation phases. This encompasses noting any discrepancies and the corrective measures implemented. Such structured documentation not only supports a transparent audit trail but also provides actionable insights for enhancing future validation processes. By adhering to a well-defined checklist, manufacturers can confidently verify that all necessary measures have been taken to uphold mold quality and process consistency.
Step 3: Conduct Initial Mold Qualification
The initial qualification phase is crucial in establishing the mold's capability to produce parts that adhere to quality standards. This phase involves a detailed examination focusing on the mold's operational effectiveness and the quality of its output. By meticulously verifying each aspect, manufacturers can ensure the mold's readiness for subsequent validation stages.
Precision and Surface Quality
Evaluating the precision of the mold involves a comprehensive analysis of the parts it produces. This includes using advanced measurement techniques to verify that critical dimensions align with the specified tolerances. It's also essential to assess the surface quality of parts, ensuring that finishes are smooth and free from defects. This step guarantees that the mold produces parts that meet both functional and visual criteria.
Functional Assessment and Records
Conducting a functional assessment involves testing the mold under realistic production conditions to ensure seamless operation. It's important to address any discrepancies or inefficiencies at this stage. Keeping detailed records of these assessments, including any issues encountered and the corrective actions taken, is vital. This documentation serves as an invaluable resource for tracking mold performance over time and guiding future improvements.
Any adjustments necessary during this phase should be clearly documented, detailing the changes implemented and their impact on the mold's performance. This record-keeping ensures transparency and provides a foundation for refining processes as needed. By maintaining comprehensive documentation, manufacturers can facilitate smoother transitions to further validation phases and uphold the integrity of the production process.
Step 4: Establish Optimal Process Parameters
Refining process parameters is essential for achieving seamless mold operation and superior part quality. This stage involves using insights gained from prior validations to calibrate and manage production settings effectively. By zeroing in on critical factors like material flow dynamics and heat management, manufacturers can ensure consistent results that meet stringent specifications.
Identifying Key Parameters
Start by identifying the variables that most critically influence the mold's performance. Analyze findings from the initial qualification to determine which conditions most affect outcomes. Factors such as material viscosity and thermal behavior play a vital role in the molding process's success.
- Material flow dynamics: Controls how efficiently the material fills the mold cavity, impacting both the structural integrity and the surface finish of the final product.
- Thermal management: Involves regulating the cooling process to stabilize the part's form and prevent defects like warping or internal stresses.
Calibration and Record-Keeping
Implement a systematic approach to adjust and perfect these parameters. Conduct methodical trials to explore different configurations and assess their impact on production efficiency and part quality. This iterative testing helps pinpoint the precise settings that optimize performance.
Recording these refined settings is crucial for ensuring uniformity across production cycles. Comprehensive logs allow for the replication of ideal conditions, reducing variability and facilitating consistent output. This record-keeping also supports ongoing process enhancements and troubleshooting efforts.
By carefully calibrating and documenting process parameters, manufacturers can secure a competitive advantage through reliable mold performance and exceptional product quality. This meticulous attention to detail underpins a robust validation system that consistently meets industry and customer expectations.
Step 5: Execute Process Validation
Implementing process validation confirms that all controlled parameters align to ensure the mold's consistent performance. This stage involves rigorous testing under simulated production scenarios to verify that the process can reliably produce parts within specified standards.
Conducting Validation Trials
Commence with comprehensive trials that mirror production settings to evaluate process capability. These trials should encompass various operating conditions, ensuring the process's adaptability and reliability.
- Holistic assessment: Evaluate the process across multiple dimensions, including temperature stability, material flow, and cycle consistency, to capture a complete picture of performance under typical production stresses.
- Data-driven insights: Document findings meticulously to enable a thorough analysis of process reliability. This information is crucial for identifying improvement opportunities and reinforcing process stability.
Real-Time Monitoring and Adjustments
Leverage sophisticated monitoring tools to facilitate continuous oversight and dynamic adjustments. These tools provide critical insights into process conditions, allowing for immediate intervention when deviations occur.
- Integrated analytics: Employ systems that seamlessly integrate with existing operations to provide real-time analytics and predictive insights. This integration enables proactive management of process variables.
- Responsive corrections: Utilize feedback loops to enact prompt corrections, ensuring the process remains within optimal ranges without delay. This approach minimizes downtime and enhances production efficiency.
Comprehensive Documentation
Develop extensive documentation that records every facet of the validation process. This documentation serves as a vital resource for demonstrating compliance and facilitating future process optimizations.
- Structured records: Create a clear, detailed account of each validation step, highlighting criteria, methodologies, and outcomes. This serves as a reference point for continuous improvement initiatives.
- Regulatory alignment: Ensure that documentation is aligned with industry regulations, establishing a foundation for compliance and audit preparedness. This alignment underscores the commitment to maintaining high standards in production practices.
Step 6: Address Common Validation Challenges
Navigating the complexities of mold validation requires proactive strategies to tackle potential hurdles. Unanticipated challenges, such as shifts in raw material properties and production deviations, can disrupt even meticulously planned processes. By anticipating these obstacles, manufacturers can implement robust contingency plans that ensure consistent outcomes.
Managing Raw Material Consistency
Variations in raw material properties can significantly affect mold validation. Differences in material characteristics, such as flow rate and chemical composition, can influence both mold performance and final product integrity. Addressing these issues involves a multi-faceted approach:
- Comprehensive Material Analysis: Conduct in-depth analysis of materials to ensure they meet specific mold requirements. This includes evaluating material behavior under projected production conditions to confirm compatibility and performance.
- Continuous Supplier Engagement: Establish and maintain ongoing communication with suppliers to ensure material consistency. Develop clear specifications and agreements to quickly address any fluctuations that arise, enabling timely adjustments to the validation process.
Ensuring Production Stability
Inconsistencies in production, such as variations in equipment performance or process parameters, can undermine validation efforts. Implementing robust quality assurance protocols is essential to maintaining process stability:
- Routine Equipment Verification: Implement a structured schedule for equipment verification to confirm all machinery operates within designated parameters. This practice prevents issues related to equipment inaccuracies or breakdowns.
- Advanced Process Monitoring: Deploy advanced monitoring technologies to track critical production metrics continuously. These systems offer predictive insights, allowing for proactive interventions before deviations impact the validation process.
Strengthening Team Coordination
Effective coordination among team members is crucial for swiftly addressing and resolving validation challenges. Establishing clear communication channels fosters collaboration and ensures that issues are addressed promptly:
- Integrated Team Workshops: Organize regular workshops bringing together diverse teams, including R&D, operations, and quality control, to foster problem-solving and innovation. This collaborative environment encourages sharing insights and developing holistic solutions.
- Feedback and Adjustment Cycles: Implement feedback loops that enable continuous refinement of validation processes. Encourage team input to adapt strategies dynamically, ensuring alignment with evolving production needs.
By proactively addressing these common validation challenges, manufacturers can enhance the reliability and efficiency of their mold validation systems. Implementing these strategies not only mitigates risks but also strengthens the overall production process, ensuring that high-quality products consistently meet industry standards.
Implementing a robust mold validation system is essential for ensuring consistent quality and efficiency in injection molding processes. By following these steps and proactively addressing common challenges, manufacturers can establish a solid foundation for producing high-quality parts that meet stringent industry standards. If you're looking to streamline your mold validation process and enhance your overall manufacturing operations, schedule a demo or try the platform to experience how we can help you achieve your goals.