What Is SLS in the Context of Additive Manufacturing?
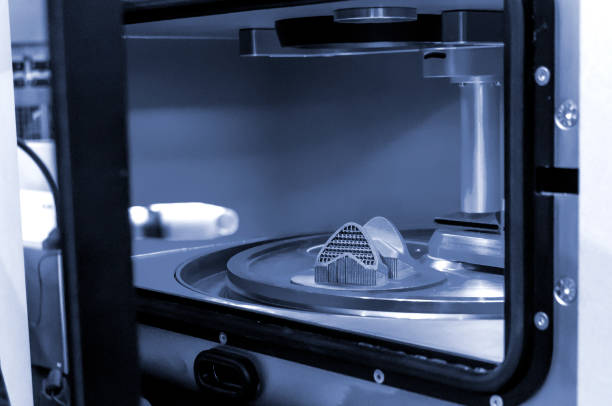
Selective Laser Sintering (SLS) has emerged as a game-changing technology in the world of additive manufacturing. It has opened up new possibilities for creating complex, functional parts with unparalleled design freedom.
SLS is an additive manufacturing process that utilizes a high-powered laser to selectively sinter powdered materials, fusing them together layer by layer to create solid 3D objects. This technology has found applications across various industries, from aerospace and automotive to medical and consumer goods.
In this article, we will dive deep into the world of SLS, exploring its definition, process, advantages, and applications. We will also discuss how to optimize SLS production workflows, implement quality control measures, and validate parts for end-use.
Definition of Selective Laser Sintering (SLS)
Selective Laser Sintering is a powder-based additive manufacturing technology that uses a laser to sinter powdered materials into solid 3D objects. The term "sintering" refers to the process of heating a powdered material to a temperature just below its melting point, causing the particles to fuse together and form a solid mass.
SLS is capable of processing a wide range of materials, including plastics, metals, and ceramics. Some of the most commonly used materials in SLS include:
- Nylon: Known for its excellent mechanical properties, durability, and chemical resistance, nylon is a popular choice for functional prototypes and end-use parts.
- Polystyrene: This lightweight, cost-effective material is often used for creating concept models and visual prototypes.
- Metals: SLS can process a variety of metal powders, such as aluminum, steel, and titanium, enabling the production of high-strength, functional metal parts.
One of the key advantages of SLS is its ability to create complex geometries without the need for support structures. Unlike some other additive manufacturing technologies, SLS does not require the use of support material because the unsintered powder surrounding the part acts as a natural support. This allows for greater design freedom and the creation of intricate internal features that would be difficult or impossible to achieve with traditional manufacturing methods.
How the SLS Process Works
Initiating with a uniform spread of powdered material across the build platform, the SLS process starts by ensuring that each layer is consistently laid out for optimal results. This uniformity is crucial for maintaining the quality and precision of the final product. A laser then meticulously traces the design, using its energy to fuse the powdered material into a solid structure. This precision allows for the creation of intricate designs with exceptional accuracy.
As the laser completes a layer, the build platform descends slightly, allowing for a fresh layer of powder to be applied. This sequential layering forms the essence of additive manufacturing: each successive layer bonds seamlessly with the one below it, gradually constructing the complete object. This method requires careful control to maintain the desired accuracy and ensure the structural integrity of the finished piece.
A unique aspect of SLS is how it utilizes the surrounding powder throughout the printing process. This untouched material envelops the part, providing inherent support to complex overhangs and internal cavities. Upon completion, the excess powder is removed, unveiling the intricately detailed component without the need for additional supports, thus facilitating the creation of complex geometries effortlessly.
Advantages of SLS Technology
SLS offers an exceptional level of design adaptability, allowing for the production of parts that feature intricate details and sophisticated internal structures. This capability encourages designers to experiment with innovative concepts and optimize components for specific functions or performance criteria. The process naturally supports complex designs, as the surrounding powder acts as a support medium, eliminating the constraints typically imposed by traditional manufacturing methods.
Parts produced using SLS are characterized by impressive mechanical properties, which include high tensile strength and resilience. These attributes make SLS parts ideal for demanding applications where reliability is paramount. Industries such as medical and consumer goods benefit significantly from SLS's ability to produce robust and precise components that meet stringent functional requirements.
SLS technology excels in producing customized, low-volume parts and prototypes rapidly and efficiently. This efficiency significantly shortens the product development timeline, facilitating faster iterations and adjustments to designs. The versatility of SLS also comes from its compatibility with a diverse range of materials, from polymers to metals, enabling its application across various sectors. This flexibility ensures manufacturers can quickly adapt to changing market needs or customize products for niche applications.
Applications of SLS in Various Industries
In the aerospace sector, SLS technology is instrumental in fabricating components with intricate designs vital for modern aircraft and spacecraft. Its precision allows for the integration of complex internal structures that optimize performance and reduce weight. By utilizing advanced materials, such as high-performance polymers, SLS contributes to creating parts that withstand the harsh conditions of aerospace environments, enhancing both durability and efficiency.
The medical field capitalizes on SLS for crafting custom medical solutions, such as tailored implants, adaptive prosthetics, and precision surgical guides. This technology's ability to produce highly detailed and patient-specific devices ensures that medical professionals can deliver personalized care. The range of biocompatible materials available for SLS further supports the development of safe, effective medical devices tailored to individual patient needs.
In the automotive industry, SLS is pivotal for producing specialized prototypes and bespoke components. The technology enables manufacturers to experiment with innovative designs, accelerating the development of new models and features. Additionally, SLS allows for the creation of complex tooling that supports efficient manufacturing processes, ultimately contributing to more streamlined production and reduced time-to-market.
