Optimizing SLS Production Workflows: A Practical Guide
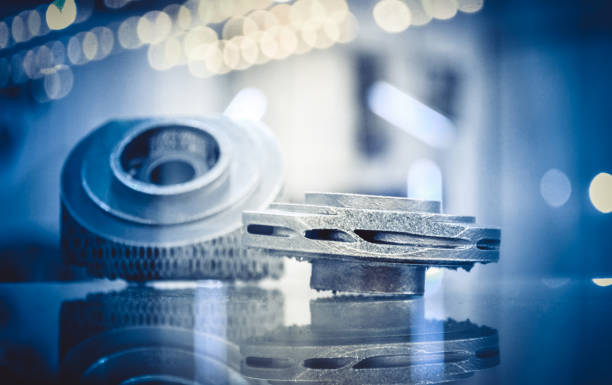
Selective laser sintering (SLS) has revolutionized the world of additive manufacturing, enabling the production of complex, high-performance parts with unparalleled precision. As the demand for SLS-manufactured components continues to grow across various industries, optimizing production workflows becomes increasingly crucial for manufacturers seeking to remain competitive in a rapidly evolving market.
Efficient SLS production workflows not only streamline the manufacturing process but also contribute to cost reduction, improved part quality, and faster time-to-market. By implementing best practices and leveraging advanced technologies, manufacturers can unlock the full potential of SLS and position themselves at the forefront of the additive manufacturing landscape.
In this article, we will explore the key aspects of SLS production workflows, delving into the strategies and techniques that can help manufacturers optimize their processes for maximum efficiency and profitability. From design optimization to post-processing techniques, we will provide valuable insights to help you navigate the complexities of SLS manufacturing and achieve optimal results.
What is SLS Production Workflow?
Selective Laser Sintering (SLS) production workflows encompass the entire process of creating parts using SLS technology—from the initial design stage to the final post-processing steps. This powder bed fusion technique utilizes a high-powered laser to selectively sinter powdered materials, such as nylon or polypropylene, layer by layer until a solid object is formed.
The SLS production workflow typically consists of several key stages:
- Design and Preparation: The process begins with creating a 3D model of the desired part using computer-aided design (CAD) software. The model is then optimized for SLS printing, taking into account factors such as wall thickness, feature size, and part orientation to ensure successful printing and optimal mechanical properties.
- Material Selection and Management: Choosing the appropriate powdered material is crucial for achieving the desired part characteristics. Material properties such as strength, flexibility, and chemical resistance must be considered based on the application requirements. Efficient material management, including storage, handling, and recycling of unused powder, is essential for maintaining consistent part quality and reducing waste.
- Printing Process: Once the design is finalized and the material is selected, the 3D model is sliced into thin layers, and the data is sent to the SLS machine. The printer preheats the powder bed to a temperature just below the material's melting point, and the laser selectively sinters the powder particles to form a solid layer. This process is repeated layer by layer until the entire part is built, with the unsintered powder acting as a support structure for overhanging features.
- Post-Processing: After printing, the build chamber is allowed to cool before the parts are removed from the powder bed. Excess powder is then removed from the parts using various techniques such as brushing, compressed air, or media blasting. Additional post-processing steps, such as sanding, dyeing, or coating, may be applied to improve surface finish, aesthetics, or functionality.
By understanding and optimizing each stage of the SLS production workflow, manufacturers can streamline their processes, reduce lead times, and produce high-quality parts consistently. Leveraging software solutions, such as those offered at Phasio, can further enhance workflow efficiency by automating tasks, improving communication, and providing valuable insights for continuous improvement.
Enhancing SLS production workflows is critical for manufacturers striving to excel in a dynamic market. This approach enables the refinement of operational processes, leading to significant reductions in production expenses and elevating the caliber of manufactured parts. By implementing a well-structured workflow, businesses can curtail inefficiencies, thereby expediting production schedules and optimizing output consistency.
In the sphere of advanced manufacturing technologies, where accuracy and rapidity are essential, a refined SLS workflow can markedly expand a manufacturer's production capabilities. By decreasing the turnaround time for each batch, manufacturers can boost their capacity, allowing them to accommodate increasing customer orders and swiftly adapt to market demands. This agility not only enhances the service provided to clients but also strengthens business relationships and fosters customer retention.
Furthermore, refining SLS workflows assures consistent and reliable product quality, a vital factor for broadening the scope of product applications. Consistent production reduces variability, ensuring that each part meets stringent quality standards and is fit for a diverse range of uses. As the demand for SLS-produced components continues to grow, manufacturers who prioritize workflow refinement are poised to seize emerging opportunities and maintain their industry leadership.
