Implementing Effective SLS Quality Control Measures
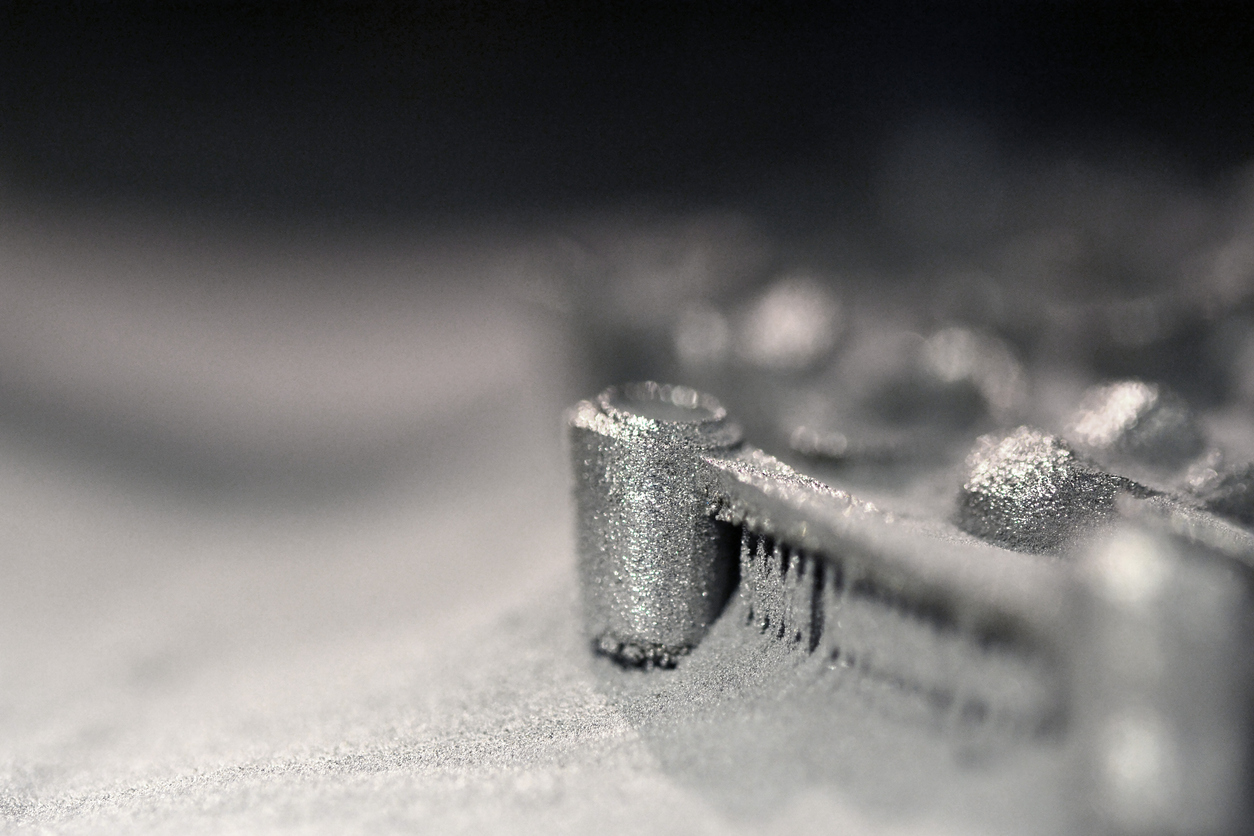
Selective Laser Sintering (SLS) has revolutionized the manufacturing landscape, enabling the production of complex parts with unparalleled precision. However, as with any advanced technology, ensuring consistent quality remains a critical challenge.
Effective quality control measures are essential to maximize the potential of SLS and deliver parts that meet the highest standards of accuracy, strength, and reliability. Implementing robust SLS quality control processes not only optimizes production workflows but also enhances customer satisfaction and builds a competitive edge in the market.
In this article, we will delve into the key aspects of SLS quality control, exploring best practices, common challenges, and strategies to ensure the production of superior parts. By understanding and implementing these measures, manufacturers can unlock the full potential of SLS technology and drive their businesses forward.
What is SLS Quality Control?
