Integrating 5-Axis CAM for Enhanced Machining Efficiency
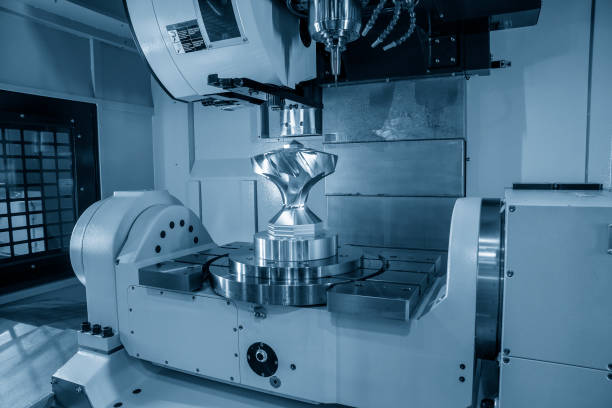
5-axis machining is a game-changer for manufacturers looking to boost efficiency and precision. By integrating advanced CAM software into existing processes, machine shops can unlock the full potential of their multi-axis machines and stay ahead of the competition.
Integrating 5-axis CAM solutions may seem daunting at first, but with the right approach and tools, it can be a seamless process that yields significant benefits. From creating complex geometries to improving surface finishes, 5-axis CAM integration empowers manufacturers to take on more challenging projects and deliver exceptional results.
In this article, we'll explore the ins and outs of 5-axis CAM integration, providing you with the knowledge and strategies needed to successfully implement this technology in your machine shop. Whether you're a seasoned professional or just starting to explore the world of multi-axis machining, this guide will help you navigate the process and make informed decisions.
What is 5-axis CAM Integration?
5-axis CAM integration is the process of incorporating advanced Computer-Aided Manufacturing (CAM) software into existing manufacturing workflows to optimize the capabilities of 5-axis CNC machines. This integration enables manufacturers to create complex part geometries with enhanced precision and efficiency, ultimately leading to improved machining performance and reduced production times.
By leveraging the power of 5-axis CAM software, machine shops can take full advantage of the unique capabilities of their multi-axis machines. This includes the ability to machine intricate features, undercuts, and contoured surfaces that would be challenging or impossible with traditional 3-axis machining. Additionally, 5-axis CAM integration allows for more efficient toolpath generation, reducing the number of setups required and minimizing tool wear.
Key benefits of 5-axis CAM integration include:
- Increased design flexibility: 5-axis machining enables the creation of complex, organic shapes and contours that are essential in industries such as aerospace, medical, and automotive.
- Improved surface finish: By maintaining optimal tool orientation throughout the machining process, 5-axis CAM software helps achieve superior surface finishes, reducing the need for manual polishing and secondary operations.
- Reduced setup times: With the ability to machine multiple sides of a part in a single setup, 5-axis CAM integration significantly reduces the time and effort required for part handling and fixturing.
- Enhanced tool life: Advanced toolpath strategies in 5-axis CAM software, such as trochoidal milling and constant tool engagement, help minimize tool wear and extend tool life.
To successfully integrate 5-axis CAM into your manufacturing processes, it's essential to assess your current setup, choose the right software solution, and implement best practices for programming and machining. By doing so, you can unlock new opportunities for growth and innovation in your machine shop, just like we offer at Phasio.
How to Integrate 5-axis CAM
Embarking on 5-axis CAM integration requires an initial, detailed assessment of your current manufacturing setup. This involves a thorough appraisal of existing CNC programming protocols to identify compatibility with multi-axis operations. By evaluating production timelines and pinpointing areas where efficiencies could be gained, you can better understand how 5-axis CAM might streamline processes and enhance output quality.
In exploring CAM software options, prioritize solutions that offer a robust array of features specifically designed for 5-axis machining environments. Look for software with capabilities that enable intricate toolpath generation and sophisticated machine simulations; these will facilitate precision in complex parts manufacturing. Advanced collision detection and avoidance mechanisms are also critical, ensuring that machine operations remain uninterrupted and safe.