How to Optimize SLS Production Workflows
Effective management of SLS workflows requires a comprehensive strategy that refines each phase of production. By focusing on critical areas such as component preparation, material efficiency, and cutting-edge printing methodologies, manufacturers can significantly enhance their SLS processes.
Component Preparation and Design
A pivotal step in optimizing SLS workflows involves strategic component preparation. Employing advanced design software enables manufacturers to tailor components specifically for SLS capabilities, emphasizing features like internal structures and reduced mass. By integrating digital validation tools, potential issues such as thermal distortion can be addressed proactively, ensuring successful outcomes during the build phase.
Efficient Material Utilization
Streamlining material usage is essential for optimizing SLS workflows. Selecting materials that align with specific performance criteria—such as flexibility and durability—is crucial. Implementing efficient storage solutions and recycling protocols minimizes waste and supports sustainability efforts. By maintaining a balance between recycled and new materials, manufacturers can ensure consistent quality while reducing costs.
Innovative Printing Methodologies
Harnessing the latest advancements in SLS printing can significantly boost production efficiency. Modern machines equipped with features such as thermal regulation and precise energy delivery enhance build accuracy and speed. Automation in the arrangement of parts within the print chamber maximizes output per cycle, while real-time analytics provide data-driven insights for continuous improvement.
Refinement of Post-Processing Techniques
The post-processing stage plays a crucial role in achieving the desired quality of SLS-produced parts. Automating post-processing tasks like powder removal and surface treatment enhances operational efficiency. Techniques such as precision finishing and surface enhancement improve the mechanical properties and aesthetic appeal of the parts. By adopting a systematic approach to post-processing, manufacturers can consistently deliver high-quality products that meet rigorous standards.
Focusing on these key aspects of SLS production allows manufacturers to refine their processes and capitalize on the full potential of this technology. Through strategic enhancements across each phase, businesses can achieve superior efficiency and maintain a competitive edge.
1. Streamlining Design and Preparation
Efficient design and preparation are vital steps in the SLS production process, as they lay the groundwork for successful manufacturing. By addressing potential hurdles early, manufacturers can ensure that each part is produced with precision, minimizing the need for extensive post-processing. This approach not only reduces material wastage but also enhances the overall effectiveness of the production workflow.
Advanced Design Techniques
Utilizing state-of-the-art CAD software is crucial for crafting parts that fully exploit the potential of SLS technology. These tools enable designers to refine geometries, integrate internal frameworks, and optimize material usage while maintaining part integrity. Innovative design techniques, such as incorporating honeycomb structures, can lead to significant weight reduction without compromising strength, which is particularly important in industries focused on lightweight components.
Key design strategies include:
- Consistent Feature Dimensions: Ensuring uniformity in feature sizes to prevent thermal stress and achieve dimensional accuracy.
- Strategic Part Placement: Positioning parts in a way that maximizes build chamber efficiency and minimizes thermal distortion.
- Innovative Structural Designs: Crafting intricate features that leverage SLS's ability to produce complex parts without conventional supports.
Implementing Additive Manufacturing Software
Integrating advanced additive manufacturing software into the design phase enhances process efficiency by providing real-time optimization and validation capabilities. These platforms enable simulation of SLS processes, allowing for proactive adjustments that increase build reliability. The software can also streamline routine checks, ensuring that designs adhere to specifications and are ready for manufacturing.
Advantages of using advanced software include:
- Predictive Analysis: Anticipating potential design issues to streamline production and reduce errors.
- Automated Workflow Integration: Simplifying repetitive tasks to allow engineers to focus on solving complex design challenges.
- Seamless Data Transfer: Ensuring that design data is accurately interpreted by SLS machines for precise manufacturing.
By concentrating on these aspects of design and preparation, manufacturers can greatly improve the efficiency and quality of their SLS production workflows. This strategic focus not only optimizes resource use but also enhances the reliability and speed of the manufacturing process.
2. Material Selection and Management
In SLS production, selecting materials that complement specific project demands is essential. The choice of material profoundly impacts the durability, aesthetics, and performance of the final part. Manufacturers must assess attributes such as elasticity, temperature tolerance, and resistance to environmental factors to ensure the material's suitability for its intended function. This thorough evaluation guarantees that each component fulfills its operational requirements with precision and reliability.