Selective Laser Sintering (SLS) is an additive manufacturing technology that uses a laser to sinter powdered material, binding it together to create a solid structure. Quality control in SLS is crucial to ensure the mechanical properties, dimensional accuracy, and surface finish of the final product meet the desired specifications.
The key aspects of SLS quality control encompass:
Material Quality
- Powder Characteristics: The quality of the powder used in SLS significantly impacts the final product. Key characteristics include particle size distribution, shape, flowability, and material composition.
- Reusability: SLS often involves reusing unsintered powder, which can degrade over time. Monitoring powder quality is essential to maintain consistency in part quality.
Process Parameters
- Laser Power and Scan Speed: These parameters must be precisely controlled to ensure proper sintering without excessive melting, which can lead to defects.
- Layer Thickness: Consistent layer thickness is critical for building accurate parts. Variations can cause warping, weak layers, and poor surface finish.
- Temperature Control: Maintaining optimal build chamber temperatures helps prevent thermal distortion and improves layer adhesion.
In-Process Monitoring
- Real-Time Monitoring: Implementing sensors and cameras to monitor the build process can help detect anomalies early, allowing for corrective actions.
- Advanced Techniques: Methods such as thermal imaging and optical tomography are used to assess layer quality and detect defects like porosity or incomplete fusion.
Post-Process Inspection
- Dimensional Accuracy: Parts are inspected for dimensional accuracy using tools like calipers, coordinate measuring machines (CMMs), and laser scanners.
- Surface Finish: Surface quality is assessed through visual inspection or using surface roughness measurement tools.
- Mechanical Testing: Parts undergo mechanical testing to ensure they meet strength and durability requirements. Common tests include tensile, compression, and impact testing.
Effective SLS quality control requires a comprehensive approach that addresses material quality, process parameters, in-process monitoring, and post-process inspection. By implementing robust quality control measures at each stage of the SLS process, manufacturers can consistently produce high-quality parts that meet customer expectations and industry standards.
Implementing robust quality control measures in Selective Laser Sintering (SLS) manufacturing plays a pivotal role in securing the reliability and performance of produced components. Grasping the significance of these measures involves recognizing the integration of advanced monitoring technologies and stringent process controls. This understanding directly influences the quality assurance framework, enhancing production efficiency, and ensuring product uniformity.
SLS manufacturing poses distinctive challenges due to the inherent complexity of the process and variability in material characteristics. Challenges often arise from maintaining optimal thermal management and ensuring uniformity in powder distribution. These factors are crucial in maintaining the structural integrity and precision of the parts. Deficiencies in quality assurance can lead to issues such as uneven material fusion and suboptimal surface finishes, undermining the functional and aesthetic attributes of the final product.
To establish a robust quality assurance system in SLS, several critical steps should be incorporated. First, setting well-defined quality benchmarks is crucial. This involves developing tailored performance metrics specific to SLS operations and using industry standards as a reference for part validation. Ensuring uniformity in material properties and production processes minimizes the risk of defects.
Monitoring SLS process parameters is another vital element. Identifying critical variables such as energy input, scanning patterns, and environmental conditions helps in reducing inconsistencies. Real-time monitoring technologies provide continuous oversight of production parameters, enabling prompt adjustments. Feedback mechanisms are essential for refining the SLS process, allowing manufacturers to leverage data-driven strategies for process enhancement.
Finally, conducting comprehensive inspections and evaluations of incoming materials is essential for maintaining material quality control. Utilizing cutting-edge techniques enhances precision in material assessments. Establishing material traceability systems aids in the early identification and resolution of potential issues. By embedding these comprehensive quality control strategies, manufacturers can uphold a superior standard in SLS production, delivering parts that consistently meet high customer expectations and industry benchmarks.
Step 1: Establishing Quality Standards
Creating robust quality benchmarks in Selective Laser Sintering (SLS) manufacturing is fundamental to ensuring that components meet design and functional specifications. By developing comprehensive technology criteria and performance indicators, manufacturers can align production with desired outcomes. These benchmarks should cover every stage of the SLS process, from initial material selection to final part examination, offering a detailed roadmap for both production and quality evaluation.
