Exploring the Future of Multi Jet Fusion
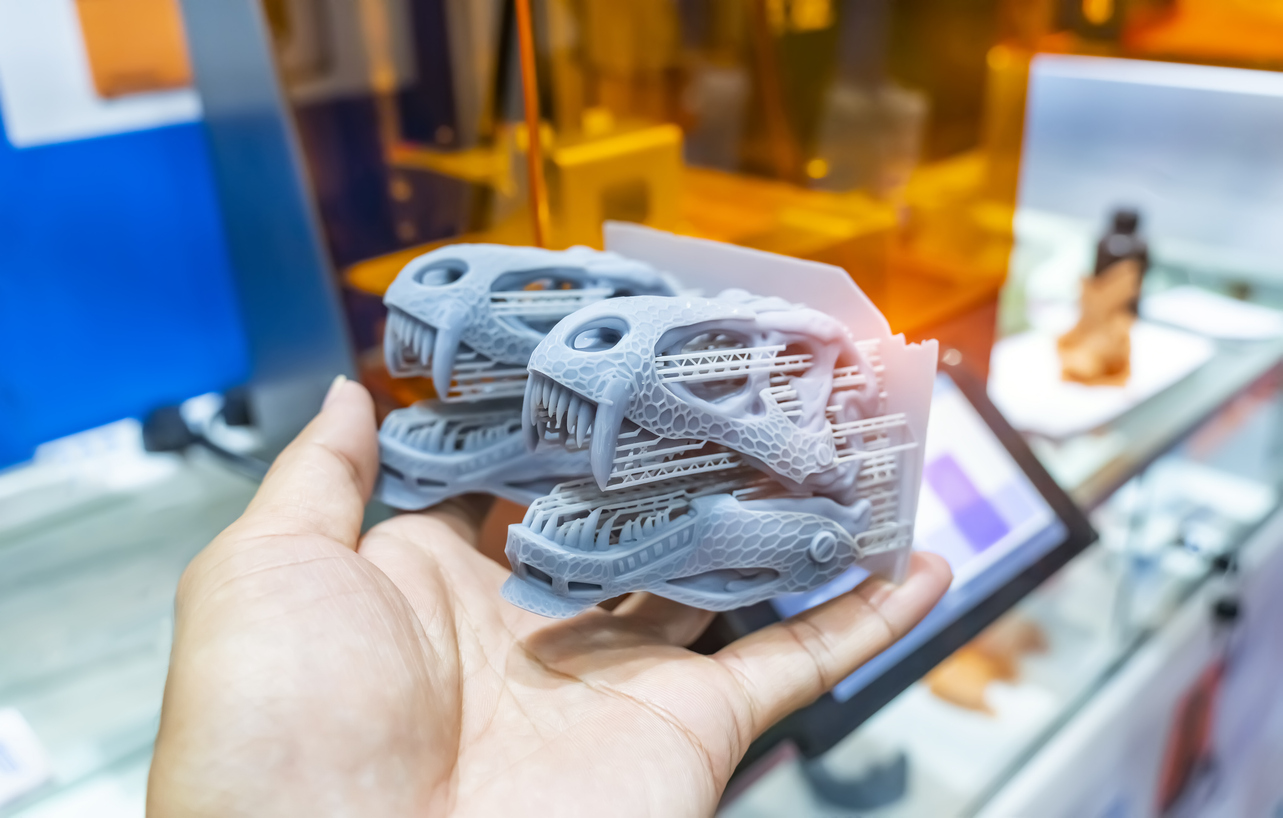
In the rapidly evolving world of additive manufacturing, new technologies are constantly pushing the boundaries of what's possible. One such groundbreaking innovation is Multi Jet Fusion (MJF), a 3D printing process that has garnered significant attention since its introduction by HP in 2016.
MJF has quickly become a go-to solution for businesses seeking to streamline their manufacturing processes and produce high-quality parts with unparalleled efficiency. Its ability to create functional prototypes and end-use components has made it an invaluable tool across various industries.
As manufacturers strive to stay competitive in an increasingly demanding market, understanding the capabilities and advantages of MJF is crucial. This article will delve into the intricacies of Multi Jet Fusion technology, exploring its unique features, benefits, and potential applications.
What is Multi Jet Fusion (MJF) Technology?
