Best Practices for Quality Control in Plastic Parts
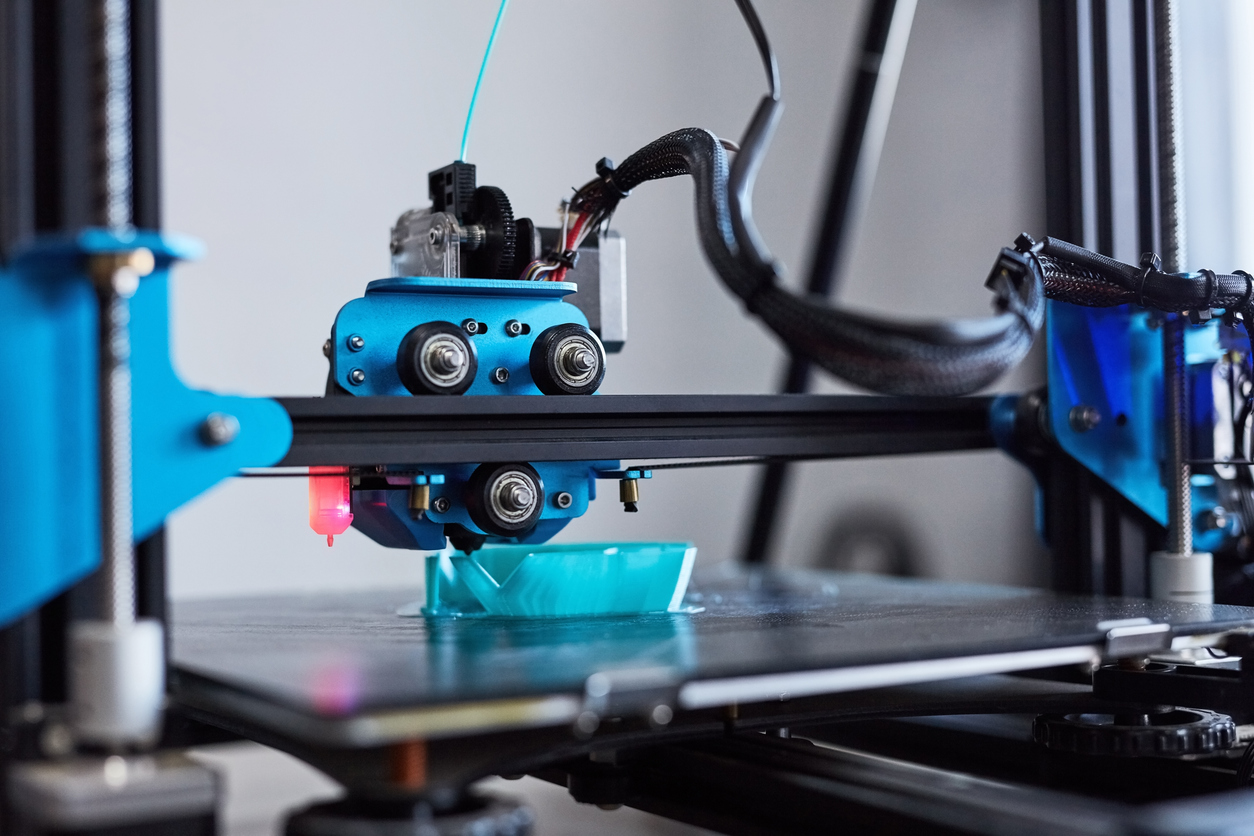
Plastic part inspection is an integral aspect of the manufacturing process, ensuring that components meet the highest quality standards and customer expectations. It involves a meticulous examination of plastic parts to identify defects, verify dimensions, and ensure compliance with industry regulations.
Effective plastic part inspection is crucial for maintaining product integrity, preventing costly recalls, and building a reputation for excellence in the competitive manufacturing landscape. By implementing rigorous quality control measures, manufacturers can minimize waste, improve efficiency, and deliver products that meet or exceed customer requirements.
In this comprehensive guide, we will delve into the world of plastic part inspection, exploring the various methods, techniques, and best practices employed by industry professionals. From visual inspections to advanced technologies, we will cover the essential steps to ensure that your plastic parts consistently meet the highest standards of quality.
What is Plastic Part Inspection?
Plastic part inspection is a critical quality control process that assesses the quality and conformity of plastic components produced through various manufacturing methods, such as injection molding. This meticulous examination involves a range of techniques to identify defects, verify dimensions, and ensure compliance with stringent industry standards.
The primary goal of plastic part inspection is to guarantee the integrity and functionality of the final product. By detecting and addressing issues early in the manufacturing process, manufacturers can prevent costly rework, reduce waste, and maintain a high level of customer satisfaction.
Plastic part inspection encompasses several key aspects:
- Visual Inspection: A thorough visual examination of the part's surface to identify defects such as scratches, discoloration, flash, or other cosmetic imperfections.
