The Future of Manufacturing: Multi-Process Software Insights
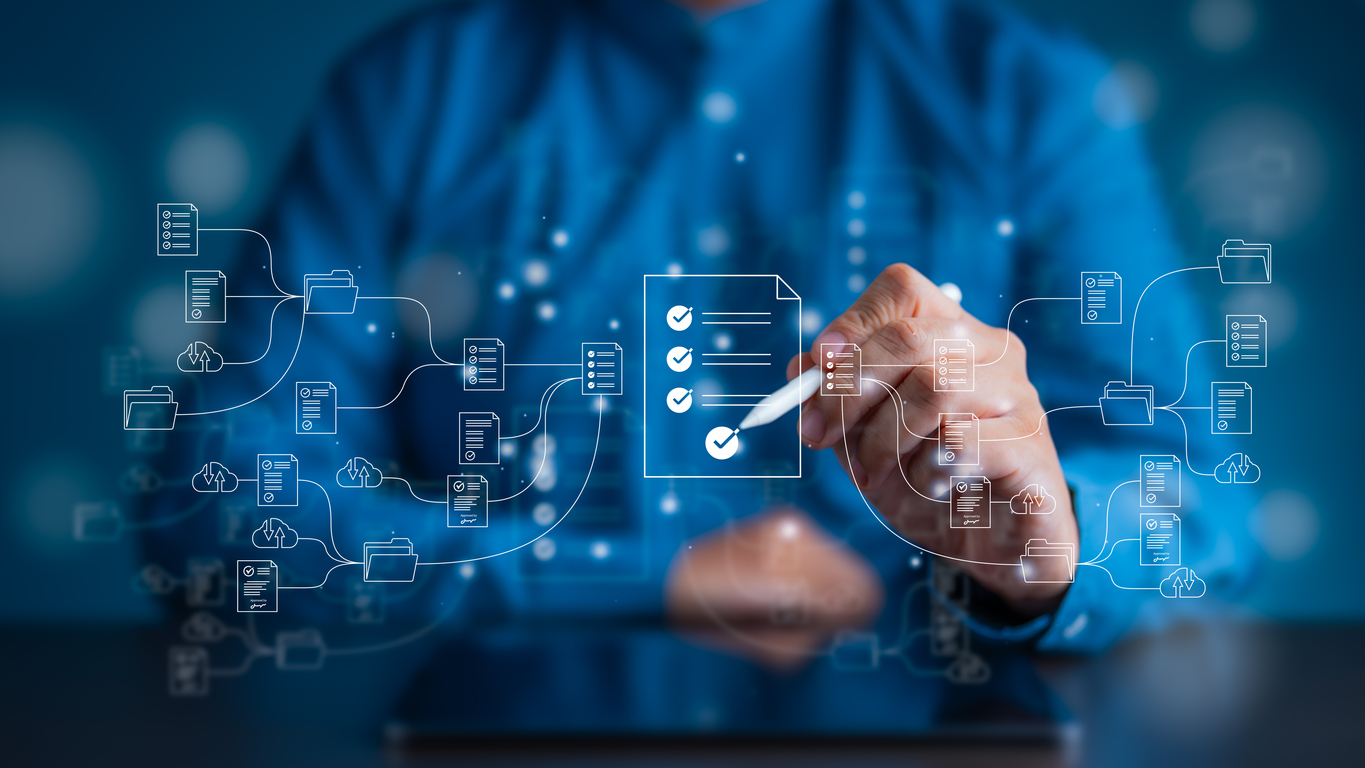
In today's fast-paced manufacturing landscape, companies face the challenge of managing multiple production processes while maintaining efficiency and quality. As manufacturing operations become increasingly complex, the need for a comprehensive solution that can streamline and optimize various processes has never been more critical. This is where multi-process manufacturing software comes into play.
Multi-process manufacturing software is designed to address the unique challenges faced by manufacturers who employ various production methods within a single facility. By integrating different manufacturing processes into a unified platform, this software enables companies to improve productivity, reduce costs, and enhance overall operational performance.
Whether you're a small-scale manufacturer looking to streamline your operations or a large enterprise seeking to optimize your production processes, understanding the capabilities and benefits of multi-process manufacturing software is crucial. In this article, we'll dive deep into the world of multi-process manufacturing software, exploring its key features, benefits, and considerations for implementation.
