Essential Tools for 3-Axis CNC Inspection Processes
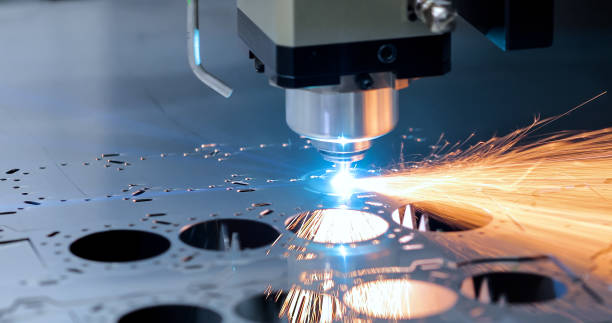
In today's fast-paced manufacturing landscape, precision and quality are paramount. As industries such as aerospace, defense, and automotive demand ever-tighter tolerances and flawless components, the importance of rigorous inspection processes for CNC machined parts cannot be overstated.
Among the various CNC machining techniques, 3-axis machining is widely used for its ability to produce complex geometries with high accuracy. However, ensuring that these machined components meet the required specifications and quality standards necessitates a robust inspection process.
This article delves into the world of 3-axis CNC inspection, exploring its significance, key parameters, essential tools and techniques, and best practices for implementing effective quality control measures. By understanding the intricacies of 3-axis CNC inspection, manufacturers can optimize their processes, enhance productivity, and deliver exceptional products to their customers.
What is 3-Axis CNC Inspection?
At its core, 3-axis CNC inspection is a meticulous process that involves verifying the accuracy, quality, and performance of parts machined using 3-axis CNC machines. This comprehensive approach ensures that machined components meet the specified tolerances and adhere to the highest quality standards.
The primary goal of 3-axis CNC inspection is to identify and address any deviations from the intended design, ensuring that the final product aligns perfectly with the customer's requirements. This process is particularly critical for industries such as aerospace, defense, and automotive, where even the slightest imperfections can have severe consequences.
By employing advanced inspection tools and techniques, manufacturers can detect and rectify issues early in the production process, minimizing waste, reducing costs, and improving overall efficiency. From dimensional accuracy and surface finish to material properties and geometric dimensioning, 3-axis CNC inspection covers a wide range of parameters to guarantee the highest level of precision and reliability.
The Importance of 3-Axis CNC Inspection
In today's competitive manufacturing environment, delivering high-quality products consistently is not just a matter of pride—it's a necessity for survival. 3-axis CNC inspection plays a vital role in ensuring that machined components meet the stringent requirements of customers and regulatory bodies alike.
By implementing a robust inspection process, manufacturers can:
- Maintain Tight Tolerances: 3-axis CNC inspection allows for the verification of dimensional accuracy, ensuring that parts are machined within the specified tolerances. This is particularly crucial for components that must fit seamlessly with other parts in an assembly.
- Ensure Functional Performance: Through thorough inspection of surface finish, material properties, and geometric features, manufacturers can guarantee that the machined parts will perform as intended in their final application. This is especially important for components subjected to high stress or extreme conditions.
- Comply with Industry Standards: Many industries have specific quality standards and regulations that must be met, such as ISO 9001 for general quality management and AS9100 for the aerospace sector. 3-axis CNC inspection helps manufacturers demonstrate compliance with these standards, instilling confidence in their customers and opening up new market opportunities.
- Reduce Costs and Waste: By identifying and addressing quality issues early in the production process, manufacturers can minimize scrap, rework, and warranty claims. This not only saves time and resources but also contributes to a more sustainable and efficient manufacturing operation.
Implementing a comprehensive 3-axis CNC inspection process is not just a matter of meeting customer expectations; it's a strategic decision that can give manufacturers a competitive edge in their industry. With the right tools, techniques, and best practices, manufacturers can unlock the full potential of their 3-axis CNC machines and deliver products that exceed expectations.
Key Parameters for 3-Axis CNC Inspection
Ensuring geometric precision in 3-axis CNC machining involves more than just checking measurements—it's about guaranteeing that each part matches its design blueprint with exactitude. This requires advanced verification tools, including Coordinate Measuring Machines (CMMs) that can accurately map complex contours and dimensions. Utilizing these tools allows for precise validation of each component’s conformity, ensuring fit and function in their respective assemblies.
The evaluation of surface integrity goes beyond mere aesthetics. It involves a detailed assessment of texture and finish to ensure components operate efficiently within their mechanical environments. By employing instruments like profilometers, manufacturers can detect minute surface discrepancies, safeguarding against potential operational inefficiencies caused by friction or other surface-related issues.
The robustness of materials under operational stress necessitates thorough examination. Using methods such as ultrasonic testing and X-ray inspection, manufacturers can uncover minute internal flaws that might not be evident through surface evaluation alone. These non-destructive testing techniques are essential for ensuring the internal integrity and reliability of components, particularly those subjected to high-stress conditions.
Geometric dimensioning and tolerancing (GD&T) serves as a critical blueprint for precision engineering. This comprehensive system allows manufacturers to define permissible variations in part geometry, ensuring exact alignment and interaction of components within assemblies. Leveraging GD&T ensures that even the most intricate designs meet stringent operational specifications, fostering reliability and performance consistency.
Monitoring the state of cutting tools is essential for maintaining production quality and efficiency. Regular inspection and timely replacement of tools prevent degradation that can compromise part precision. Implementing real-time monitoring systems helps capture data on tool performance, enabling manufacturers to optimize tool life and minimize downtime, ensuring continuous production flow.
Adherence to established quality benchmarks like ISO 9001 and AS9100 signifies a commitment to excellence. These standards provide a structured approach to quality management that bolsters a manufacturer's capability to produce consistent, high-quality outputs. Compliance not only reinforces customer confidence but also enhances operational processes, positioning manufacturers as leaders in precision and reliability.
