Key Benefits of a Production Tracking System
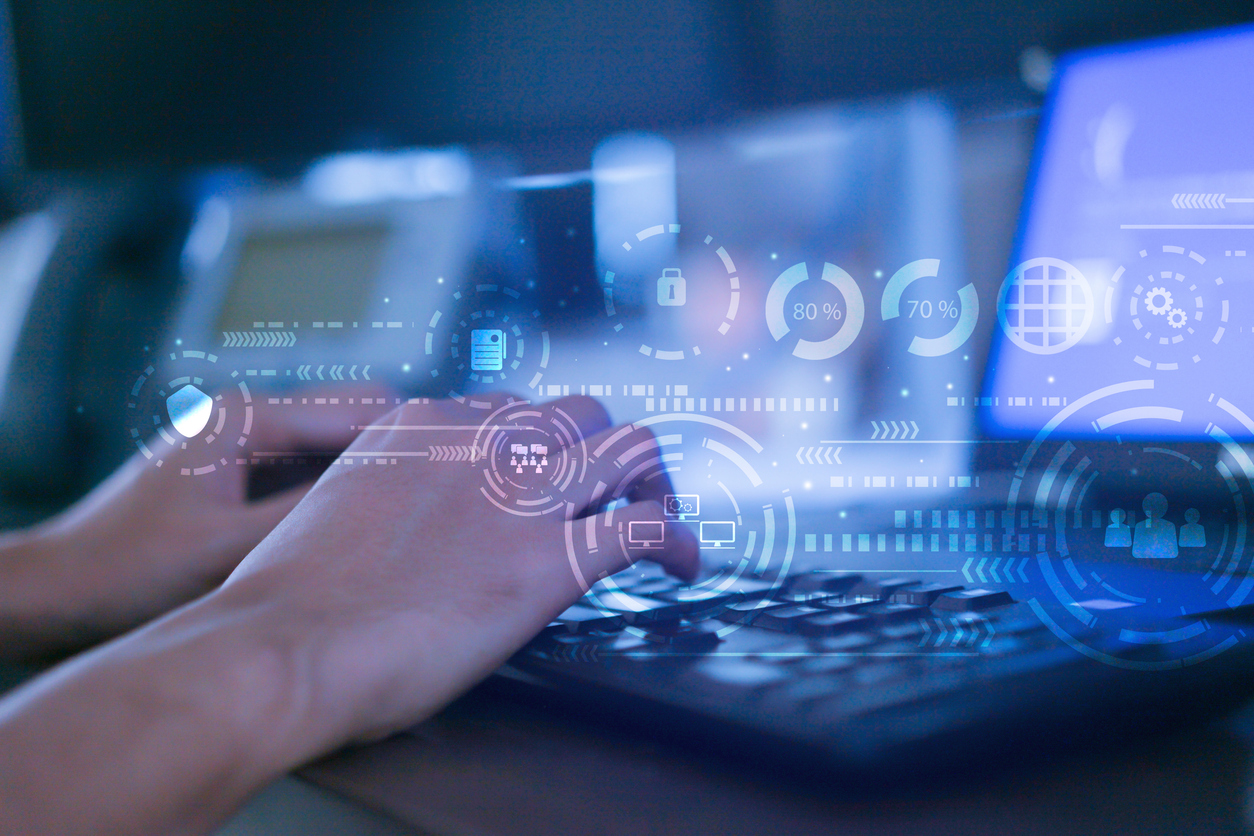
In today's fast-paced manufacturing landscape, staying on top of production processes is crucial for success. Manufacturers are constantly seeking ways to streamline operations, improve efficiency, and deliver high-quality products to their customers.
This is where production tracking systems come into play. These powerful software solutions provide real-time visibility into the manufacturing process, enabling manufacturers to make informed decisions and optimize their operations.
By leveraging production tracking software, manufacturers can gain a competitive edge in the market. They can reduce waste, improve quality control, and ultimately, increase customer satisfaction.
What is a Production Tracking System?
