Next Generation Productivity: Transforming Additive Manufacturing
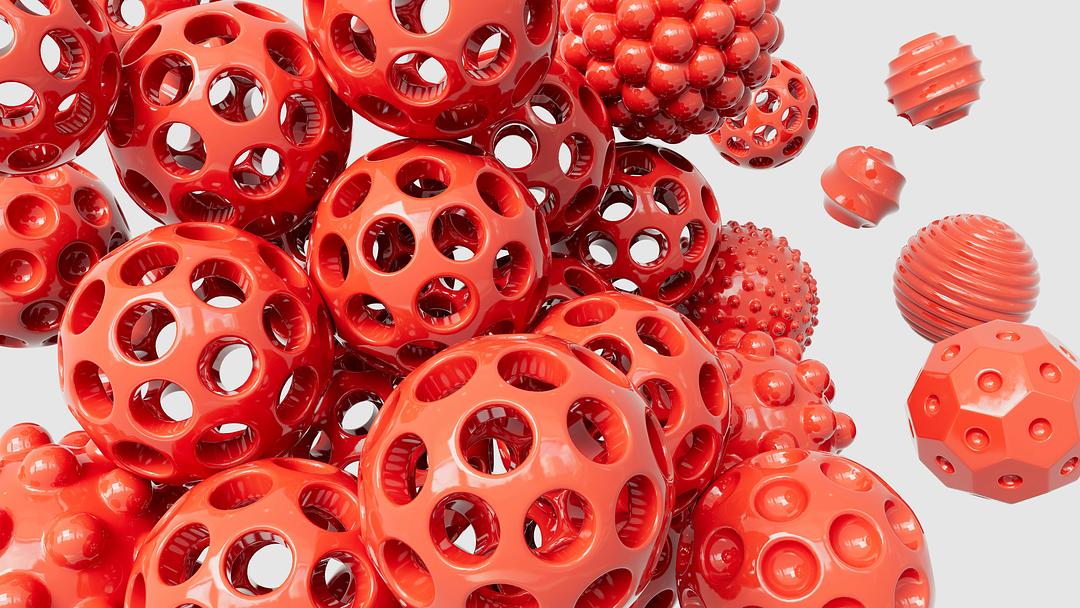
Next Generation Productivity: Transforming Additive Manufacturing
Additive manufacturing, also known as 3D printing, has revolutionized the way products are designed and manufactured. As the technology continues to evolve, the focus has shifted towards enhancing productivity and efficiency to drive wider adoption across industries.
Next-generation additive manufacturing technologies are pushing the boundaries of what is possible, enabling faster production times, improved part quality, and reduced costs. These advancements are transforming the manufacturing landscape, making additive manufacturing a viable option for an increasing range of applications.
In this article, we will explore the concept of next-generation productivity in additive manufacturing and delve into the innovations and strategies that are driving this transformation. From intelligent software platforms to material innovations and automation, we will examine the key factors contributing to enhanced productivity in the world of additive manufacturing.
What is Next Generation Productivity in Additive Manufacturing?
Next-generation productivity in additive manufacturing refers to the advancements and innovations that are driving significant improvements in efficiency, speed, and cost-effectiveness. These developments focus on streamlining the entire additive manufacturing workflow, from design to post-processing, to achieve higher throughput and better part quality.
One of the key aspects of next-generation productivity is the integration of intelligent software solutions. Platforms like Phasio simplify workflows by automating repetitive tasks, optimizing process parameters, and enabling seamless collaboration among stakeholders. These software tools leverage machine learning algorithms and cloud-based technologies to enhance efficiency and reduce manual intervention.
Material innovations also play a crucial role in driving productivity gains. The development of high-performance, production-grade materials specifically designed for additive manufacturing is expanding the range of applications and improving part performance. These materials offer enhanced mechanical properties, better surface finish, and increased durability, enabling the production of end-use parts with superior quality.
