What is MJF and Why It Matters in 3D Printing
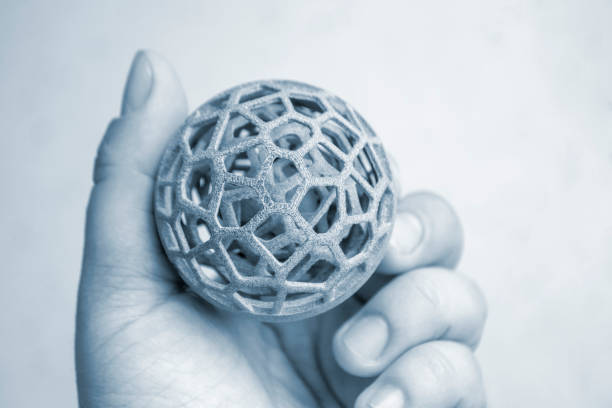
Multi Jet Fusion (MJF) has emerged as a game-changing technology in the world of additive manufacturing. This industrial 3D printing process, developed by HP, is revolutionizing the way functional parts are produced.
MJF offers unprecedented speed, accuracy, and repeatability, making it a top choice for rapid prototyping and low-volume production. Its ability to print hundreds of parts in a single build has caught the attention of industries ranging from automotive to healthcare.
As the demand for customized and sustainably manufactured products grows, MJF is poised to play a significant role in shaping the future of manufacturing. In this article, we'll dive deep into the intricacies of MJF technology, exploring its benefits, applications, and potential impact on supply chains and sustainability.
What is Multi Jet Fusion (MJF) Technology?
At its core, MJF is a powder-bed fusion process that uses inkjet arrays to selectively apply fusing and detailing agents across a bed of nylon powder. Infrared lamps then pass over the bed, fusing the areas where the agents were applied. This process is repeated layer by layer until the parts are complete.
One of the key advantages of MJF is its ability to produce parts with high dimensional accuracy and fine feature resolution. The technology is capable of printing features as small as 0.1mm, making it suitable for applications that require intricate geometries and precise tolerances.
MJF also boasts impressive build speeds, outpacing other 3D printing technologies like selective laser sintering (SLS) and fused deposition modeling (FDM). This speed advantage is due to the technology's ability to print multiple parts simultaneously, without the need for support structures. The result is faster turnaround times and lower production costs.
How MJF Compares to Other 3D Printing Technologies
When stacked up against other 3D printing technologies, MJF stands out in several key areas:
- Speed: MJF's build speeds are significantly faster than SLS and FDM, thanks to its ability to print multiple parts in a single build.
- Part quality: MJF produces more robust and durable parts compared to binder jetting and material jetting processes. It also offers better surface quality and finer feature resolution than SLS and FDM.
- Mechanical properties: Parts printed with MJF exhibit isotropic mechanical properties, meaning they have consistent strength in all directions. In contrast, FDM parts are anisotropic, with varying strength depending on the direction of the print.
These advantages have made MJF a popular choice for applications that require high-quality parts with quick turnaround times. Industries such as automotive, consumer goods, and healthcare are increasingly turning to MJF to accelerate their product development cycles and enable on-demand manufacturing.
Benefits and Applications of MJF 3D Printing
MJF technology introduces a significant shift in how manufacturers approach their production processes. One of its standout advantages lies in its ability to streamline workflows by reducing the time traditionally required for design validation and prototyping. This attribute is invaluable for industries where agility and adaptability are key to staying ahead.
The technology's contribution to on-demand manufacturing extends beyond just speed. It enables manufacturers to operate with a lean inventory, minimizing excess stock and lowering associated costs. This adaptability aligns with the push for more sustainable production practices, as it allows for production tailored to immediate demand without overproduction.
MJF's capability for tailored production is particularly transformative. It allows manufacturers to efficiently produce unique and complex parts within a single build cycle. This capacity to cater to individual specifications is particularly advantageous in sectors aiming to deliver personalized solutions, enhancing product differentiation and customer satisfaction.
Industries Adopting MJF Technology
The automotive and transportation sectors are leveraging MJF's capabilities to enhance their product design and manufacturing processes. The technology's precision and ability to create intricate components support these industries' efforts to innovate while maintaining high-quality standards. This innovation is critical in staying competitive in a rapidly evolving market.
In the healthcare industry, MJF plays a crucial role in developing patient-specific models and devices. The precision and customization offered by this technology enable healthcare providers to improve the accuracy and effectiveness of medical interventions. Meanwhile, the consumer goods sector is utilizing MJF to create unique, personalized experiences for consumers, driving engagement and loyalty through bespoke products. These applications highlight MJF's versatility and its ability to meet the diverse needs of various industries.
Materials and Post-Processing for MJF Parts
The versatility of Multi Jet Fusion technology extends to the diverse materials it supports, each contributing unique characteristics to the final parts. Nylon 12 remains a prevalent choice due to its robust combination of durability and chemical resistance, making it suitable for various applications where consistent performance is necessary. This material's adaptability allows manufacturers to address needs across multiple sectors effectively.
