Understanding SLS Part Validation: Key Considerations
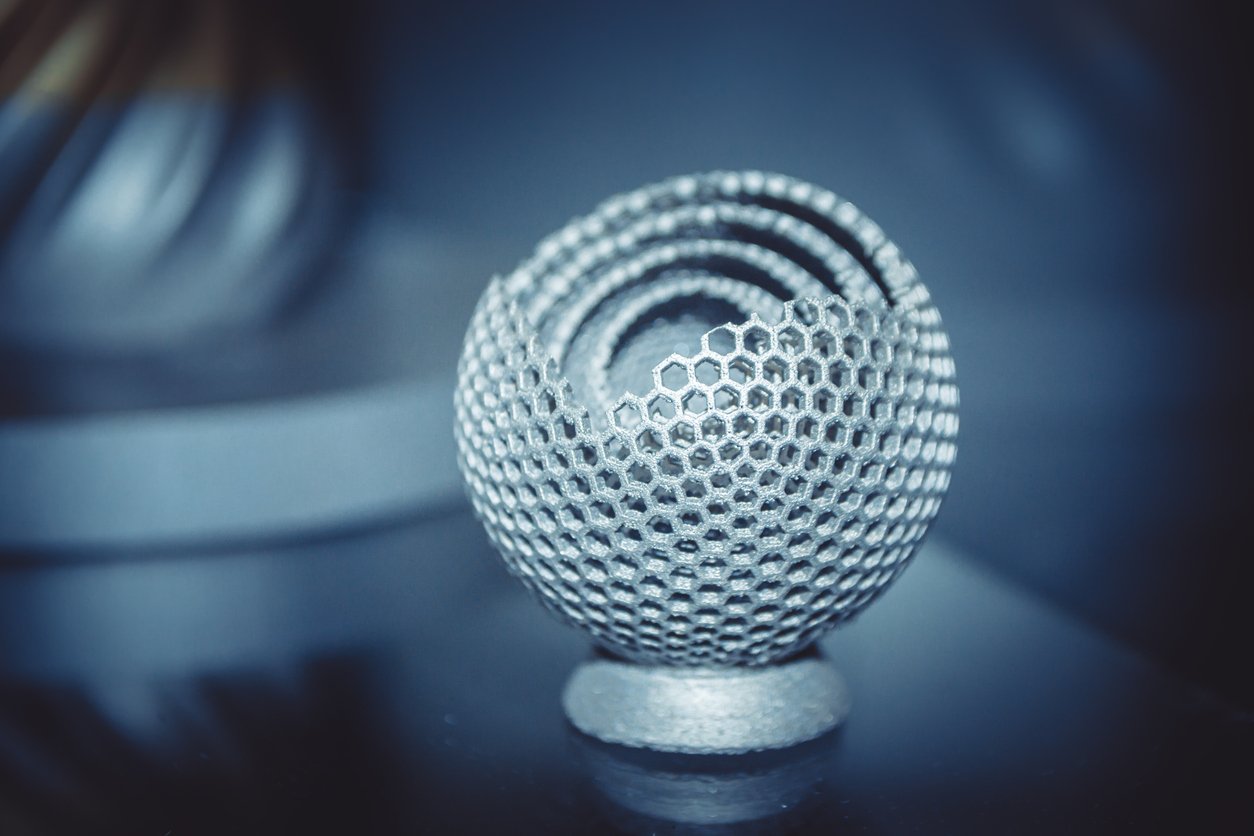
Selective Laser Sintering (SLS) has emerged as a powerful additive manufacturing technology, enabling the production of complex, high-performance parts. However, ensuring the quality and reliability of SLS-printed components is crucial for their successful implementation in various applications.
Validating SLS parts involves a comprehensive set of processes and techniques designed to assess their dimensional accuracy, mechanical properties, and overall functionality. By implementing robust validation methods, manufacturers can minimize defects, optimize part performance, and deliver consistent results to their customers.
In this article, we will delve into the key aspects of SLS part validation, exploring the best practices, challenges, and solutions for ensuring the highest quality standards in SLS 3D printing.
What is SLS Part Validation?
SLS part validation is a critical process that ensures 3D-printed components meet the required quality standards and performance specifications. It involves a series of inspections, tests, and measurements designed to identify potential defects, verify dimensional accuracy, and assess the mechanical properties of SLS parts.