Industry standards play a pivotal role in part validation and quality assurance. By incorporating these standards, manufacturers can ensure their components adhere to widely accepted quality levels, thereby maintaining competitive quality within the market. Standards provide a framework for continuous improvement, highlighting areas that may require refinement. Aligning manufacturing processes with these established norms not only validates quality control efforts but also ensures adherence to customer and regulatory expectations.
Ensuring uniformity in materials and production techniques is crucial to achieving consistent quality in SLS parts. This uniformity guarantees that variations in material characteristics—such as particle shape and distribution—do not compromise part integrity. Implementing rigorous oversight of material handling and process variables minimizes defects and enhances product reliability. Consistency in these areas is vital to producing parts that consistently exhibit high quality, reinforcing a manufacturer's reputation for reliability and excellence in SLS technology.
Step 2: Monitoring SLS Process Parameters
Navigating the complex landscape of Selective Laser Sintering (SLS) necessitates a focused approach to process parameters, pivotal for achieving parts that meet rigorous standards. In-depth understanding and control of aspects such as energy application and material deposition patterns are essential. These factors significantly influence the structural integrity and dimensional accuracy of the components, making their precise management a cornerstone of successful SLS production.
Key to refining SLS part quality is the identification and calibration of critical process variables. Elements like thermal exposure, powder bed consistency, and build orientation are crucial in shaping the final product's properties. By concentrating efforts on these areas, manufacturers minimize variability and enhance the reliability of their output. This targeted control allows for the fine-tuning required to produce parts with high fidelity and minimal defects.
To maintain optimal oversight, employing integrated monitoring technologies becomes imperative. Advanced data acquisition systems capture real-time production metrics, facilitating instant adjustments to maintain consistency. Through intelligent feedback mechanisms, the system autonomously adapts to maintain optimal conditions, ensuring that each layer adheres to the intended specifications. This proactive management of the SLS environment not only streamlines operations but also assures a high standard of product quality.
Step 3: Conducting Regular SLS Material Quality Control
Ensuring the consistency of materials in Selective Laser Sintering (SLS) is pivotal for the precision and reliability of manufactured parts. A diligent approach involves systematically assessing the incoming materials to verify their compliance with stringent quality criteria. This entails a comprehensive evaluation of material properties—such as purity and thermal behavior—to ensure they align with the demands of the SLS process. Conducting these inspections systematically helps preemptively address potential issues that could affect the final product's integrity.
Utilizing cutting-edge verification techniques enhances the accuracy of material assessments. These methods provide deeper insights into the material's performance characteristics, enabling manufacturers to tailor the sintering process for optimal results. By incorporating these advanced methodologies, manufacturers can refine their understanding of how materials interact with process variables, thereby enhancing the overall quality of the output. This approach bolsters the efficiency of production by minimizing errors related to material inconsistencies.
Implementing comprehensive traceability systems is essential to uphold the integrity of SLS operations. These systems meticulously document the material's journey from acquisition through production, creating a transparent and accountable workflow. This detailed record-keeping allows for swift identification and resolution of any material-related issues, facilitating quick corrective actions. Such robust traceability measures ensure that each step of material handling aligns with the overarching quality objectives, reinforcing the reliability of the SLS manufacturing process.
Step 4: Analyzing and Addressing SLS Production Challenges
Overcoming challenges in Selective Laser Sintering (SLS) demands a methodical approach to diagnosing and resolving production inefficiencies. Conducting a comprehensive analysis of defects is crucial to uncovering the root causes of issues like warping, porosity, or other inconsistencies. By leveraging diagnostic technologies, manufacturers can isolate the variables contributing to these problems, enabling targeted interventions that refine the production process.
A structured approach to defect analysis integrates a thorough review of operational data and process dynamics. This involves evaluating process parameters, powder behavior, and control settings to identify connections with observed defects. Employing data analytics and machine learning provides a sophisticated framework for pinpointing patterns and irregularities, facilitating the discovery of recurring problems. This nuanced understanding empowers manufacturers to devise specific strategies to address these defects, enhancing overall product quality and reducing inefficiencies.
