What You Need to Know About FDM Technology in Manufacturing
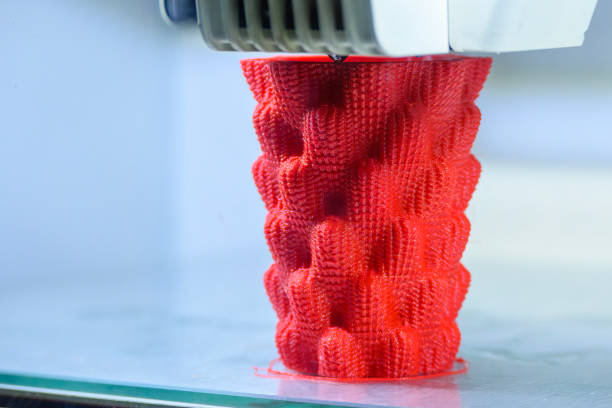
Fused Deposition Modeling (FDM) has emerged as a game-changing technology in the world of manufacturing. This innovative process is revolutionizing the way businesses approach prototyping and production.
FDM offers a cost-effective and efficient alternative to traditional manufacturing methods. By leveraging the power of additive manufacturing, companies can now create complex parts and products with ease.
In this article, we'll dive deep into the world of FDM technology. We'll explore its inner workings, benefits, and the myriad of applications it enables across various industries.
What is FDM Technology?
FDM, short for Fused Deposition Modeling, is an additive manufacturing process that builds objects layer by layer using extruded thermoplastic filament. Unlike subtractive manufacturing methods such as machining, which removes material to create an object, FDM adds material in successive layers until the desired shape is achieved.
One of the key advantages of FDM is its ability to create complex geometries and internal cavities that would be challenging or impossible with traditional manufacturing techniques. This is made possible by the use of soluble support material, which can be easily removed after the printing process is complete.
FDM technology offers a clean and office-friendly production environment, thanks to the use of durable and stable thermoplastics. These materials are mechanically and environmentally stable, ensuring that the final products are of high quality and can withstand various conditions.
Benefits of FDM in Manufacturing
- Cost-effectiveness: FDM significantly cuts production costs compared to conventional methods by eliminating the need for expensive tooling and reducing material waste.
- Faster lead times: With FDM, businesses can bring products to market faster by streamlining the prototyping and production processes.
- Material diversity: FDM offers a broad selection of materials, ranging from standard thermoplastics to engineering-grade and high-performance polymers, enabling a wide range of applications.
- Precision and reliability: FDM technology is trusted across industries for its ability to produce parts with high precision, reliability, and repeatability.
- User-friendly systems: FDM printers are available in various sizes, from desktop models to industrial-grade machines, making the technology accessible to businesses of all scales.
The versatility and cost-effectiveness of FDM make it an attractive option for manufacturers looking to optimize their operations. By integrating automated pricing and order management solutions, such as those offered by Phasio, businesses can further streamline their FDM workflow and boost efficiency.
FDM technology is transforming manufacturing across a wide range of industries — from aerospace and automotive to medical and consumer goods. As the technology continues to evolve, we can expect to see even more innovative applications and materials that push the boundaries of what's possible with additive manufacturing.
Advantages of FDM in Manufacturing
Fused Deposition Modeling (FDM) offers manufacturers a distinct advantage by enabling efficient production processes. By directly fabricating components from digital files, FDM reduces dependency on traditional tooling, streamlining the path from concept to creation. This capability not only accelerates the transition from design to finished product but also minimizes excess material use, providing an economical solution for both prototypes and full-scale manufacturing.
Material Versatility
FDM technology is compatible with a diverse range of materials, catering to various industrial requirements. From basic thermoplastics to advanced engineering resins, FDM supports the production of components with tailored properties, ensuring they meet specific functional needs. This versatility makes it possible to select materials based on the unique demands of each application, whether it requires flexibility, strength, or resistance to environmental factors.
- Thermoplastic Range: With materials spanning from PLA and ABS to advanced options like ULTEM and Nylon, manufacturers have the flexibility to choose based on mechanical needs.
- Innovative Composites: FDM systems can incorporate composite materials, such as carbon fiber-filled filaments, enhancing the strength-to-weight ratio of parts without compromising on performance.
Precision and Reliability
FDM's precision offers a reliable solution for industries that demand high accuracy and consistency. The process of layering materials allows for the creation of complex and detailed designs with precision, meeting stringent quality standards. This reliability is integral for sectors that require consistent, high-quality outputs from each production run.
- Accurate Output: The method's precision ensures that parts meet exact specifications consistently, essential for industries like aerospace and medical devices.
