Why AM growth forecasts have it wrong
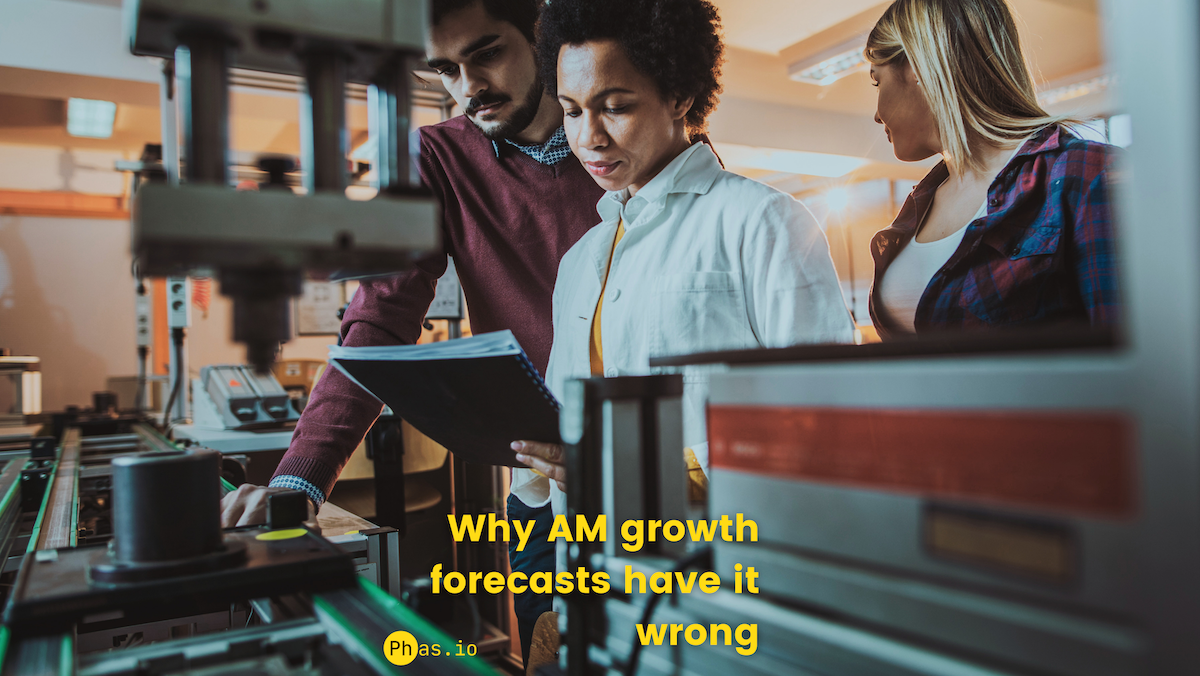
Current Status: Too Expensive for Consumer Marketplaces
If you’ve had any exposure to additive manufacturing, you probably realize that it’s an expensive process if you want multiple units produced. This makes it tough for consumers to truly utilize the technology.
After all, the consumer market is all about mass-producing a commodity item and selling it to the public. If one company chooses additive manufacturing for their part, they’ll likely lose to their competitors using injection molding.
This is especially true in the car industry. Tesla titan Elon Musk recently pointed out that printing consumer parts is too costly, but the technology can unlock faster innovation. That’s just the tip of the iceberg when you look at what additive manufacturing can unlock.
What Additive Manufacturing Can Unlock
We strongly believe that additive manufacturing is just in its infant years right now. Despite it being so versatile and useful today, we know that it could do even more tomorrow. It’s not just for rocket parts, there’s much more that this technology can unlock.
More Customization
One of the biggest selling points of additive manufacturing is its ability to help customize your project. A designer can create a new 3D printed part from scratch. There are fewer design restrictions which ultimately means more room for creativity.
From materials to geometries to overall form and function — the current state of additive manufacturing already has a lot of customization. We know that this will only get better in the coming years.
More customization also comes with more abilities for industries to start using this technology (beyond just rockets).
Fewer, More Complex Parts
One of the struggles of creating an assembled part is the complexity of assembly. Engineers have to spend extra hours and machinists have to dial in their tolerances in a lot of cases. This translates to more money and time spent in the process.
To have multiple parts come together into a single, robust assembly is harder than you might think.
Additive manufacturing unlocks the ability to simplify an assembly. You can use fewer, more complex parts in an assembly than you could with traditional machining.
This could remove the need for fasteners and adhesives. It also improves the overall accuracy and precision of the assembly.