The validation process begins with a thorough examination of the part geometry and design. Complex internal features, thin walls, and fine details can push the limits of SLS resolution and accuracy, making them more challenging to inspect and test. Experienced engineers carefully review the part design to identify areas that may be susceptible to warping, curling, or incomplete sintering during the SLS build process.
Material properties and behavior also play a significant role in SLS part validation. Each SLS material exhibits unique mechanical characteristics that impact the final part performance. For example, crystalline and semi-crystalline materials are prone to shrinkage and warping, while fiber-reinforced materials may display anisotropic properties in the build direction. Understanding these material-specific behaviors is essential for developing effective validation strategies.
Automated pricing solutions, such as those offered by Phasio, can provide valuable insights during the validation process. By capturing key design elements that impact production time and cost, these tools factor in material usage, machine time, and post-processing requirements. This information serves as a baseline for quoting and validating SLS parts before production begins, ensuring that the final components meet both quality and cost expectations.
Key Considerations for SLS Part Validation
Part Geometry and Design
The design intricacies of SLS parts play a pivotal role in the validation process. While SLS technology excels at producing intricate geometries, evaluating these complex structures requires advanced inspection methods. Features like intricate internal channels and fine details demand precise validation techniques to ensure they meet design specifications.
Some geometries, especially those with unsupported sections or large overhangs, are prone to deformation during the build phase. Addressing these potential issues in the design phase is critical to maintain the dimensional integrity of the final product. Engineers must preemptively consider these factors to optimize performance without compromising on accuracy or reliability.
Material Properties and Behavior
The unique properties of each SLS material significantly affect validation outcomes. Materials used in SLS exhibit distinct mechanical characteristics that influence part performance. For example, materials with higher crystallinity may undergo dimensional changes, necessitating adjustments during the validation phase to accommodate these properties.
Materials reinforced with fibers introduce additional complexity, as the orientation of these fibers can influence the mechanical properties of the finished part. Understanding how these materials behave under different conditions is essential for accurate validation and to ensure the parts meet the desired performance criteria.
Automated Pricing for SLS
Automated pricing tools enhance the SLS validation process by providing insights into design elements that impact production efficiency. These systems account for factors such as material consumption, machine operation time, and the need for post-processing, offering a detailed baseline for pre-production validation. By integrating these insights, manufacturers can ensure that each SLS part aligns with quality and cost objectives, supporting broader operational goals.
Methods for Validating SLS Parts
To achieve the highest standards in SLS part production, a comprehensive validation strategy is essential, incorporating diverse inspection and testing methodologies. By leveraging advanced techniques in visual assessment, precise dimensional analysis, and rigorous mechanical evaluation, manufacturers can ensure the integrity and performance of SLS components.
Visual Inspection
Implementing an SLS Part Validation Workflow
Establishing a structured validation workflow ensures that SLS parts consistently meet quality standards. The process begins with setting precise specifications and acceptance criteria, which guide the entire manufacturing trajectory. By clarifying these parameters at the outset, manufacturers can align production efforts with defined objectives, minimizing errors and ensuring adherence to desired standards.
Incorporating inspection and testing throughout the production timeline is critical. Strategically placed evaluation points—such as visual inspections and dimensional analyses—detect potential issues early, allowing for timely interventions. This proactive approach not only reduces material waste but also enhances the efficiency of the production line, ensuring that quality is maintained from start to finish.
Documentation serves as the backbone of a successful validation workflow. Detailed records of each validation step provide traceability, allowing manufacturers to track part performance and identify patterns over time. This data is invaluable for refining processes, enabling continuous improvement. By leveraging performance insights, manufacturers can adapt validation strategies to meet evolving technological capabilities and market demands, ensuring that the workflow remains robust and responsive.
As the additive manufacturing landscape continues to evolve, SLS part validation remains a critical aspect of ensuring the highest quality standards in 3D printing. By understanding the key considerations and implementing robust validation methods, manufacturers can unlock the full potential of SLS technology, delivering reliable and high-performance parts to their customers. If you're ready to streamline your manufacturing processes and enhance your SLS part validation capabilities, schedule a demo or try the platform to experience how we can help you achieve your goals.