Essential Inspection Tools and Techniques
Accurate dimensional measurement is fundamental to effective CNC inspection. Basic tools like calipers and micrometers serve as the first line of defense in confirming that parts meet their specified dimensions. These instruments allow for precise measurement of both external and internal features, providing immediate feedback on machining accuracy. For complex geometries, advanced equipment like Coordinate Measuring Machines (CMMs) offers a comprehensive solution. These machines utilize touch probes or laser technology to capture detailed data on a part's form, ensuring that its dimensions align with design specifications. By integrating CMMs into inspection routines, manufacturers gain an intricate understanding of their components' geometric fidelity.
Surface quality plays a crucial role in a part's functionality and performance. Instruments such as surface roughness testers and optical comparators are vital for assessing surface conditions, offering a quantitative analysis of texture and finish. Surface roughness testers, for instance, can measure the micro-texture of a surface, identifying any irregularities that might affect performance. Optical comparators allow inspectors to visually examine surfaces, magnifying features to detect defects that could compromise a part's operational integrity. This dual approach—combining quantitative measurement with visual inspection—ensures a comprehensive evaluation of surface quality.
Assessing material properties is essential for determining a component's suitability for its intended use. Hardness testing devices, like those using the Rockwell or Brinell scale, provide critical insights into a material's resistance to deformation. For identifying hidden internal defects, non-destructive testing methods, including ultrasonic and radiographic techniques, are employed. Ultrasonic testing uses sound waves to detect subsurface discontinuities, while radiographic techniques reveal internal structures through imaging. These methods enable manufacturers to ensure the internal soundness of their components, preventing potential failures in service.
Statistical Process Control (SPC) stands as a cornerstone of quality management in CNC machining. Through the use of specialized software, manufacturers can collect and interpret production data to monitor process stability. Real-time data collection allows for the immediate identification of anomalies, enabling corrective actions to be taken swiftly. This dynamic approach ensures that production remains consistent and within quality parameters, fostering a proactive environment focused on continuous improvement and operational excellence.
Inspection Stages in 3-Axis CNC Machining
The inspection process for 3-axis CNC machining involves multiple stages, each aimed at ensuring the highest quality and precision of machined parts. These stages are meticulously designed to catch discrepancies early, maintain consistent quality, and refine the production process.
In-Process Inspection by Machine Operators
During the machining process, operators play a crucial role by utilizing precise tools to ensure components are manufactured to specification. Using inspection techniques such as runout gauges and dial indicators, operators verify the alignment and stability of parts in real time. This hands-on approach allows for immediate detection of potential issues, enabling swift corrective actions that enhance the overall efficiency and accuracy of the production process.
Automated Probing for Real-Time Verification
Automated probing systems are integral to the verification process, providing sophisticated measurement capabilities during the machining cycle. These systems employ high-precision sensors to conduct detailed checks on critical dimensions, ensuring compliance with design specifications as machining progresses. The integration of automated probing allows for seamless adjustments to be made, maintaining consistent quality across production runs and significantly reducing the likelihood of defects.
Final Inspection by Quality Control Department
The final inspection stage involves an exhaustive assessment by the quality assurance team, utilizing cutting-edge equipment like laser scanners and advanced imaging technology. This stage serves as a comprehensive review, focusing on verifying intricate part geometries and ensuring adherence to design criteria. By applying these advanced inspection methods, the quality control department ensures that all components meet the highest standards of precision and reliability before proceeding to further manufacturing stages or delivery.
Best Practices for Effective 3-Axis CNC Inspection
Implementing a robust quality management system forms the backbone of effective 3-axis CNC inspection. This system should encompass clear protocols and documentation procedures, ensuring consistency and traceability throughout the inspection process. By establishing a structured framework, manufacturers can effectively manage inspection schedules, maintain accurate records, and facilitate continuous improvement initiatives. This systematic approach not only enhances overall inspection efficiency but also supports compliance with industry certifications and standards.
Ensuring the precision and reliability of inspection equipment requires a strategic approach to calibration and upkeep. Instead of periodic checks, adopting a predictive maintenance model can proactively identify potential issues before they impact accuracy. Using data-driven insights to schedule maintenance activities minimizes downtime and extends the lifespan of equipment, enhancing the overall efficiency of the inspection process.
Equipping personnel with advanced skills through targeted training programs is essential to maintaining high levels of inspection accuracy. Rather than focusing solely on equipment operation, these programs should cover data interpretation and problem-solving to empower staff in making informed decisions. By fostering an adaptable and skilled workforce, manufacturers can swiftly address discrepancies, optimizing both inspection accuracy and production outcomes.
Incorporating machine learning algorithms and IoT-enabled devices into inspection processes can significantly enhance operational efficiency. These technologies provide real-time insights and predictive analytics, allowing for dynamic adjustments and improvements. By implementing smart manufacturing solutions, manufacturers can achieve greater precision, reduce error rates, and align with cutting-edge industry practices.
Building strategic alliances with specialized CNC services can offer invaluable technical support and innovation access. These partnerships provide opportunities for collaborative problem-solving and technology sharing, elevating a manufacturer's inspection capabilities. By engaging with industry experts, manufacturers stay at the forefront of technological advancements, ensuring the highest quality outcomes in their inspection processes.
As the manufacturing landscape evolves, embracing advanced inspection tools and techniques is crucial for staying competitive and delivering exceptional products. By implementing best practices and leveraging cutting-edge technologies, manufacturers can optimize their 3-axis CNC inspection processes, ensuring the highest levels of precision, quality, and customer satisfaction. If you're ready to take your inspection processes to the next level, schedule a demo or try the platform to experience how we can help you streamline your operations and achieve your quality goals.