- Design Flexibility: FDM allows for the production of intricate designs that are challenging with traditional methods, fostering innovation and creative design solutions.
FDM's adaptability extends to its accessible systems, available in configurations that range from small-scale desktop models to large industrial units. This range makes the technology suitable for diverse manufacturing environments, from independent prototyping workshops to extensive production facilities. As such, FDM enhances operational efficiency and expands the possibilities for innovation in modern manufacturing.
FDM Workflow Efficiency
FDM technology excels by offering a cohesive and efficient production pathway, transforming digital designs into tangible products with remarkable ease. This method simplifies traditional manufacturing complexities, enabling rapid realization of designs while conserving both time and resources, thus boosting overall operational productivity.
Streamlined Process
The seamless integration of each stage within the FDM workflow minimizes the need for manual intervention. Advanced software tools ensure that digital models are faithfully rendered into physical objects, maintaining the integrity and precision of the original design. This streamlined transition from concept to completion enhances accuracy and reduces potential inefficiencies.
- Direct Model Translation: Utilizing sophisticated software, digital models are directly converted into three-dimensional objects, ensuring high precision and fidelity throughout the process.
- Enhanced Process Management: Integrating advanced management systems further refines the workflow by automating cost estimation and processing tasks, thereby reducing administrative overhead and expediting production timelines.
Reduced Post-Processing
A distinctive feature of FDM technology is its ability to minimize post-processing through the use of easily removable support structures. This capability significantly reduces manual labor, ensuring that complex parts emerge from the printer ready for immediate use or minimal finishing.
- Efficient Support Removal: The use of supports that dissolve quickly and cleanly streamlines the finishing process, allowing for intricate designs without extensive manual intervention.
- Complex Design Capabilities: With the ability to handle intricate geometries efficiently, FDM opens up new avenues for innovative designs that were previously challenging to manufacture.
Adopting FDM technology in manufacturing processes not only optimizes the production cycle but also leverages precision and efficiency to explore novel design possibilities and reduce overall production costs.
Industries Revolutionized by FDM
FDM technology has fundamentally altered the landscape of several key industries, each benefitting uniquely from its capabilities. In aerospace, where structural efficiency is paramount, FDM enables the creation of components that enhance performance without compromising safety. This technology allows engineers to produce parts that streamline aircraft operations and improve fuel efficiency, offering both economic and ecological benefits.
Automotive Advancements
In the automotive industry, FDM's impact is equally transformative. The ability to create robust, intricate components with advanced thermoplastics has opened up new possibilities for innovation and rapid prototyping. Automotive manufacturers can now experiment with designs efficiently, reducing the time to market for new models and technological advancements. The adaptability of FDM supports the development of complex structures that enhance vehicle functionality and design, meeting industry demands for both efficiency and aesthetics.
- Innovative Prototyping: FDM supports the swift creation of detailed, functional prototypes. This capability enables accelerated testing and refinement, helping manufacturers to stay ahead in a competitive market.
- Complex Geometries: With FDM, automotive engineers can design and produce parts with intricate geometries that were previously difficult to achieve, supporting innovative design solutions.
Railway and Beyond
FDM's influence extends into the railway industry, where it excels in meeting stringent safety and performance standards. The technology adeptly produces components tailored to specific regulatory requirements, ensuring the reliability and safety of rail systems. By leveraging FDM, railway companies can efficiently manage maintenance and part replacements, enhancing operational effectiveness and longevity.
Beyond these sectors, FDM continues to make significant inroads into medical, dental, and consumer goods industries. In healthcare, its ability to produce custom, patient-specific implants and devices marks a pivotal advancement in personalized medicine. For consumer products, FDM offers the versatility to create tailored, unique items that align with individual consumer preferences, supporting the growing trend towards bespoke and personalized goods.
The adaptability and broad applicability of FDM technology facilitate its integration across diverse industries, each benefiting from its capacity to drive innovation and optimize production processes.
Versatile FDM Applications
FDM technology's adaptability extends into a multitude of practical applications, each offering distinct advantages. In manufacturing settings, FDM excels at producing jigs and fixtures, streamlining the creation of essential tools with efficiency. By enabling rapid customization, manufacturers can enhance assembly processes, leading to improved operational dynamics.
Functional Prototyping
The role of FDM in functional prototyping is underscored by its ability to deliver robust prototypes with exceptional speed. These prototypes undergo extensive testing, offering critical insights into design viability and functionality prior to mass production. The technology's ability to accommodate swift prototyping cycles enhances the capacity for iterative improvements based on real-world data.
- Swift Design Adaptation: FDM supports quick modifications, empowering engineers to refine designs efficiently and enhance product performance through successive trials.