Multi Jet Fusion is a cutting-edge 3D printing process that enables the production of highly detailed and functional parts using powdered thermoplastic materials. Developed by HP, this technology builds objects layer by layer, creating complex geometries with consistent mechanical properties.
At the heart of the MJF process is an inkjet array that selectively deposits fusing and detailing agents onto a bed of powdered material. An infrared energy source then passes over the powder bed, fusing the areas where the agents have been applied. This process repeats until the entire part is complete, resulting in a solid object with intricate details and smooth surfaces.
One of the key advantages of MJF is its ability to produce parts with isotropic mechanical properties — meaning the strength and durability of the object are consistent in all directions. This makes MJF ideal for creating functional prototypes and end-use parts that can withstand the rigors of real-world applications.
Materials Used in MJF
HP's Multi Jet Fusion technology primarily uses a proprietary material called HP PA12, a strong and versatile nylon powder. This engineering-grade thermoplastic offers excellent mechanical properties, chemical resistance, and fine surface finishes. Parts printed with HP PA12 can be water-dyed and are capable of being watertight.
In addition to PA12, MJF printers can also work with other materials, such as PA11 (for more ductile parts) and polypropylene (HP High Reusability PP). As the technology continues to evolve, HP is collaborating with partners through its Open Platform project to develop new materials that will expand the range of applications for MJF.
The MJF Printing Process
The MJF printing process begins with a computer-aided design (CAD) model, which is processed using HP's proprietary software. Once the model is ready, the machine operator loads the powdered material into the build chamber.
A powder recoater spreads a thin layer of powder onto the build plate, and the printer's inkjet heads begin printing the first layer by selectively jetting the fusing and detailing agents. The fusing agent acts as a binding material, while the detailing agent enhances the resolution of the part's edges.
After the agents are deposited, a heat lamp solidifies and fuses the areas where they are present. The build plate then descends slightly, allowing the powder recoater to spread another thin layer of powder onto the previous layer. This process continues until all layers of the part are complete.
Once the printing is finished, the parts are taken to a post-processing station for cleaning. The unused powder can be recycled for subsequent builds — a significant advantage over other 3D printing technologies like selective laser sintering (SLS), which typically has lower recycling rates. Finally, the parts undergo bead blasting to improve surface quality and remove any remaining powder.
Benefits and Applications of MJF
The innovative Multi Jet Fusion technology distinguishes itself by delivering parts with consistently robust mechanical properties. This uniformity ensures that components remain reliable and effective for various uses, making it an ideal option for precision-driven applications. Such consistency is particularly beneficial in industries that demand high-performance parts, including automotive, aerospace, and medical sectors.
MJF technology excels with its rapid production speeds, setting it apart from other 3D printing techniques like Fused Deposition Modeling (FDM) and Stereolithography (SLA). This acceleration in manufacturing enables companies to shorten their development cycles and bring products to market more swiftly. With faster iteration capabilities, manufacturers can adapt quickly to evolving market needs without sacrificing quality.
Applications Across Industries
- Automotive and Aerospace: MJF is crucial for producing intricate and weight-efficient components such as engine casings and ventilation systems. Its precision and strength suit the demanding conditions in these fields.
- Medical: The customization potential of MJF provides significant advantages for creating patient-specific prosthetics and orthotic devices, enhancing both comfort and function.
- Consumer Electronics and Robotics: For intricate and detailed designs, such as tailored drone components, MJF delivers high-resolution outputs efficiently, eliminating the need for additional support structure removal.
The ability of MJF to create complex geometries without the necessity of support structures broadens its application potential. This flexibility empowers designers to innovate freely, crafting parts with complex internal features that would be difficult to achieve with other manufacturing methods. Consequently, MJF is the preferred technology for producing components that demand both complexity and precision.
Advantages of MJF Over Other 3D Printing Technologies
MJF technology excels by offering unparalleled production efficiency. Unlike traditional 3D printing methods, it applies multiple agents across the entire build platform simultaneously. This approach significantly reduces production times, allowing manufacturers to keep pace with dynamic market requirements. The streamlined process in MJF enhances throughput, making it an ideal choice for high-demand scenarios.