Choosing the right software involves not only technological capabilities but also alignment with your shop's specific needs. Consider the typical complexity of parts and the materials you work with—these factors should guide your software choice to ensure it supports your current and future manufacturing objectives efficiently. Opt for a solution that integrates smoothly with your existing systems and can adapt to evolving production challenges, thus ensuring a comprehensive enhancement of your machining processes.
Step 1: Evaluate Your Current Setup
A comprehensive examination of your machining environment sets the foundation for successful 5-axis CAM integration. Begin by scrutinizing your CNC programming landscape, focusing on its readiness to accommodate the nuanced demands of multi-axis operations. The inspection should include a review of the software's ability to handle intricate toolpath strategies and the machine’s readiness for enhanced kinematic challenges.
Focus on your machines' hardware capabilities to ensure they are equipped for 5-axis tasks. Evaluate the machine controllers for their capacity to execute complex, simultaneous multi-axis maneuvers. This step is crucial for identifying any technological gaps, such as outdated interfaces or limited processing capabilities, that could hinder the transition and require upgrades or replacements.
Finally, project the potential transformation integrating 5-axis CAM software could bring to your production floor. Consider how it could broaden your manufacturing capabilities, allowing you to tackle projects involving sophisticated geometries with greater ease. Assess the anticipated advancements in cycle times and throughput, which result from streamlined setups and optimized tool paths. This strategic evaluation helps align your technological investments with your shop’s long-term productivity goals.
Step 2: Choose the Right CAM Software
Selecting a CAM software that aligns with your 5-axis machining needs requires careful consideration of its capabilities and adaptability. Begin by exploring software options renowned for their innovative 5-axis machining solutions, which should include efficient toolpath generation tailored to handle complex contours and surfaces. Look into platforms like hyperMILL, known for its ease of use and advanced machining strategies, which can streamline operations and enhance part accuracy.
When assessing CAM software, prioritize platforms that offer dynamic simulation environments and robust collision prevention systems. These features are essential for preemptively mitigating machining errors and ensuring safe operations. Simulation capabilities provide a virtual environment to refine toolpaths before actual production, reducing downtime and avoiding costly mishaps. This focus on preemptive safety measures is crucial for maintaining smooth production flows.
Additionally, consider the software’s ability to integrate with your existing infrastructure seamlessly. Opt for solutions that offer intuitive interfaces and are compatible with your machine controllers to facilitate a straightforward implementation process. This ensures that the transition to advanced CAM software enhances your current processes without unnecessary disruptions, allowing for increased productivity and operational efficiency.
Step 3: Implement Software and Train Staff
Integrating new CAM software demands a meticulous approach to ensure a smooth transition and effective utilization. Begin by crafting a detailed implementation roadmap that outlines the stages of software setup, taking into account production schedules to minimize workflow interruptions. This roadmap should be designed with flexibility in mind, allowing adjustments as the integration progresses, ensuring the software becomes an integral part of your operations swiftly and efficiently.
Training programs are essential for empowering your team to use the CAM software proficiently. Organize targeted training sessions that delve into the software's full capabilities, from basic navigation to advanced programming techniques. These sessions should cater to diverse skill levels within your team and include interactive components that allow staff to engage directly with the software in simulated real-world scenarios. This hands-on experience is crucial for building confidence and competence in using the new tools.
To promote consistent and efficient software use, establish a set of operational guidelines that align with your shop's specific needs and goals. These guidelines should provide clear instructions on executing tasks and optimizing processes using the software's features. Encourage an environment where feedback is actively sought and shared, fostering a culture of continuous learning and adaptation. By doing so, your team can fully capitalize on the capabilities of the new CAM software, enhancing productivity and innovation on the shop floor.
