Estimating Costs for Plastic Molding: Key Factors to Consider
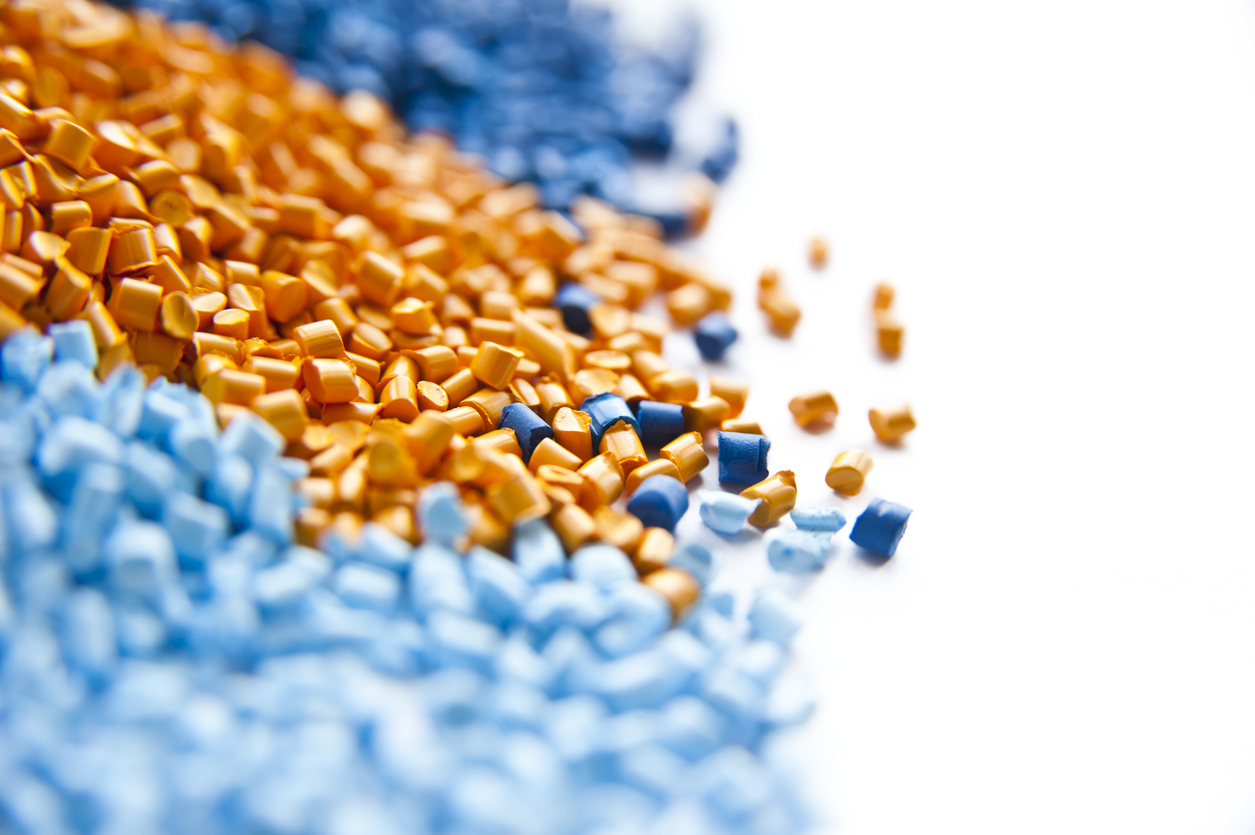
Plastic molding is a manufacturing process that enables the mass production of identical parts with tight tolerances. It's a cost-effective and highly repeatable technology that yields high-quality parts for large series production.
The cost of plastic molding can vary significantly depending on several factors, such as the complexity of the part design, the materials used, and the required production volume. Estimating these costs accurately is crucial for manufacturers to plan their budgets and optimize their operations.
In this article, we'll dive into the world of plastic molding cost estimation, exploring the key factors that influence the overall expenses and providing practical insights to help you navigate the process more effectively.
What is Plastic Molding Cost Estimation?
Plastic molding cost estimation is the process of predicting the expenses associated with manufacturing plastic parts through various molding techniques. It involves analyzing multiple variables that contribute to the overall cost, such as material selection, mold complexity, production volume, and labor requirements.
Accurate cost estimation is essential for several reasons:
- Budgeting: It helps manufacturers allocate financial resources effectively and make informed decisions about their projects.
- Pricing: By understanding the costs involved, businesses can determine competitive pricing strategies for their products.
- Optimization: Identifying cost drivers enables manufacturers to explore ways to optimize their processes and reduce expenses without compromising quality.