A production tracking system is a software solution designed to help manufacturers monitor and manage their production processes in real-time. It serves as a centralized platform that tracks materials, orders, and production activities from raw materials to finished products.
The primary goal of a production tracking system is to provide end-to-end traceability and visibility into the manufacturing process. By capturing data at every stage of production, the system enables manufacturers to have a clear understanding of their operations.
Real-Time Monitoring and Data Collection
One of the key features of a production tracking system is its ability to collect and display data in real-time. The system integrates with various sensors, machines, and devices on the shop floor to gather information about production progress, machine performance, and quality metrics.
This real-time data collection allows manufacturers to:
- Monitor production status and identify potential issues before they escalate
- Track key performance indicators (KPIs) such as overall equipment effectiveness (OEE) and cycle times
- Make data-driven decisions to optimize processes and improve efficiency
Traceability and Genealogy
Production tracking systems provide complete traceability throughout the manufacturing process. They capture detailed information about each product, including:
- Raw materials used
- Suppliers involved
- Production steps and operations performed
- Quality inspection results
- Shipping and delivery details
This level of traceability is essential for maintaining quality standards, complying with regulations, and quickly identifying and resolving issues. In case of a product recall or customer complaint, manufacturers can easily trace the affected products back to their source and take appropriate action.
Integration with Other Business Systems
To provide a holistic view of the manufacturing operation, production tracking systems integrate seamlessly with other business systems such as enterprise resource planning (ERP), customer relationship management (CRM), and accounting software. This integration eliminates data silos and ensures that all departments have access to accurate and up-to-date information.
By connecting the production tracking system with the ERP system, for example, manufacturers can:
- Automatically update inventory levels based on production consumption and output
- Generate accurate cost estimates and pricing based on real-time production data
- Streamline order fulfillment and improve on-time delivery performance
Integrating with CRM systems allows manufacturers to provide better customer service by giving sales and support teams visibility into production status and estimated delivery dates.
Empowering the Shop Floor Workforce
A production tracking system not only benefits managers and executives but also empowers the shop floor workforce. By providing real-time work instructions, quality guidelines, and performance feedback, the system helps operators perform their tasks more efficiently and accurately.
Some ways in which a production tracking system supports the shop floor include:
- Displaying digital work instructions and quality checkpoints at each workstation
- Enabling paperless production processes and electronic data capture
- Facilitating skill-based task assignment and performance tracking
- Providing real-time alerts and notifications for quality issues or machine downtime
By involving the shop floor workforce in the production tracking process, manufacturers can foster a culture of continuous improvement and employee engagement. Operators feel more ownership of the production process and are motivated to contribute ideas for optimization.
Improved Efficiency and Productivity
Efficiency and productivity drive success in manufacturing operations. Implementing a production tracking system fosters these outcomes by delivering comprehensive insights into operational dynamics and asset deployment. This access to timely data empowers manufacturers to focus on optimizing every aspect of production, from machine performance to material flow, ensuring seamless operations.
Identifying and Resolving Inefficiencies
Production tracking systems excel in revealing inefficiencies and process slowdowns. By harnessing detailed analytics from various production stages, manufacturers can quickly spot areas requiring attention. Addressing these inefficiencies involves strategic interventions, such as:
- Resource Optimization: Allocating resources more effectively to streamline production flow.
- Process Refinement: Adjusting workflows to remove redundancies and enhance throughput.
- Predictive Maintenance Strategies: Implementing planned maintenance to avert potential disruptions.
These measures enable a proactive approach to maintaining continuous and efficient production.
Facilitating Interdepartmental Collaboration
Production tracking systems significantly enhance interdepartmental collaboration by centralizing information flow. With all relevant data accessible in one platform, teams can coordinate efforts more effectively, reducing the likelihood of misalignment. The minimization of manual data entry further augments productivity:
- Automated Reporting: Reduces manual work, allowing staff to focus on critical tasks.
- Current Data Access: Ensures that team members stay informed with the most recent updates, decreasing the need for frequent briefings.
