The Essentials of Rapid Prototyping: Methods and Applications
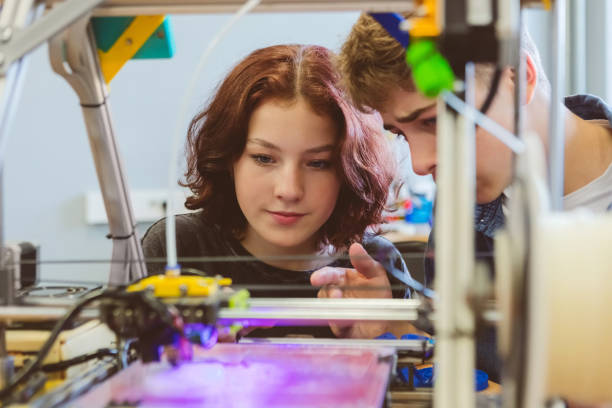
Rapid prototyping has revolutionized the way products are designed and developed. By leveraging advanced technologies and materials, manufacturers can now create physical models and functional prototypes faster than ever before.
This speed and flexibility have made rapid prototyping an essential tool for businesses looking to stay competitive in today's fast-paced market. Companies that embrace these techniques can iterate designs more efficiently, validate concepts with real-world testing, and ultimately bring better products to market in less time.
In this article, we'll dive into the world of rapid prototyping, exploring its definition, key methods, and the many benefits it offers to product development teams across industries.
What is Rapid Prototyping?
Rapid prototyping refers to a group of techniques used to quickly fabricate a scale model of a physical part or assembly using three-dimensional computer-aided design (CAD) data. Unlike traditional manufacturing methods that require costly tooling and setup, rapid prototyping enables the creation of parts directly from digital files, making it an ideal solution for low-volume production and iterative design.
The advent of additive manufacturing technologies, such as 3D printing, has been a major driver behind the growth of rapid prototyping. These tools allow designers and engineers to transform virtual models into tangible objects in a matter of hours, rather than days or weeks. By streamlining the prototyping process, teams can experiment with more design variations, gather feedback from stakeholders, and refine their concepts based on real-world testing.
Ultimately, the speed and agility offered by rapid prototyping help companies bring innovative products to market faster than their competition. By catching design flaws early, incorporating user insights, and optimizing for manufacturability, businesses can deliver higher-quality solutions that meet customer needs more effectively. Platforms like Phasio further enhance these benefits by integrating rapid prototyping into a seamless workflow that automates key tasks and facilitates collaboration between design and manufacturing teams.
Rapid Prototyping Methods and Tools
Rapid prototyping encompasses a diverse range of techniques designed to quickly transform digital designs into physical models. Each method offers unique capabilities tailored to specific materials and applications, providing manufacturers with robust tools to refine their product development processes.
Stereolithography (SLA)
Stereolithography (SLA) employs a focused laser to solidify liquid photopolymer resins, layer by layer, into precise three-dimensional objects. This method is particularly valued for its ability to produce parts with exceptional detail and smooth surfaces, which are essential for applications demanding high aesthetic and structural accuracy. The versatility of SLA in material choice allows for the creation of prototypes that closely replicate the properties of various end-use materials, making it a go-to solution for industries that require precision.
Selective Laser Sintering (SLS)
Selective Laser Sintering (SLS) utilizes a high-powered laser to fuse powdered materials like nylon or TPU into solid forms. This method excels at producing durable, functional parts without the need for support structures, enabling the creation of intricate geometries and complex assemblies. SLS is widely adopted in sectors such as automotive and aerospace, where the strength and precision of components are critical, and the ability to work with a variety of materials enhances design flexibility.
Fused Deposition Modeling (FDM)
Fused Deposition Modeling (FDM) constructs parts by extruding thermoplastic filaments in a layer-by-layer fashion. It is known for its broad accessibility and ability to use a wide array of materials, including ABS and PLA, which suits a range of applications from simple mock-ups to more durable prototypes. The cost-effectiveness and straightforward operation of FDM make it an attractive option for businesses integrating prototyping into their development cycles.