Cost estimation tools, such as plastic molding price estimators offered by Phasio, streamline this process by considering various inputs and providing quick, reliable estimates. These tools empower manufacturers to make data-driven decisions and adapt their strategies accordingly.
How to Estimate Costs for Plastic Molding
Estimating costs for plastic molding involves understanding the key components that contribute to the overall expenses. Let's break down these components and explore how they impact the total cost:
Material Costs
The type and quantity of material used in plastic molding significantly influence the cost. Different materials have varying properties and price points, so it's essential to consider the specific requirements of your project.
- Thermoplastics: These materials, such as ABS, polypropylene, and nylon, are commonly used in injection molding. Their cost varies based on factors like grade, additives, and market conditions.
- Resins: Specialty resins, such as engineering plastics or high-performance polymers, often come with a higher price tag due to their enhanced properties and more complex manufacturing processes.
Mold Complexity
The complexity of the mold is another critical factor in determining the cost of plastic molding. More intricate designs require greater precision and expertise in mold fabrication, leading to higher expenses.
- Geometry: Parts with complex geometries, such as undercuts, thin walls, or intricate surface details, demand more sophisticated molds and may increase costs.
- Precision: Tight tolerances and high-precision requirements necessitate advanced machining techniques and quality control measures, which can drive up mold costs.
Production Volume
The number of parts you plan to manufacture plays a significant role in the cost per unit. Higher production volumes generally lead to lower costs due to economies of scale.
- Tooling Costs: The initial investment in mold tooling is spread across the total number of parts produced, so larger quantities can help amortize these costs more effectively.
- Efficiency: Increased production volumes allow for optimized machine utilization and reduced setup times, resulting in cost savings.
By assessing these key components and leveraging tools like plastic molding price estimators, manufacturers can gain a comprehensive understanding of the costs involved in their projects. This knowledge empowers them to make informed decisions, optimize their processes, and achieve cost-effective results.
Estimating costs for plastic molding requires a comprehensive approach that addresses the multifaceted nature of manufacturing expenses. By dissecting and understanding the diverse components that contribute to these costs, businesses can align their financial strategies with production goals. Utilizing a plastic molding price estimator enhances this process, offering clarity and precision in cost projections.
Material, Labor, and Overhead Costs
In manufacturing, three central cost categories—raw materials, workforce, and fixed operational expenses—are crucial in shaping the overall financial outlay of plastic molding.
- Raw Material Expenses: The selection of plastic plays a significant role in cost determination. Materials vary widely in terms of mechanical properties such as impact resistance, flexibility, and thermal endurance, which directly influence their pricing. Balancing these factors ensures optimal performance without unnecessary expenditure.
- Workforce Expenses: The skills and time required for machinery setup and operation factor heavily into labor costs. This includes machine calibration, ongoing production oversight, and any necessary adjustments. Streamlining workflows to reduce idle times can significantly cut labor expenses.
- Fixed Operational Expenses: Overhead encompasses indirect costs like energy consumption, equipment maintenance, and facility operations. Additionally, it covers equipment depreciation and administrative support. Implementing preventive maintenance and energy-efficient practices helps to lower these expenses.
Harnessing Technology for Cost Assessment
Advanced technologies, such as plastic molding cost estimators, provide substantial benefits in accurately assessing expenses. These tools evaluate numerous production parameters, delivering a detailed cost breakdown.
- CAD Model Integration: Many estimators feature direct CAD model integration to precisely calculate material requirements and identify cost-saving opportunities. This ensures all design elements are factored into the cost assessment.
- Scenario Evaluation: These tools often enable the analysis of different production scenarios, allowing manufacturers to see how changes in materials, batch sizes, or design intricacies affect total costs. This supports strategic decision-making and cost efficiency.
- Dynamic Updates: Fluctuations in market conditions can impact material costs and availability. Effective estimators provide dynamic updates and adjustments based on current data, maintaining the relevance and accuracy of estimates.
By focusing on these crucial aspects and effectively leveraging technological tools, manufacturers can gain a deeper insight into their plastic molding costs. This strategic approach facilitates better financial planning and enhances adaptability to changing production needs and market trends.
Step 1: Assess Material Costs
Assessing material costs is a foundational step in estimating plastic molding expenses. The choice of material impacts not only the cost but also the performance and durability of the final product. Manufacturers must identify the type and quantity of material required to meet the specifications of their parts. This step involves evaluating various material options to ensure they align with both budgetary constraints and functional requirements.