What is Multi-Process Manufacturing Software?
Multi-process manufacturing software is a comprehensive solution designed to manage and optimize various manufacturing processes within a single platform. This type of software is specifically tailored to handle multiple production methods, such as batch, continuous, discrete, and repetitive manufacturing, all within a unified system.
The primary goal of multi-process manufacturing software is to integrate different manufacturing operations, enabling seamless data flow and improved visibility across the entire production lifecycle. By consolidating disparate processes and data into a centralized platform, manufacturers can gain real-time insights into their operations, identify bottlenecks, and make informed decisions to optimize performance.
Key features of multi-process manufacturing software include:
- Recipe Management: Centralized management of recipes, formulas, and bill of materials, with version control and approval workflows for recipe changes. This feature allows manufacturers to maintain consistency and quality across multiple production runs.
- Production Planning: Advanced planning and scheduling tools for optimizing production, supporting both make-to-stock and make-to-order production models. Multi-process manufacturing software integrates with demand forecasting and inventory management systems to ensure optimal resource allocation and minimize waste.
- Quality Control: Integrated quality control processes and checkpoints, supporting in-process and finished product testing. The software enables statistical process control (SPC) and quality trending analysis, facilitating corrective and preventive actions (CAPA) management to maintain high product quality standards.
- Traceability: End-to-end traceability from raw materials to finished goods, ensuring compliance with industry regulations and quality standards. Multi-process manufacturing software maintains detailed audit trails and documentation, enabling rapid response to quality issues and product recalls.
By incorporating these key features, multi-process manufacturing software empowers manufacturers to streamline their operations, improve product quality, and enhance overall efficiency. Whether you're producing food and beverages, chemicals, pharmaceuticals, or other products that require multiple production methods, a robust multi-process manufacturing software solution can help you optimize your processes and stay competitive in today's dynamic manufacturing environment.
The Benefits of Multi-Process Manufacturing Software
Improved Efficiency and Productivity
With multi-process manufacturing software, efficiency and productivity receive a remarkable enhancement through the seamless integration of various production operations. This software serves as a cohesive platform that unites different manufacturing processes, leading to smoother workflows and faster production cycles. By unifying operations, manufacturers eliminate redundancies and ensure each process component aligns perfectly.
The capability to monitor and control production in real-time transforms how manufacturers manage their workflows. The software provides visibility that allows for immediate identification of inefficiencies, enabling swift adjustments that keep operations running optimally. This proactive approach ensures that resources are used effectively, minimizing material and time waste.
Additionally, the software empowers manufacturers with actionable insights and comprehensive analytics. By delivering clear production metrics and performance data, this technology supports strategic decision-making that drives continuous improvement. Such insights reveal opportunities for enhancement, allowing manufacturers to refine processes and boost productivity further.
Enhanced Traceability and Compliance
One of the standout features of multi-process manufacturing software is its capacity to enhance traceability and ensure compliance. The software meticulously tracks every aspect of the production journey, from raw materials to final products, offering a clear and complete picture of the entire process. This level of traceability is crucial for industries where adherence to regulations is critical.
The software facilitates compliance with industry standards through meticulous record-keeping and documentation. Manufacturers benefit from a robust framework that ensures regulatory requirements are met, reducing the risk of penalties and bolstering market credibility. This system not only supports current compliance needs but also adapts seamlessly to evolving regulations.
Furthermore, the software enhances responsiveness to quality issues and recall situations. By providing detailed traceability information, manufacturers can quickly identify and address potential concerns, safeguarding product integrity and brand reputation. This capability builds trust with customers and stakeholders, reinforcing a commitment to quality and reliability.
Key Features of Multi-Process Manufacturing Software
Recipe and Formula Management
Efficient control of complex recipes and formulas is a defining feature of multi-process manufacturing software. This software allows manufacturers to organize and oversee intricate formulations with precision, facilitating seamless updates and access. Such management ensures consistency across production batches, enabling manufacturers to adapt swiftly to evolving requirements while maintaining product integrity.