Step 4: Optimize 5-axis Setup
To fully capitalize on the capabilities of your 5-axis setup, meticulous fine-tuning of machine parameters and tool orientations is essential. This process begins with a thorough review of machine settings, ensuring they are optimized for your specific machining tasks and materials. Adjust spindle speeds, feed rates, and tool path strategies to match the demands of high-precision operations. Precision in these settings ensures that your machine can execute complex tasks with the accuracy required for high-quality production outcomes.
Effective tool orientation involves leveraging multi-directional capabilities to maintain optimal contact with the workpiece. Implement strategies that dynamically adjust the tool’s position relative to the part’s geometry, enhancing cutting conditions and minimizing deflection. Such adjustments allow for smoother transitions across complex surfaces, ensuring consistent quality and reducing the likelihood of tool fatigue.
Incorporating advanced machining techniques, such as high-speed surfacing and barrel milling, significantly enhances both efficiency and quality. High-speed surfacing facilitates rapid material removal with superior finish by utilizing optimized paths that reduce machining time. Barrel milling, utilizing tools with complex geometries, effectively manages large surface areas with fewer passes, enhancing surface integrity and decreasing cycle times. These methodologies, when integrated into your 5-axis setup, transform operational efficiency, ensuring your production processes are not only faster but also more reliable and cost-effective.
Step 5: Monitor and Adjust Processes
Achieving sustained excellence in 5-axis machining demands a vigilant approach to monitoring operations and a readiness to refine processes. Establish a comprehensive set of performance indicators, such as operational efficiency, tool life, and finish quality, to assess machine effectiveness continuously. These indicators offer a data-driven foundation for detecting potential areas of improvement. Regular analysis of this data allows you to identify trends or irregularities that may signal process issues or optimization opportunities.
Addressing any inefficiencies involves a holistic evaluation of the entire machining workflow, from initial programming to final execution. This detailed examination helps uncover the root causes of any deviations, enabling precise corrections rather than superficial fixes. Engage multidisciplinary teams in this diagnostic process to draw on a wide range of skills and insights, promoting a culture of collaboration and innovation focused on refining operations.
Consistently revisiting machine configurations and toolpath strategies is essential for sustaining high standards. Factor in the effects of normal wear on machinery and tools; regular maintenance and timely upgrades are crucial. Implement feedback mechanisms within your monitoring system to gather insights from operators directly involved in the machining process. This real-time input, integrated with analytical reviews, empowers you to make strategic adjustments that enhance efficiency and product quality, ensuring your 5-axis machining remains at the forefront of industry standards.
Final Thoughts
Adopting 5-axis CAM technology in machining processes heralds a significant advancement in manufacturing capabilities. With its ability to produce intricate components and complex surfaces, this technology becomes essential for manufacturers seeking to expand their production repertoire. By integrating 5-axis machining, operations not only become more efficient but also unlock new avenues for creative and precise production.
Strategic Benefits: Embracing 5-axis CAM provides a range of strategic improvements, including:
- Expanded Design Possibilities: The capability to manufacture parts with intricate details enhances product offerings, allowing access to new market segments and client needs.
- Operational Agility: The versatility of multi-axis machining supports rapid transitions and adaptability, catering to diverse project specifications and accelerating innovation.
Industry Leadership: In the ever-evolving manufacturing landscape, the ability to swiftly address complex machining challenges and deliver high-quality results sets businesses apart. Efficiency improvements lead to shorter lead times and increased capacity for handling multiple projects without compromising precision. This technological edge empowers shops to continuously innovate and respond proactively to market demands.
The integration of 5-axis CAM transcends mere technological enhancement; it represents a strategic evolution in manufacturing practices. By leveraging this technology, machine shops position themselves to not only meet today's complex machining challenges but also to anticipate and adapt to future industry shifts.
As you embark on your 5-axis CAM integration journey, remember that the key to success lies in careful planning, strategic implementation, and continuous optimization. By leveraging the right tools and best practices, you can unlock new opportunities for growth and innovation in your machine shop. If you're ready to take your manufacturing processes to the next level, schedule a demo or try the platform to experience how we can help you streamline your operations and boost your productivity.