The Complete Guide to Implementing a Production Tracking System
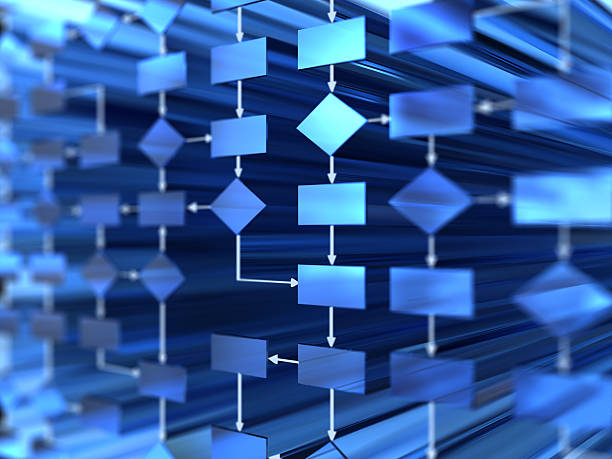
In today's fast-paced manufacturing landscape, staying competitive requires embracing technology and leveraging data-driven insights. Production tracking has emerged as an indispensable practice, enabling manufacturers to make informed decisions based on real-time, accurate information about their operations.
By implementing a robust production tracking system, manufacturers can unlock a wealth of benefits—from optimizing efficiency and quality to reducing costs and maintaining accountability. This transition aligns with the value proposition of Industry 4.0 and digital manufacturing, empowering businesses to move from simply monitoring output to proactively improving processes.
Throughout this comprehensive guide, we will explore the world of production tracking systems, delving into their functionality, benefits, implementation strategies, and best practices. Whether you're a seasoned professional looking to enhance operational efficiency or a manufacturing newcomer seeking to understand the technology, this guide aims to provide valuable insights and practical guidance to help you navigate the production tracking landscape with confidence.
What is a Production Tracking System?
A production tracking system is a comprehensive solution that monitors, records, and analyzes various aspects of the manufacturing process in real-time. It captures data on production rates, equipment utilization, quality metrics, and other key performance indicators (KPIs), providing manufacturers with a holistic view of their operations. By leveraging this data, manufacturers can make informed decisions to optimize workflows, improve efficiency, and drive continuous improvement.
At its core, a production tracking system serves as the heartbeat monitor for your manufacturing process. It offers a real-time view of the project's health, enabling you to identify bottlenecks, inefficiencies, and potential issues before they escalate into significant problems. This visibility is crucial for ensuring that projects stay on track, within budget, and adhere to quality standards.
The level of detail captured by a production tracking system can vary depending on the size and complexity of your manufacturing operation. It can range from tracking a single metric, such as the number of units produced per shift, to monitoring multiple intertwined aspects of a larger production line. Sophisticated systems, such as those offered by Phasio, can even provide advanced analytics and reporting capabilities, empowering manufacturers to uncover hidden insights and make data-driven decisions.
One of the key advantages of a production tracking system is its ability to transform raw data into actionable information. By presenting production metrics in a clear and digestible format, such as real-time dashboards and customizable reports, these systems enable stakeholders at all levels—from shop floor operators to executives—to quickly grasp the current state of operations and identify areas for improvement.
Moreover, production tracking systems play a vital role in fostering collaboration and communication among team members. With everyone having access to the same pool of trusted data, decision-making becomes more streamlined and aligned with company objectives. This transparency promotes a culture of accountability and continuous improvement, as team members can see the direct impact of their actions on production performance.
Implementing a production tracking system starts with a deep dive into your manufacturing operations. Begin by scrutinizing existing production workflows to uncover inefficiencies or constraints that may affect performance. Articulate your specific objectives—whether targeting heightened efficiency, improved quality control, or resource optimization—to guide the selection of a system that addresses these targeted areas.