The implementation of structured workflows for changes introduces robust quality assurance. This ensures that any modifications to formulations undergo a thorough review process, maintaining compliance with industry standards. By managing revisions within a controlled environment, manufacturers can minimize errors and uphold the highest quality levels.
Additionally, the software's capacity to handle batch scaling and calculate yield enhances operational efficiency. It effectively manages co-products, by-products, and waste, optimizing resource utilization and minimizing environmental impact. This feature is essential for manufacturers aiming to achieve sustainable production practices.
Production Planning and Scheduling
Advanced production planning tools embedded within multi-process manufacturing software enable manufacturers to refine their operational efficiency. These tools provide a comprehensive view of production schedules, ensuring optimal resource allocation and streamlined workflows. By minimizing downtime and maximizing output, manufacturers can enhance their overall productivity.
The adaptability of the software supports diverse production models, allowing manufacturers to align operations with market demands. Integration with inventory and forecast systems ensures that production aligns with real-time demand, reducing surplus inventory and ensuring timely product delivery.
The ability to dynamically adjust production schedules in response to shifting conditions offers a competitive advantage. Manufacturers can swiftly adapt to changes in demand or operational constraints, maintaining efficiency and meeting customer expectations without compromising on quality or delivery timelines.
Quality Control and Assurance
Incorporating robust quality assurance protocols, multi-process manufacturing software ensures product excellence. By embedding quality control checkpoints throughout the production process, manufacturers can promptly detect and address potential issues. This proactive approach safeguards product integrity and minimizes the risk of defects.
Comprehensive testing capabilities for both in-process and finished products are integral to the software. These tools allow for thorough validation of product quality, ensuring that only the highest standards are met before products reach the market.
The software's support for corrective and preventive actions (CAPA) facilitates structured responses to quality challenges. By addressing root causes and implementing preventive measures, manufacturers can effectively maintain quality standards, fostering trust and reliability with their customers.
Choosing the Right Multi-Process Manufacturing Software
Selecting the optimal multi-process manufacturing software demands careful consideration, as it influences both present operations and future adaptability. Manufacturers should assess the software's ability to scale in tandem with their business, ensuring it remains effective as production requirements change. This involves not just accommodating increased output but also embracing process innovations. A flexible system capable of incorporating new technologies and expanding functionalities is vital for sustained growth.
When it comes to integration, the software must seamlessly connect with existing platforms, such as ERP systems, to ensure harmonious data flow across operations. This capability prevents data bottlenecks and promotes a unified approach to managing production activities. By facilitating seamless communication between various departments, integrated systems enhance overall operational coherence and enable informed decision-making.
The ease of use, reflected in intuitive interfaces and straightforward navigation, plays a significant role in the software's successful implementation. It is essential for users to access and utilize the software's features without extensive training. Vendors offering robust support services, including thorough training and smooth implementation assistance, can significantly ease the transition. This ensures that teams can quickly adapt to the new system, minimizing operational interruptions.
Industry-Specific Requirements
Catering to industry-specific needs is crucial in the selection process for multi-process manufacturing software. Each sector, such as aerospace or chemicals, has its own set of compliance requirements and operational nuances. For sectors governed by intricate regulations or quality standards, the software must support these mandates with precision. This includes features that facilitate compliance reporting and documentation, ensuring a seamless alignment with industry expectations.
The software should also be equipped to handle specialized industry processes and incorporate best practices, offering solutions that match distinct production methodologies. Ensuring compatibility with standard data formats and protocols enhances the ability to communicate effectively with outside partners, including suppliers and certification bodies. This compatibility fosters a collaborative manufacturing environment, streamlining interactions and boosting efficiency.
Pre-configured templates and workflows tailored to specific industries can expedite the deployment process. By minimizing the need for extensive customization, these pre-configured solutions allow manufacturers to implement the software swiftly and start leveraging its benefits. By aligning with industry-specific requirements, manufacturers can optimize operations while maintaining compliance and quality standards.
Implementing Multi-Process Manufacturing Software
Strategic planning is essential for a smooth implementation of multi-process manufacturing software. Initiating the process with precise definitions of project scope, objectives, and success criteria establishes a clear roadmap for the entire team. This clarity facilitates alignment among stakeholders, ensuring everyone understands the desired outcomes and the benchmarks for measuring success.