Identifying Material Types and Quantities
The first task in material cost assessment involves selecting the appropriate material type. Polyethylene and polycarbonate are popular choices for their strength and versatility. Additionally, materials like thermosetting plastics may be chosen for their heat resistance and durability. Determining the precise quantity needed for production is equally important. Accurate volume estimation prevents material shortages and excess, both of which can lead to increased costs.
Cost Implications of Material Choices
Different materials carry different cost implications due to their inherent properties and market dynamics. Understanding these factors can help in making cost-effective decisions:
- Polyethylene and Polycarbonate: These materials offer a balance between affordability and performance, making them ideal for applications requiring moderate strength and flexibility.
- Thermosetting Plastics: Although often more expensive, thermosetting plastics provide superior heat resistance and structural integrity, suitable for specialized applications where durability is paramount.
- Supply Chain Variability: Material costs can fluctuate based on global supply chain conditions and raw material availability. Staying informed about these factors is crucial for adjusting cost estimates accurately.
To effectively manage material costs, manufacturers may also consider working closely with suppliers to negotiate favorable pricing and secure stable supply agreements. By thoroughly assessing these factors, businesses can make informed decisions that balance cost and performance, ensuring efficient use of resources in their plastic molding operations.
Step 2: Evaluate Mold Complexity
Evaluating mold complexity plays a crucial role in estimating costs for plastic molding. Mold design impacts not only the feasibility of part production but also the precision and quality of the final product. Delving into the intricacies of mold design involves understanding how specific features and tolerances affect both the manufacturing process and its associated costs.
Analyzing Design Complexity
The design intricacy of a mold is a major determinant of its cost. By examining the design's core elements, manufacturers can identify areas that may require specialized attention or advanced technology. This analysis aids in recognizing cost drivers and potential optimization areas.
- Complex Features: Detailed features such as grooves, cavities, and intricate patterns demand sophisticated engineering solutions. These features might necessitate additional tooling or custom solutions, impacting the overall mold cost.
- Dimensional Accuracy: Achieving dimensional accuracy involves adhering to specific measurements and tolerances, which require precise machining and thorough quality assurance. This need can increase costs, often requiring cutting-edge equipment and skilled craftsmanship.
Impact of Mold Features on Costs
Particular mold features can significantly influence the overall cost, affecting decisions on design and production methods. Understanding these impacts allows for more strategic planning and effective resource management.
- Multi-Part Molds: Complex parts may require multi-part mold assemblies to achieve the desired shape and function. These assemblies add to the initial tooling costs due to the additional components needed.
- Texturing and Engraving: Applying textures or engravings to molds requires specialized processes that can increase manufacturing expenses. These aesthetic elements should be considered carefully in relation to their added cost.
- Cooling and Venting Systems: Efficient cooling and venting systems in molds are essential for maintaining part integrity and reducing cycle times. Designing these systems within intricate molds can elevate the initial investment.
Manufacturers should balance the advantages of complex design features against their cost implications, taking into account the project's scope and budget. By thoroughly evaluating mold complexity, businesses can make informed decisions that align with both production objectives and financial considerations.
Step 3: Determine Production Volume
Determining production volume is a crucial step in assessing costs for plastic molding, as it influences not only efficiency but also the strategic planning of manufacturing operations. Calculating the number of units you plan to manufacture involves aligning production goals with market demand, available resources, and budgetary constraints, ensuring that output meets business objectives effectively.
Calculating Units for Production
Establishing the production volume requires a thorough evaluation of various elements that impact both manufacturing and financial planning. This evaluation supports a balanced approach to production that meets demand while optimizing resources.
- Demand Forecasting: Accurately predicting market demand helps prevent excess inventory or stockouts. Utilizing sales data analytics, market research, and historical trends supports precise production planning.
- Resource Assessment: The capacity of manufacturing facilities, including equipment and labor, should match the intended production output. Assessing these capabilities helps in scheduling production runs to maximize efficiency without overextending resources.
- Cost-Benefit Analysis: Analyzing the financial implications of different production volumes aids in determining the most cost-effective approach. Comparing potential revenue with associated costs helps find a volume that supports profitability and aligns with financial goals.
Production Volume and Operational Efficiency
Understanding the link between production volume and operational efficiency is essential for minimizing costs and maximizing throughput. Larger production volumes can unlock various efficiencies that contribute to overall cost reduction.
- Operational Streamlining: High production volumes facilitate the use of more automated processes and workflow improvements, reducing manual intervention and cycle times. Investing in automation and process optimization enhances these efficiencies.
- Supplier Negotiations: Engaging in negotiations with suppliers for bulk material orders can result in cost advantages, such as reduced unit prices and favorable terms. Strengthening supplier relationships is critical for leveraging these benefits.