- Dimensional Verification: Utilizing precise measuring tools to ensure that the part's dimensions align with the specified design tolerances, guaranteeing proper fit and function.
- Material Properties: Assessing the material characteristics of the plastic, such as strength, flexibility, and durability, to confirm that the part meets the required performance criteria.
- Compliance with Standards: Verifying that the plastic part adheres to relevant industry standards and regulations, ensuring the product's safety and reliability.
By conducting comprehensive plastic part inspections, manufacturers can maintain a high level of quality control throughout the production process. This not only safeguards the company's reputation but also fosters trust and loyalty among customers who rely on the consistent performance of these plastic components.
How to Conduct a Plastic Part Inspection
Ensuring the quality of plastic parts in manufacturing requires a systematic and thorough approach. This begins with recognizing how quality control influences the integrity of each part and the cost-effectiveness of the production process. Implementing a comprehensive inspection protocol is essential to prevent defects that could lead to product failure or customer dissatisfaction.
Visual Inspection Methods
Visual inspection involves a detailed examination of the part to identify any surface-level issues. This process focuses on detecting visible anomalies such as irregular textures, unintended marks, or excess material at the seams. By employing consistent visual inspection practices, operators can rapidly address surface issues, preventing further complications down the line.
- Surface Irregularity Detection: Focus on identifying irregular textures or unintended marks that could affect the part's functionality or appearance.
- Standardized Inspection Practices: Utilizing uniform practices ensures reliability and repeatability across inspections, maintaining consistent quality.
Dimensional Inspection Techniques
Dimensional inspection is a precise evaluation of the part's measurements against design specifications, using advanced tools to achieve accuracy. This process often involves the use of technologies like laser scanners and 3D imaging to provide a comprehensive analysis.
- Advanced Measurement Tools: Tools such as laser scanners and coordinate measuring machines (CMMs) are crucial for verifying the part's dimensions with high precision.
- Comprehensive 3D Analysis: Employing 3D imaging technologies offers a detailed view of the part's geometry, ensuring it aligns with the design intent.
Identifying Injection Molding Defects
Identifying defects specific to injection molding is a critical aspect of the inspection process. Common issues include surface depressions, fusion lines, and dimensional distortions, which can undermine both the appearance and performance of the part.
- Defect Identification: Train staff to recognize typical molding defects like surface depressions and fusion lines, which may indicate underlying process issues.
- Preventive Measures: Implement measures to address and prevent defects, optimizing conditions to ensure consistent quality.
Non-Destructive Testing for Plastics
Non-destructive testing (NDT) methods assess the internal integrity of plastic parts without causing damage. Techniques such as thermography and acoustic emission testing reveal internal inconsistencies that might otherwise go unnoticed.
- Thermographic Analysis: Utilize infrared thermography to detect internal flaws, offering insights into material consistency.
- Acoustic Emission Testing: Use acoustic signals to identify hidden defects, ensuring the part's internal integrity remains uncompromised.
Ensuring Compliance with Plastic Part Testing Standards
Adherence to industry standards is vital to ensure that plastic parts meet safety and performance criteria. Establishing a compliance-focused inspection framework guarantees that all parts conform to essential regulations.
- Understanding Standards: Stay informed of industry standards and integrate them into your inspection practices to ensure compliance.
- Compliance Verification: Develop processes that regularly assess and verify compliance, protecting against potential non-conformities.
Employing Advanced Inspection Equipment
Incorporating modern technologies into the inspection process enhances precision and reduces reliance on manual checks. Advanced equipment, like automated imaging systems, streamlines inspections and delivers consistent results.
- Automated Imaging Systems: Leverage systems for rapid, precise inspections that limit human error and boost efficiency.
- Inspection Technology Role: Use cutting-edge technologies to enhance detection capabilities, ensuring parts are inspected to the highest standards.
Step 1: Visual Inspection Methods
Visual inspection is crucial for identifying early-stage defects that could affect the functionality or appearance of plastic parts. This process involves a detailed evaluation of the part's surface to spot irregularities such as color inconsistencies, surface blemishes, or unintended material residues. Prompt detection of these issues helps maintain quality throughout the manufacturing process and reduces the potential for costly downstream corrections.
Implementing a methodical approach enhances the reliability of visual inspections. Utilizing detailed inspection protocols, inspectors can consistently assess surface conditions, reducing subjective interpretation. Incorporating high-resolution imaging tools allows for more accurate identification of fine surface details, which might otherwise remain unnoticed, ensuring that the inspection process is thorough and effective.
Incorporating advanced quality assurance techniques bolsters the visual inspection process. This includes providing ongoing training programs that equip inspectors with the skills needed to accurately assess surface conditions. Regular maintenance and calibration of inspection tools ensure consistent performance, while systematic process evaluations identify areas for potential enhancement. These practices not only improve inspection accuracy but also embed a strong quality ethos across the manufacturing operation, ensuring every part meets rigorous industry standards.