Incorporating insights from key stakeholders and end-users from the outset is crucial. Their early involvement ensures the software configuration meets actual operational needs, enhancing its relevance and usability. Engaging these groups through interactive sessions and discussions allows for valuable input, tailoring the solution to fit specific business requirements.
Conducting comprehensive data migration and integration testing is critical to a successful rollout. Ensuring the accuracy of migrated data involves meticulous mapping and validation to prevent discrepancies. Rigorous testing ensures that the software integrates seamlessly with existing systems, reducing the risk of disruptions. These proactive measures address potential issues, paving the way for a seamless transition.
Overcoming Common Challenges
Resistance to change often emerges as a significant hurdle during software implementation. Addressing this involves a robust change management strategy that includes comprehensive training programs. These programs should focus on demonstrating the software’s advantages and providing hands-on experience, boosting user confidence and adoption. Encouraging transparent communication and addressing concerns promptly fosters a supportive environment for change.
Maintaining data quality and consistency during migration requires careful attention. Implementing stringent data cleansing and validation protocols ensures data integrity. Establishing clear procedures for data verification helps prevent inaccuracies and inconsistencies. This focus on data quality mitigates potential complications that may arise from poor data management.
Integrating the software with legacy systems and equipment can present technical challenges. Evaluating the compatibility of existing infrastructure with the new software is essential. Developing custom interfaces or utilizing middleware solutions can facilitate seamless integration, ensuring effective communication across systems. By proactively addressing these integration challenges, organizations can maintain operational continuity and fully leverage the new software’s capabilities.
Minimizing disruptions to ongoing operations during implementation is vital for maintaining efficiency. Adopting a phased rollout strategy allows for testing the software’s functionality in smaller segments, mitigating the risk of operational setbacks. This approach ensures a gradual transition, enabling organizations to implement the software while maintaining productivity and setting the stage for future success.
The Future of Multi-Process Manufacturing Software
As the industry evolves, multi-process manufacturing software is increasingly moving toward cloud-based and software-as-a-service (SaaS) models. These solutions offer the advantage of scalability and adaptability, allowing manufacturers to dynamically adjust to changing production needs. By utilizing cloud technology, businesses achieve greater flexibility, enabling access to critical applications and data from any location, which fosters enhanced collaboration and operational agility. This shift reduces reliance on physical infrastructure, streamlining the process of updates and maintenance to ensure continuous innovation and efficiency.
The integration of cutting-edge technologies such as artificial intelligence, machine learning, and the Internet of Things (IoT) is redefining the capabilities of manufacturing software. AI and machine learning tools provide advanced analytics and predictive modeling, helping manufacturers anticipate operational challenges and optimize resource use. IoT connectivity enhances this by offering comprehensive, real-time data from interconnected devices, which supports proactive maintenance strategies and adaptive process management, ultimately driving improved performance across the board.
Focusing on user experience and mobile accessibility is becoming increasingly important in the development of future manufacturing software solutions. As the demand for real-time data access grows, designing intuitive interfaces that simplify interaction is crucial. Mobile-friendly solutions empower users to obtain essential information and make informed decisions swiftly, whether on the factory floor or remotely. This emphasis on design not only increases user engagement but also ensures that teams can fully leverage technological advancements to maintain their competitive edge.
Interoperability, guided by open standards, is key to seamless integration with existing systems and future technologies. Forward-looking software solutions prioritize ease of integration, allowing manufacturers to connect with a diverse array of digital tools without interruption. Such compatibility supports a unified data environment, enhancing visibility and control over all operations. By adhering to open standards, manufacturers can also foster stronger partnerships and collaborations, creating a more cohesive and efficient supply chain network.
As the manufacturing landscape continues to evolve, embracing multi-process manufacturing software becomes a strategic imperative for businesses seeking to thrive in an increasingly competitive environment. By leveraging the power of advanced technologies and intuitive design, these solutions empower manufacturers to optimize operations, enhance quality, and drive innovation. If you're ready to explore how multi-process manufacturing software can transform your business, schedule a demo or try the platform to experience its capabilities firsthand and let us help you unlock your manufacturing potential.