Advancements in Additive Manufacturing Technologies
- Faster print speeds: Next-generation additive manufacturing systems boast significantly faster print speeds compared to traditional 3D printers. This is achieved through advanced hardware designs, optimized motion control, and improved material deposition techniques.
- Larger build volumes: Newer additive manufacturing machines offer increased build volumes, allowing for the production of larger parts or the simultaneous printing of multiple smaller components. This capability enhances productivity by reducing the need for multiple print runs.
- Multi-material printing: Some advanced additive manufacturing systems support the simultaneous printing of multiple materials within a single build. This enables the creation of complex, multi-functional parts with varying material properties, eliminating the need for assembly and reducing lead times.
Innovations in Production Processes
- Hybrid manufacturing: The integration of additive manufacturing with traditional subtractive technologies, such as CNC machining, is gaining traction. Hybrid manufacturing combines the benefits of both processes, allowing for the production of parts with complex geometries and high precision.
- Automated post-processing: Post-processing steps, such as support removal and surface finishing, have traditionally been time-consuming and labor-intensive. Next-generation additive manufacturing systems incorporate automated post-processing solutions, such as robotic support removal and automated polishing, to streamline these processes and improve efficiency.
- In-process monitoring and quality control: Advanced sensor technologies and machine learning algorithms are being integrated into additive manufacturing systems to enable real-time monitoring and quality control. These systems can detect and correct defects during the printing process, ensuring consistent part quality and reducing waste.
By leveraging these advancements and innovations, manufacturers can achieve significant productivity gains in additive manufacturing. Faster print speeds, larger build volumes, and automated processes enable higher throughput and reduced lead times. Material innovations and hybrid manufacturing approaches expand the range of applications and improve part performance. Intelligent software solutions streamline workflows, optimize process parameters, and facilitate collaboration.
As the additive manufacturing industry continues to evolve, next-generation productivity will play a pivotal role in driving adoption and unlocking new opportunities. By embracing these advancements and implementing best practices, manufacturers can harness the full potential of additive manufacturing, improving efficiency, reducing costs, and delivering high-quality parts faster than ever before.
The Role of Software in Driving Productivity
Advanced software solutions form the backbone of productivity improvements in additive manufacturing. These solutions streamline the manufacturing process by orchestrating complex operations and minimizing manual oversight. By incorporating sophisticated algorithms, software tools refine production settings, ensuring high quality and efficiency throughout the manufacturing cycle.
Intelligent Software Platforms
Central to productivity enhancements are software platforms that revolutionize operational efficiency. These platforms integrate seamlessly with existing systems, providing automation that reduces operational complexity. By delivering real-time insights and analytics, they empower manufacturers to respond swiftly to production changes, enhancing both speed and adaptability in the manufacturing process.
Cloud-Based Solutions
Cloud technologies facilitate unparalleled collaboration and data handling, critical for modern manufacturing environments. These solutions enable synchronized data access and collaboration across global teams, ensuring all participants work with the most current information. The adaptability of cloud infrastructures allows for dynamic resource allocation, supporting fluctuating production needs with precision.
Generative Design and Quoting Software
Generative design tools are redefining the design and production landscape in additive manufacturing. Utilizing advanced computational techniques, these tools create optimized designs that enhance performance while minimizing material use. This leads to cost-effective production without compromising quality.
Simultaneously, quoting software revolutionizes customer interactions by delivering precise and swift estimates. This capability enhances client communication, fostering better relationships and aligning production with market demands. By integrating quoting capabilities into manufacturing workflows, businesses can ensure competitive pricing and improved customer satisfaction.
Software solutions are thus critical to unlocking productivity in additive manufacturing. They provide essential tools for optimizing operations, managing data efficiently, and enhancing customer interactions, all while maintaining superior production quality. Through these technological advancements, manufacturers can achieve significant gains, setting the stage for innovative applications and business models in the evolving field of additive manufacturing.
