MJF Part Quote Accuracy: How to Ensure Competitive Pricing
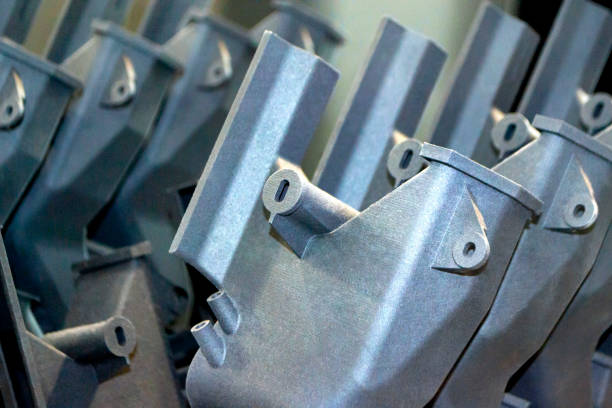
Multi Jet Fusion (MJF) has emerged as a game-changing 3D printing technology, offering unparalleled speed, accuracy, and cost-effectiveness for prototyping and production. As more businesses explore the potential of MJF, understanding the intricacies of part quoting becomes crucial for making informed decisions.
In this article, we will delve into the world of MJF part quoting, providing valuable insights to help you navigate the process and ensure competitive pricing for your projects. By the end, you will have a solid grasp of the factors influencing MJF part quotes and strategies to optimize your manufacturing workflow.
What is Multi Jet Fusion (MJF) Part Quoting?
Multi Jet Fusion (MJF) part quoting is the process of providing a detailed pricing estimate for parts manufactured using HP's advanced 3D printing technology. It involves a comprehensive assessment of various factors that contribute to the overall cost of producing MJF parts, ensuring that customers receive accurate and competitive quotes for their projects.
MJF part quoting takes into account several key elements:
- Material Costs: The specific MJF materials used, such as HP 3D High Reusability PA 12 (Nylon 12) or HP 3D High Reusability PP (Polypropylene), play a significant role in determining the final quote. Each material has its own unique properties and associated costs that must be factored in.
- Part Complexity: The complexity of the part design directly impacts the quoting process. Intricate geometries, fine features, and large build volumes may require additional processing time and resources, affecting the overall cost.
- Production Volume: The quantity of parts being produced is another crucial factor in MJF part quoting. Higher volumes often lead to economies of scale, allowing for more competitive pricing. Quoting systems like those offered at Phasio can automatically adjust prices based on order quantity.
- Lead Time: The urgency of the project and the required turnaround time also influence the final quote. Rush orders or expedited shipping may incur additional costs to meet tight deadlines.
By carefully analyzing these factors, MJF service providers can generate accurate and transparent quotes that help customers make informed decisions about their 3D printing projects. The quoting process aims to strike a balance between offering competitive prices and ensuring the highest quality parts are delivered within the specified timeframe.
In the following sections, we will explore the steps involved in ensuring competitive pricing for MJF part quotes and address frequently asked questions to help you navigate the process with confidence.
Analyze Material Costs
The choice of material plays a pivotal role in determining MJF part pricing. Each material has distinct characteristics that influence both the manufacturing process and the end-use application. For example, Nylon 12 offers excellent mechanical strength and is widely used for robust applications, while Polypropylene provides flexibility and chemical resistance for specialized uses. Understanding these attributes helps in selecting the right material that balances performance with cost-effectiveness.
Assess Production Complexity
Production complexity stems from the design's requirements and the intricacies involved in manufacturing. The design's level of detail can significantly impact production strategies, necessitating advanced techniques for intricate features. It's essential to evaluate how design complexity affects the overall manufacturing effort, ensuring that quotes accurately reflect the resources and expertise required.
Factor in Lead Times and Capacity
Effective management of lead times and production capacity directly influences pricing. Balancing the urgency of delivery with available resources can optimize production schedules, reducing costs. Real-time capacity management allows for dynamic adjustments to quotes, ensuring that pricing remains competitive while meeting client deadlines efficiently.