Implementing effective corrective action plans is integral to eliminating root causes and preventing future occurrences. These plans should be meticulously drafted based on insights from the defect analysis and customized to the unique characteristics of the SLS process. Essential elements of a robust corrective action plan include:
- Problem Diagnosis: Accurately diagnosing the core issue ensures that corrective measures address the correct aspects. This phase often requires interdisciplinary collaboration, drawing insights from quality assurance, engineering, and materials science to form a comprehensive perspective on the defect.
- Strategic Solutions: Developing solutions necessitates a creative approach, focusing on both procedural adjustments and technological innovations. Solutions might involve recalibrating process settings, enhancing material consistency checks, or deploying advanced monitoring systems to preempt defects.
- Execution and Evaluation: Executing corrective measures involves strategic planning and implementation. Continuous evaluation is key to assessing the efficacy of these solutions and making necessary refinements. Feedback mechanisms and performance indicators are vital for maintaining oversight and ensuring ongoing improvements in the SLS workflow.
Incorporating these corrective strategies into production workflows is essential for efficient problem-solving and minimizing operational interruptions. This integration necessitates aligning organizational practices with quality goals, ensuring all team members are informed and compliant with updated protocols. By embedding quality-focused practices into the core of the production process, manufacturers can cultivate a proactive environment that prioritizes defect prevention, leading to more productive and dependable SLS operations.
Step 5: Continuous Improvement and Training
Incorporating a framework of continuous improvement within Selective Laser Sintering (SLS) operations ensures sustained process excellence and adaptability to new challenges. Encouraging a mindset that prioritizes iterative enhancement allows organizations to respond dynamically to technological shifts and evolving production demands. This approach fosters an environment where innovation and proactive refinement are integral to operational success.
Targeted training initiatives are vital in ensuring staff are proficient in contemporary SLS quality assurance techniques and methodologies. These programs should offer both foundational education and advanced skill-building to keep personnel abreast of the latest industry advancements. By cultivating a culture of ongoing learning and development, organizations empower their teams to harness cutting-edge technologies and industry best practices, thereby optimizing production efficiency.
Leveraging data analytics is crucial for refining SLS quality metrics and driving process improvements. By employing comprehensive data analysis, organizations can identify trends and insights that guide strategic improvements. This analytical approach enables precise identification of inefficiencies and supports the implementation of data-informed enhancements, ensuring that manufacturing processes are consistently aligned with high-quality output standards.
Tips on Ensuring SLS Quality Control
1. Leverage Technology
Integrating cutting-edge digital solutions into SLS workflows can revolutionize quality assurance practices. Advanced imaging systems and machine learning algorithms provide deeper insights into the sintering process, allowing for precise control over production variables. By deploying these technologies, manufacturers can achieve higher levels of accuracy and consistency, thereby reducing the likelihood of defects and enhancing overall product quality.
To further bolster quality control, employing condition monitoring tools can play a pivotal role in maintaining equipment performance. These systems continuously track the operational status of machinery, identifying subtle changes that might indicate potential issues. By acting on these insights, manufacturers can schedule timely maintenance and avoid unexpected disruptions. This proactive maintenance strategy not only ensures smooth operations but also extends the service life of critical components, fostering a more efficient production environment.
2. Collaborate with Industry Experts
Partnering with leading experts in the field provides access to the latest research and innovations in SLS quality control. These collaborations can introduce novel approaches and methodologies that enhance the robustness of quality assurance protocols. Experts can offer tailored advice on optimizing processes and adopting new technologies, contributing to a more refined and effective SLS operation.
Engagement in professional networks and technical symposiums encourages the sharing of best practices and success stories. These interactions facilitate a rich exchange of knowledge, enabling manufacturers to learn from the experiences of others and apply these lessons to their own practices. By actively participating in these industry circles, organizations can foster a culture of continuous learning and adaptation, ensuring they remain at the cutting edge of SLS technology and quality management.
Implementing effective SLS quality control measures is essential for manufacturers to consistently deliver high-quality parts that meet customer expectations and industry standards. By establishing robust quality standards, monitoring process parameters, conducting regular material quality control, analyzing production challenges, and fostering continuous improvement, manufacturers can unlock the full potential of SLS technology. If you're ready to streamline your manufacturing processes and enhance your quality control efforts, schedule a demo or try the platform to experience how we can help you achieve your goals.