Material Innovations Fueling Productivity Gains
The forefront of productivity advancements in additive manufacturing lies in the continuous evolution of materials. As the industry progresses, the focus remains on crafting materials that align with production demands, enhancing both efficiency and application possibilities. These novel materials are integral in achieving superior performance characteristics, suitable for a broad array of industrial applications.
Cutting-Edge Materials Development
In the quest for next-generation productivity, the creation of materials with refined attributes is essential. These materials are designed to meet stringent specifications for various applications, offering benefits like enhanced resilience and thermal endurance. For instance, breakthroughs in ceramic composites provide remarkable heat resistance and structural integrity, expanding their utility in high-temperature environments.
- Metallurgical Advances: Innovations in alloys, such as those incorporating rare earth elements, are pivotal for sectors that necessitate lightweight yet robust components. These materials are transforming industries by providing unprecedented strength-to-weight ratios.
- Polymeric Innovations: Advanced polymers with self-healing properties and enhanced electrical conductivity are leading the charge in sectors like consumer electronics and healthcare, where adaptability and performance are crucial.
Enhanced Material Attributes
Modern materials are engineered to deliver specific functions that expand the possibilities of additive manufacturing. These properties enable the production of intricate components that serve specialized roles in diverse applications.
- Thermally Conductive Materials: The rise of materials with superior thermal conductivity is vital for applications requiring efficient heat dissipation, such as in electronics where maintaining operational temperatures is critical.
- Adaptable Composites: Materials that exhibit adaptive responses to environmental conditions, such as shape memory alloys, are facilitating innovation in fields like aerospace, where performance under varying conditions is essential.
Broader Accessibility and Economic Viability
The expansion of the materials market, coupled with cost reductions, is instrumental in making additive manufacturing technologies more accessible. As material options broaden, industries are finding it increasingly feasible to adopt these technologies for mainstream production.
- Supplier Diversification: An increase in material suppliers fosters competition, driving innovation and reducing costs. This diversification allows manufacturers to tailor material selections to specific industry requirements, from medical to automotive.
- Eco-Friendly Options: The development of sustainable materials, such as those derived from bio-based sources, supports environmentally conscious manufacturing practices. These materials not only meet ecological standards but also appeal to the growing demand for green production solutions.
By integrating these material innovations, manufacturers can enhance their productivity, crafting parts that are both functionally superior and economically viable. As the material landscape continues to evolve, the opportunities for innovation in additive manufacturing only expand.
Automation and Intelligent Systems
The advent of intelligent systems in additive manufacturing marks a significant shift toward more streamlined production processes. With cutting-edge technologies, manufacturers can achieve higher throughput and maintain precision across operations. Innovations in automated systems have reduced the need for human intervention, fostering operational efficiency and consistency.
Robotics and Automation
Robotics are revolutionizing the landscape of additive manufacturing by automating intricate tasks traditionally done manually. These advanced systems enhance productivity by efficiently managing complex operations, such as component assembly and precision finishing. By utilizing robotics, manufacturers can ensure each part meets stringent quality standards with minimal manual input.
- Precision Robotics: These systems are designed to handle delicate tasks with unmatched accuracy, ensuring consistent quality across all manufactured parts. By automating repetitive processes, precision robotics allow human resources to focus on more strategic aspects of manufacturing.
- Smart Conveyance Systems: Innovations in conveyance technology facilitate the seamless transition of components through various production stages, optimizing workflow and reducing bottlenecks. These systems work to ensure timely processing, supporting increased production capabilities.
Machine Learning and Process Optimization
Machine learning technologies play a pivotal role in optimizing manufacturing processes by analyzing vast sets of data to refine operational parameters. These intelligent systems adapt to real-time changes, ensuring that production runs are optimized for quality and efficiency without manual oversight.