In the next phase, explore a variety of production tracking software solutions available in the marketplace. An ideal system should facilitate real-time data acquisition and integrate smoothly with your current technological framework, ensuring uninterrupted information flow throughout the organization. Scalability is crucial—opt for a platform that accommodates growth, adapting to increasing production demands without compromising functionality. Evaluate the vendor’s offerings for user-friendliness and support, ensuring the software aligns with both immediate and long-term operational goals while providing deep insights into production dynamics.
Upon selecting an appropriate system, craft a comprehensive implementation blueprint detailing timelines, resources, and stakeholder roles. Seamless integration with existing systems, like ERP or MES, is key to maintaining a unified data environment, enhancing informed decision-making. Equip your team with thorough training, offering the tools and knowledge necessary to maximize the system’s capabilities. Continuous support and resources will aid in adapting to new workflows and fully exploiting the system’s potential.
Finally, establish a robust framework for ongoing monitoring and refinement of the production tracking system. Regularly evaluate collected data to pinpoint improvement opportunities and recalibrate processes to align with shifting business objectives. Foster an environment of perpetual enhancement, encouraging team involvement in initiatives aimed at refining production workflows. This proactive strategy ensures the production tracking system remains a pivotal asset, propelling efficiency, quality, and productivity across the manufacturing spectrum.
Step 1: Assess Your Manufacturing Needs
Initiate your journey by conducting a comprehensive evaluation of your production environment to identify areas ripe for optimization. This assessment should encompass the entirety of your manufacturing processes, focusing on resource utilization and workflow efficiency. By gaining a detailed understanding of your operational landscape, you set the stage for meaningful improvements that align with your strategic objectives.
To effectively assess your needs, consider the following structured approach:
- Document Process Flow: Create a detailed flowchart of your production processes, capturing each stage from raw material input to final product output. This visualization aids in pinpointing inefficiencies and resource misallocations, offering a clear pathway to potential enhancements.
- Evaluate Operational Data: Gather and analyze key performance indicators (KPIs) such as throughput, scrap rates, and machine uptime. This data-driven evaluation provides a benchmark for future improvements and highlights critical areas impacting overall performance.
- Solicit Team Feedback: Engage with employees across various departments to obtain a wide range of insights into operational challenges. Their practical experience can uncover issues that data alone might overlook, such as workflow disruptions or equipment reliability concerns.
With these insights, you can articulate specific improvement goals tailored to your unique operational challenges. Whether your focus is on boosting throughput, enhancing quality assurance practices, or optimizing resource distribution, these objectives will guide the selection of a production tracking system that seamlessly integrates with your existing infrastructure and supports your vision for ongoing advancement. Prioritizing these focus areas ensures that the system not only fits into your current setup but also propels your strategic initiatives forward.
Step 2: Research Production Tracking Software Options
Embarking on the selection of the ideal production tracking software necessitates a thorough exploration of available solutions that align with your operational demands. This stage is pivotal, as the right software can significantly enhance your ability to monitor, analyze, and optimize production processes. Consider a multi-faceted approach to ensure you select a system that not only meets your immediate needs but also supports future growth and technological advancements.
Begin your research by identifying software solutions renowned for their capacity to provide immediate insights into production performance. Systems equipped with sophisticated analytics tools offer a comprehensive view of production metrics, facilitating proactive management and continuous improvement. Such capabilities are invaluable for swiftly identifying and addressing inefficiencies, thereby optimizing overall productivity.
When evaluating options, focus on solutions that seamlessly incorporate into your current technological framework, ensuring a cohesive flow of information across all operational levels. This compatibility minimizes disruptions and enhances cross-functional collaboration, enabling your team to work more effectively. Additionally, prioritize solutions that come with intuitive interfaces and strong vendor support, as these elements are essential for ensuring smooth adoption and maximizing the software's potential without extensive training.
Growth adaptability should remain a core consideration throughout your selection process. Choose platforms that can evolve alongside your business, accommodating increasing production demands without necessitating frequent overhauls. This flexibility ensures your organization can scale operations efficiently, preserving both time and resources. By concentrating on these critical aspects, you'll be well-prepared to choose a production tracking system that not only fits your current operational landscape but also positions your business for sustained success in an ever-evolving manufacturing environment.
