Effective SLA Batch Planning for Streamlined Operations
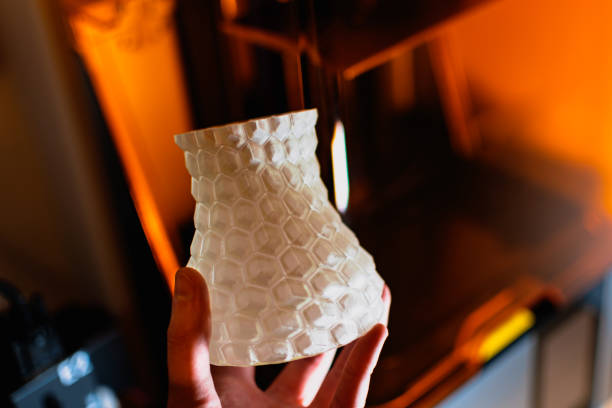
In today's fast-paced manufacturing environment, meeting customer expectations while optimizing production processes is paramount. Service Level Agreements (SLAs) play a crucial role in defining the standards and requirements that manufacturers must adhere to in order to deliver products and services effectively.
One key strategy for aligning production with SLA objectives is SLA batch planning. By strategically scheduling and organizing production batches, manufacturers can streamline their operations, improve efficiency, and ensure timely delivery of products to their customers.
In this article, we will delve into the concept of SLA batch planning, exploring its benefits, implementation steps, and best practices. Whether you are a machine shop owner, manufacturing professional, or prototyping facility manager, understanding and leveraging SLA batch planning can help you optimize your operations and deliver a seamless experience to your clients.
What is SLA Batch Planning?
SLA batch planning is a strategic approach to scheduling and organizing production batches in alignment with specific Service Level Agreement (SLA) requirements. It involves carefully planning and executing manufacturing processes to meet the agreed-upon service standards, ensuring that products are delivered to customers within the specified timeframes and quality parameters.
The primary goal of SLA batch planning is to optimize operational efficiency while meeting customer expectations. By aligning production goals with SLA requirements, manufacturers can streamline their processes, minimize waste, and maximize resource utilization. This approach enables them to deliver products and services consistently, reliably, and cost-effectively.
SLA batch planning takes into account various factors such as production capacity, lead times, inventory levels, and resource availability. It requires a deep understanding of the manufacturing process, customer demands, and the constraints outlined in the SLA. By carefully analyzing these factors and developing a comprehensive batch planning strategy, manufacturers can make informed decisions that drive operational excellence and customer satisfaction.
How to Implement SLA Batch Planning
Implementing SLA batch planning requires a strategic approach that enhances production alignment with Service Level Agreements. Begin by pinpointing the specific objectives of the SLA and their implications on production workflows. This initial analysis is crucial for setting production targets that seamlessly integrate with SLA goals, thereby boosting operational effectiveness.
Step 1: Analyze SLA Requirements
To effectively incorporate SLA batch planning, pinpoint the metrics that critically influence batch scheduling. These often encompass timelines, quality benchmarks, and production capacities. Engage with key stakeholders—including production leads, quality control teams, and logistics partners—to gather a complete understanding of the expectations and limitations outlined in the SLA. This collaboration fosters a unified direction and facilitates shared goals.
Step 2: Develop a Batch Planning Strategy
After understanding SLA requirements, create a robust batch planning strategy that aligns with these goals. This strategy should outline the necessary actions to organize production cycles efficiently. Use innovative planning methodologies to enhance precision in scheduling and execution. Methods like Demand Forecasting and Capacity Planning can be integrated into your strategy to optimize resource allocation and reduce downtime. By incorporating these techniques, your batch planning strategy not only meets SLA expectations but also drives cost efficiency and enhances productivity.
Step 3: Design a Template for Batch Planning
Developing a versatile SLA batch planning template is key to improving process flow and ensuring uniformity. The template should comprise essential elements such as deadlines, resource distribution, and fallback strategies. By standardizing these components, you offer a clear blueprint for production teams, minimizing the risk of errors. Consider leveraging digital tools that automate the template design process, enabling real-time updates and modifications as necessary.
With these steps, SLA batch planning becomes an actionable framework that elevates production efficiency and fulfills client requirements. By concentrating on these facets, manufacturers can ensure their operations not only comply with SLA mandates but are also fine-tuned for peak performance and cost-effectiveness.
