Optimizing Your SLA Batch Planning Process: Best Practices
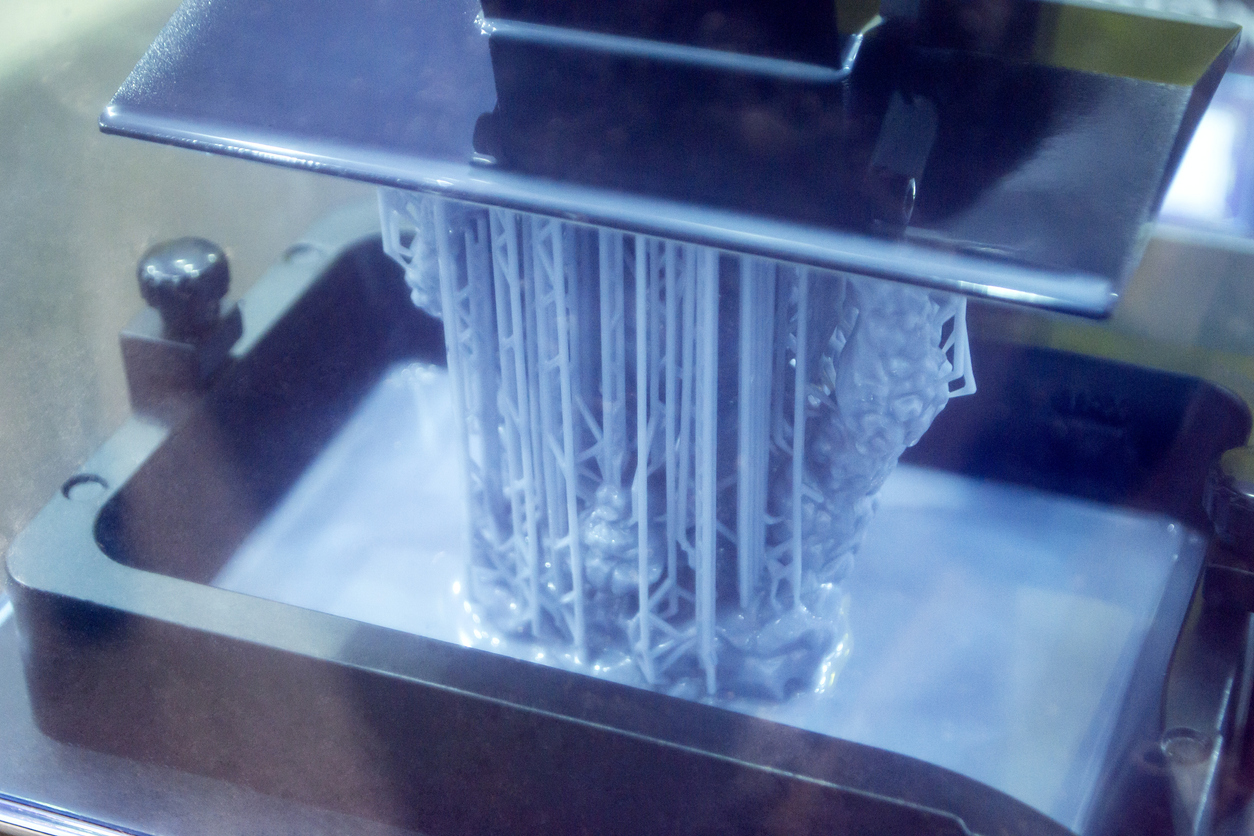
Effective batch planning is a critical component of meeting service level agreements (SLAs) in manufacturing environments. By optimizing production schedules and resource allocation, manufacturers can ensure timely delivery of products while maintaining high levels of efficiency and quality.
Implementing a well-designed SLA batch planning process can lead to significant improvements in operational performance and customer satisfaction. It enables manufacturers to streamline their workflows, reduce waste, and minimize the risk of missed deadlines or subpar quality.
In this article, we will explore the concept of SLA batch planning and provide practical strategies for optimizing your planning process. We'll cover key techniques, best practices, and real-world examples to help you achieve better results in your manufacturing operations.
What is SLA Batch Planning?
SLA batch planning is the process of organizing and scheduling production activities to meet service level agreements effectively. It involves coordinating resources, timelines, and priorities to ensure that batch jobs are completed within the constraints defined in the SLAs. The primary goal is to optimize production efficiency while consistently delivering products or services that meet or exceed customer expectations.