Material Properties and Application Requirements
Delving into the specific characteristics of SLS-compatible materials enables manufacturers to tailor their choices to each project's unique needs. For example, polyamide powders, such as PA12, offer excellent rigidity and impact resistance, making them ideal for high-stress applications like aerospace and automotive parts. Alternatively, materials like polypropylene provide chemical resistance and flexibility, suited for components exposed to harsh environments or requiring some degree of flex.
Important factors for material consideration include:
- Elastic Modulus: Ensuring the material can withstand expected loads without permanent deformation.
- Heat Deflection: Selecting materials that maintain integrity under operational temperatures.
- Environmental Compatibility: Choosing options that resist degradation from UV exposure or corrosive substances.
Effective Material Management Practices
Managing materials efficiently involves strategic approaches to minimize wastage and optimize resource allocation. Implementing closed-loop systems for material reuse can significantly enhance sustainability and cost-effectiveness. Proper environmental controls, such as maintaining optimal temperature and humidity levels, are crucial for preserving material quality and ensuring consistent output.
Strategies for effective material management:
- Material Reuse: Utilizing advanced sorting and cleaning techniques to reclaim powder from the production process.
- Supply Chain Integration: Coordinating with suppliers to ensure a steady flow of high-quality materials and mitigate risks of shortages.
- Process Monitoring: Employing real-time data analytics to track material usage patterns and adjust inventory accordingly.
By honing in on material selection and management with a strategic mindset, manufacturers can bolster their SLS workflows. This focus not only enhances the quality of the final products but also aligns with sustainable manufacturing practices, setting a benchmark for industry excellence.
3. Enhancing Print Efficiency
Boosting print efficiency in SLS production involves the strategic integration of cutting-edge machinery and process automation. Contemporary SLS equipment features advanced capabilities that drive productivity and consistency, essential for high-volume production. By selecting machines equipped with innovative functionalities like enhanced thermal regulation and refined laser precision, manufacturers can achieve superior part quality with reduced production cycles.
Harnessing Next-Generation SLS Machinery
State-of-the-art SLS machines now incorporate sophisticated temperature control systems, which are pivotal for maintaining uniform thermal conditions throughout the build. This consistency prevents material distortion and ensures precise layer bonding. Reliable repeatability in machine operations enhances output quality by reducing variations between builds.
Notable technological innovations include:
- Advanced Temperature Control: Ensuring stable thermal conditions to improve layer bonding and reduce defects.
- Enhanced Laser Precision: Utilizing high-fidelity laser systems for accurate layer tracing and optimal sintering.
- Integrated Monitoring Systems: Using built-in sensors to continuously track build parameters and immediately address any anomalies.
Automation and Strategic Layout Optimization
Automating part placement within the SLS printer's build chamber plays a critical role in optimizing print efficiency. By refining the layout of components, manufacturers can fully utilize the build volume, leading to increased production capacity per cycle. Intelligent software tools can assist in configuring the optimal arrangement, taking into account factors such as part orientation and thermal distribution to enhance energy efficiency and cooling.
Optimal practices for layout configuration:
- Efficient Part Arrangement: Structuring parts to minimize the need for supports and maximize space utilization.
- Orientation Optimization: Adjusting part positioning to reduce print duration and enhance structural performance.
- Balanced Loading: Distributing parts evenly to promote uniform thermal conditions and minimize stress concentrations.
By focusing on these components, manufacturers can significantly enhance the SLS printing process. Embracing these advancements not only elevates productivity but also strengthens overall operational effectiveness, enabling scalable manufacturing solutions that cater to the evolving demands of diverse industries.
4. Post-Processing Enhancement
Enhancing the post-processing phase in SLS production requires a focus on refining the transition from raw prints to market-ready products. Leveraging automated technologies can revolutionize traditionally labor-intensive tasks such as cleaning and surface refinement. These systems not only minimize human error but also ensure uniformity and precision across large production volumes.
Automated Powder Removal Solutions
Adopting automated powder removal solutions is crucial for efficiently cleaning parts with complex geometries. These systems utilize precise airflows and specialized tools to ensure thorough cleaning without compromising delicate features. Consistency in this process ensures each component meets cleanliness standards, facilitating seamless advancement to final refinement stages.
Advantages of automated powder removal:
- Delicate Handling: Protects intricate features while achieving thorough cleaning.
- Uniform Standards: Ensures consistency across large production batches, maintaining high quality.
- Operational Efficiency: Frees up skilled labor for more complex tasks, optimizing workforce utilization.
Innovative Surface Polishing Methods
Surface polishing is a pivotal post-processing step, influencing both the visual appeal and functionality of SLS parts. Techniques like precision polishing and advanced media treatments play a key role in achieving desired surface characteristics. Precision polishing, for instance, uses controlled abrasive techniques to create smooth textures and enhance part performance without altering structural integrity.