Step 3: Choose the Right System for Your Needs
Selecting the most appropriate production tracking system requires careful consideration of several key factors, each playing a crucial role in how well the system will integrate and enhance your manufacturing operations. To ensure the system aligns with your strategic objectives, focus on technological alignment, user accessibility, and depth of functionality.
Technological Alignment: It's essential to select a system that can effortlessly connect with your existing technological ecosystem. This means ensuring compatibility not only with current hardware and software but also with communication protocols that facilitate seamless data flow across all operational levels. An effectively aligned system will support efficient data exchange and collaboration, thereby enhancing overall productivity without the need for extensive modifications.
User Accessibility and Experience: The system should prioritize user accessibility through a design that reduces complexity and streamlines interactions. A focus on user experience encourages swift onboarding and active participation among team members. Look for solutions that offer features like customizable interfaces and intuitive navigation—these elements empower users to access pertinent data efficiently, which is vital for timely decision-making and improved operational outcomes.
Functionality and Vendor Support: Prioritize systems that offer robust functionality, including detailed analytics and real-time monitoring capabilities. These features are critical for gaining insights into production dynamics and driving continuous improvements. Evaluate the support services provided by vendors, ensuring they offer comprehensive resources and responsive assistance to help your team leverage the system's full potential and adapt to evolving needs.
Step 4: Implement and Integrate the System
Embarking on the implementation phase demands a well-coordinated plan that encompasses precise timelines and resource allocation, ensuring a seamless transition to the newly selected production tracking system. This strategic roadmap should detail each step of the roll-out process, with clearly defined milestones that guide the project’s progression. Identifying key stakeholders responsible for various aspects of the implementation is crucial to maintain focus and accountability.
Begin by forming a cross-functional project team that includes members from IT, production, and operations. This diverse group will provide valuable insights and address the distinct requirements of each department, facilitating a comprehensive integration approach. Their collective expertise is instrumental in anticipating challenges and devising effective solutions from the outset.
A pivotal element of integration is ensuring that the new system harmonizes with existing enterprise resource planning (ERP) and manufacturing execution systems (MES). This compatibility is essential for maintaining a cohesive data environment that enhances analytical capabilities and supports strategic decision-making. Opt for systems with robust APIs or integration tools that enable efficient data sharing across platforms, minimizing the risk of isolated data pools.
During this phase, prioritize data integrity by conducting thorough testing and validation to ensure the accuracy and reliability of production metrics. Address any discrepancies or technical issues promptly to build a foundation of trust in the system's outputs. This focus on data quality empowers your team to derive meaningful insights and make informed operational decisions.
As the system becomes operational, provide tailored training sessions to equip users with the skills necessary to maximize the system’s features. Design these sessions to cater to the distinct roles and responsibilities of various user groups, ensuring they can effectively navigate the new processes. Maintain ongoing support and resources to address emerging questions and challenges, fostering a culture of confidence and adaptability as your team transitions to the updated workflows.
Step 5: Train Your Team
Ensuring that your team is proficient in using the new production tracking system requires a strategic training initiative tailored to your organization’s distinct needs. Begin by conducting an assessment to determine the specific competencies required across different roles, enabling you to design a training program that addresses these targeted skills. By aligning training content with actual job requirements, you empower employees to seamlessly integrate the system into their daily operations, maximizing its effectiveness.
Incorporate a blend of instructional methods, including workshops, interactive sessions, and real-world simulations that mirror actual production scenarios. This comprehensive approach not only enhances engagement but also allows team members to practice in a realistic setting, solidifying their understanding and boosting confidence. Encourage active participation and dialogue throughout the training process, fostering an environment where employees feel comfortable voicing concerns and sharing insights, which aids in collective problem-solving.
Support ongoing development by providing accessible resources such as digital manuals, step-by-step guides, and a centralized knowledge base. These tools serve as continual learning aids, enabling team members to resolve challenges independently and deepen their system proficiency over time. Establish a robust support network, including an internal helpdesk or dedicated contact, to address any technical issues promptly. This ensures that assistance is readily available, promoting a smooth transition and fostering a culture of continuous improvement that encourages feedback and iterative learning.