PolyJet and Multi Jet Fusion (MJF)
PolyJet technology deposits layers of liquid photopolymer, curing them with UV light to create prototypes with complex details and varied material properties. This process is ideal for applications requiring intricate designs and a high-quality finish, particularly in consumer goods and healthcare. Multi Jet Fusion (MJF) employs a precise inkjet array to selectively fuse nylon powder, producing highly detailed and consistent parts. MJF is increasingly popular in industries that demand rapid prototyping for functional testing and iterative design.
These innovative methods and tools have expanded the possibilities in rapid prototyping, providing manufacturers with the ability to efficiently produce and iterate their designs. By selecting the most appropriate process for their needs, businesses enhance their capacity to innovate and maintain a competitive edge in the market.
Benefits of Rapid Prototyping for Product Development
Rapid prototyping offers transformative advantages that redefine the product development process, making it an essential component for modern manufacturers. By shortening the cycle of design refinement, it empowers teams to innovate confidently and address challenges promptly. This dynamic approach not only enhances development agility but also encourages creative exploration with unprecedented efficiency.
A pivotal advantage of rapid prototyping lies in its capacity to reveal potential design issues at an early stage. This proactive identification is essential for ensuring product quality and adherence to performance criteria. By resolving discrepancies before the production phase, manufacturers can sidestep the drawbacks of costly redesigns and maintain project momentum, ensuring timely delivery without budget overruns.
Moreover, rapid prototyping enhances the exchange of ideas and feedback among stakeholders, providing a tangible medium for visualizing complex designs. This interaction strengthens collaboration and ensures alignment across teams, facilitating informed decision-making based on practical insights. Stakeholders benefit from a clear understanding of the design intent, fostering a cohesive approach to achieving project objectives.
Financially, rapid prototyping minimizes expenditures related to traditional manufacturing setups, such as mold creation and machining processes. This resource efficiency is particularly advantageous for projects demanding frequent revisions and bespoke solutions, as it allows for comprehensive exploration without substantial financial commitments. By streamlining production and enabling flexible adjustments, rapid prototyping supports a more sustainable and responsive development model.
In addition, the adaptability of rapid prototyping supports intricate design and customization, breaking free from the constraints typically associated with conventional methods. This capability unlocks new opportunities for designers to experiment with innovative geometries and achieve specific customer requirements, ultimately leading to superior and differentiated products in the marketplace.
Applications of Rapid Prototyping Across Industries
Rapid prototyping's adaptability has led to its widespread adoption across numerous industries, each leveraging its unique capabilities for their specific needs. By fostering innovative approaches and practical solutions, rapid prototyping has become a cornerstone in sectors where precision and customization are paramount.
Aerospace
In aerospace, rapid prototyping plays a critical role in the development of advanced components with complex geometries and functional integration. Engineers can explore cutting-edge designs that enhance aerodynamic efficiency and structural integrity, crucial for improving fuel economy and overall aircraft performance. This technology allows for the swift transition from concept to testable prototypes, ensuring compliance with rigorous industry standards and accelerating the innovation cycle.
Automotive
The automotive industry utilizes rapid prototyping to enhance the design and testing of engine components, interior elements, and exterior panels. It allows for the exploration of novel materials and innovative design strategies that prioritize sustainability and performance. By rapidly producing prototypes, automotive manufacturers can validate new technologies and adapt to shifting consumer preferences, driving advancements in vehicle safety, efficiency, and personalization.
Medical
In the medical sector, rapid prototyping has transformed the development of anatomical models, surgical tools, and custom implants. The precision and adaptability of this technology enable healthcare professionals to tailor solutions to individual patient needs, enhancing surgical planning and outcomes. Additionally, it supports the iterative development of medical devices, allowing for comprehensive validation and refinement before clinical implementation.
Consumer Goods
For consumer goods manufacturers, rapid prototyping accelerates the design process and facilitates frequent user testing. This enables companies to respond swiftly to market trends and consumer feedback, ensuring products are both functional and appealing. By reducing the barriers to prototyping, manufacturers can focus on refining product features and optimizing user experience, resulting in more competitive offerings.