A notable strength of MJF is its material utilization efficiency. The process optimizes the use of powder, enabling up to 80% of unfused material to be reclaimed and reused in subsequent builds. This high recycling rate not only curtails waste but also provides cost benefits by decreasing the need for fresh materials. In comparison, other technologies like SLS typically have lower reclaiming efficiencies, which can lead to increased material costs over time.
Precision and Uniformity
MJF provides exceptional precision and uniformity in part production. The technology ensures that each piece exhibits consistent mechanical attributes, a critical requirement for applications that demand reliability and durability. By delivering precise detail in complex parts, MJF opens new avenues for innovation, allowing designers to push the boundaries of what is manufacturable. The fine resolution achieved without the need for additional support structures further enhances the flexibility and creativity in engineering design.
The Future Outlook for MJF Technology
The path forward for Multi Jet Fusion (MJF) technology looks promising, with significant advancements aimed at enhancing both its affordability and functionality. HP's initiative to introduce cost-effective MJF models aims to broaden the accessibility of this technology, enabling a diverse array of businesses to harness its capabilities. By lowering the financial barriers, HP facilitates a more inclusive environment where enterprises of all sizes can integrate MJF into their operations, fostering widespread innovation within the manufacturing sector.
Emerging developments in MJF include the integration of full-color printing capabilities, which could revolutionize the production of detailed and vibrant components. This advancement stands to benefit industries where aesthetic appeal is paramount, such as consumer goods and design-focused sectors. The ability to produce full-color parts may inspire new levels of creativity and innovation, offering manufacturers and designers a richer toolkit for prototyping and production.
Expanding Material Choices and Collaborative Innovation
HP's collaborations with leading material developers signal a commitment to broadening the material spectrum available for MJF technology. These partnerships are instrumental in driving the introduction of new materials, enhancing the versatility and adaptability of MJF. By expanding material options, HP positions MJF as a versatile solution capable of meeting diverse manufacturing needs across various industries.
As material innovation continues, manufacturers will have the opportunity to explore novel applications, integrating MJF more deeply into their production strategies. These collaborative efforts also ensure that MJF technology remains responsive to shifting market demands, maintaining its relevance and competitiveness. Additionally, the potential for other companies to develop their own MJF variants could create a dynamic and competitive landscape, spurring further innovation and driving down costs, thus solidifying MJF's role as a leading force in the future of additive manufacturing.
Implementing MJF in Your Manufacturing Workflow
Integrating Multi Jet Fusion (MJF) technology into your manufacturing process requires a strategic approach to identify how this advanced 3D printing solution can enhance your operations. Start by pinpointing specific applications where traditional methods may be inefficient or limited—particularly those demanding complex geometries or rapid turnaround times. MJF's precision in producing detailed parts without the need for additional support structures makes it an excellent choice for intricate designs and components requiring internal features.
Evaluating Economic Viability
When considering MJF, it's crucial to conduct a thorough analysis of its economic impact in relation to your production requirements. Assess how MJF fits into your production strategy, especially for small to medium batch sizes where setup costs are minimized. Examine the potential cost benefits from reduced material consumption and expedited production processes. Balance these factors against existing manufacturing expenses to determine if MJF offers a cost-effective solution for your specific needs.
Engaging with Specialized Partners
Partnering with seasoned MJF service providers can significantly enhance your implementation strategy. These professionals bring a wealth of experience in adapting designs to leverage MJF's capabilities fully, ensuring parts are optimized for both performance and cost. They provide essential guidance in navigating material selections and refining design parameters to exploit MJF's strengths. By collaborating with these experts, you can streamline your manufacturing process, ensuring high-quality outcomes and efficient integration of MJF technology.
Understanding the intricacies of MJF—such as its material capabilities and design flexibility—demands close cooperation with your service provider. Together, you can tailor your designs to maximize the benefits of MJF, ensuring your transition is smooth and strategically sound. This collaboration fosters informed decision-making, leading to effective use of MJF in your manufacturing operations.
As the manufacturing landscape continues to evolve, embracing innovative technologies like Multi Jet Fusion will be essential for staying competitive and meeting the demands of the future. At Phasio, we are committed to helping manufacturers harness the power of MJF and other cutting-edge solutions to drive success. If you're ready to explore how you can revolutionize your MJF manufacturing workflow, schedule a demo or try the platform to experience its capabilities firsthand and let us guide you on your journey to a more efficient, profitable future.