Compare with Other 3D Printing Technologies
MJF's advantages over other 3D printing technologies, such as its speed and precision, offer distinct benefits for certain applications. Highlighting these strengths can justify pricing by demonstrating the superior quality and efficiency of MJF-produced parts. This comparison helps educate customers on why MJF is suitable for their projects, emphasizing its value in delivering high-quality, cost-effective solutions.
Step 1: Analyze Material Costs
Evaluating material costs is essential for setting competitive prices in MJF part quotes. Each material involved in the Multi Jet Fusion process offers unique attributes that affect both pricing and application suitability. For example, HP 3D High Reusability PA 11 offers excellent impact resistance, making it ideal for applications demanding flexibility and toughness. Meanwhile, HP 3D High Reusability PA 12 Glass Beads provides enhanced stiffness and dimensional stability, suitable for structural components requiring rigidity.
Choosing the right material extends beyond cost considerations—it requires a thorough assessment of how specific material properties align with the project’s demands. This includes examining factors such as mechanical strength, thermal resistance, and environmental compatibility. By matching these attributes with the part's intended function, manufacturers ensure that the material not only satisfies technical requirements but also optimizes cost-effectiveness.
Access to comprehensive resources like material data sheets and performance comparisons is crucial in this decision-making process. These tools offer detailed information on each material's capabilities, facilitating an informed choice that balances performance requirements with budget constraints. By leveraging these insights, manufacturers can make strategic decisions that enhance both the quality and cost-efficiency of their MJF projects, resulting in precise quotes that meet customer expectations.
Step 2: Assess Production Complexity
Addressing the intricacies of MJF part production is critical for producing accurate quotes. Each design element—from complex geometries to fine details—requires careful consideration to determine the precise manufacturing approach. These elements influence the technical requirements and resources necessary for production, affecting the overall cost and efficiency. Analyzing these factors ensures that every aspect of the design is factored into the quoting process.
The quantity of parts required introduces additional layers to production planning. Larger orders can streamline operations through batch processing, which offers cost benefits and improved efficiency. Conversely, smaller runs might necessitate more frequent adjustments, influencing production timelines. Understanding the interplay between part complexity and order volume is key to optimizing production strategies and maintaining cost-effectiveness.
- Design Evaluation: Begin by thoroughly reviewing the part's design to pinpoint areas that could pose challenges during manufacturing. This includes examining complex shapes, precise tolerances, and any special requirements integral to the production process.
- Volume Considerations: Grasping how order size impacts production strategies is crucial. High-volume orders may leverage batch processing to achieve cost benefits, whereas smaller batches might require more agile approaches, impacting scheduling and efficiency.
- Technical Capabilities: It is essential to match design requirements with the technical capabilities of the MJF process. This ensures the chosen methods meet design criteria while remaining efficient and cost-effective.
Through a comprehensive assessment of these factors, manufacturers can align their quotes with the true cost of production. This approach not only ensures competitive pricing but also enhances the efficiency of the manufacturing process.
Step 3: Factor in Lead Times and Capacity
Navigating the intricacies of MJF production requires a keen understanding of how lead times affect the entire manufacturing workflow. Lead times for 3D printing can fluctuate based on part complexity, batch size, and the current workload. This knowledge allows for precise scheduling and helps set realistic client expectations, ensuring that quotes are accurate reflections of both cost and delivery feasibility.
Production capacity must be managed effectively to maintain efficiency. Factors such as equipment availability and workforce utilization can significantly impact product turnaround. To optimize capacity, consider strategies such as efficient resource allocation and predictive maintenance scheduling. This proactive approach minimizes potential bottlenecks, ensuring that production remains consistent and prices stay competitive.
Automated systems offer a sophisticated method for refining the quoting process by leveraging current production data. These systems can provide dynamic adjustments to quotes based on capacity and demand. This integration ensures that quotes are always aligned with the shop's operational realities:
- Dynamic Adaptation: Automated systems continuously analyze production data, making it possible to adjust quotes quickly as conditions change.
- Precision and Clarity: By minimizing manual input, these systems enhance the accuracy and transparency of pricing.
- Streamlined Operations: Automation reduces administrative burdens, allowing focus to shift toward enhancing production and customer engagement.
By implementing these strategies, manufacturers can ensure that their MJF part quotes are both reflective of true operational capabilities and competitive in the marketplace.