Step 1: Analyze SLA Requirements
Delving into the specifics of SLA requirements is the initial step in crafting an effective batch planning strategy. Start by focusing on the critical performance indicators that influence production schedules. These include parameters such as cycle times, quality thresholds, and delivery commitments. These indicators act as a framework, ensuring that production efforts align with SLA directives and consistently satisfy client expectations.
After establishing the core metrics, fostering collaboration with key personnel is paramount. Engaging with diverse teams—including production, supply chain, and quality assurance—offers a comprehensive perspective on the SLA's stipulations and potential hurdles. This cross-functional engagement not only clarifies roles but also uncovers areas where process improvements can be made. By nurturing an environment of collaboration, teams can synchronize their objectives to meet SLA challenges head-on.
Organizing strategic sessions with relevant stakeholders facilitates a deeper discussion of SLA requirements. These meetings provide a dedicated space for unpacking the complexities of the SLA and crafting tailored solutions to enhance batch planning. The exchange of ideas in such forums helps align team actions with the SLA's goals, fostering a cohesive and responsive production strategy.
Step 2: Develop a Batch Planning Strategy
Formulating an effective batch planning strategy necessitates a focus on aligning production processes with SLA requirements. This involves a comprehensive assessment of operational workflows to pinpoint areas of improvement and optimize task prioritization. By thoroughly evaluating production sequences, you can ensure that resources are allocated optimally, eliminating potential delays and enhancing workflow efficiency.
Embracing cutting-edge technology is crucial for enhancing the precision and flexibility of your batch planning strategy. Consider employing algorithmic tools and automated systems that facilitate dynamic scheduling and predictive analytics. Such tools empower you to anticipate production demands and adjust schedules proactively. By leveraging these advanced solutions, you gain the ability to swiftly adapt to changes, maintaining a seamless production flow.
Cultivating an environment that encourages innovation and adaptation is key to sustaining an effective batch planning strategy. Regularly conduct team workshops and brainstorming sessions to explore new process improvements. Encourage cross-departmental collaboration to gather diverse insights and foster a culture of shared learning. This approach not only refines your batch planning strategy but also ensures that your operations remain agile and responsive to evolving SLA demands.
Step 3: Design a Template for Batch Planning
Constructing a personalized batch planning template represents a pivotal step in refining operational workflows. This template serves as a roadmap, ensuring that every key factor is methodically addressed, thus facilitating a coherent and efficient execution of batch plans. It should be tailored to accommodate the unique intricacies of your production processes, with an emphasis on flexibility and accuracy.
Core Elements of the Template
Incorporate detailed schedules that align with SLA directives and production timelines. Well-structured schedules facilitate progress monitoring and foster accountability within cross-functional teams. This alignment helps maintain synchronization with SLA commitments, minimizing the risk of deviations.
Another fundamental aspect is the detailed mapping of resource allocation. The template should clearly delineate how various resources—be it personnel, materials, or machinery—are allocated throughout the production phases. This specificity helps avert potential resource constraints and maximizes operational throughput.
Additionally, proactive risk management strategies should be embedded within the template. These strategies provide actionable steps to mitigate potential setbacks, ensuring continuity and stability in production operations. By preemptively identifying challenges and crafting solutions, you bolster the robustness of your batch planning framework.
Advancing Template Customization
Ensuring the template's ability to adapt to various production scenarios is crucial. This involves integrating capabilities for on-the-fly adjustments based on evolving SLA requirements or shifts in production dynamics. A flexible template enhances the ability to swiftly accommodate changes in demand or unexpected hurdles.
To further advance customization, leverage technological solutions that facilitate seamless updates and dissemination of templates. These solutions enhance cross-departmental communication and keep all stakeholders apprised of any modifications. The incorporation of such technology not only streamlines the planning process but also ensures consistent alignment with SLA objectives.
By meticulously crafting a batch planning template with an emphasis on schedules, resource mapping, and risk strategies, it becomes a strategic asset. This asset not only enhances process efficiency but also encourages a proactive stance on fulfilling SLA obligations, thereby strengthening operational capability and resilience.
Step 4: Implement Optimization Techniques
Elevating batch planning efficiency requires a strategic blend of technological integration and process refinement. The focus is on advancing production cycles to meet SLA standards effectively while optimizing resource management. Begin by assessing current workflows to pinpoint where innovative optimization methods can enhance productivity.
Utilizing Advanced Technologies
Integrating cutting-edge technologies into batch planning can transform efficiency and precision. Tools like sophisticated scheduling software and real-time analytics platforms enable a more agile approach to managing production schedules. By automating repetitive tasks, these technologies allow teams to concentrate on high-value activities. Moreover, leveraging data analytics can provide predictive insights, helping to identify and mitigate potential disruptions before they impact operations.