- Data-Driven Maintenance: Machine learning enables predictive insights into equipment health, allowing for timely maintenance actions that minimize downtime. This forward-thinking approach ensures machinery operates at peak efficiency, extending operational longevity.
- Dynamic Process Adjustments: Algorithms continuously refine process parameters based on real-time data, maintaining optimal conditions throughout production. This adaptability enhances yield and reduces waste, with process settings tailored to current manufacturing needs.
In-Process Monitoring and Quality Control
Implementing state-of-the-art monitoring systems elevates the standard of quality control within additive manufacturing. Utilizing advanced sensors and data analytics, these systems provide comprehensive oversight of the production process, identifying discrepancies before they impact final output.
- Continuous Feedback Mechanisms: Real-time data collection allows systems to make immediate adjustments, ensuring adherence to quality standards. This capability ensures only parts that meet precise specifications continue through the production line.
- Advanced Anomaly Detection: Utilizing sophisticated sensors and analytics, these systems detect and address defects at an early stage, safeguarding against production errors. This proactive approach enhances product reliability and minimizes the need for extensive post-production inspections.
Through the integration of automation and intelligent systems, manufacturers are redefining the potential of additive manufacturing. By harnessing the capabilities of robotics, machine learning, and advanced monitoring, production processes achieve unprecedented levels of efficiency and quality.
Scalable and Flexible Production Strategies
Adopting scalable and flexible production strategies is essential in maximizing the potential of additive manufacturing. These strategies enable manufacturers to respond swiftly to market demands, ensuring that production processes remain agile and efficient. By incorporating innovative production frameworks and adaptive methodologies, manufacturers can tailor their operations to meet specific production requirements without compromising on quality or efficiency.
Modular and Scalable Systems
Dynamic systems form the backbone of adaptable manufacturing environments. These systems allow for the seamless integration of new technologies and workflows, providing the flexibility needed to scale operations up or down based on demand.
- Versatile Configurations: Dynamic systems offer unparalleled versatility, enabling manufacturers to reconfigure production lines to accommodate evolving product specifications or volumes. This flexibility ensures that production remains efficient, regardless of market fluctuations.
- Resource Optimization: By allowing for strategic resource allocation, dynamic systems minimize unnecessary expenditure. Manufacturers can optimize production capabilities as needed, aligning with market trends and reducing financial risk.
Advanced Manufacturing Techniques
Advanced manufacturing techniques offer a versatile solution for producing complex parts with high precision. This approach leverages cutting-edge technologies, resulting in components that meet stringent quality standards while minimizing production time.
- Innovative Fabrication Methods: Advanced techniques enable the creation of intricate structures with fine detail, utilizing revolutionary methods for complex designs. This integration enhances both precision and efficiency, ensuring superior product quality.
- Broad Application Spectrum: By employing advanced methods, manufacturers cater to a wide range of applications, from aerospace to electronics, where innovation and reliability are paramount. This approach expands the possibilities of additive manufacturing, unlocking new potential across various sectors.
Distributed Manufacturing Networks
Distributed manufacturing networks facilitate decentralized production, reducing lead times and transportation costs while enhancing responsiveness to market needs. These networks consist of interconnected production facilities that operate in harmony, providing a scalable and flexible manufacturing solution.
- Decentralized Production: By situating production capabilities closer to end-users, distributed networks reduce the need for extensive logistics and expedite delivery times. This decentralization enhances customer satisfaction and strengthens market presence.
- Collaborative Ecosystems: Distributed networks foster collaboration between facilities, enabling the sharing of resources, expertise, and best practices. This interconnectedness drives innovation and continuous improvement, ensuring that production processes remain at the forefront of efficiency and quality.
Through these scalable and flexible production strategies, manufacturers can harness the full potential of additive manufacturing. Dynamic systems, advanced techniques, and distributed networks work in harmony to create a responsive manufacturing environment capable of meeting ever-changing market demands.