Even though the individual parts are more complex, the assembly as a whole is simpler. Rather than four parts assembling together, a good designer could make a single part through additive manufacturing that does the same thing.
Industrial Settings Will Use More Plastics
For some reason, a lot of industries have been afraid of using plastics. Traditionally, they’ve been too expensive to make low-batch plastic parts, they don’t have the best material properties, and they’re really hard to manufacture.
Of course, additive manufacturing changed this for plenty of industries. Companies are understanding the viability of plastics, and more industries are using plastics in their everyday processes.
When you look around an industrial facility, you’ll typically see an assortment of metals being used. In the coming decades, we predict that trend will change, and you’ll find specialty plastics everywhere. Plastics are lighter, cheaper, and easier to design in most cases.
This is an idea that transcends just space travel and has plenty of uses on Earth.
Materials Will Improve
One of the current hold-ups is material selection. If an application calls for an engineered plastic, there’s not much opportunity for additive manufacturing.
That is, until the materials improve. We’re already seeing carbon fiber-infused filaments and plastics with embedded ceramics. Filament manufacturers are understanding how to strengthen the plastic and tweak the material properties with some minor changes.
Industries like automotive and marine are using nylon-reinforced plastic to save weight, money, and time as opposed to metal-based solutions.
Again, as the materials improve, we expect to see many more consumer applications.
High-Quality Engineered Materials
The new materials aren’t just new versions of PLA and ABS. Companies around the world are working on developing new high-quality engineered materials that can be used in a 3D printer.
For example, Orion AM is leading additive manufacturing technologies through printing with aerospace-grade polymers and composites with injection-moulded strength. Their patent-pending technologies have broadened the scope of applications 3D printing can deliver including lightweight structures and components for space missions such as CubeSats and rovers.
Companies can create industry-specific materials that can be fed into an additive manufacturing machine and print products. It’s no longer just a matter of picking between PLA or ABS. This is huge news for every industry, beyond just rocket companies.
An Application for Most Industries
As of today, dozens of industries are using 3D printing to some capacity. For many, it’s used to prototype, test, and prove theories before moving to larger-scale production.
You’ll find industries like automotive, marine, military, chemical, medical, and pharmaceutical companies using additive manufacturing every day.
Significantly Lower Costs
Our CEO, Raman, recently co-authored a research paper that reduces the costs of producing single-crystal metals by orders of magnitude using an SLM Solutions, SLM 500 printer.
With improved additive manufacturing technology, we expect these same cost savings to trickle into everyday consumer goods. This is great news for every industry and application that has been deterred by additive manufacturing’s currently high costs.
More Opportunities for Innovation
When you combine all of these benefits, you’re left with an incredible opportunity for accelerated innovation.
People are becoming their own machine shop by buying and setting up 3D printers around their facilities. Companies can create prototypes at speeds, prices, and accuracies that they have never dreamed of.
This allows for expedited and iterative testing within their own facilities without spending an arm and a leg on manufacturing costs. As you can imagine, additive manufacturing is becoming a launching point for companies to start pushing the envelope and developing new technologies.
Creating Printed Metal Parts
The market can currently print metal parts in titanium, stainless steel, and aluminum. This technology can save countless amounts of money and time each year for your operation.
Looking at the physical properties, it’s nearly impossible to discern a 3D-printed metal part from a traditionally machined one. The big differences are higher accuracy, added levels of intricacies, and a better finish on the printed parts.
Look around your operation at how many metal parts are being used. If you’re due for a replacement or want to upgrade your process, you can simply 3D print a new part in metal.
Additive Manufacturing: It Isn’t Rocket Science
As you can see, this process isn’t just for rockets. Additive manufacturing is simple to use and readily available. We’re seeing a number of industries start implementing additive manufacturing into their process, and the results are great.
The whole process is far from rocket science. In fact, some schools are having middle schoolers use 3D printers to make custom parts. If they can do it, so can your operation. So can any application or industry on the market today.
The only thing missing is an intelligent platform to hold it all together.
Bridging the Gap with an Intelligent Platform
What we’ve found over the years is that additive manufacturing needs a more robust platform. The work is often too operator-reliant and uses a lot of human interaction. This wastes time, money, and strays away from peak efficiency.
At Phasio, our mission is to bridge the gap and provide an intelligent platform. We can help your operation improve its throughput and turnaround time, increasing your sales and moving closer to low-cost additive manufactured goods for consumers. Contact us today to see how we can help.