Step 2: Dimensional Inspection Techniques
Dimensional inspection techniques play a critical role in ensuring that plastic components conform precisely to their intended design specifications. This process involves a thorough evaluation of each part’s measurements to ensure they align with the exacting standards required for optimal performance and interoperability with other components. Precision in these measurements is indispensable, as even minor inaccuracies can lead to significant issues in downstream applications.
To achieve these high standards, inspection processes employ cutting-edge technologies such as optical measurement systems and 3D scanning. Optical systems offer the ability to measure complex shapes and fine details with high accuracy, capturing data points that ensure each dimension falls within the prescribed limits. 3D scanning complements these efforts by creating a detailed digital representation of the part, allowing for comprehensive analysis and verification against design models.
By leveraging these advanced dimensional inspection techniques, manufacturers gain a complete understanding of a part’s geometry, ensuring conformity across all aspects. This thorough approach not only enhances quality assurance but also supports the consistent production of parts that meet or exceed customer expectations, ensuring reliability and satisfaction in the final product.
Step 3: Identifying Injection Molding Defects
Identifying imperfections in injection molded parts is pivotal for maintaining high standards of product quality and performance. The complexity of the molding process often leads to various anomalies that can impact the mechanical properties and visual aspects of the parts. Early detection of these issues is crucial to streamline production and uphold quality benchmarks.
A comprehensive understanding of prevalent defects is essential for their identification and resolution. Surface irregularities, such as flash where excess material forms along the mold parting line, can detract from the part’s appearance and functionality. Knit lines, formed by the joining of two flow fronts, may introduce points of weakness if not properly managed. Additionally, internal voids, resulting from trapped air during the molding process, can compromise the structural integrity of the part.
To effectively address and prevent these defects, a multi-faceted approach is necessary. Fine-tuning process parameters like pressure and cooling rates can help in minimizing defect occurrence. Utilizing predictive modeling and simulation during the design phase aids in foreseeing potential problem areas and implementing design modifications proactively. The integration of high-speed machine vision systems offers an agile solution for immediate detection and feedback, facilitating swift interventions to maintain defect-free production.
By embedding these strategies into the production process, manufacturers can ensure that defects are systematically identified and addressed. This approach not only enhances the reliability of the injection molding operation but also ensures the delivery of superior quality products that meet customer expectations. In doing so, manufacturers reinforce their commitment to excellence and competitiveness in the marketplace.
Step 4: Non-Destructive Testing for Plastics
Incorporating non-destructive testing (NDT) within the quality control framework allows manufacturers to assess the internal attributes of plastic parts without causing any damage. These advanced inspection methods are invaluable for uncovering hidden defects beneath the surface that could potentially compromise the part's integrity. By leveraging state-of-the-art techniques such as thermography and acoustic emission testing, it becomes feasible to maintain high standards of quality, ensuring compliance and durability of the final product.
Thermographic Analysis
Thermographic analysis utilizes infrared technology to evaluate the thermal profile of a plastic component, revealing inconsistencies that may indicate underlying issues. By detecting variations in surface temperature, this method can pinpoint areas of concern such as voids or inclusions. Thermographic analysis is particularly beneficial due to its non-contact nature and ability to provide rapid assessments, making it ideal for manufacturing settings where speed and accuracy are paramount.
- Non-Contact Evaluation: Offers a method to inspect parts without physical contact, thus preserving the integrity of the component.
- Swift Diagnostics: Enables quick identification of potential issues, facilitating timely interventions and adjustments in the manufacturing process.
Acoustic Emission Testing
Acoustic emission testing involves listening for stress waves emitted by a material under load, which can indicate the presence of internal defects. This technique is highly effective for detecting the onset of structural failures, allowing for preventive measures before any visible damage occurs. Although it requires specialized equipment and expertise, acoustic emission testing provides valuable insights into the material's condition without altering its structure.
- Early Detection: Captures signals of potential failures at an early stage, enabling proactive measures to prevent part failure.
- Specialized Equipment: Requires sophisticated tools and skilled operators to accurately interpret the data and ensure effective analysis.
Benefits and Limitations
The integration of thermographic and acoustic emission testing into the inspection process enhances the capacity to deliver components that adhere to rigorous quality criteria. These methods offer a non-invasive approach to identifying internal anomalies, contributing to the overall reliability and safety of the product. However, each technique comes with its own set of challenges—thermographic analysis depends on accurate interpretation of thermal data, while acoustic emission testing demands precise equipment calibration and expertise.
- Increased Assurance: Both methods significantly contribute to the assurance of high-quality, defect-free parts, reinforcing trust in the manufacturing process.