Effective SLA batch planning requires a deep understanding of the manufacturing process, available resources, and customer requirements. It involves analyzing historical data, forecasting demand, and developing contingency plans to mitigate potential risks or disruptions. By aligning production schedules with SLA targets, manufacturers can improve on-time delivery rates, reduce lead times, and enhance overall customer satisfaction.
One key aspect of SLA batch planning is the use of performance metrics to monitor and optimize the production process. Common metrics include throughput, cycle time, and quality levels. By tracking these metrics in real-time and comparing them against SLA targets, manufacturers can quickly identify bottlenecks or issues and take corrective action. Tools like Phasio can help automate data collection and analysis, providing valuable insights for continuous improvement.
How to Optimize Your SLA Batch Planning Process
Enhancing SLA batch planning requires embedding service level objectives into the production framework. This starts with a comprehensive grasp of client expectations and translating these into detailed operational plans. Every stage in the manufacturing process must reflect SLA commitments, ensuring consistency and reliability. By integrating SLA targets at the foundational level, manufacturers can preemptively align their activities with the desired outcomes.
To effectively manage SLA batch planning, focus on key operational metrics that drive performance. Metrics such as production efficiency, downtime minimization, and defect rates highlight areas needing attention. Consistent tracking and analysis enable manufacturers to spot inefficiencies and implement corrective measures swiftly. Leveraging advanced data analytics provides insights for continuous refinement and proactive strategy adjustments.
Balancing efficiency with SLA adherence calls for a structured approach that leverages both operational strengths and customer requirements. Implementing agile manufacturing methodologies can enhance responsiveness while maintaining SLA standards. Optimal resource utilization ensures that capabilities are maximized without straining SLA compliance. Cross-functional communication plays a pivotal role, fostering an environment where all teams work towards unified service goals.
1. Analyze Current Processes
Begin by conducting an in-depth audit of your current batch planning methods. This process involves examining the entirety of your production workflow to identify specific areas that contribute to bottlenecks or delays. Engage with cross-functional teams to gather diverse perspectives on operational challenges. Their input can uncover hidden issues and provide a comprehensive view of the planning landscape.
Pinpointing inefficiencies requires a strategic approach. Focus on areas where resources are frequently strained or where manual interventions disrupt flow. Consider the impact of equipment age, maintenance schedules, and procedural complexities on your operations. By understanding these contributing factors, you can formulate targeted strategies to streamline processes and enhance productivity.
Leverage the power of advanced data analytics to gain a nuanced understanding of production dynamics. Utilize tools that allow for the tracking of detailed performance metrics such as lead times and defect rates. Analyzing historical data and patterns enables you to anticipate potential disruptions and adjust plans accordingly. This analytical approach ensures your batch planning remains agile and aligned with broader operational goals.
2. Develop a SLA Batch Planning Template
Designing a structured SLA batch planning template is crucial for maintaining uniformity and efficiency in production scheduling. This template serves as a comprehensive guide, ensuring that all necessary planning phases are systematically addressed. By establishing standardized procedures, manufacturers can enhance operational consistency and streamline adherence to service level agreements. The template acts as a central reference point that aligns planning efforts with broader organizational and customer objectives.
The template should integrate pivotal components essential for efficient batch planning. Clear timelines are imperative for outlining each production phase and synchronizing milestone achievements with SLA requirements. Detailed plans for resource deployment must be included, specifying the allocation of personnel, equipment, and materials to optimize their use and prevent delays. Moreover, robust contingency plans are essential; they provide predefined strategies to address potential disruptions, ensuring that production continues smoothly despite unforeseen challenges.
Flexibility is a core characteristic of an effective SLA batch planning template. Manufacturing environments are inherently dynamic, with production demands often shifting due to varying market conditions or customer requirements. Therefore, the template must be adaptable, allowing for seamless modifications without jeopardizing SLA goals. By incorporating scalable procedures and adaptive resource management tactics, the template remains resilient under changing conditions. This adaptability enables manufacturers to respond promptly to shifts while maintaining high standards of quality and delivery.
3. Implement SLA Optimization Techniques
Integrating cutting-edge technologies into SLA batch planning elevates accuracy and operational efficiency. Advanced planning systems can streamline complex processes, reducing the dependency on manual oversight. These systems enhance the reliability of scheduling and resource distribution, allowing teams to focus on strategic improvements rather than routine tasks. This transition not only refines operational precision but also maintains alignment with SLA benchmarks during periods of high demand.