Step 4: Compare with Other 3D Printing Technologies
Multi Jet Fusion (MJF) offers unique benefits that set it apart within the 3D printing landscape. Unlike Fused Deposition Modeling (FDM) and Selective Laser Sintering (SLS), MJF excels in producing parts with high isotropy and consistent mechanical properties, essential for robust industrial applications. This distinction makes MJF particularly appealing for projects where material performance and part integrity are paramount.
MJF stands out with its simultaneous application of fusing and detailing agents, which enables the production of parts with intricate details and clean finishes—a capability that distinguishes it from SLS, where surface smoothness may require additional post-processing. Meanwhile, FDM, known for its versatility in material options, often lacks the precision and uniformity in mechanical properties that MJF provides.
- Comprehensive Material Use: MJF uses materials like Nylon 12 and Polypropylene, which offer balanced properties suitable for both prototypes and end-use parts. This contrasts with FDM's focus on a wide range of plastics and SLS's ability to handle high-temperature materials.
- Uniformity: The MJF process ensures parts have isotropic mechanical properties, meaning their strength is consistent in all directions. This feature is particularly beneficial for applications requiring reliable performance under stress, a challenge for FDM due to its layer-by-layer deposition.
- Surface Quality: MJF parts typically require minimal post-processing to achieve a smooth finish, reducing additional labor and costs compared to SLS, where surface refinement is often necessary.
Educating customers on these aspects involves demonstrating how MJF's strengths align with their specific needs, especially for applications demanding high mechanical integrity and precise detail. While SLS may be preferred for its ability to handle complex geometries without supports, and FDM for its cost-effective prototyping capabilities, MJF provides a compelling option for projects where the combination of high performance and surface quality is critical.
How to MJF Part Quote: Frequently Asked Questions
What factors influence the pricing of MJF parts?
Several vital elements contribute to the pricing of MJF parts, each playing a distinct role in shaping the final quote. The selection of materials directly impacts costs—materials like Nylon 12 and Polypropylene vary in price and suitability for different applications. Evaluating the specific needs of each project ensures that material choice aligns with both performance expectations and budget constraints.
The intricacy of the design dictates the technical approach required for production. Complex geometrical features may necessitate advanced techniques, influencing the manufacturing effort and associated costs. Considering the design's demands early in the process is essential for accurate quoting.
Lead times are another critical factor. The urgency of delivery schedules can affect production planning; expedited orders may incur additional charges to accommodate swift turnaround. Efficient scheduling and resource management are essential in maintaining competitive pricing while meeting client timelines.
- Material Characteristics: Opt for materials that balance cost with functionality, considering the specific requirements of each application.
- Design Complexity: Address intricate features with appropriate manufacturing techniques, ensuring that complexity is reflected in the quote.
- Production Scheduling: Efficiently manage timelines to balance cost and delivery requirements, optimizing resources to maintain competitiveness.
How does MJF compare to other 3D printing technologies?
Multi Jet Fusion distinguishes itself in the realm of 3D printing with its unique capabilities. Unlike some other technologies, MJF excels at producing parts with minimal post-processing, owing to its simultaneous application of fusing and detailing agents. This process results in parts that are ready for use with exceptional surface finishes and consistent mechanical properties, making it an ideal choice for high-precision applications.
In contrast to technologies like FDM and SLS, MJF offers a notable advantage in speed, producing parts rapidly without compromising on the quality of detail. Its ability to deliver parts with isotropic properties ensures that strength and performance are uniform across all dimensions—a crucial consideration for demanding industrial applications.
- Efficient Production: MJF's process reduces the need for extensive finishing, streamlining production and minimizing additional labor.
- Rapid Turnaround: The technology's swift production capability meets tight deadlines effectively, enhancing its appeal for time-sensitive projects.
- Consistent Quality: MJF parts boast uniform mechanical properties, supporting applications where reliability and strength are paramount.
By understanding the nuances of MJF part quoting, you can make informed decisions that optimize your manufacturing workflow and ensure competitive pricing for your projects. We invite you to schedule a demo or try the platform to experience its capabilities firsthand. Let us help you unlock the full potential of MJF technology and revolutionize your production process.