- Technical Challenges: Implementing these techniques necessitates a high level of technical proficiency and attention to detail to ensure accurate and reliable results.
By embedding non-destructive testing methods into quality assurance practices, manufacturers can ensure that plastic parts consistently meet the highest standards of performance and safety. Understanding the unique advantages and constraints of each technique allows companies to customize their inspection protocols to align with specific production objectives and quality expectations.
Step 5: Ensuring Compliance with Plastic Part Testing Standards
Adhering to testing standards in the production of plastic parts is essential for maintaining high quality and ensuring safety across various applications. These standards help manufacturers align their processes with industry best practices, which are critical for meeting both regulatory and customer expectations. Familiarizing with these standards and regulations is vital for anyone involved in the manufacturing of plastic components.
Navigating Standard Requirements
A deep understanding of applicable standards and guidelines is crucial for compliance. For example, standards like ASTM D638, which specifies methods for tensile property testing of plastics, or ISO 527, which covers similar areas, provide detailed instructions for assessing material performance. These standards serve as benchmarks that ensure parts meet required specifications for strength, flexibility, and durability.
- ASTM D638: Focuses on the tensile testing of plastic materials, providing methods to assess mechanical properties.
- ISO 527: Covers tensile testing procedures to ensure parts meet international material performance criteria.
Building Compliance Frameworks
Establishing a structured compliance framework supports consistent adherence to these standards. This involves setting up checkpoints throughout the production process to verify that parts meet the necessary criteria. Routine evaluations and updates to these frameworks are necessary to adapt to any changes in regulatory requirements or industry advancements.
- Process Checkpoints: Implement these at key stages to confirm compliance with material and performance standards.
- Routine Evaluations: Regularly assess and update compliance frameworks to reflect current standards and practices.
Record-Keeping and Part Tracking
Comprehensive record-keeping and tracking systems are essential for demonstrating compliance. Detailed documentation of inspection results, including material tests and process adjustments, creates a transparent record that can be reviewed by regulatory bodies if needed. A robust tracking system ensures that each part's journey through the production line is well-documented, enabling quick identification and resolution of any compliance issues.
- Inspection Documentation: Keep detailed records of all testing and inspection activities to support compliance verification.
- Tracking Systems: Use these to monitor each part's progress, ensuring any deviations from standards are promptly identified and addressed.
Step 6: Employing Advanced Inspection Equipment
Incorporating sophisticated inspection equipment into production workflows represents a transformative approach to quality assurance in plastic part manufacturing. These innovations provide enhanced capabilities for identifying defects and verifying dimensions with unprecedented precision. By leveraging such technologies, manufacturers can minimize inaccuracies and improve overall product reliability.
Cutting-Edge Imaging Solutions
Cutting-edge imaging solutions have become indispensable in contemporary inspection processes. These systems utilize high-resolution imaging techniques to perform detailed analyses, swiftly identifying any anomalies or variances from design specifications. The deployment of these solutions increases throughput while maintaining rigorous quality standards across diverse production scenarios.
- Detailed Imaging: Offers comprehensive evaluations of part surfaces and structures, detecting irregularities that might go unnoticed during manual inspections.
- Enhanced Throughput: Facilitates rapid assessments of large quantities of parts, ensuring consistent quality management throughout production runs.
Precision Measurement Tools
Precision tools like optical comparators and digital calipers are vital for achieving exact measurements necessary for product compliance. These instruments deliver unparalleled accuracy, enabling detailed scrutiny of complex part geometries and ensuring adherence to defined tolerances. With such tools, manufacturers can maintain rigorous standards and ensure the integrity of each component.
- Optical Comparators: Provide a precise visual comparison of parts against design templates, ensuring dimensional integrity.
- Digital Calipers: Offer accurate dimensional readings, crucial for maintaining strict tolerances and quality benchmarks.
Mitigating Manual Inspection Variability
By integrating advanced technologies, the potential for manual inspection variability is significantly reduced. Automated systems ensure uniform application of inspection criteria, leading to more consistent quality outcomes. This standardization allows human resources to concentrate on process improvement initiatives and strategic operational tasks.
- Uniform Inspection Criteria: Ensures standardized evaluations, reducing discrepancies and enhancing the reliability of quality assessments.
- Focus on Improvement: Frees skilled personnel to engage in optimizing processes and addressing strategic operational challenges.
By embracing these advanced inspection techniques and adhering to rigorous quality control standards, manufacturers can confidently deliver plastic parts that meet the highest expectations of performance and reliability. As the industry continues to evolve, staying at the forefront of inspection technology will be crucial for maintaining a competitive edge and ensuring customer satisfaction. If you're ready to streamline your plastic part inspection process and elevate your quality control, we invite you to schedule a demo or try the platform to experience its capabilities firsthand – let us help you unlock the full potential of your manufacturing operation.