Design Optimization for Additive Manufacturing
Design optimization in additive manufacturing capitalizes on the technology’s unique capabilities to enhance both functionality and efficiency. The ability to create complex geometries and innovative structures allows designers to rethink traditional manufacturing constraints, opening new avenues for part integration and performance enhancement.
Part Consolidation and Assembly Reduction
Additive manufacturing enables the seamless integration of components, reducing the need for conventional assembly processes. This innovation allows for the production of unified structures that offer improved performance and reliability while streamlining workflows.
- Integrated Functionality: By merging multiple components into a single unit, manufacturers can eliminate additional assembly steps, enhancing product reliability by reducing potential points of failure.
- Workflow Efficiency: Reduced assembly requirements translate into faster production cycles and lower manufacturing costs, optimizing resource allocation across the production line.
Topology Optimization
Utilizing advanced computational tools, topology optimization refines part designs to ensure optimal material distribution. This approach not only minimizes waste but also enhances the structural integrity and performance of manufactured parts.
- Optimized Designs: Algorithms identify and remove excess material, resulting in lighter, more efficient structures without compromising strength or functionality.
- Performance Enhancement: By focusing on critical load paths, optimized designs deliver superior mechanical performance, crucial for industries that demand high strength-to-weight ratios.
Lattice Structures and Nesting Strategies
Incorporating lattice structures within designs provides an innovative means of achieving high strength with minimal material use. These complex patterns are instrumental in applications where weight reduction is paramount without sacrificing structural integrity.
- Strength and Lightness: Lattice structures distribute loads efficiently, maintaining robustness while significantly lowering weight, essential for aerospace and automotive applications.
- Space Utilization: Effective nesting strategies maximize build chamber usage, enabling the production of more parts in a single run, thereby increasing throughput and reducing costs.
These design optimization strategies elevate the potential of additive manufacturing, enabling the production of superior components that meet the evolving needs of various industries. By leveraging advanced design techniques, manufacturers can achieve unprecedented levels of innovation and efficiency.
Unlocking New Applications and Business Models
Additive manufacturing is at the forefront of enabling unprecedented levels of product customization and personalization. By leveraging the adaptability of 3D printing, manufacturers can design products that precisely match individual customer requirements, resulting in tailored solutions that enhance user experience. This capability is revolutionizing sectors such as healthcare, where custom-fitted medical devices improve patient outcomes, and consumer products, where personalized designs add unique value.
- Bespoke Fabrication: Crafting items to exact customer specifications, providing a competitive edge through truly individualized offerings.
- Customer-Centric Solutions: Developing products that reflect consumer preferences, enhancing market differentiation and customer loyalty.
In the realm of product development, additive manufacturing significantly accelerates the cycle from conception to market introduction. By utilizing agile prototyping capabilities, companies can swiftly iterate designs, ensuring that final products meet rigorous standards for performance and quality. This agility allows businesses to stay ahead of market trends, quickly adapting to changing consumer demands and maintaining a competitive advantage.
- Rapid Iteration: Employing 3D printing for quick design changes, allowing for immediate testing and refinement, which speeds up the overall development timeline.
- Agile Market Response: Streamlining processes to quickly adapt products to new trends, ensuring timely market entry and relevance.
The emergence of on-demand manufacturing is reshaping traditional supply chain models, offering new efficiencies and responsiveness. This approach focuses on producing items precisely when needed, thereby reducing excess inventory and associated costs. Particularly advantageous for industries with complex or specialized components, such as aerospace and automotive, on-demand production minimizes both storage requirements and environmental impact.
- Just-In-Time Manufacturing: Producing components only as required, optimizing inventory levels and reducing lead times, which enhances operational efficiency.
- Localized Production Hubs: Establishing regional manufacturing sites to decrease logistics costs and improve delivery speed, meeting local market needs more effectively.