Automation in Process Enhancement
Automation plays a crucial role in modernizing batch planning processes. Implementing systems that automate data collection and analysis ensures that managers have timely access to critical information. This capability allows for rapid response to changing SLA requirements or unexpected production issues. Automated notifications can alert teams to deviations, ensuring swift corrective actions to maintain operational integrity.
Commitment to Continuous Improvement
Optimization is an ongoing pursuit of operational excellence. Regular evaluations of optimization strategies help ensure their continued effectiveness and adaptability to changing demands. Conduct routine process reviews to gauge the impact of optimization efforts, identifying new opportunities for improvement. Fostering a culture that values continuous improvement and open feedback can drive further enhancements in batch planning processes.
By systematically applying optimization techniques and harnessing technology, manufacturers can achieve a more streamlined, adaptable, and efficient batch planning system. This not only aligns with SLA commitments but also supports long-term operational success.
Step 5: Monitor and Adjust
Establishing a dynamic review framework is essential for ensuring batch planning remains effective. This involves setting up detailed metrics that provide actionable insights into current production processes. Regular assessment of these metrics allows for timely identification of areas needing improvement, enabling swift responses to maintain operational goals. By actively reviewing outcomes, you can adapt strategies to meet evolving requirements, thereby enhancing productivity and maintaining high standards.
Implementing Real-Time Monitoring Solutions
To effectively track batch planning outcomes, integrating robust real-time monitoring solutions is key. These solutions should offer advanced data visualization and reporting features, giving a comprehensive view of production dynamics. Cutting-edge monitoring tools enable the early detection of potential issues, promoting immediate corrective measures. This continuous feedback mechanism ensures operations can quickly adapt to changes, maintaining smooth production flows.
Tactical Adjustments and Enhancement Strategies
Once monitoring tools pinpoint areas for improvement, tactical adjustments become necessary. This involves refining operational strategies to boost efficiency and address identified challenges. Regular strategy sessions with cross-functional teams ensure these adjustments are both informed and aligned with overarching goals. By fostering a proactive approach, teams can implement changes that strengthen operational capabilities and sustain performance levels.
Harnessing Predictive Analytics
Utilizing predictive analytics is crucial for enhancing batch planning strategies. By leveraging advanced analytics, teams can forecast trends and make informed decisions to optimize processes. This forward-thinking approach enhances strategic planning, enabling teams to anticipate challenges and devise solutions proactively. Incorporating predictive insights further refines the ability to maintain seamless operations and drive continuous advancement.
Through diligent monitoring and strategic adaptability, manufacturers can uphold a standard of excellence. This proactive approach not only ensures alignment with production objectives but also fosters an environment of innovation and resilience.
Tips on Effective SLA Batch Planning
A dynamic SLA batch planning process relies on consistently adapting strategies to address evolving requirements. Central to this approach is the continuous evaluation of performance indicators that directly impact production efficiency. By staying abreast of industry standards and incorporating best practices, you ensure that your batch planning aligns with cutting-edge methodologies. This vigilant oversight allows for the early detection of potential inefficiencies, facilitating timely interventions that maintain production excellence.
Foster Collaborative Synergy
Creating an environment that prioritizes interdepartmental synergy is vital for achieving SLA objectives. Encourage regular interaction and collaboration among teams to cultivate a shared understanding of operational goals and challenges. By establishing forums for open dialogue, such as cross-functional workshops and joint strategy sessions, organizations can harness a diversity of perspectives. This collective intelligence enhances the ability to innovate and implement agile solutions that are responsive to changing conditions.
Harness Advanced Technological Tools
Incorporating state-of-the-art technological tools into your batch planning process transforms operational efficiency. Explore sophisticated software solutions that offer comprehensive features like real-time data integration and advanced analytics. These platforms facilitate seamless coordination and execution of batch plans by providing actionable insights and automating complex tasks. By leveraging these technological advancements, you not only streamline operations but also position your organization at the forefront of industry innovation.
Embracing effective SLA batch planning is a transformative step towards operational excellence. By aligning production processes with SLA objectives, leveraging advanced technologies, and fostering a culture of continuous improvement, you can unlock new levels of efficiency and customer satisfaction. If you're ready to revolutionize your manufacturing operations, schedule a demo or try the platform to experience how we can help you achieve your goals.