- Dynamic Resource Allocation: Adjusting resource allocation based on production needs ensures optimal use of machinery and labor. Implementing flexible scheduling and resource management practices supports cost-effective operations.
By carefully determining production volume and incorporating these strategies into manufacturing plans, businesses can achieve a balance between responsiveness to market conditions and cost efficiency, fostering growth and competitive advantage.
Step 4: Consider Production Methods
Selecting the appropriate production method is a critical decision that influences both the operational efficiency and economic feasibility of plastic molding. Different techniques offer unique benefits and limitations, affecting the complexity and cost of manufacturing. By understanding these methods, manufacturers can tailor their production processes to meet specific project demands and strategic objectives.
Evaluating Molding Techniques
A variety of molding techniques exist, each catering to specific part designs and production requirements. Assessing these options helps identify the best fit for your manufacturing goals.
- Thermoforming: This process involves heating a plastic sheet until pliable and then forming it over a mold. It's particularly effective for large, simple parts with shallow details, offering cost savings in tooling and quick turnaround times.
- Compression Molding: Ideal for durable, heat-resistant products, compression molding uses heat and pressure to shape materials within a mold cavity. It suits medium to high-volume production and complex designs, although it requires precise control and setup.
- Extrusion Blow Molding: This method combines extrusion and blowing to produce hollow parts, like containers and bottles. It is efficient for high-speed production of lightweight items, offering economical material use and consistent quality.
Economic Considerations of Molding Choices
The choice of production method directly impacts costs, influencing material efficiency, production speed, and equipment needs. Evaluating these economic factors ensures optimal resource utilization.
- Initial Tooling Investment: While thermoforming involves lower tooling costs due to simpler mold designs, compression molding requires more substantial initial investments for detailed molds and precise equipment.
- Material Utilization: Extrusion blow molding offers material efficiency by reducing waste, but energy consumption and cycle times must be optimized to maintain cost-effectiveness.
- Labor and Process Management: Each technique imposes different demands on labor and process management. Thermoforming may require less manual intervention, whereas compression molding necessitates skilled labor for setup and monitoring.
By thoroughly evaluating these production methods and their economic implications, manufacturers can make informed decisions that align with their operational capabilities and strategic goals.
Step 5: Factor in Additional Costs
In the realm of plastic molding, considering ancillary expenses is crucial for maintaining a comprehensive view of the overall budget. These additional costs, often underestimated, are essential for the seamless execution of manufacturing projects. By incorporating these expenses into your planning process, you can prevent unforeseen financial challenges and maintain control over project expenditures.
Auxiliary Expenses and Their Impact
Various auxiliary expenses arise during the manufacturing process, each contributing to the total cost of production. Understanding these expenses allows for better financial planning and resource allocation.
- Packaging: Effective packaging is essential to safeguard products during shipping and storage. This involves both material costs and the labor associated with creating secure packaging solutions. Prioritizing efficient packaging can minimize damage and reduce the need for returns, thus preserving product quality.
- Transportation: Shipping expenses depend on factors like distance, weight, and delivery method. Streamlining logistics, including selecting optimal carriers and routes, helps minimize these costs while ensuring timely delivery.
- Quality Control: Implementing rigorous quality control measures is key to maintaining uniformity and meeting industry standards. This includes costs related to inspections, testing, and compliance certifications, which help detect defects early, reducing the risk of costly recalls or reworks.
Using Mold Cost Analysis for Financial Oversight
Employing a mold cost analysis provides valuable insights into potential overages and helps anticipate financial challenges. This analysis offers a detailed breakdown of expenses, enabling manufacturers to make informed decisions and adjust strategies accordingly.
- Identifying Cost Overruns: A thorough mold cost analysis highlights areas where expenses may surpass initial estimates, enabling manufacturers to address potential issues proactively. This foresight helps avoid budget overruns and ensures financial stability throughout the project.
- Resource Optimization: By understanding the cost implications of various production elements, manufacturers can allocate resources more effectively. This involves focusing investments on areas with the highest return on investment and seeking cost-saving opportunities without compromising quality.
- Continuous Improvement: Regular mold cost analyses foster a culture of continuous improvement, encouraging manufacturers to refine processes and adopt innovative solutions. This iterative approach leads to enhanced efficiency, reduced costs, and sustained competitive advantage.
By leveraging the power of technology and adopting a strategic approach to cost estimation, you can navigate the complexities of plastic molding with greater confidence and precision. Phasio's innovative platform offers a comprehensive plastic molding price estimator that empowers you to make informed decisions and optimize your manufacturing processes. Schedule a demo or try the platform to experience how we can help you streamline your operations and achieve your production goals.