Exceptional communication and collaboration are key drivers in maximizing the benefits of additive manufacturing. By utilizing advanced digital tools, design, engineering, and production teams can seamlessly share information, ensuring all stakeholders are aligned. This connectivity fosters innovation, enabling rapid development of creative solutions and new business models that fully exploit the capabilities of additive manufacturing.
- Integrated Collaboration Tools: Leveraging digital platforms for seamless interaction among diverse teams, promoting cohesive development efforts and accelerating innovation.
- Stakeholder Synergy: Actively engaging all involved parties, including suppliers and customers, to drive continuous improvement and ensure products meet market expectations.
These developments in additive manufacturing allow for a transformation of business models, opening doors to innovative approaches and expanding market opportunities. As industries embrace these capabilities, the potential for growth and evolution remains vast, driven by a commitment to efficiency, customization, and collaboration.
Overcoming Challenges and Driving Adoption
Navigating the path to widespread adoption of additive manufacturing presents several challenges that require strategic solutions and forward-thinking initiatives. Addressing the skills gap is paramount as the industry advances, necessitating robust training programs to empower the workforce with critical expertise. Cultivating a learning-centric culture will ensure teams are well-equipped to harness the potential of advanced manufacturing technologies.
Bridging the Skills Gap
Successfully integrating additive manufacturing into workflows demands a workforce skilled in both technical and practical domains. Tailored educational resources serve as a cornerstone in this mission, offering practical experience coupled with theoretical insights essential for mastering complex systems.
- Targeted Training Initiatives: Creating comprehensive training frameworks that include both foundational and advanced modules ensures a well-rounded understanding of the technology among team members, from novices to experts.
- Accredited Certification Programs: Developing industry-recognized certifications affirms skill proficiency and builds confidence among clients, highlighting the competence and reliability of manufacturing partners.
Establishing Industry Standards
Creating universally accepted industry standards is crucial for ensuring consistency and reliability throughout the additive manufacturing sector. By collaborating with regulatory bodies and industry leaders, manufacturers can establish best practices that elevate product quality and manufacturing efficiency.
- Unified Quality Assurance Systems: Implementing standardized quality control measures across the industry reduces variability and enhances the dependability of manufactured components, fostering trust among end-users.
- Performance Benchmarks and Compliance: Setting clear performance benchmarks and compliance requirements encourages continuous improvement and innovation, propelling the industry toward higher standards.
Collaborative Innovation
Collaboration with technology providers and industry partners is vital for accelerating innovation and broadening the scope of additive manufacturing. By pooling resources and expertise, stakeholders can tackle technical and logistical hurdles, facilitating groundbreaking advancements.
- Collaborative Research Ventures: Partnering in research projects with academic institutions and technology developers promotes the exploration of new materials and techniques, expanding the possibilities of additive manufacturing.
- Strategic Industry Alliances: Forming strategic alliances with key industry players enables the exchange of insights and resources, fostering the development of innovative solutions to complex manufacturing challenges.
Showcasing Value and ROI
Demonstrating the tangible benefits and return on investment of additive manufacturing is essential for convincing stakeholders to embrace the technology. Highlighting successful case studies can illustrate the transformative impact of additive manufacturing on efficiency, cost savings, and product innovation.
- In-Depth Case Studies: Providing comprehensive accounts of successful implementations offers concrete proof of the benefits of additive manufacturing, showing how it can enhance operational capabilities and stimulate business growth.
- Measurable Advantages: Presenting data on improvements in productivity, cost reductions, and time savings underscores the economic feasibility of adopting additive manufacturing, encouraging wider acceptance and integration across various industries.
As the additive manufacturing landscape continues to evolve, embracing next-generation productivity is crucial for staying competitive and unlocking new opportunities. By leveraging advanced technologies, optimizing processes, and fostering collaboration, manufacturers can harness the full potential of additive manufacturing and drive innovation across industries. If you're ready to transform your additive manufacturing operations and achieve next-level productivity, schedule a demo or try the platform to experience how we can help you streamline your workflows and boost efficiency.