Key polishing methods include:
- Precision Polishing: Utilizes fine abrasives for high-quality surface finishes, enhancing both appearance and functionality.
- Advanced Media Treatments: Implements state-of-the-art techniques to refine surface quality and improve part robustness.
- Consistent Texture Development: Ensures uniform surface characteristics, critical for applications demanding high aesthetic standards.
By focusing on post-processing enhancements, manufacturers can dramatically improve the final quality of their SLS-produced components. These advancements not only align with rigorous industry standards but also open new opportunities for application across diverse markets.
5. Cost Analysis and Workflow Adjustments
In the realm of SLS production, maintaining a keen eye on cost efficiency is vital for sustaining operations and enhancing profitability. By systematically reviewing production metrics, manufacturers can unveil inefficiencies and devise strategies to optimize expenditures. This careful examination not only highlights resource overuse but also uncovers opportunities for cost savings, strengthening financial performance.
Strategic Cost Management
A thorough analysis of financial metrics involves dissecting various facets of the production workflow to evaluate their economic contributions. Key areas for scrutiny include material utilization efficiency, operational energy demands, and workforce deployment. By assessing these components, manufacturers can identify costly inefficiencies and develop targeted interventions.
Essential evaluation areas include:
- Material Utilization: Assessing how effectively materials are used to minimize waste and ensure maximum yield.
- Energy Use: Tracking energy consumption throughout the production process to explore reduction opportunities.
- Labor Optimization: Reviewing labor assignments to ensure efficient use of human resources and assess automation potential.
Implementing Targeted Adjustments
Insights gained from cost analysis pave the way for strategic modifications in production workflows. Such adjustments may encompass revising production timelines, integrating advanced technologies, or refining material handling processes. The focus should remain on boosting operational flexibility and reducing cycle times.
Adjustment strategies include:
- Schedule Refinement: Aligning production timelines with demand trends to optimize machine usage and reduce idle times.
- Technological Advancements: Employing state-of-the-art technologies to streamline processes and minimize manual tasks.
- Material Flow Improvements: Enhancing material handling procedures to increase throughput and decrease processing times.
By emphasizing cost management and workflow refinement, manufacturers can elevate their financial outcomes while sustaining high production quality. This forward-thinking approach not only secures profitability but also enables businesses to seize new opportunities in the competitive additive manufacturing landscape.
Tips on Optimizing SLS Production
To achieve peak performance in SLS production, it is crucial to focus on refining processes and fostering innovation. These strategies enhance production outcomes and ensure adaptability to evolving industry needs.
1. Enhance Design for SLS
Unlocking the full potential of SLS technology involves designing parts that capitalize on its unique attributes. By embracing the freedom to create intricate geometries, manufacturers can innovate with complex structures and reduce component weight. This approach not only enhances functionality but also streamlines the manufacturing process by minimizing material use.
Key design strategies include:
- Complex Structural Integration: Developing intricate internal features that maximize strength while minimizing weight, ideal for sectors like aerospace.
- Efficiency in Part Consolidation: Merging multiple components into singular, cohesive units to simplify assembly and improve durability.
- Advanced Functional Elements: Incorporating novel features that leverage SLS's ability to produce detailed, high-precision parts.
2. Foster a Culture of Innovation
Cultivating an atmosphere of innovation is vital for maintaining a competitive edge in SLS production. By continuously evaluating production methods and embracing cutting-edge advancements, manufacturers can remain agile. This proactive stance ensures that operations not only keep pace with technological progress but also anticipate market shifts and customer expectations.
Innovation practices include:
- Strategic Process Adjustments: Implementing iterative assessments to refine workflows and enhance production efficiency.
- Adopting Emerging Technologies: Leveraging new tools and methodologies to streamline operations and elevate the quality of output.
- Comprehensive Feedback Systems: Establishing robust channels for feedback from both production teams and clients to inform ongoing improvements.
By implementing these strategies, manufacturers can harness the full capabilities of SLS technology. Through thoughtful design enhancements and a commitment to innovation, the scope for operational excellence and market leadership expands significantly.
As the additive manufacturing landscape continues to evolve, embracing innovative solutions and refining SLS production workflows will be essential for staying ahead of the curve. By leveraging advanced technologies, optimizing processes, and fostering a culture of continuous improvement, manufacturers can unlock new opportunities and drive success in this dynamic industry. If you're ready to take your SLS production to the next level, schedule a demo or try the platform to experience how we can help you streamline your workflows and achieve your manufacturing goals.