- Consistent Documentation: Offers standardized reports for strategic planning and operational adjustments.
By capitalizing on these functionalities, manufacturers can cultivate a responsive and agile production environment, thereby boosting overall efficiency.
Enhanced Quality Control and Compliance
Maintaining stringent quality control and ensuring compliance are essential for any manufacturing operation. Production tracking systems offer sophisticated tools to enhance oversight and control, allowing manufacturers to deliver products that meet high standards while adhering to regulatory requirements. These systems provide a structured approach to managing quality, reducing the risk of defects and non-compliance.
Robust Quality Assurance Processes
Production tracking systems implement rigorous quality assurance protocols throughout the manufacturing cycle. This ensures that every facet of production maintains the required quality standards. Key functionalities include:
- Integrated Quality Checks: Embeds quality assessments within production stages, ensuring timely and consistent evaluations.
- Specifications Matching: Continuously verifies product attributes against set benchmarks, promptly identifying discrepancies.
- Defect Categorization and Analysis: Systematically logs defects, facilitating precise analysis and targeted quality improvements.
By incorporating these processes, manufacturers can uphold quality across their production lines with consistency.
Streamlined Compliance and Record-Keeping
Adhering to industry regulations is crucial for operational legitimacy. Production tracking systems streamline compliance through automated documentation and effective management of audit trails:
- Efficient Documentation: Automates the creation and maintenance of detailed records for quality inspections and process changes, ensuring accuracy and availability for audits.
- Regulatory Compliance Tools: Configures to align with industry-specific standards and requirements, supporting seamless regulatory adherence.
- Transparent Audit Trails: Generates comprehensive audit trails that record every production activity, simplifying preparation for compliance audits.
These capabilities not only mitigate compliance risks but also enhance operational transparency and accountability.
Upon examining the section, let's refine the content to ensure uniqueness while maintaining its informative nature.
Optimized Inventory Management
Maximizing inventory efficiency is crucial for maintaining a streamlined manufacturing operation. Production tracking systems provide comprehensive tools for monitoring inventory levels and managing stock movements. This capability allows manufacturers to keep inventory aligned with production demands, minimizing both surplus and shortages.
Precision in Inventory Control
Production tracking systems deliver precision by offering tools that continuously update inventory status, crucial for an agile production environment:
- Real-Time Synchronization: Ensures that inventory records reflect actual stock levels, reducing discrepancies and errors.
- Dynamic Inventory Adjustments: Allows for immediate adjustments based on changes in production schedules or demand fluctuations.
- Integrated Valuation Updates: Automatically adjusts inventory valuations to reflect current market conditions and production costs.
These features provide manufacturers with the accuracy needed to support efficient inventory management practices.
Lean Manufacturing and Agile Response
The adoption of production tracking systems facilitates lean inventory practices and enhances responsiveness to market changes:
- Demand-Driven Inventory Replenishment: Automates restocking based on real-time consumption data, helping to maintain lean inventory levels.
- Enhanced Supplier Coordination: Strengthens collaboration with suppliers, ensuring prompt material delivery aligned with production needs.
- Flexibility and Adaptability: Supports quick adjustments to production plans in response to market dynamics, reducing waste and improving efficiency.
This approach not only optimizes inventory costs but also enhances the ability to respond to evolving market conditions.
Accurate Production Planning and Scheduling
Optimizing production planning and scheduling is essential for achieving seamless manufacturing operations. Production tracking systems act as an integrated platform that provides a detailed overview of production timelines, available resources, and operational limits. This clarity allows manufacturers to develop precise schedules that align with strategic goals and meet market demands efficiently.
Adaptive Scheduling and Resource Coordination
Adaptive scheduling capabilities in production tracking systems allow manufacturers to swiftly respond to shifting priorities and demand fluctuations. These systems enable efficient coordination of resources, ensuring production remains uninterrupted even when unexpected challenges arise. Key aspects include:
- Order-Driven Scheduling: Continuously adjusts production timelines to align with the most critical business objectives.