As the capabilities of additive manufacturing continue to advance, rapid prototyping is finding new applications across various industry sectors. This expansion highlights its ongoing impact in refining design processes, fostering innovation, and enhancing the quality of products in diverse markets.
Choosing the Right Rapid Prototyping Process
Selecting the best rapid prototyping process demands a strategic evaluation of several critical factors, each influencing the success of product development. The right choice not only ensures that the prototype meets performance criteria but also aligns with project budgets and timelines.
Material Properties and Application Requirements
A crucial aspect of selecting a prototyping method is aligning the material characteristics with the intended application. Each technique offers unique material compatibilities, affecting the prototype's strength, flexibility, and durability. For instance, processes like Multi Jet Fusion (MJF) excel in producing functional parts with consistent mechanical properties, while PolyJet is ideal for prototypes requiring fine details and multiple material textures. By tailoring the material choice to the specific demands of the application, manufacturers can ensure that the prototype performs as expected under real-world conditions.
Precision and Surface Quality
The precision and surface quality required from a prototype guide the selection of the appropriate method. For projects necessitating intricate designs and smooth finishes, technologies such as PolyJet and SLA provide the necessary precision and aesthetic quality. Alternatively, when the focus is on validating the fit and functionality rather than detail, methods like FDM offer a practical solution with efficient use of resources. Understanding these nuances helps in selecting a process that delivers the desired level of detail without overextending the project budget.
Budget, Timeline, and Design Constraints
Balancing budget, timeline, and design constraints is paramount when choosing a rapid prototyping method. Different processes incur varying costs and production times, requiring careful assessment to align with project goals. For instance, while SLA might offer quicker turnaround for detailed prototypes, FDM might present a cost-effective alternative for simpler designs. Additionally, being aware of each method's limitations—such as build volume and support requirements—ensures that the design intent is preserved throughout the prototyping phase. Engaging with knowledgeable service providers can further refine the selection process, ensuring that the chosen method supports the project's objectives effectively and efficiently.
Streamlining Rapid Prototyping Workflows
To enhance efficiency in rapid prototyping, it's essential to develop a workflow that integrates design, prototyping, and testing seamlessly. By tailoring CAD models specifically for the prototyping technique chosen, manufacturers can ensure a smooth transition from digital designs to tangible prototypes. This involves making precise adjustments to align with the technological constraints and capabilities, thereby reducing errors and ensuring the prototype accurately reflects the design's intent.
Adopting principles of Design for Additive Manufacturing (DfAM) is crucial in this optimization process. DfAM focuses on leveraging the unique advantages of additive technologies, such as creating complex geometries and reducing material use. By factoring in aspects like build orientation and the reduction of support material, designers can maximize the efficiency and quality of the prototypes produced, ensuring they are both functional and optimized for further development.
Software tools play a pivotal role in automating the preparation of files for 3D printing, streamlining tasks such as slicing and error detection. These automated processes minimize the need for manual input, thus reducing setup times and improving accuracy. By focusing efforts on innovation and iterative design rather than troubleshooting, teams can allocate more resources to refining their ideas and speeding up the overall development cycle.
Implementing an agile framework that emphasizes rapid design, prototyping, and testing cycles enhances the ability to adapt quickly to feedback and refine designs. This iterative approach promotes continuous learning and agility, allowing for swift adjustments based on real-world testing and stakeholder input. Such a framework supports dynamic decision-making and encourages a culture of flexibility and innovation.
Incorporating technologies like simulation and metrology into the rapid prototyping workflow further enriches the development process. Simulation provides crucial insights into how designs will perform in various scenarios, enabling design refinements before physical prototypes are created. Metrology ensures that prototypes meet stringent specifications and quality standards, adding an extra layer of assurance to the development cycle. This comprehensive integration of tools and processes not only streamlines prototyping but also empowers manufacturers to leverage the full potential of digital manufacturing advancements.
As the landscape of manufacturing evolves, rapid prototyping will continue to play a vital role in driving innovation and competitiveness. By leveraging the right methods and tools, and integrating them into streamlined workflows, businesses can unlock new possibilities in product development. If you're ready to take your prototyping process to the next level, schedule a demo or try the platform to experience how we can help you transform your manufacturing operations.