Harnessing the power of data-driven insights provides a competitive edge in managing production demands. By employing sophisticated analytical tools, manufacturers can predict shifts in demand and adjust their resource strategies accordingly. These insights enable a more responsive allocation of resources and inventory management, ensuring that production levels are optimized without compromising service agreements. This proactive approach minimizes disruptions and aligns production outputs with the expectations set by SLAs.
Clear communication channels are vital for aligning team efforts with SLA objectives. Establishing robust communication frameworks ensures that all team members have access to up-to-date information and can react promptly to changes. Utilizing integrated communication platforms enhances visibility across departments, facilitating swift coordination and problem resolution. Regular inter-departmental check-ins foster a unified approach to meeting service goals, enabling teams to work collaboratively towards maintaining SLA standards.
4. Monitor and Adjust Plans
To maintain robust SLA compliance, focus on refining the precision of batch planning through targeted assessments. This involves evaluating production outcomes using detailed performance indicators tailored to specific SLA criteria. A structured evaluation framework ensures that deviations are swiftly identified and addressed. By consistently applying this methodology, manufacturers can uphold SLA standards and enhance overall process reliability.
Implement iterative refinement processes to ensure ongoing enhancements. These processes collect insights from diverse operational areas, including logistics, production control, and customer feedback. Analyzing these insights offers a holistic perspective on workflow efficiency and uncovers opportunities for strategic adjustments. Incorporating such iterative refinements into the planning framework allows manufacturers to systematically enhance their approach.
Remaining agile in adopting industry innovations is crucial for sustaining competitive advantages. Regularly update strategies to incorporate new technological tools and methodologies that improve operational precision and scalability. Being proactive in this regard ensures that batch planning adapts swiftly to changes in the industry landscape. This adaptability is key to ensuring that planning processes remain effective and aligned with evolving SLA requirements.
5. Train and Educate Your Team
Empowering your team with targeted training programs is essential for mastering SLA batch planning. These programs should focus on both the technical aspects and strategic application of planning tools. Providing instruction on advanced scheduling technologies and resource allocation strategies can significantly improve your team's operational capabilities. By prioritizing training, organizations ensure that their teams are well-prepared to meet the dynamic demands of SLA compliance.
Commitment to continuous learning is vital for staying competitive. Facilitate access to cutting-edge SLA management solutions by offering workshops and seminars that explore emerging technologies. This exposure encourages team members to integrate fresh methodologies into their planning processes. Additionally, fostering an environment where team members share insights and best practices can enhance collective expertise and adaptability.
Cultivating a collaborative and innovative culture is crucial in optimizing batch production planning. Encourage collaborative efforts across departments to tackle complex planning challenges, utilizing a broad range of insights to develop effective solutions. Implement regular sessions where teams can brainstorm and exchange ideas, promoting an atmosphere of open communication and creativity. By nurturing a cooperative spirit, organizations can drive continuous improvement and align closely with SLA objectives.
6. Evaluate and Refine Your Strategy
Conducting post-implementation reviews provides valuable insights into the performance of your batch planning strategies. Focus these reviews on analyzing key metrics such as cycle times, resource utilization, and throughput rates. By using this data-driven approach, you can pinpoint inefficiencies and areas for enhancement. This systematic evaluation enables you to make informed decisions, ensuring your planning processes align with both operational goals and customer expectations.
Involving stakeholders from various departments enriches the evaluation process with diverse perspectives. Gather insights from supply chain managers, production technicians, and quality assurance teams to uncover practical challenges and opportunities. Host collaborative workshops to facilitate dialogue and gather actionable feedback. By integrating these insights, you cultivate a culture of continuous improvement, driving innovations that align with SLA objectives.
Remaining agile in your strategy is essential to responding to dynamic market and customer demands. Regularly update your planning methodologies to incorporate the latest technological advancements and industry best practices. This adaptive approach involves reassessing assumptions, reallocating resources, and integrating new tools to maintain peak performance. By staying proactive and flexible, you ensure your operations remain robust and SLA-compliant in the face of change.
Optimizing your SLA batch planning process is an ongoing journey that requires dedication, adaptability, and a commitment to continuous improvement. By leveraging the right strategies, tools, and mindset, you can drive significant enhancements in your manufacturing operations, ensuring consistent compliance with service level agreements. If you're ready to take your batch planning to the next level, schedule a demo or try the platform to experience its capabilities – we're here to support you every step of the way.