- Resource Allocation Agility: Ensures optimal deployment of machinery, workforce, and materials, minimizing idle time and maximizing efficiency.
- Modeling Diverse Scenarios: Analyzes different production scenarios to determine the most effective strategy for achieving targets.
By utilizing these features, manufacturers maintain a responsive and robust production environment.
Elevated Delivery Accuracy
Delivering products on time is crucial for maintaining customer trust and loyalty. Production tracking systems enhance delivery accuracy by offering insights into potential bottlenecks and production timelines. This proactive management results in:
- Accurate Demand Forecasting: Leverages past data and trends to anticipate future needs and fine-tune production plans.
- Balanced Workload Distribution: Equitably assigns tasks across resources to avoid overloads and ensure consistent output.
- Ongoing Order Monitoring: Provides continuous updates on order progress, allowing for timely interventions if delays occur.
These improvements foster a dependable manufacturing process that consistently meets customer expectations.
Production tracking systems are pivotal in refining the complex interplay of production planning and scheduling. By offering a comprehensive framework for managing timelines, resources, and constraints, these systems empower manufacturers to excel operationally and uphold customer satisfaction.
Data-Driven Insights and Decision Making
Leveraging data effectively stands as a pivotal element in modern manufacturing. Production tracking systems are adept at gathering comprehensive data, transforming it into valuable insights that guide strategic decisions. This capability provides manufacturers with a solid foundation for monitoring operations and identifying improvement opportunities.
Advanced Analytics for Operational Insight
Production tracking systems employ sophisticated analytics to convert raw data into meaningful insights. These insights allow manufacturers to refine processes and drive continuous improvements. Central features include:
- Interactive Data Visualization: Displays production metrics in an intuitive format, making it easier to identify trends and anomalies swiftly.
- Performance Benchmarking: Compares key metrics against industry standards, offering a clear perspective on efficiency and areas for enhancement.
- Customizable Reporting: Creates detailed reports tailored to specific operational needs, facilitating targeted improvement strategies.
These analytics enable manufacturers to enhance efficiency and optimize resource allocation effectively.
Strategic Decision Framework and Predictive Analysis
Accurate, timely data transforms decision-making into a strategic process. Production tracking systems provide tools for developing proactive strategies and forecasts, keeping manufacturers ahead in a competitive landscape:
- Predictive Maintenance: Uses data analytics to foresee maintenance needs, reducing unexpected downtime and enhancing equipment reliability.
- Production Scenario Modeling: Simulates various production strategies to assess potential impacts, aiding in risk management and decision-making.
- Resource Forecasting: Utilizes data trends to forecast future resource requirements, aligning production capabilities with market demand.
Such tools empower manufacturers to adopt a forward-thinking approach, enhancing operational resilience and flexibility.
Framework for Ongoing Enhancement
Production tracking systems foster a commitment to ongoing enhancement by equipping manufacturers with the necessary tools to evaluate and improve processes continuously. By embedding data into decision-making, manufacturers can sustain growth and achieve operational excellence.
Seamless Integration with Other Business Systems
In the modern manufacturing landscape, the ability to connect with a range of business systems is essential for maintaining operational efficiency and cohesion. Advanced production tracking systems offer robust integration capabilities that link with diverse platforms, facilitating a unified approach to managing manufacturing data. This integration ensures comprehensive insights and streamlined processes throughout the organization.
Cohesive Data Environment
Production tracking systems connect with a variety of complementary systems, such as inventory management and supply chain platforms. This connectivity creates a cohesive data environment that enhances operational oversight. The benefits of this comprehensive integration extend across several key areas:
- Holistic Process Visibility: Offers a complete view of production workflows, enabling more strategic and informed decision-making.
- Data Consistency: Maintains accurate and up-to-date records across all systems, reducing the potential for errors.
- Automated Process Management: Facilitates the automation of repetitive tasks, freeing up resources for more strategic activities.
By building a cohesive data environment, manufacturers can ensure that all stakeholders have access to consistent and reliable information, promoting transparency and accountability.
