Calculating 3 Axis Milling Costs: Tips for Accurate Estimates
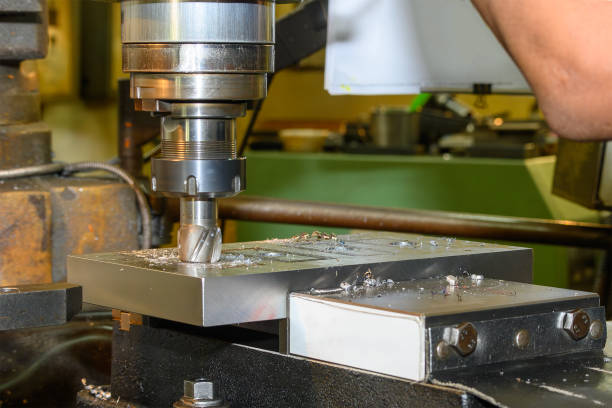
Calculating the cost of 3-axis milling is a critical task for machine shops looking to maintain profitability and deliver competitive pricing. By understanding the various factors that influence machining expenses, businesses can make informed decisions about their manufacturing processes.
Accurate cost estimation is essential for effective project planning and budgeting. It allows machine shops to allocate resources efficiently and ensures that they can deliver high-quality parts while maintaining healthy profit margins.
In this article, we will explore the key components of 3-axis milling cost calculation and provide insights on how to optimize your machining operations for cost-effectiveness. We will delve into the details of machine time, labor, materials, and overhead expenses, offering practical tips and tools to help you streamline your cost estimation process.
What is 3-Axis Milling Cost Calculation?
3-axis milling cost calculation is a comprehensive process that takes into account all the expenses associated with producing parts using a 3-axis CNC milling machine. This includes the cost of machine time, labor, materials, and overhead. By carefully analyzing these factors, machine shops can develop accurate estimates for their projects, ensuring they remain competitive and profitable.
Precise cost estimation is crucial for the success of any machining business. Underestimating costs can lead to reduced profits or even losses, while overestimating can result in lost opportunities and uncompetitive pricing. By understanding the intricacies of 3-axis milling cost calculation, machine shops can strike the right balance and make informed decisions about their manufacturing processes.
Some key components that influence 3-axis milling costs include:
- Machine hourly rate: The cost of operating the CNC machine per hour, considering factors such as depreciation, maintenance, and utilities.
- Material costs: The price of raw materials, including the cost of the workpiece and any additional materials required for the machining process.
- Labor costs: The wages of machine operators, programmers, and other personnel involved in the setup and operation of the 3-axis milling machine.
- Overhead expenses: Indirect costs such as facility rent, insurance, and administrative expenses that contribute to the overall cost of running the machine shop.
By carefully evaluating each of these components, machine shops can develop a comprehensive understanding of their 3-axis milling costs and make data-driven decisions to optimize their operations. This process is essential for maintaining a competitive edge in today's fast-paced manufacturing landscape.
Calculating 3-axis milling costs demands a thorough evaluation of distinct elements that influence the total expense of machining operations. The assessment commences with an analysis of the operational hours required by the CNC machine, which significantly impacts the cost structure. This operational time is a crucial determinant in setting the final pricing, as it ensures that the machinery's capacity is utilized effectively and aligns with competitive market demands.
An in-depth cost analysis holds paramount importance in this context. By dissecting individual components such as materials, labor, and overhead, businesses gain an accurate picture of their financial commitments. This methodical approach not only aids in precise budgeting but also highlights potential areas for cost optimization and improved resource distribution. By focusing on each aspect separately, manufacturers can streamline operations and enhance cost-efficiency.
Leveraging sophisticated tools and methodologies, like cost estimation software, can greatly refine the accuracy of 3-axis milling cost calculations. These solutions facilitate the process by automating detailed computations and offering insights rooted in data analysis. Such a strategy not only expedites the estimation process but also minimizes the risk of inaccuracies, resulting in more dependable financial projections.
Step 1: Analyze Machine Time
Analyzing machine time is essential for calculating the costs of 3-axis milling. This involves determining the exact duration each part requires on the CNC machine, factoring in the complexity and intricacy of the design. By accurately estimating this time, manufacturers can ensure projects adhere to production schedules and financial plans.
Integrating sophisticated cost estimation algorithms can significantly enhance precision in machine time calculations. These algorithms evaluate factors such as toolpath efficiency and cutting dynamics to offer a comprehensive view of the necessary machining time. Utilizing such technology simplifies the estimation process, leading to improved operational efficiency and minimizing reliance on manual calculations.