Step 6: Monitor and Optimize
Once the production tracking system is operational, focus on harnessing the data it delivers to propel ongoing enhancements. Establish a routine that involves actively reviewing key metrics indicative of your production's health. This vigilance enables early identification of patterns or anomalies, providing critical insights into potential inefficiencies or areas ripe for improvement.
Extracting Actionable Insights: Engage deeply with the wealth of data generated by your system to reveal trends that can drive strategic decisions. For instance, persistent increases in machine idle times might indicate the need for better scheduling practices, while deviations in production cycles could point to process inefficiencies. By translating these insights into action, you can enact changes that significantly boost operational performance and product quality.
Facilitate regular meetings with cross-functional teams to dissect performance data, encouraging a collaborative approach to problem-solving. These sessions should focus on evaluating the effect of any changes made, recognizing achievements, and setting new targets for enhancement. Cultivate an environment where team members are empowered to suggest creative solutions, fostering an ethos of continuous adaptation and improvement in response to emerging challenges and market shifts.
Strategic Optimization Tactics: Implement a systematic approach to optimization, giving priority to initiatives based on their potential impact and ease of implementation. This might include:
- Streamlining Processes: Examine and refine workflows to remove inefficiencies and increase throughput, possibly through automation or process reengineering.
- Resource Management: Reevaluate how resources are allocated to ensure they are utilized most effectively, aligning with current production needs.
- Quality Assurance: Introduce robust quality measures to reduce variability and defects, informed by insights gleaned from real-time data analysis.
Stay vigilant for advancements in technology, continually assessing new tools and features that could further enhance your production tracking capabilities. Embracing such innovations ensures that your system remains an integral part of achieving operational excellence, driving growth, and maintaining a competitive edge.
Tips on Maximizing Production Tracking Efficiency
Leverage Immediate Data Insights
Utilizing immediate data insights is crucial for enhancing decision-making processes and boosting operational efficiency. By accessing timely information, you can swiftly detect process disruptions or inefficiencies, allowing for rapid actions that prevent costly delays. This approach ensures that manufacturing remains flexible and responsive, adapting swiftly to changing production demands.
Incorporating these insights into your operational strategy provides a comprehensive view of production dynamics, uncovering patterns that inform strategic planning. Such data-driven approaches facilitate the refinement of operational processes, driving improvements and fostering a culture where informed decisions are standard, thereby increasing overall productivity.
Strengthen Information Security
Securing data within your production tracking system is of utmost importance in maintaining operational integrity. Implementing comprehensive security measures protects sensitive information from unauthorized access and ensures compliance with industry standards, which is vital for maintaining system credibility.
Develop a robust security framework that includes encryption, user authentication, and routine security checks. These measures safeguard data accuracy and enhance trust in the production insights used for decision-making. A strong focus on data security not only protects valuable information but also empowers your team to fully exploit the tracking system's capabilities without concerns over data integrity.
Cultivate an Environment of Continuous Enhancement
Promoting an ethos of continuous enhancement is essential for achieving sustained excellence in manufacturing. Encourage your team to regularly analyze production data and participate in initiatives that seek to refine and evolve workflows. This collective effort fosters a proactive mindset that is responsive to industry developments.
Encourage collaboration and open communication across all levels of the organization to identify potential improvements. By engaging diverse perspectives, you can leverage a wide range of insights to drive innovation and operational enhancements. This dedication to ongoing improvement not only optimizes production processes but also reinforces a sense of shared responsibility and commitment to excellence throughout the company.
As you embark on your journey to revolutionize your manufacturing operations with a production tracking system, remember that the path to success is paved with continuous improvement and a commitment to leveraging data-driven insights. By following the steps outlined in this guide and embracing the power of real-time production tracking, you can unlock new levels of efficiency, quality, and profitability in your manufacturing processes. If you're ready to take your operations to the next level, schedule a demo or try the platform to experience its capabilities and see how we can help you achieve your manufacturing goals.