- Application-Specific Testing: By producing prototypes that closely simulate end-use conditions, FDM enables realistic assessments of design functionality and durability.
Advanced Tooling and Customization
For applications involving advanced tooling, FDM demonstrates a remarkable capacity for crafting intricate components with precision. This capability is crucial in developing molds and dies that adhere to stringent specifications, integral for sectors requiring detailed craftsmanship. Moreover, FDM's adaptability in producing limited-run and custom parts underscores its economic advantage in addressing specific market demands with precision.
- Precision Tool Fabrication: FDM facilitates the creation of complex tools essential for high-precision industries, ensuring adherence to exacting design standards.
- Targeted Solutions: The technology's flexibility accommodates the production of specialized parts, catering to distinct client specifications without the constraints of traditional methods.
The ability of FDM to optimize quality across various applications further solidifies its value proposition. By exercising meticulous control over production parameters, FDM ensures that each output aligns with the intended use case, reinforcing its position as a versatile asset in modern manufacturing practices.
FDM Materials: Diverse and Capable
The material offerings in FDM technology are expansive, tailored to meet a variety of industrial demands. This selection allows manufacturers to choose materials that not only fulfill the functional requirements of their projects but also align with specific performance criteria. By leveraging this diversity, components are produced efficiently and can withstand a range of operational conditions, whether they need to endure stress, provide strength, or resist environmental factors.
Thermoplastics and Advanced Options
FDM technology provides a comprehensive suite of production-grade thermoplastics, each with unique attributes suited for different applications. Materials such as Polycarbonate (PC) and Polyphenylsulfone (PPSU) offer enhanced mechanical properties, catering to environments where durability and stability are paramount.
- High-Temperature Endurance: Materials like PPSU are ideal for applications demanding resistance to high temperatures and challenging chemical environments.
- Mechanical Robustness: Polycarbonate provides exceptional durability, making it suitable for parts that require impact resistance.
Reinforced and Specialized Filaments
Beyond standard thermoplastics, FDM technology incorporates filaments enhanced with reinforcing elements, such as fiberglass and Kevlar. These specialized materials provide superior mechanical performance, enabling the creation of lightweight yet strong components for demanding applications.
- Fiberglass Reinforcement: Filaments with fiberglass offer increased tensile strength, making them suitable for high-stress applications where weight savings are crucial.
- Kevlar Infusion: Known for its durability and impact resistance, Kevlar-reinforced filaments provide excellent performance in protective and structural applications.
The integration of dissolvable support materials in FDM enhances the printing of intricate geometries, eliminating the need for complex manual post-processing. This capability preserves the integrity of detailed designs and supports the continuous innovation of new materials, broadening the scope and potential of FDM applications in the manufacturing industry.
Evaluating FDM for Your Business
Assessing the suitability of FDM technology for your business involves a strategic evaluation of potential applications and their specific requirements. Begin by identifying areas where FDM could enhance or streamline production processes. Consider applications ranging from rapid prototyping to the production of custom, low-volume parts, taking into account the unique demands of each use case.
Tailored Material Selection
Selecting the right materials is pivotal for realizing the full potential of FDM technology. It's essential to examine the specific properties of available thermoplastics, ensuring they align with the operational conditions and performance criteria of the intended application. This includes assessing how materials perform under various stresses and environmental factors.
- Operational Performance: Focus on materials that offer the necessary durability, flexibility, or resistance required for your products.
- Environmental Suitability: Choose materials that can withstand the specific environmental challenges pertinent to your application, such as UV exposure or chemical contact.
Capacity Planning and Financial Consideration
Accurately determining the production capacity and appropriate printer size is crucial for optimal integration. Evaluate your current and projected production needs to select a system that offers both efficiency and scalability. Additionally, a comprehensive cost analysis should include not only the purchase price but also the long-term expenses related to maintenance and materials.
- Adaptable Systems: Opt for a printer that provides flexibility to expand operations as demand increases, ensuring sustained productivity.
- Comprehensive Cost Review: Factor in all elements of cost, from initial setup to operational expenditures, to establish a clear understanding of the financial implications.
Exploiting FDM's design capabilities allows for innovation in product design, offering opportunities to improve both the aesthetics and functionality of components. By taking advantage of this design flexibility, businesses can overcome traditional manufacturing constraints and enhance their competitive edge in the market.
As you explore the potential of FDM technology for your business, remember that the right tools and expertise can make all the difference in your success. We're here to help you navigate this exciting frontier and unlock new possibilities for your manufacturing processes. Schedule a demo or try the platform to experience its capabilities — let us show you how Phasio can revolutionize your approach to FDM and take your business to the next level.