The consumer goods sector leverages SLS to offer uniquely personalized items, such as custom jewelry and bespoke eyewear. The flexibility of SLS enables the crafting of products with intricate details and personalized features, meeting the growing consumer demand for tailored goods. This customization capability not only enhances customer satisfaction but also positions brands to stand out in a competitive marketplace.
Refining SLS production processes demands a strategic approach to design parameters and the deployment of advanced technologies. Critical considerations include ensuring consistent wall thickness, precise feature dimensions, and optimal part orientation. Uniform wall thickness is crucial to avoid defects like warping, while feature size must be meticulously adjusted to maintain part strength without sacrificing detail. Orientation on the build platform influences surface quality and the stability of complex geometries, necessitating careful planning.
Enhancing the workflow from initial design through to final processing involves leveraging sophisticated software solutions. These tools assist in organizing part placement and orientation, minimizing potential build errors. Software for slicing efficiently converts 3D models into precise instructions for the machine, facilitating accurate laser paths. These digital resources, coupled with robust machine control systems, maintain essential parameters during production. This integration minimizes errors early in the process, facilitating a more efficient and successful manufacturing cycle.
To ensure excellence in final products, a comprehensive approach to the post-processing phase is essential, incorporating both automated checks and manual inspections. Automated systems swiftly detect any variances from design specifications, prompting additional review where necessary. Manual checks provide an additional layer of assurance, verifying that each part meets stringent quality standards. This dual approach enhances the consistency and reliability of SLS-produced parts, positioning manufacturers to excel in the competitive landscape of advanced manufacturing.
Quality Control in SLS Manufacturing
Ensuring superior quality in SLS manufacturing demands precise oversight of essential process variables. These include the calibration of laser intensity, regulation of scanning velocity, and control of individual layer height. Each parameter significantly influences the final product's accuracy and structural properties. The laser's intensity must be finely adjusted to achieve optimal fusion without causing material degradation, while scanning velocity affects the smoothness of layer transitions. Layer height plays a crucial role in determining the level of detail possible, necessitating careful adjustments to harmonize speed and precision.
Beyond initial settings, a comprehensive quality strategy is vital for consistent results across multiple production runs. Implementing sophisticated monitoring systems enables real-time tracking of these variables during the manufacturing process. These systems provide immediate feedback, allowing for adjustments that maintain consistency and prevent defects. Such proactive control mechanisms are essential for maintaining the reliability and repeatability of SLS production.
Post-production evaluations are critical to confirm that parts adhere to design specifications. Dimensional checks ensure components fit within specified tolerances, which is vital for parts destined for assembly or functional applications. Surface assessments evaluate the texture and finish, important for both aesthetic and functional requirements. These evaluations, combined with precision measurement tools, guarantee that SLS-manufactured parts meet the high standards necessary for their intended applications.
Validating SLS Parts for End-Use
Evaluating SLS-manufactured parts for end-use begins with a comprehensive suite of tests to confirm their mechanical properties. These evaluations focus on assessing the tensile strength, flexibility, and impact resistance of the components. Such rigorous testing is essential to ensure that parts are robust enough to withstand the operational demands they will face, whether it's in high-stress environments or under varying temperature conditions. Ensuring these properties are met is crucial for manufacturers aiming to deliver reliable and high-performance products.
Moving beyond basic property assessments, functionality and performance validation simulates real-world conditions to verify that parts operate as intended. This involves subjecting components to stress tests that replicate actual use scenarios, such as load-bearing tests or environmental exposure trials. By doing so, manufacturers can identify any potential weaknesses or performance issues that may arise during actual use, allowing for necessary adjustments before broader production and deployment.
Achieving compliance with industry-specific standards is the final step in the validation process, especially in fields with rigorous regulatory demands such as aerospace, medical, and automotive sectors. Obtaining the necessary certifications not only affirms the quality and safety of SLS parts but also facilitates their acceptance in the market. This compliance ensures that parts meet all relevant safety and legal requirements, providing assurance to end-users and enhancing the credibility of manufacturers in competitive industries.
Advancements and Future of SLS
The realm of Selective Laser Sintering is witnessing exciting transformations, particularly through the emergence of innovative materials that expand its capabilities and application potential. Recent breakthroughs in material science have introduced advanced polymers and hybrid composites that exhibit enhanced thermal stability and electrical properties. These developments widen the application horizons of SLS, allowing it to cater to industries with stringent material demands, such as electronics and high-performance automotive components.
The incorporation of artificial intelligence and machine learning into SLS technology is revolutionizing process control and efficiency. These technologies enable dynamic monitoring and precise adjustments during production, significantly reducing errors and optimizing resource use. Through AI, manufacturers can anticipate potential challenges and adjust parameters in real time, ensuring a high degree of accuracy and consistency. Machine learning models analyze extensive data sets to refine process parameters, leading to more efficient and fault-tolerant production cycles.
Selective Laser Sintering is increasingly being adopted for direct production of functional parts, embracing the trend of mass customization. This shift is propelled by SLS's ability to create tailor-made, high-quality components swiftly and cost-effectively. The growing consumer demand for bespoke products, such as custom-fit protective gear or personalized electronic housings, aligns perfectly with SLS's capability to innovate without the constraints of traditional manufacturing. This adaptability ensures SLS remains at the forefront of manufacturing innovation, ready to meet the evolving requirements of diverse markets.
As the landscape of additive manufacturing continues to evolve, SLS stands as a powerful technology that empowers businesses to innovate, customize, and deliver high-quality products efficiently. Its versatility, precision, and ability to process a wide range of materials make it an indispensable tool for industries seeking to push the boundaries of what's possible in manufacturing. If you're ready to explore how SLS can transform your manufacturing processes, schedule a demo or try the platform to experience its capabilities – we're here to help you unlock the full potential of this remarkable technology.