In scenarios demanding greater flexibility and impact resilience, Nylon 11 serves as an optimal alternative. Its improved ductility ensures that parts can withstand more rigorous conditions without sacrificing structural integrity. Additionally, Thermoplastic Polyurethane (TPU), with its elastic, rubber-like properties, is ideal for creating components that require flexibility and resilience, such as seals and gaskets.
The inclusion of materials like glass, aluminum, and carbon fiber reinforcements further enhances the mechanical attributes of MJF parts. These reinforcements are crucial for applications needing increased stiffness and thermal stability, demonstrating MJF's capability to cater to industries with stringent material requirements. This material diversity highlights MJF's potential to address specific industrial challenges.
Dyeing, Painting, and Finishing MJF Parts
Post-processing in MJF production plays a vital role in refining parts to meet desired specifications. Dyeing techniques enable the coloration of parts across a spectrum of colors, enhancing both functional and aesthetic qualities. This flexibility is particularly advantageous for consumer products, where visual appeal is a significant factor.
To achieve a high-quality finish, parts can undergo sealing and painting processes, which not only improve appearance but also add protective layers against environmental influences. For applications where surface smoothness is crucial, techniques such as media blasting, sanding, and polishing are employed. These steps ensure that each part meets precise standards for integration into complex assemblies, underscoring MJF's ability to produce finely finished, ready-to-use components.
Designing for MJF 3D Printing Success
Creating successful designs for Multi Jet Fusion (MJF) demands a meticulous approach, ensuring each element is crafted for both efficiency and performance. One key tactic is merging multiple components into a singular, cohesive design. This reduces assembly complexity and minimizes potential points of failure, thereby bolstering the dependability of the final product. By integrating various elements, manufacturers can achieve both operational efficiencies and enhanced product robustness.
Strategically managing material usage is another crucial aspect of MJF design. By utilizing advanced geometric configurations such as lattice structures, designers can significantly reduce material requirements while maintaining structural integrity. This approach not only curtails costs but also aligns with modern sustainability objectives, promoting resource-efficient production. Additionally, optimizing the design's topology can improve the balance between strength and weight, which is particularly advantageous in sectors where reducing mass is a priority, like aerospace and automotive.
Design Guidelines and Considerations
When designing for MJF, adhering to precise guidelines is essential for achieving optimal results. For instance, ensuring a minimum wall thickness of 0.3mm for rigid parts and 0.5mm for flexible ones helps prevent structural weaknesses. These parameters are critical for delivering the necessary durability and functionality, especially in demanding applications.
Detailing in MJF requires a high degree of precision; maintaining a minimum feature size of 0.1mm for intricate designs ensures that even the most complex geometries can be accurately reproduced. This capability allows for the creation of parts with detailed functionalities and aesthetic qualities. Furthermore, adhering to the maximum part size—380 x 285 x 380 mm (15 x 11.2 x 15 in)—keeps designs within the practical build limits of MJF printers.
Part orientation is a vital consideration, significantly impacting the need for support structures and the quality of the surface finish. By carefully planning the orientation during the design phase, manufacturers can minimize post-processing efforts, conserving both time and materials. This strategic approach not only streamlines the production process but also enhances the uniformity and quality of the end product.
The Future of MJF in Additive Manufacturing
As Multi Jet Fusion (MJF) technology progresses, material advancements will significantly broaden its reach across diverse industries. With the introduction of new materials, MJF can cater to sectors requiring unique properties, such as enhanced thermal resistance or superior mechanical performance. These developments will empower manufacturers to explore innovative applications, addressing complex industrial challenges with efficiency and precision.
Enhancements in processing capabilities will further cement MJF's role in large-scale production environments. As processing speeds increase, manufacturers can scale their operations more effectively, maintaining product quality while reducing lead times. This evolution supports industries that depend on rapid iteration and market responsiveness, maintaining their competitive edge in dynamic markets.
Potential Impact on Supply Chains and Sustainability
The automation of post-processing and finishing stages through MJF integration represents a leap towards streamlined and efficient production workflows. By reducing reliance on manual interventions, manufacturers can achieve higher consistency and lower operational costs. This shift aligns with the industry's move towards sustainability, optimizing energy use and minimizing waste.
MJF's contribution to producing digital spare parts and eco-friendly products is becoming increasingly pivotal. With its capability for on-demand manufacturing, MJF reduces dependency on extensive logistics networks, as production can occur closer to the point of need. This localized approach not only lowers emissions but also mitigates the risks of overproduction. By aligning production closely with demand, industries can minimize surplus inventory and its associated waste.
In the realm of environmental responsibility, MJF sets a benchmark by significantly reducing material waste compared to traditional manufacturing methods. The technology's support for recyclable thermoplastics and innovations in powder reuse further enhance its sustainability profile. As industries prioritize environmental stewardship, MJF's ability to deliver efficient, resource-conscious solutions positions it at the forefront of future manufacturing strategies.
As MJF continues to shape the landscape of additive manufacturing, its impact on industries, supply chains, and sustainability is undeniable. We are excited to be at the forefront of this transformative technology, empowering manufacturers to innovate, optimize, and thrive in the digital age. If you're ready to revolutionize your production processes with MJF, schedule a demo or try the platform to experience its capabilities firsthand and see how we can help you achieve your manufacturing goals.