Dynamic Synchronization and Team Collaboration
Effective integration also enables dynamic data synchronization, a vital feature for adapting to market changes. This capability enhances collaboration and communication among teams, ensuring alignment with organizational objectives. Key features include:
- Instantaneous Data Updates: Guarantees that any changes made in one system are immediately reflected in others, maintaining consistency across all platforms.
- Shared Planning Interfaces: Provides access to collaborative planning tools, allowing different teams to work together more effectively on strategic projects.
- Proactive Notifications: Delivers automated alerts to keep teams informed of critical updates, such as changes in production schedules or inventory levels.
Through dynamic synchronization, production tracking systems empower organizations to operate with agility and responsiveness, essential traits in today's competitive manufacturing environment.
Establishing a Centralized Information Hub
The ultimate goal of integrating production tracking systems with other business solutions is to establish a centralized information hub. This hub ensures that all data, regardless of its source within the organization, is consistent, accurate, and readily available. The advantages of such a centralized hub include:
- Strategic Insight Development: Supports data-driven strategies by providing comprehensive insights into operational performance and emerging market trends.
- Enhanced Communication: Ensures clear and consistent information flow between departments and with external partners, strengthening collaboration and trust.
- Regulatory Adherence: Facilitates compliance with industry standards and regulations by ensuring data integrity and accessibility.
By creating a centralized information hub, production tracking systems enable manufacturers to drive efficiencies, optimize resources, and maintain a competitive edge in the market.
Empowering the Shop Floor Workforce
A crucial aspect of a thriving manufacturing operation is empowering the shop floor workforce. Production tracking systems enhance this empowerment by equipping operators with the necessary tools and insights to perform their tasks accurately and efficiently. These systems create a bridge between management and operators, fostering an environment where collaboration and shared objectives are paramount.
Dynamic Task Guidance and Assurance
Production tracking systems offer dynamic task guidance, ensuring operators have access to the latest procedural updates and quality standards. This capability allows operators to:
- Execute Tasks with Precision: Receive updated procedural guidance that minimizes errors and enhances consistency.
- Maintain High Standards: Access to detailed quality benchmarks ensures compliance with customer and regulatory expectations.
- Adapt Swiftly to Changes: Respond quickly to evolving production needs through real-time procedural updates.
These features not only enhance operational precision but also contribute to maintaining product excellence.
Digital Transformation of Work Processes
The shift towards digitized work processes is a significant advantage of implementing production tracking systems. By replacing paper-based methods with digital solutions, these systems streamline operations and enhance data integrity. Key advantages of digital work processes include:
- Accurate Data Capture: Digital systems reduce errors associated with manual data entry, ensuring information reliability.
- Process Efficiency: Streamlined digital workflows accelerate information dissemination and reduce administrative overhead.
- Sustainability Initiatives: Reducing paper usage supports environmental goals and promotes sustainable practices.
Embracing digital transformation fosters productivity and aligns with sustainability objectives.
Targeted Task Allocation and Workforce Motivation
Production tracking systems support targeted task allocation, ensuring assignments align with operator expertise. This strategic approach optimizes workforce utilization and enhances performance. Additionally, these systems boost workforce motivation by:
- Offering Insightful Feedback: Real-time performance analytics provide operators with constructive feedback, enhancing job satisfaction.
- Fostering Skill Development: Identifying skill gaps and facilitating tailored training opportunities encourage continuous improvement.
- Encouraging Team Dynamics: Transparent communication and unified goals promote collaboration and a cohesive work culture.
Through these initiatives, manufacturers can cultivate a skilled and motivated workforce that drives operational success.
In conclusion, production tracking systems are transformative tools that empower manufacturers to optimize operations, enhance quality, and drive continuous improvement. By leveraging the capabilities of these systems, you can position your manufacturing business for long-term success in an increasingly competitive landscape. If you're ready to explore how a production tracking system can revolutionize your operations, schedule a demo or try the platform to experience its capabilities – we're here to support you every step of the way.