The specific CNC hourly rate is vital in this analysis, encapsulating the comprehensive cost of machine operation. This includes elements like machine wear, tool costs, and energy usage. By considering the hourly rate tailored to 3-axis milling, businesses can develop cost estimates that reflect true operational expenses, enabling them to maintain competitive pricing while ensuring quality and timely delivery.
Step 2: Determine Material Costs
Material selection plays a pivotal role in calculating costs for 3-axis milling. When selecting materials, it is important to consider their machinability and how they align with the project’s specifications. Materials with high machinability, like aluminum, often require less machining time and tool wear, making them cost-effective choices. In contrast, tougher materials may need slower cutting speeds and more frequent tool replacements, impacting the total expenditure.
The cost of raw materials must be assessed by looking at unit prices and potential waste generation. Efficiently managing material usage can lead to substantial savings. Strategies such as optimizing part layouts and reducing scrap can minimize waste and decrease the cost per finished component. Moreover, keeping an eye on market trends and material price shifts ensures that cost estimates remain accurate and reliable over time.
Step 3: Evaluate Labor Costs
Assessing labor costs requires a focused look at the time and skills necessary for both the setup and execution stages in 3-axis milling. Setup involves configuring machine parameters, tool selection, and ensuring proper alignment, which can be streamlined by experienced staff to reduce idle machine time and increase efficiency.
Incorporating the rates for operators and programmers into your cost analysis is vital for a holistic financial overview. Operators oversee the machine's operation, ensuring accuracy and consistency, while programmers develop and refine the machining paths. Both roles demand specialized knowledge, and it is crucial to balance competitive compensation with operational budgets to sustain a skilled workforce.
By thoroughly evaluating labor costs, manufacturers can pinpoint areas for improvement and optimize resource allocation. This analysis not only supports competitive pricing strategies but also ensures the workforce's productivity is maximized, directly influencing the profitability of milling operations.
Step 4: Consider Overhead Expenses
Overhead expenses include a broad array of indirect costs essential for the day-to-day operations of a machine shop. These encompass expenditures such as utilities—electricity, water, and gas—necessary for running CNC machines, as well as costs related to facility upkeep and general administrative functions. Understanding the impact of these expenses is crucial for comprehensive financial planning and maintaining the efficiency of operations.
Adopting adaptable pricing models can significantly aid in managing these overhead expenses. Such models enable machine shops to adjust their pricing structures in response to changes in overhead, ensuring competitiveness and profitability. For example, during periods of decreased production, cutting back on non-essential utilities can help control costs. Conversely, when demand surges, adjusting pricing to reflect increased operational needs ensures that profit margins remain intact. This flexibility allows businesses to navigate market fluctuations effectively and maintain financial stability.
Incorporating a detailed analysis of overheads into the cost estimation process yields a more accurate depiction of the financial landscape. By factoring in these indirect costs, manufacturers can craft pricing strategies that encompass all aspects of production, from direct expenses to long-term sustainability. This approach not only ensures value delivery to clients but also fortifies the business against economic shifts, supporting enduring success in a competitive industry.
Step 5: Compile the Machining Cost Breakdown
To compile the machining cost breakdown, it's essential to integrate all calculated expenses into a single, cohesive estimate. This integration should encompass every aspect of the machining process, from the precise duration of machine utilization and material choices to labor input and associated overheads. By ensuring that each cost component is meticulously accounted for, manufacturers can gain a comprehensive understanding of the project's financial scope, facilitating competitive pricing strategies and sustainable profitability.
Advanced cost estimation tools, such as specific software solutions tailored for 3-axis milling, can significantly aid in this compilation. These tools automate the aggregation of data, providing detailed breakdowns that highlight cost drivers and potential areas for optimization. By employing these technologies, manufacturers can swiftly adapt to changing production variables, ensuring that cost assessments remain both accurate and reflective of current operational conditions. This method not only enhances the efficiency of the estimation process but also bolsters the reliability of financial projections, supporting informed decision-making and strategic planning within the organization.
Calculating 3-axis milling costs is a complex process that requires careful consideration of various factors, from machine time and material expenses to labor costs and overhead. By leveraging advanced tools and methodologies, manufacturers can streamline this process, ensuring accurate estimates that support competitive pricing and profitability. If you're looking to optimize your machining operations and enhance your cost estimation capabilities, schedule a demo or try the platform to experience its capabilities – we're here to help you every step of the way.